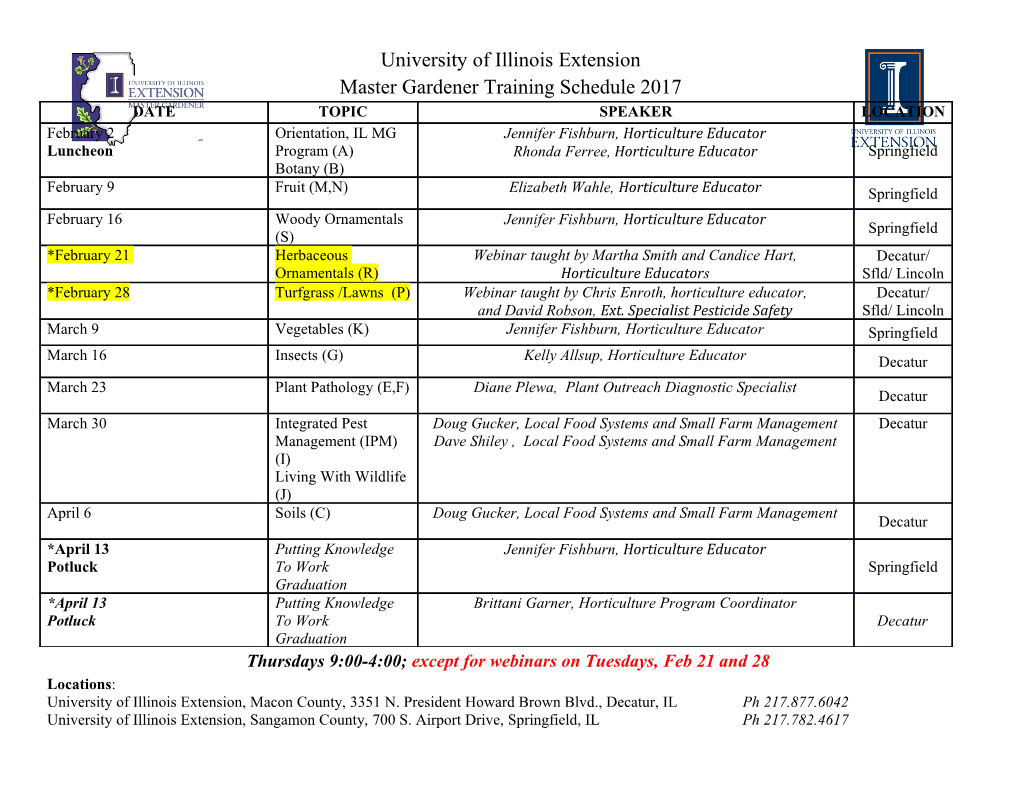
Medical Device Packaging Tips, Learnings and Cautionary Tales OMTEC 2015 Chicago Alison Tyler Technical Director Beacon Converters, Inc. June 2015 © 2012 Beacon Converters, Inc. Presentation Topics • Why is Medical Packaging so Important? • Packaging Guidance and Compliance Standards • Major decision points for selecting materials and packaging design • Review of Recent FDA Recalls © 2012 Beacon Converters, Inc. A Glimpse Inside Healthcare Environment (Where Medical Device Packaging is Used) • 490,000 Americans have died in 5 year period due to medical errors. These were all categorized as preventable deaths 1. 1. Kohn LT, Corrigan JM, Donaldson MS, eds. To Err Is Human: Building a Safer Health 2. System (Washington: National Academy Press 1999) © 2012 Beacon Converters, Inc. Survey of: 831 practicing physicians 1207 members of the public © 2012 Beacon Converters, Inc. Physicians 35% 291 Reported Medical Errors in their own care of family member care Public 42% 507 Reported Medical Errors in their own care of family member care © 2012 Beacon Converters, Inc. Neither physicians nor the public named medical errors as one of the largest problems in health care today. Malpractice Cost of Insurance Companies Insurance Healthcare and Health Plans 29% 27% 22% Cost of Cost of Prescription Healthcare Drugs 38% 31% © 2012 Beacon Converters, Inc. Medical Errors were reported as a minimal problem... Medical Errors 5% So how big a deal are they really? Medical Errors 6% © 2012 Beacon Converters, Inc. Medical Reality • From 1994-1999 a study was done regarding how many people DIED from preventable medical errors • 490,000 Americans have died in this 5 year period due to medical errors. These were all categorized as preventable deaths • 1. Kohn LT, Corrigan JM, Donaldson MS, eds. To Err Is Human: Building a Safer Health • System (Washington: National Academy Press 1999) © 2012 Beacon Converters, Inc. So we were in Bad Shape in 1999…how are we today? • Well, lets just say things aren’t pretty Current data estimates that annually as many as …. 440,000 Americans die every single year from preventable medical errors. This now ranks medical errors as the 3rd leading cause of death in the United States. © 2012 Beacon Converters, Inc. Hospital Safety Score Source www.hospitalsafetyscore.org Highland Park Hospital Highland Park Hospital Greater Boston Area © 2012 Beacon Converters, Inc. West Virginia © 2012 Beacon Converters, Inc. So What Does this Have to Do with Packaging? • This is the same environment that packages will be opened in, one that is riddled with errors • You aren’t only going to sell your device in Boston. • Your design must be easy to follow, must NOT contribute to any additional errors. • You cannot depend on people working in this environment to police for package failures • Lets get on to making great packages! © 2012 Beacon Converters, Inc. Guidance Standards – Use Them! Packaging Guidance and Compliance Standards 1. AAMI/ISO- 11607 Packaging for terminally sterilized medical devices • Part 1- materials, sterile barrier systems and packaging systems • Part 2- Validation requirements for forming, sealing and assembly processes 2. AAMI TIR 22- Guidance for ANSI/AMMI/ISO-11607 Parts 1 & 2 (Don’t try to reinvent the wheel) © 2012 Beacon Converters, Inc. AAMI/ISO Standards 11607- Part 1 1. Protect the device from physical damage 2. Protect the device from undesirable environmental conditions 3. Allow device to be terminally sterilized 4. Allow that sterility to be maintained until the product is dispensed 5. Allow aseptic presentation © 2012 Beacon Converters, Inc. AAMI / ISO Standards TIR-22 (ISO 16775) Design Inputs • Product Attributes • Protection Requirements • Storage, Distribution and Handling Requirements • Manufacturing Requirements • Sterilization Requirements • Customer Requirements © 2012 Beacon Converters, Inc. AAMI Standards TIR-22 (ISO 16775) Annex Information • Regulatory references • Test Method Validation • Sterilization Considerations • Design Inputs-Attributes & Requirements • Investigating Failure • Selection, Evaluation and Testing • Generating a Validation Protocol • Risk Analysis Tools © 2012 Beacon Converters, Inc. 5 Major Points; Packaging Performance What does your package need to do? 1• Protect your device from physical damage • Puncture • Abrasion • Improper cushioning Glue flap • Crushing • Insufficient shielding Inside out / outside in puncture © 2012 Beacon Converters, Inc. Design Inputs Protection from Physical Damage Predict Damage Possibilities with good inputs – Size, Profile – Weight – Center of Gravity – Fragile or rugged – Sharp edges or points – Surface Characteristics – Small component pieces – Bend Sensitive © 2012 Beacon Converters, Inc. Design Inputs Protection from Physical Damage • Multiple components of varying size and shape • Heavy, bulky handle • Fragile knob used to control the laser source • Large fluid reservoir • Bend-sensitive fiber optics and tubing PMP News webinar archive: Reduce, Recycle, Recover: Redefine your sterile barrier system in a flexible footprint © 2012 Beacon Converters, Inc. Design Inputs Protection from Physical Damage Orthopedic Drill and Pin Kit • Multiple components • Varied size/shape. • Sharp edged • Heavy (surgical steel). • Materials include steel and molded polymer parts. © 2012 Beacon Converters, Inc. Damaging Environmental Conditions Moisture Protect the device from 2 Microbes undesirable environmental conditions Carbon Dioxide What conditions could harm or degrade your device and packaging system? Temperature Extremes Ultra Violet © 2012 Beacon Converters, Inc. Design Inputs Protection from Environment Water Vapor Oxygen Material (g-mil / 100 in2-day) (cc-mil / 100 in2-day) LDPE 1.2 510 LLDPE 0.8 280 HDPE 0.4 170 Ionomer 1.7 500 Cast PP 0.7 240 OPP 0.4 120 PET 1.2 2.3 BON 10 1.7 PVdC 0.1 0.1 PCTFE 0.015 9.8 AlOx PET 0.1--0.005 0.2--0.006 MVTR: 100°F, 90% RH OTR: 73°F, 50%RH © 2012 Beacon Converters, Inc. Design Inputs Protection from Environment Typical Vapor Barrier Levels MVTR (g/100 sq.in/day) 12 10 8 6 4 2 0 A60 AlOx PET PCTFE PVdC BON PET OTR OPP MVTR Cast PP Ionomer Materials (0.001" caliper) Materials HDPE LLDPE LDPE 0 100 200 300 400 500 600 OTR (cc/100 sq.in./day) © 2012 Beacon Converters, Inc. Layers of Protection What do your flexible packaging materials do Strength HDPE PET Moisture Barrier Oxygen Barrier PP UV Barrier Chemical Resistance LDPE Seal Strength © 2012 Beacon Converters, Inc. Protection from Environment Overwrap Bag for IV products • Active drug substance will degrade in light. • Fluid loss affects drug dosage. • Must be autoclaved to sterilize. • Product visibility is required. Overwrap Bag for IV products Protection from Environment FDA • UV Light Barrier protects active drug substance. • AlOx Moisture/Oxygen Barrier prevents loss of fluid/drug effectiveness. • Heat resistant layers are durable in high heat process temperatures of autoclaving. • Bag is translucent for product visibility • Bag designed for tear open application Tissue / Collagen Like Products Protection from Environment A3460 A34 –Polyester/LDPE/Aluminum Foil/Seal layer A60- AlOx Polyester/Seal layer • Increase in products requiring very high barrier • Sometimes liquid is part of product • Low profile • Moisture loss critical 5 Major Points; Packaging Performance What does your package need to do? 3• Allow device to be terminally sterilized • Porous or impermeable? • Compatibility with process – steam, autoclave, VHP, EO, Gamma and electron beam Guidance for ANSI/AAMI/ISO 11607 Sterilization Compatibility of Considerations materials subject to sterilization © 2012 Beacon Converters, Inc. Sterilization Steam & Autoclave • Steam Sterilization requires porous package – Paper with good wet strength – In some cases Tyvek can be used if temperature is less than about 121°C. • HDPe, PP, PA are common film webs incorporated into high temperature moist applications • Autoclave utilizes non-porous materials © 2012 Beacon Converters, Inc. Sterilization Ethylene Oxide • Suitable for heat and humidity • Porosity must be sufficient to: – allow gases to penetrate or exhaust all layers – reach the interior of the product – minimize the stress on materials and seals (don’t mask Tyvek®) • How many layers will surround product? • Primary and secondary packaging • Double or triple bagged • Kit building (all components must be considered) • Be Careful with labels © 2012 Beacon Converters, Inc. Sterilization Radiation- Gamma & E-beam • Radiation – Materials must maintain their properties for desired shelf life protection – Package need not be breathable • Provide for outgassing – Radiation can be damaging to packaging materials, paper and polypropylene in particular. • Refer to TIR 17 or ask your supplier cumulative • Flexible packaging uses thin caliper materials, more affected by sterilization dosages • If re-sterilizing, re-package for safety and durability © 2012 Beacon Converters, Inc. Sterilization VHP- Plasma • A hydrogen peroxide plasma is the primary sterilizing agent – Non-cellulose porous packaging needed – Process can be damaging to extrusion coated/laminated materials (adhesion to substrate is compromised) – Typical package: PET/PE adhesive laminate sealed to Tyvek © 2012 Beacon Converters, Inc. 5 Major Points; Packaging Performance What does your package need to do? Allow that sterility be maintained until the 4 product is dispensed • Compromise of Sterility is event related • Sterility is not time related • A sterilized object will remain sterile until an
Details
-
File Typepdf
-
Upload Time-
-
Content LanguagesEnglish
-
Upload UserAnonymous/Not logged-in
-
File Pages56 Page
-
File Size-