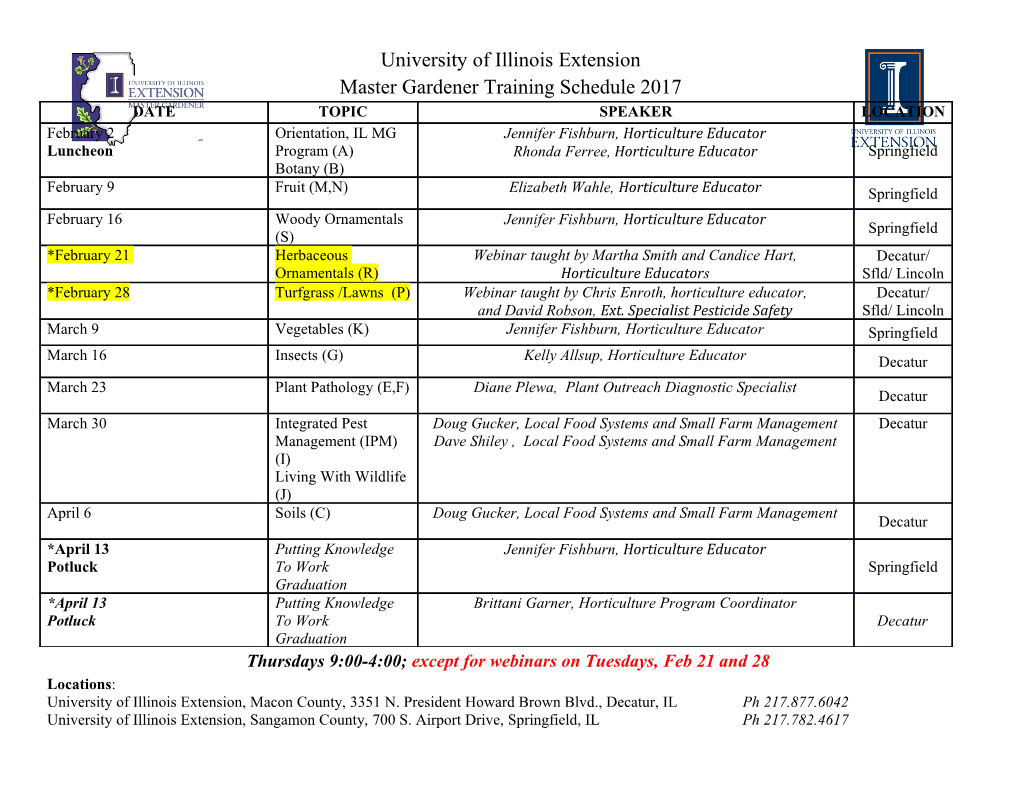
Journal of Manufacturing Processes xxx (xxxx) xxx–xxx Contents lists available at ScienceDirect Journal of Manufacturing Processes journal homepage: www.elsevier.com/locate/manpro Study effects of particle size in metal nanoink for electrohydrodynamic inkjet printing through analysis of droplet impact behaviors Yanhua Huanga,1, Liangkui Jiangb,1, Beiwen Lic, Pavithra Premaratned, Shan Jianga,*, Hantang Qinb,* a Materials Science & Engineering, Iowa State University, Ames, IA, 50011, United States b Industrial & Manufacturing Systems Engineering, Iowa State University, Ames, IA, 50011, United States c Mechanical Engineering, Iowa State University, Ames, IA, 50011, United States d Department of Physics and Engineering, Central College, Pella, IA, 50219, United States ARTICLE INFO ABSTRACT Keywords: Ink properties play a critical role in different printing techniques. However, it is not straightforward to correlate Electrohydrodynamic inkjet printing ink properties to the printing results. In this study, several parameters were identified and analyzed to evaluate Droplet impact behavior the droplet behavior in electrohydrodynamic inkjet printing. More specifically, the effects of metallic nano- Particle size particle sizes in the ink formulation were explored through the analysis of droplet impact behaviors. These Ink formulation parameters include droplet wetting diameter, height, initial impact velocity, and contact angle. With the as- Metal nanoink sistance of machine vision, a high-speed camera captured a sequence of images, which were analyzed to extract the aforementioned parameters. Under fields of gravitational force with/without electric force, four phases of ink droplet behaviors were identified. Our data suggest that with an electric force field, particle size dominates the droplet behavior in respect to contact angle and wetting diameter. The increase of particle size decreased the droplet wetting diameter with an electric field, while increased the droplet wetting diameter without the electric field applied. Larger droplet size resulted in higher bouncing frequency and lower droplet height. Furthermore, under both gravitational and electrical fields, the droplet with medium particle size (average diameter of 276 nm) had a higher impact velocity than that with small (average diameter of 140 nm) and big (average diameter of 1517 nm) particle sizes. This study contributes to fundamental understanding of particle size effects. The results will help optimize ink formulations when designing new ink materials for electrohydrodynamic inkjet printing. 1. Introduction and a time-consuming process, thus limiting this technology to print a circuit board (PCB) manufacturing [14]. The template-assist method The ability to fabricate Nano/micro scale droplet/wire with func- provides the flexibility to print multiple materials [15] as well as print tional inks plays key role in a wide range of manufacturing applications on soft flexible substrates such as Polyethylene terephthalate (PET) such as circuit boards [1], transistors [2], capacitors [3], solar cells [4], substrate [16]. It is still limited by the high cost of template fabrication new sensor developments [5], flexible electronics development and and short life cycle [17]. On the contrary, inkjet printing is a non- productions [6]. In order to precisely regulate shape, size, and se- contact printing approach that delivers pigments in the form of droplets paration distance perspective of the engineered patterns and droplet [18]. Inkjet printing is a bottom-up manufacturing approach that arrays fabrication processes, several techniques were developed and overcomes many obstacles faced by traditional subtractive manu- optimized, including template-assisted methods [7,8], optical litho- facturing [19] similar to additive manufacturing. Although inkjet graphy [9,10], and ink-jet printing [11,12]. Optical lithography has printing may not provide the same resolution as optical lithography, its been widely used in the industry because of the two to three orders of inexpensiveness still attracts a vast amount of industries [20]. magnitude higher resolution compared to other approaches [13]. There are two major categories of inkjet printing: Drop-On-Demand However, it requires expensive equipment, complex chemical reactions, (DOD) and continuous methods [21]. By eliminating the ink recovery ⁎ Corresponding authors. E-mail addresses: [email protected] (S. Jiang), [email protected] (H. Qin). 1 Co-first authors. https://doi.org/10.1016/j.jmapro.2020.04.021 Received 1 December 2019; Received in revised form 19 February 2020; Accepted 11 March 2020 1526-6125/ © 2020 The Society of Manufacturing Engineers. Published by Elsevier Ltd. All rights reserved. Please cite this article as: Yanhua Huang, et al., Journal of Manufacturing Processes, https://doi.org/10.1016/j.jmapro.2020.04.021 Y. Huang, et al. Journal of Manufacturing Processes xxx (xxxx) xxx–xxx mechanism and improving the efficiency of the ink usage, DOD method were purchased from Sigma-Aldrich (St. Louis, MO) unless specified. has become popular in the industry. Based on the droplet forming physics, DOD ink-jet printing categories into four methods: thermal, electrostatic, piezoelectric, and acoustic [21]. For the thermal method, 2.2. Particle size separation the inks shall contain highly volatile chemical solvents, so that the heater imbedded in the print head can generate solvent gas bubbles to In a 50-mL centrifuge tube, 2 g of dry tungsten nano-powder was eject ink out of the ink chamber forming the ink droplet [22]. For the mixed with 40 mL of ethylene glycol with the assistance of vertex and piezoelectric method, droplets are generated by electric potential trig- sonication for 30 min. The resulting mixture was centrifuged under gered mechanical deformation of piezoelectric material installed in the 300 rpm for 60 min. Secondly, 5 mL of ethanol was added to the cen- ink chamber. The viscosity of the inks was modified by a series of trifuged supernatant (S1) and precipitate (P1). P1 was homogenized surfactants in order to ensure droplet generation reliability [23]. The with the assistance of vertex and sonication for 10 min. S1 and P1 were electrostatic method utilizes an electric potential applied on the nozzle centrifuged under 5000 rpm for 60 min. Resulting supernatant from S1 to generate droplets by providing energy to create new surfaces where (S1S2) was further centrifuged down with 10,000 rpm for 10 min, fi droplets separated from ink mainstream. The acoustic method uses precipitating particles are classi ed as small particles (average diameter mechanical vibrations to generate droplets by resonating ink liquid of 140 nm). Resulting precipitate form S1 (S1P2) and resulting super- [24]. Ink formulation for acoustic DOD printing requires modifications natant form P1 (P1S2) were centrifuged under 10,000 rpm for 10 min to thermodynamic and acoustic behavior in addition to viscosity opti- after mixing and 10 min sonication. The resulting precipitate (S1P2- fi mizations [25,26]. Among DOD inkjet printing, electrohydrodynamic P1S2) P3 was classi ed as the medium particle (average diameter of fi (EHD) printing, also known as e-jet printing, possess unique aspects and 276 nm). The resulting precipitate from P1 (P1P2) was classi ed as a countless potential applications [27–32]. Lyu, et al. were able to print large particle (average diameter of 1517 nm). tungsten nano ink on a flexible substrate to shield x-ray radiation for electronic chips [31]. By combining the advantages of the thermal and 2.3. Ink formulation electrostatic DOD method, EHD printing requires no volatile chemicals fl present in its formulation [33], tolerates ink with exible properties The working solution defines as the aqueous solution of the ink [34]. except for the pigment. The working solution shall be prepared and To better understand the ink properties impacting the printing homogenized prior to the final mix with the pigment, which is size process, some studies have been conducted to further investigate the classified tungsten particle in this study. Based on the function and correlation between materials properties (density, surface tension, and printing method, working solution properties were optimized accord- fl viscosity) and the printing conditions (nozzle size and ink ow rate). By ingly. The working solution was optimized according to several para- analyzing high-speed droplet images, Jang et al. found that Ohnesorge meters: viscosity, density, evaporation speed, wettability, surface ten- number in the range between 4 and 14 provides droplet formability, sion. maximum allowable jetting frequency, and positional accuracy [26]. Triethylene glycol monomethyl ether (TGME) was chosen to be the ff With di erent compositions of ethylene glycol, water, and diethylene organic solvent based on its excellent solubility with most hydrophilic fl ’ fi glycol, uid s Re, We, and Oh can be engineered with a xed nozzle liquid and high evaporation rate. Polyvinylpyrrolidone (PVP) is one of fl diameter and ow rate [26]. Derby reported that with the increase of the most commonly used metallic nanoparticle surfactants, stabilizers, solid content level, relative viscosity, density will increase, which leads and adhesive additive in the ink formulation industry [42–46]. With to the decrease of Ohnesorge number [35]. Tai et al. later demonstrated excellent solubility in water and ethanol and low reactivity, PVP was the velocity of ejected droplets was governed by the Ohnesorge num- chosen to serve
Details
-
File Typepdf
-
Upload Time-
-
Content LanguagesEnglish
-
Upload UserAnonymous/Not logged-in
-
File Pages7 Page
-
File Size-