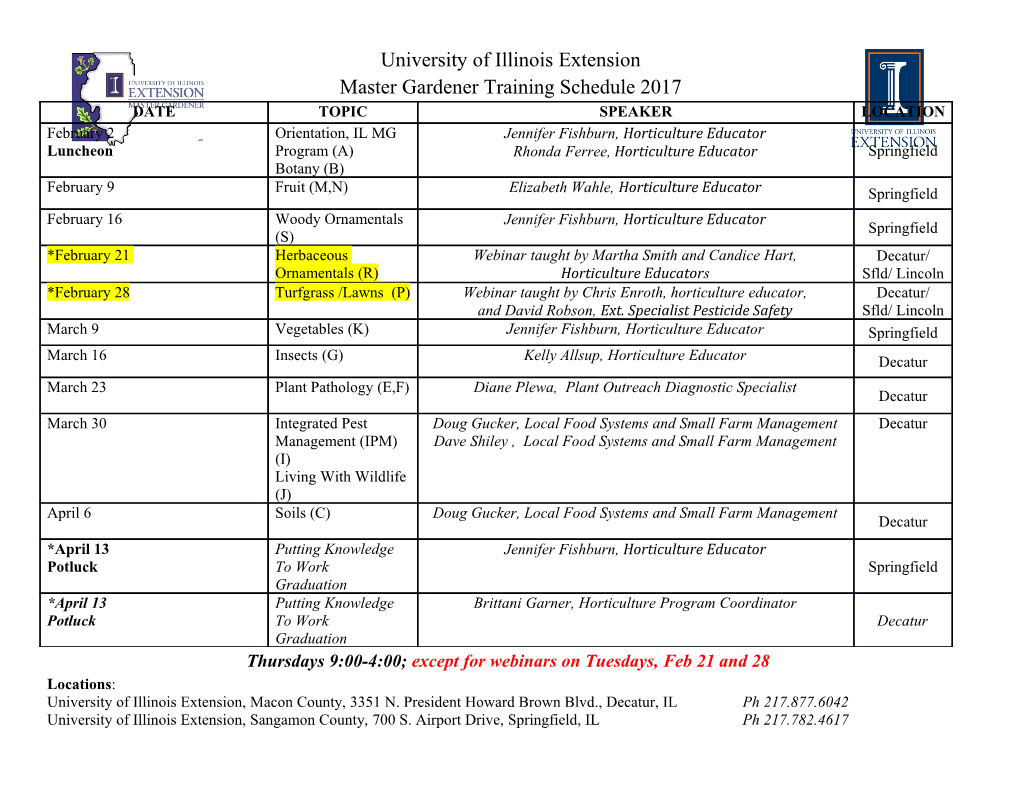
Simulation of Laser Additive Manufacturing and its Applications DISSERTATION Presented in Partial Fulfillment of the Requirements for the Degree Doctor of Philosophy in the Graduate School of The Ohio State University By Yousub Lee Graduate Program in Welding Engineering The Ohio State University 2015 Dissertation Committee: Professor Dave F. Farson, Advisor Professor Wei Zhang, Advisor Professor Antonio J. Ramirez Copyright by Yousub Lee 2015 Abstract Laser and metal powder based additive manufacturing (AM), a key category of advanced Direct Digital Manufacturing (DDM), produces metallic components directly from a digital representation of the part such as a CAD file. It is well suited for the production of high-value, customizable components with complex geometry and the repair of damaged components. Currently, the main challenges for laser and metal powder based AM include the formation of defects (e.g., porosity), low surface finish quality, and spatially non-uniform properties of material. Such challenges stem largely from the limited knowledge of complex physical processes in AM especially the molten pool physics such as melting, molten metal flow, heat conduction, vaporization of alloying elements, and solidification. Direct experimental measurement of melt pool phenomena is highly difficult since the process is localized (on the order of 0.1 mm to 1 mm melt pool size) and transient (on the order of 1 m/s scanning speed). Furthermore, current optical and infrared cameras are limited to observe the melt pool surface. As a result, fluid flows in the melt pool, melt pool shape and formation of sub-surface defects are difficult to be visualized by experiment. On the other hand, numerical simulation, based on rigorous solution of mass, ii momentum and energy transport equations, can provide important quantitative knowledge of complex transport phenomena taking place in AM. The overarching goal of this dissertation research is to develop an analytical foundation for fundamental understanding of heat transfer, molten metal flow and free surface evolution. Two key types of laser AM processes are studied: a) powder injection, commonly used for repairing of turbine blades, and b) powder bed, commonly used for manufacturing of new parts with complex geometry. In the powder injection simulation, fluid convection, temperature gradient (G), solidification rate (R) and melt pool shape are calculated using a heat transfer and fluid flow model, which solves the mass, momentum and energy transport equations using the volume of fluid (VOF) method. These results provide quantitative understanding of underlying mechanisms of solidification morphology, solidification scale and deposit side bulging. In particular, it is shown that convective mixing alters solidification conditions (G and R), cooling trend and resultant size of primary dendrite arm spacing. Melt pool convexity in multiple layer LAM is associated not only with the convex shape of prior deposit but also with Marangoni flow. Lastly, it is shown that the lateral width of bulge is possibly controlled by the type of surface tension gradient. It is noted that laser beam spot size in the powder injection AM is about 2 mm and it melts hundreds of powder particles. Hence, the injection of individual particles is approximated by a lumped mass flux into the molten pool. On the other hand, for laser powder bed AM, the laser beam spot size is about 100 μm and thus it only melts a few iii tens of particles. Therefore, resolution of individual powder particles is essential for the accurate simulation of laser powder bed AM. To obtain the powder packing information in the powder bed, dynamic discrete element simulation (DEM) is used. It considers particle-particle interactions during packing to provide the quantitative structural powder bed properties such as particle arrangement, size and packing density, which is then an inputted as initial geometry for heat transfer and fluid flow simulation. This coupled 3D transient transport model provides a high spatial resolution while requiring less demanding computation. The results show that negatively skewed particle size distribution, faster scanning speed, low power and low packing density worsen the surface finish quality and promote the formation of balling defects. Taken together, both powder injection and powder bed models have resulted in an improved quantitative understanding of heat transfer, molten metal flow and free surface evolution. Furthermore, the analytical foundation that is developed in this dissertation provides the temperature history in AM, a prerequisite for predicting the solid-state phase transformation kinetics, residual stresses and distortion using other models. Moreover, it can be integrated with experimental monitoring and sensing tools to provide the capability of controlling melt pool shape, solidification microstructure, defect formation and surface finish. iv Dedicated to my parents and wife v Acknowledgments I would like to greatly appreciate my advisor, Prof. Dave Farson for his guidance, valuable advice and support throughout my PhD studies at The Ohio State University. As a professor, Dr. Farson is one of the distinctive researchers in the welding engineering and laser materials processing. He is actively serving technical societies as President, Board Member and other offices for Laser Institute of America. As my advisor, he has pleasantly helped me all the time with big patience to correct my scientific mistakes. I must thank to my co-advisor, Prof. Wei Zhang for his smart advices, encouragement and support for the last year of my PhD study. Before he came to OSU as a professor, he was a distinctive researcher at Oak Ridge National Laboratory (ORNL) and Edison Welding Institute (EWI). He is now a core faculty for Simulation Innovation and Modeling Center (SIMCenter). Being his student, I have learned critical thinking and writing making me an independent researcher. Moreover, I realize that he is always ready to help his students to achieve academic and career goals. Also, I truly thank Prof. Suresh Babu at University of Tennessee, Knoxville for his enthusiastic comments and help during my graduate school. I would like to thank Prof. Antonio Ramirez being a committee member and his critical comments on my dissertation. vi I would like to acknowledge Rolls Royce, CIMJSEA center (Now, Ma2JIC) and Office of Naval Research for the financial support. I appreciate Dr. J.S. Bader and M. Nordin (Rolls Royce), Prof. John Lippold (CIMJSEA) and Dr. Richard W. Fonda (ORN). Thanks to all my colleagues and professors in WE and MSE for all helps. Last but not least, thanks to my parents and younger sister for their unbelievable support and love. Special thanks to my wife, Jinmo. I will always remember your endless patience and love. vii Vita 1979................................................................Born-Daegu, South Korea 2007................................................................B.S. Materials Science and Metallurgical Engineering, Kyungpook National University 2009................................................................M.S. Materials Science and Engineering, Seoul National University 2011 to present ..............................................Graduate Research Associate, Welding Engineering, The Ohio State University Publications 1. Lee YS, Nordin M, Babu SS, Farson DF (2014) Influence of fluid convection on weld pool formation in laser cladding. Welding Journal 93(8):292S-300S. 2. Lee Y, Nordin M, Babu SS, Farson DF (2014) Effect of Fluid Convection on Dendrite Arm Spacing in Laser Deposition. Metallurgical and Materials Transactions B 45(4): 1520-1529. 3. Lee YS and Zhang W Mesoscopic (2015) Simulation of Heat Transfer and Fluid Flow in Laser Powder Bed Fusion Additive Manufacturing. In Proceeding of Solid Freeform Fabrication Symposium, Austin, Texas viii Fields of Study Major Field: Welding Engineering ix Table of Contents Abstract ............................................................................................................................... ii Acknowledgments.............................................................................................................. vi Vita ................................................................................................................................... viii Table of Contents ................................................................................................................ x List of Tables ................................................................................................................... xiv List of Figures ................................................................................................................... xv Chapter 1: Introduction ....................................................................................................... 1 Chapter 2: Influence of Fluid Convection on Weld Pool Formation in Laser Cladding .... 9 2.1 Introduction ............................................................................................................... 9 2.2 Experimental Conditions ......................................................................................... 12 2.3 Clad deposit modeling ............................................................................................. 13 2.3.1 Governing equations ......................................................................................... 14 2.3.2 Boundary conditions and physical properties for the simulation
Details
-
File Typepdf
-
Upload Time-
-
Content LanguagesEnglish
-
Upload UserAnonymous/Not logged-in
-
File Pages215 Page
-
File Size-