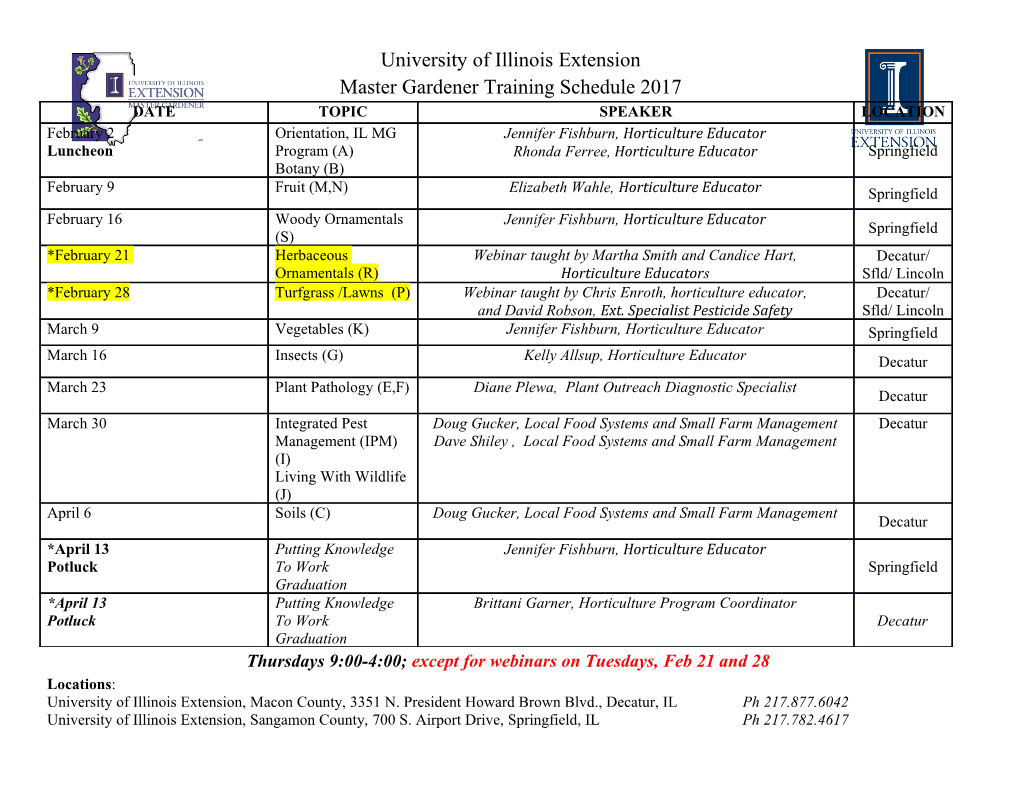
Accessible Motorcycle Sidecar: Fabrication & Assembly Manual Process Sheet Revision: A Page 1 of 10 P18031-MAN-001 1.0 PURPOSE The purpose of this document is to explain all processes necessary for the fabrication and assembly of the P18031 Wheelchair accessible Ural Patrol motorcycle sidecar. 2.0 SCOPE This document summarizes all manufacturing steps to build the complete assembly, some sections are left to the discretion of the operator and will depend on available facilities. 3.0 RESPONSIBILITY MSD Team P18031 4.0 REVISION HISTORY 4.1 Revision A 4.1.1 Author: Dobhran Black 4.1.2 Change Notes: Initial Release 5.0 DEFINITIONS Word Definition Cope Create a cylindrical “mouth” at the end of a tube 6.0 TOOLS, GAUGES, FIXTURES 6.1 Tube bender 6.2 Tube coping tool 6.3 Mig welder 7.0 SAFETY REQUIREMENTS 7.1 Wear proper eye protection with side shields during all machining ops. 7.2 Use proper PPE for welding 8.0 Tube Frame Fabrication 8.1 Cut all tube elements referenced on [BODY_FRAME_SH1] & [DOOR_FRAME_SH1]. NOTE: All lengths provided on these sheets are maximum overall lengths, usually including 0.375” of coping overhang at each end. Operator may want to cut tube lengths 0.5-1” longer than specified to avoid scrapping the tube due to a bad cope. Accessible Motorcycle Sidecar: Fabrication & Assembly Manual Process Sheet Revision: A Page 2 of 10 P18031-MAN-001 8.2 Bend all tube elements which require bending, referencing their individual item level drawings. NOTE: All bends are 2” centerline radius. 8.3 Cut or cope all tube ends for assembly. Cut and coping angles can be obtained either from item level drawings or from [BODY_FRAME_SH2] & [DOOR_FRAME_SH2] dimensions. NOTE: Intersections of >2 items may require an iterative approach for proper fitment. 8.4 Using Aluminum Jig with vertical pins to ensure proper perpendicularity of the frame and prevent deformation during the build process, tack weld the base frame together. 8.5 Verify correct dimensions of the base are being held, then complete welding of the base frame. 8.6 Complete full welds of door frame once dimensions are verified. 8.7 Cut tack welds between door and body frame. 8.8 Clean up welds and exposed burrs as needed. 8.9 Repeat steps 8.4 through 8.8 for the Door Frame, in order to offset for uneven cross bars, pile up aluminum blocks on jig to get the frame level. 9.0 Skin Fabrication 9.1 Use provided DXF files to cut skin sections on water jet (or equivalent). 9.2 Remove any burrs from edges and sand off any scale or rust. 9.2 Spot weld or braze (maximum 3” spacing) skin sections to tube. Ensure skin is at least tangent or overhangs tube on all sides. Weld or braze together free hanging skin segments from around engine head, operator may insert steel stiffener to strengthen weld along internal edges. Place fillet welds along diagonal tube of door to minimize sheet rattle. 9.3 Sand down all exposed welds until flush. 9.4 Insert filler between all gaps in skin and clean up until there are no unsightly gaps in exterior. 9.5 Weld on steel stiffeners to skin on unsupported areas as needed. Accessible Motorcycle Sidecar: Fabrication & Assembly Manual Process Sheet Revision: A Page 3 of 10 P18031-MAN-001 9.6 Cut off exposed edges of door skin until there is a gap approximately ½ the width of the elastomer. Use Exacto knife (or equivalent) to make incision into o-profile elastomer. Heat up exposed skin with blowtorch, then press cut side of elastomer onto heated edge until all possible pinch points are covered. Alternatively the elastomer can be glued in place. 10.0 General Build 10.1 Fabricate all accessory parts according to drawings. NOTE: All elements which support significant forces must be of min 12ga thickness. NOTE: Measure seat bolt pattern and make necessary alterations to Adapter Plate to fit. 10.2 Place assembled door on top of base so that the front ends are tangent to each other. Place the piano-hinge over this edge and mark the hole locations. Drill and bolt the holes one each side, then stitch weld around the edges. Accessible Motorcycle Sidecar: Fabrication & Assembly Manual Process Sheet Revision: A Page 4 of 10 P18031-MAN-001 10.4 Weld or Bolt Strike Plate and Handle mounts to outside of door and body skin so that they form a single plane with a max 1/4”-1/2” gap when the door is fully closed. NOTE: It may be necessary to insert steel stiffener into skin to increase stiffness under handle mounts. Accessible Motorcycle Sidecar: Fabrication & Assembly Manual Process Sheet Revision: A Page 5 of 10 P18031-MAN-001 10.4 Weld spring mounts to junctions shown in the figure below: Thread one end of each gas spring into these mounts, then raise the door until it is nearly balanced, mark where the other ends of the springs rest on the base tube frame. Weld the other mount at this location and thread in the spring. Accessible Motorcycle Sidecar: Fabrication & Assembly Manual Process Sheet Revision: A Page 6 of 10 P18031-MAN-001 10.5 Bleed each spring using the included allen key, rotating the key one quarter turn and holding for approximately 2 seconds at a time. Make sure to bleed both springs as equally as possible. After each spring has been bled, attempt to close the door using minimal force. Repeat until door closes with minimal force. 10.6 Remove windshield from existing Ural Sidecar and hold mounts against sheet metal of the door nose at an acceptable location relative to the rider and the bike handles (some locations will interfere with rider’s ability to turn handlebars), then mark hole locations, drill, and bolt. Mark where the holes in the cowling rest against the nose, then weld buckles at those locations. Note: in image below buckles are in wrong location due to the windshield being relocated. 10.7 Weld the hasp for the trunk lid the the center of the rear crossbar, then hook the toggle over it, mark the bolt hole locations on the lid, drill and bolt them. Accessible Motorcycle Sidecar: Fabrication & Assembly Manual Process Sheet Revision: A Page 7 of 10 P18031-MAN-001 10.8 Attach trunk hinge in same way as in 10.2, marking hole locations and drilling. Note: Welding is not necessary for trunk hinge. 10.8 Weld Shock strip so that its holes are 36 ¼” away from the center of the front mounts (rear shocks are approximately 3’ rear of the front bar). Drill through sheet metal where shock strip holes are. Bolt Shock strip to Shock-Squares and torque down. 10.9 Mount V-Risers to front crossbar of bike frame. Mark where they line up with tub floor and cut out slots for them to pass through. Grind down inside edges of V-Risers to allow them to press-fit onto tubes. 11.0 Ingress-Egress System Assembly 11.1 Place turntable onto 2 item 18 base crossbars, forward of the drive shaft clearance, so that it is centered between the two sides of the sidecar (measuring beyond cut out). When turntable is verified centered, weld it in place. Accessible Motorcycle Sidecar: Fabrication & Assembly Manual Process Sheet Revision: A Page 8 of 10 P18031-MAN-001 11.2 Lay out ingress-egress system components, Note that these are only used in the prototype and are replaced by a single component in the MK2 and all future designs. Weld a single ½-13 nut to the underside of the base at the location where you can see the carriage bolt below to allow the carriage bolt to thread through. Bolt base onto turntable and torque down. Bolt rails to top, then bolt tubes between top and base, being sure to torque down all bolts. Ensure that final bolt hole on the forward end of the rail lays above flush so that it stops the carriage from derailing off the end. 11.3 Thread carriage bolt (or equivalent uncoated steel bolt) through nut placed on top of base until aluminum part presses into floor, locking system rotation, then tighten top nut until it locks down tongue (not shown). Make sure that both bolt and nut can lock and unlock in one quarter rotation, then spot weld nut to bolt so that they rotate in tandem. Add box wrench to assembly to act as lever. Accessible Motorcycle Sidecar: Fabrication & Assembly Manual Process Sheet Revision: A Page 9 of 10 P18031-MAN-001 11.4 Assemble adapter plate to carriages and tongue, then slide onto rails. Finally, bolt seat onto adapter plate. Note: The adapter plate shown does not reflect the ideal state. If available make adapter plate out of a single sheet of 12ga steel or equivalent, this adapter plate was made with available materials. Note also that the MK2 plate should have a slot down the center to serve the purpose of the tongue in this prototype. 12.0 Final Mounting 12.1 Before mounting V-Risers cut out ~⅝” wide strips of flat ~1/16” thick rubber material and pack into space between Tube retainers and V-Riser, and between Riser bottom and Riser, then bolt in and torque down. If V-Riser rattles or does not hold tight in anyway, unbolt and add more rubber sheet. Note: Riser bottom was erroneously threaded in prototype, so if it isn’t holding tight just remove, back the bolts off to decrease spacing, then bolt back on.
Details
-
File Typepdf
-
Upload Time-
-
Content LanguagesEnglish
-
Upload UserAnonymous/Not logged-in
-
File Pages10 Page
-
File Size-