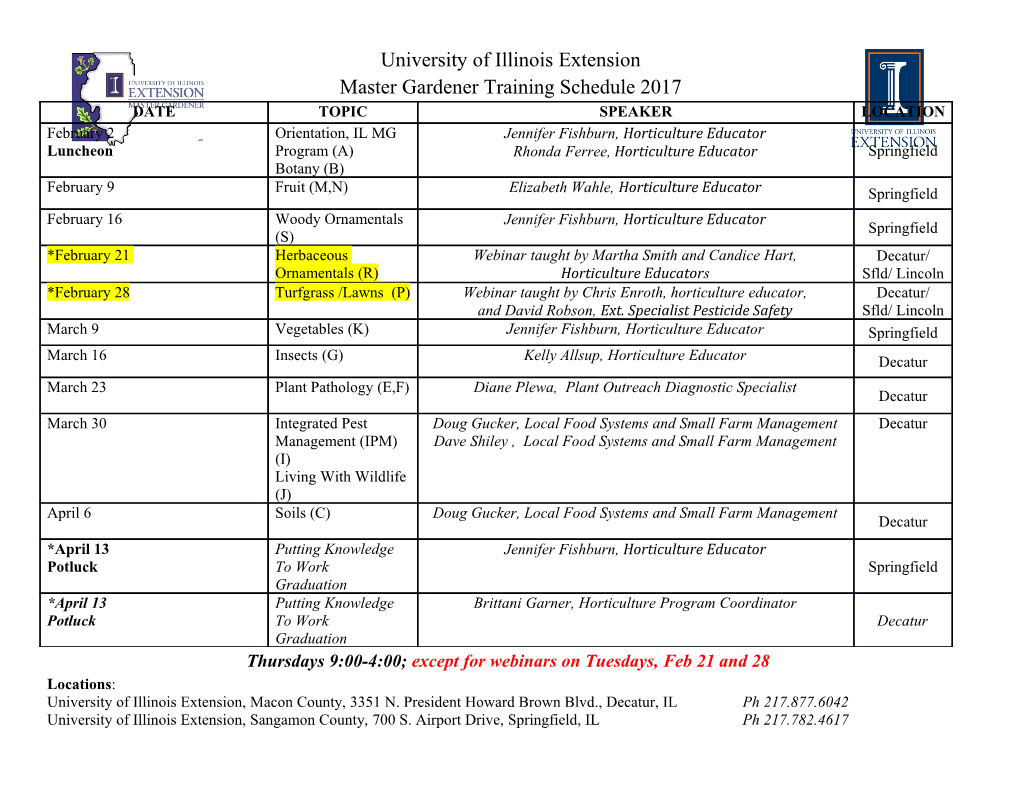
REAL VALUE QUALITY FROM SILICON TO SYSTEM Production www.solarworld.com Foreword I 3 Real Value you can count on. This is our promise to our customers. The use of solar power is noticeably increasing, and it has become the leader in renewable energies worldwide. Fortunately, a development that cannot be stopped – in favor of cleaner, safer and fairer energy production. But solar is not always solar! Where others stand still, SolarWorld takes the decisive step further, developing quality standards beyond the norm and driving the development of new technologies. We are now putting 40 years of production and technology know-how to use in all our processes worldwide. Our products must deliver what they promise. And under the real-world conditions that the modules are exposed to for at least 25 years. Our standards for the reliability of our products are defined and implemented globally at all production sites in equal measure. For our customers worldwide this means: “Quality made by SolarWorld.“ Real Value that pays off over the long term – this is our special commitment to our customers.“ Sunny regards, Dr.-Ing. E. h. Frank Asbeck CEO SolarWorld AG 4 I Company history Bill Yerkes founds Solar Technology Siemens Solar celebrates Solar cell manufacturing Robert Bosch GmbH acquires SolarWorld acquires Bosch Solar Energy in Arnstadt International with the vision of 100 megawatts of starts in Freiberg and expands ersol Solar Energy (700 MW solar cell production capacity and 200 MW manufacturing solar cells for use on Earth installed modules in Arnstadt module capacity, along with solar cell development) made in Camarillo SolarWorld acquires Production ramps up at Cell Fab 3 Expansion of module production Solar Technology ARCO Solar installs Shell Solar (formerly and module production in Arnstadt in Hillsboro (170 MW) International the world’s first Production launches Siemens Solar) becomes ARCO 1-megawatt solar at world’s first fully Third solar module factory Start of mono-crystallization Solar upon its power system and Frank Asbeck starts up automated solar module in Arnstadt debut in Camarillo, becomes market SolarWorld AG production in Freiberg in Freiberg starts production California leader Expansion of PERC- Ersol Solar Energy AG Start of PERC production capacities acquires ASi Industries production in Arnstadt in Arnstadt, Freiberg and Hillsboro and Hillsboro 1975 1977 1980 1982 1990 1994 1996 1997 1998 2000 2001 2002 2003 2004 2006 2007 2008 2010 2011 2012 2013 2014 2015 2016 ARCO Solar is Bayer Solar GmbH SolarWorld opens SolarWorld’s wafer production in Start mass production the first company is founded in production facility Freiberg becomes the first solar- of the bifacial to produce more Freiberg in Hillsboro, Oregon, industry company honored with Sunmodule Bisun than 1 megawatt ASi Industries GmbH in the United States the Silver Award for Operational of solar modules is founded in Arnstadt Excellence by the CETPM institute in a single year Logistics Production begins at Siemens Solar center opens Cell Fab 2 in Arnstadt Siemens is the first in Freiberg acquires ARCO manufacturer SolarWorld acquires Production launches at second Entire building complex – featuring cell, wafer Restart of mono- Solar, creating to offer a 25-year the wafer production of module factory in Freiberg, and module production, research and development crystallization in Siemens Solar guarantee Bayer Solar GmbH in Freiberg doubling module production center, vocational training center and new Hillsboro headquarters – is completed in Arnstadt 6 I Crystallization 1 2 1 5 2 3 3 4 5 A) MULTI-CRYSTALLINE PRODUCTION B) MONO-CRYSTALLINE PRODUCTION LEGEND 1 FILLING OF CRUCIBLE: Technicians fill a crucible with LEGEND CRYSTALLIZATION highly pure silicon, using boron to dope the silicon. MELT: 1 FILLING THE MOLDS: Semiconductor-pure silicon 2 The silicon is melted at a temperature over 1,410 degrees Celsius. is poured into a coated mold made of highly pure SolarWorld AG is the largest and oldest manufacturer At the Arnstadt and Hillsboro facilities, our monocrys- quartz. The material is positively doped with boron. In all crystallization processes, cleanliness of silicon wafers in Europe. The company’s operation in talline silicon crystals are produced via the Czochralski 3 SEED: A small, highly pure silicon mono-crystal is is crucial. Freiberg, Germany, has manufactured multi-crystalline process, which uses a seed crystal to crystallize molten dipped into the melt and partially melted. wafers for the photovoltaic industry since 1994. In fact, silicon in the form of a round mono-crystal. Arnstadt ROTATING CRUCIBLE: 2 A LOOK INSIDE A FURNACE: The silicon is melted at a 4 Via controlled cooling and temperature over 1,410 degrees Celsius. many manufacturing processes and tools commonly is the largest SolarWorld production site for mono- counter-rotation of the crystal and crucible, the used today were first developed at that facility. The pro- crystals. crystal grows continuously from the melt. 3 FINISHED BLOCK: The silicon melt is allowed to cess begins with highly pure silicon, which is melted in solidify in a controlled manner. A square block 5 FINISHED MONO-CRYSTAL: A more than 5-foot-long of multi-crystalline silicon is formed over a furnaces, crystallized under controlled cooling conditions mono-crystal with a regular crystalline structure period of three days. and doped with the element boron. This boron-doped is created over three days. silicon constitutes the positive pole of a finished solar cell. PROVEN QUALITY: Crystallization is a process step that is critical in the efficiency of a finished solar cell. The cleaner, more even and more controlled the crystallization process is, the more charge carriers can be generated from incidental light and, in turn, used at the cell contacts to transmit electricity. 8 I Wafer manufacturing 1 2 WAFER MANUFACTURING LEGEND After cooling, the silicon block or mono-crystal is cut where employees have gathered many years of exper- 1 WIRE SAWING: Ultra-thin wires, which carry an abrasive 2 FINISHING: Residue from the sawing process is carefully into columns, then further cut into wafers for use ience. Some leading wafer-sawing technologies have consisting of polyethylene glycol and silicon carbide, removed in cleaning baths. The wafers are then checked, cut the silicon block or mono-crystal into (quasi) square packed and labeled according to quality group and sent in solar cells. These wafers have the dimensions of been developed here. Modern technologies, such as columns. In the next step, those columns are cut into to solar cell production. the later solar cell, but they are not yet electrically sawing with a diamond wire, are driven forward by wafers by another type of wire saw. conductive. SolarWorld has concentrated its global SolarWorld’s engineers. wafer production activities in Freiberg, Germany, PROVEN QUALITY: Every single wafer is measured automatically and sorted by thickness, surface quality AUTHENTIC FOCUS ON SUSTAINABILITY: The SolarWorld wafer production facility in Freiberg, which won and possible damage. A technician also checks each wafer box and typically gives each a quality stamp. the German Sustainability Award, is highly efficient in terms of the consumption of water, energy and operating materials. Production byproducts are recycled and then reintroduced into the production process. Naturally, all waste water and emissions are professionally filtered. Excess heat from the furnaces is used to heat the building while a photovoltaic system on the roof provides clean electricity. 10 I Cell production 1 2 3 LEGEND 1 CLEANING: In multiple cleaning baths, damage caused by the sawing process CELL PRODUCTION is removed, and the surface of the wafer is textured. 2 DIFFUSION: A positive-negative (p-n) junction, responsible for separating electron-hole pairs, is formed via phosphorus diffusion. The wafer is now The cleanliness of production rooms and equipment The front and the rear side of the silicon wafer are a solar cell. Acid oxide is then applied to remove a phosphorus glass layer is a decisive factor in the quality and performance of covered with electrical and optical layers, which make created during diffusion. solar cells. This is why wafers are processed into solar the wafer electrically active. Subsequently, the solar 3 LASER: A laser is used to heat the cell surface in the specific areas where a cells in clean rooms at all SolarWorld sites in Germa- cell is measured and classified with precise measuring contact is to be subsequently made using silver paste. This step creates a ny and the United States. methods according to SolarWorlds’ strict specifications. selective emitter with high sheet resistance between the contact fingers and low sheet resistance below them, reducing electrical losses. AUTHENTIC FOCUS ON SUSTAINABILITY: All auxiliary materials used in production are regularly evaluated PROVEN QUALITY: Fully automated facilities, end-to-end process and material monitoring, and continuous both quantitatively and qualitatively. Every year, SolarWorld establishes environmental goals and measures to quality control throughout all production stages help ensure the incomparable standard of quality for which reduce the use of chemicals in cell production. The legal requirements for hazardous materials are scrupulously SolarWorld is known. Solar cells are produced according to the highest standards and measured according to followed at all SolarWorld production sites. Despite an increase in production volumes and therefore in material strict specifications and precise measurement methods. use, the consumption of hazardous materials was sharply reduced in 2015. 12 I Cell production 7 4 5 6 7 INTELLIGENT CELL TECHNOLOGY FOR HIGH-PERFORMANCE MODULES LEGEND 4 SURFACE TREATMENT: A blue anti-reflective coating is applied 6 EDGE ISOLATION: To electrically isolate the front from the back, With both dielectric and me- Front contacts using a chemical vapor-deposition process. This coating either a groove is made on the front along the edge of the tallic layers as well as local minimizes optical losses and achieves an electrical solar cell using a laser, or the back is etched.
Details
-
File Typepdf
-
Upload Time-
-
Content LanguagesEnglish
-
Upload UserAnonymous/Not logged-in
-
File Pages11 Page
-
File Size-