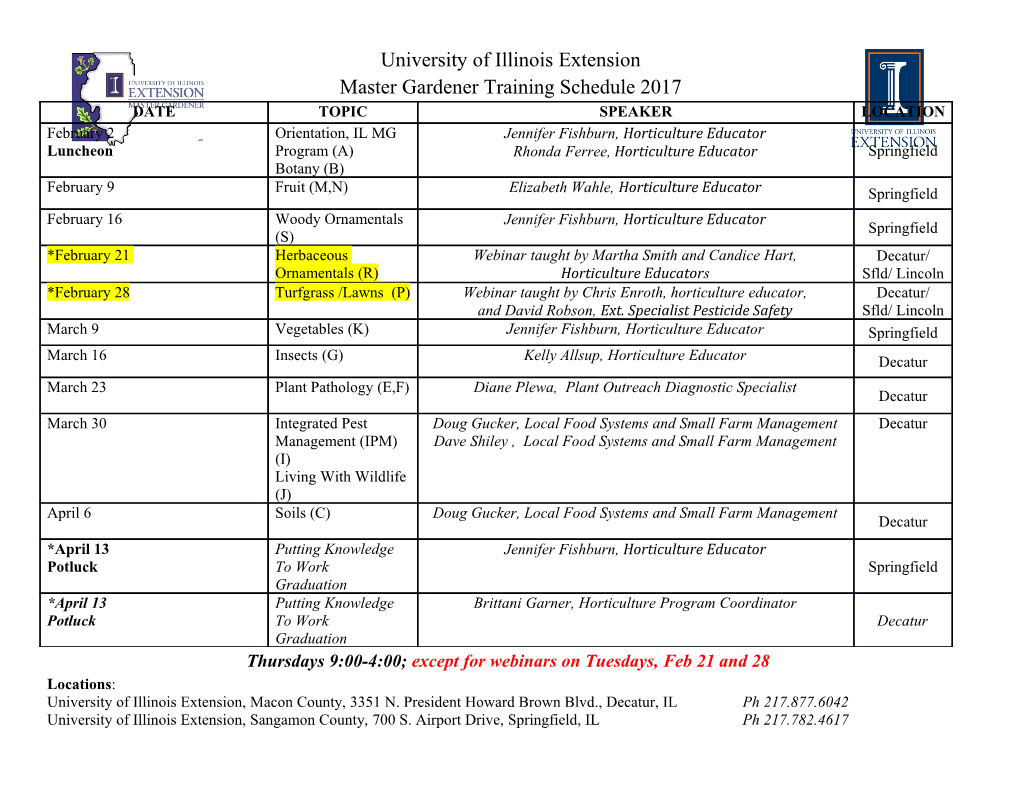
Fire Safety Journal 70 (2014) 46–60 Contents lists available at ScienceDirect Fire Safety Journal journal homepage: www.elsevier.com/locate/firesaf Outlining the mechanism of flame retardancy in polyamide 66 blended with melamine-poly(zinc phosphate) Anil D. Naik a, Gaëlle Fontaine a, Fabienne Samyn a, Xavier Delva b, Jérémie Louisy b, Séverine Bellayer a, Yann Bourgeois b, Serge Bourbigot a,n a ISP/UMET—UMR/CNRS 8207, Ecole Nationale Supérieure de Chimie de Lille (ENSCL), Avenue Dimitri Mendeleïev—Bât. C7a, BP 90108, 59652 Villeneuve d’Ascq Cedex, France b Floridienne Chimie, 12 Quai des Usines, 7800 Ath, Belgium article info abstract Article history: Glass-fiber reinforced polyamide 66 is flame retarded with a mixture of melamine-poly(zinc phosphate), Received 16 May 2014 (Safires400) and diethyl aluminium phosphinate. The performance of this synergistic combination of Received in revised form additives is multi-modal and a comprehensive investigation is undertaken to elucidate the underlying 27 August 2014 flame retardancy mechanism. The strategy was to characterize the different chemical species responsible Accepted 31 August 2014 for flame retardancy that are generated in gas and condensed phases under different fire scenarios. Available online 10 October 2014 Following heat release rate (HRR) curve of flame retarded polyamide formulations obtained by mass loss Keywords: calorimeter, samples in different stages of degradation are collected and investigated. Further flame Flame retardancy retardants and formulations were degraded in tubular furnace whose temperature protocol relied on Polyamide-66 thermal degradation profile obtained from thermogravimetric analysis (TGA). In either case, species Melamine polyphosphate generated in condensed phase were studied by solid state nuclear magnetic resonance spectroscopy Aluminum phosphinate 27 31 13 Zinc polyphosphate (magic angle spinning (MAS) NMR; Al, P and C), Fourier transform Infra-red spectroscopy (FTIR), Safires400 X-ray powder diffraction (XRD), electron probe microanalysis (EPMA), scanning electron microscopy (SEM), and optical microscopy, whereas TGA coupled FTIR, and pyrolysis gas chromatography mass spectrometry (Py/GC/MS) were utilised to investigate species released in gas phase. Flame retardancy mechanism is elaborated based on the identification of the chemical species in both gas and condensed phases and their specific contributing role. & 2014 Elsevier Ltd. All rights reserved. 1. Introduction recycling-waste disposal, and theoretical studies involving simulation of fire scenario. Fire risks involving polymers have devastating consequences as Among several inorganic flame retardants (FRs), metal phos- polymer utility ranges from consumer products to high-performance phates have been an efficient ingredient in the formulation of flame hardware manufacturing [1–6].Apanelofflame retardants are retardant polymers particularly with cations like Zn2þ ,Mg2þ ,Al3þ, developed to confront these issues and safeguard vulnerable targets Zr4þ ,Ti4þ [3,4,6–12].Midstofthem,zincphosphates(ZnPO)are like E&E products, materials used in transport vehicles, building- found to be multi-faceted in flame retardancy [12]. ZnPOs have rich construction materials, upholstery etc … depending on the type of structural chemistry mainly due to the coordination flexibility of the plastics and targeted application. The current preventive fire safety zinc ions, which can form polyhedral by coordinating to four, five or trend, aimed at keeping the highest fire safety standards, explores six donor atoms in the framework. Such zinc polyhedra have the novel additives to insulate polymers from fire hazards that are not ability to catenate to chains by face, edge, or vertice-sharing [13]. only efficient, synergistic, multifunctional, but are tailored to be tagged ZnPO also exhibits a wide glass forming composition ranging from with ‘eco-label’ to comply with stringent regulations [3,7].Further, ultraphosphate region (y¼ZnO/P2O5o1) to highly cross-linked poly- flame retardancy mechanism is multifaceted and an insight into its phosphate glasses (yZ1) [14–18]. The basic structural unit of all mode of action provide valuable information for issues like additive- phosphates, crystalline or amorphous, is the PO4 tetrahedron. polymer compatibility, synergism, re-design strategy for additives, Coupling such efficient metal phosphates with tailored organic molecules is promising strategy to further upgrade phosphates to attain multi-functionality. In this respect, flame retardancy label of melamine family was further widened and strengthened by introdu- n Corresponding author. cing melamine intercalated metal polyphosphates [8,9,11,19,20]. s E-mail address: [email protected] (S. Bourbigot). Safire series is a good example for this that was introduced recently http://dx.doi.org/10.1016/j.firesaf.2014.08.019 0379-7112/& 2014 Elsevier Ltd. All rights reserved. A.D. Naik et al. / Fire Safety Journal 70 (2014) 46–60 47 by Wehner and Dave [8,9].Safires400 (hereafter referred S400), plastics (St Fons, France), Diethyl aluminium phosphinate with Melamine‐poly(zinc phosphate) is one among them. The molecular trade name of Exolit OP1230 (AlPi) was from Clariant (Knapsack, s structure of S400 is given in Fig. 1a. This molecule can also be Germany). Safire 400, Melamine‐poly(zinc phosphate), {(MelH)2 considered as a categorized molecular state of melamine which [Zn(P2O7)]}n) was kindly provided by Catena Additives a fully shares the responsibility of charge balancing, structure directing owned subsidiary of Floridienne Group (Ath, Belgium) and are moiety besides actively participating in flame retardancy. On a supplied in polycrystalline form (Fig. 1b and c). molecular level, the cationic chains of melamine are assumed to be alternated by anionic ZnPO chains with dense secondary interactions 2.2. Formulations, processing and sampling with the matrix similar to melamine phosphates [21]. fi fl fi S400 is found to have signi cant in uence on re performance of 2.2.1. Formulation and processing fi glass- bre reinforced polyamide 66, particularly when coupled with Compounding of formulations (Table 1) were performed using diethyl aluminium phosphinate and passes mandatory tests like UL- HAAKE Rheomix OS PTW 16 twin screw extruder [11a]. All the 94, and glow wire tests. Further there is substantial reduction in peak materials were dried at 80 1C under vacuum for 24 h prior to of heat release and total heat release evaluated by mass loss extrusion. calorimeter [8,9,11]. S400 is also found to be a char/intumescence forming agent. Our investigation has been focussed on the elucida- 2.2.2. Sampling tion of flame retardancy mechanism of S400 and aluminium Samples for the study were collected from two sources (Table 1). phosphinate (1:2 ratio, total 18 wt% of flame retardants) blended One is from mass loss calorimeter experiment which is based on HRR glass fibre reinforced polyamide-66. There are several comprehensive curve [11a] wherein exposure to heat flux/flaming were stopped reports on mechanistic aspects of melamine based flame retardants and extinguished manually at 100, 300, 600 and 1000 s. The intended in polyamides [22–33]. Our study has been supported by parallel (100 to 1000 s) time selection for sample collection is principally based investigation on decomposition of neat S400, and single additive on HRR profile of PA66/GFþAlPiþS400 formulation which approxi- (S400) blended glass fibre reinforced polyamide-66. Further supple- mately denotes ascending, peak, descending and end of degradation, mentary data on neat polymer, aluminium phosphinate, and alumi- respectively. The same profile is extended for single additive formula- nium phosphinate blended polymer are also recorded and used as tions and neat PA66/GF. Most of the results investigated are based on references. Samples at different stages of degradation were collected these tests. Pyrolysis experiments were performed in tubular furnace based on heat release rate (HRR) curve from mass loss calorimeter. under nitrogen atmosphere. At the selected temperature, the sa- Samples were also pyrolysed in tubular furnace based on thermal mple placed in ceramic crucible was introduced into the quartz tube decomposition pattern obtained from thermogravimetry. The poten- fixed inside the tubular furnace and kept for 3 h. The tempera- tial chemical species formed during the decomposition pathway of ture selection is derived from TGA profile of formulations/additives these formulations in either method were tracked with solid state which corresponds to temperature of maximum weight loss in each nuclear magnetic resonance spectroscopy (MAS NMR; 27Al, 31Pand step performed at heating rate of 20 1C/min under nitrogen atmo- 13C), Fourier transform Infra-red spectroscopy (FTIR), and X-ray sphere. Additional temperatures mentioned in Table 1 under this powder diffraction (XRD). The gaseous products released during section correspond to either a stable plateau at the end of major the thermal decomposition of these formulations/additives were degradation step or completion of decomposition. To have an characterised by thermogravimetric analysis (TGA) coupled FTIR and pyrolysis gas chromatography mass spectrometry (py/GC/MS). Morphology of intumescence/char and additives were studied by Table 1 optical microscopy, electron probe microanalysis (EPMA), and scan- Materials investigated in the present study and conditions of sample collection. ning electron microscopy (SEM). The results are gathered to establish Materialsa
Details
-
File Typepdf
-
Upload Time-
-
Content LanguagesEnglish
-
Upload UserAnonymous/Not logged-in
-
File Pages16 Page
-
File Size-