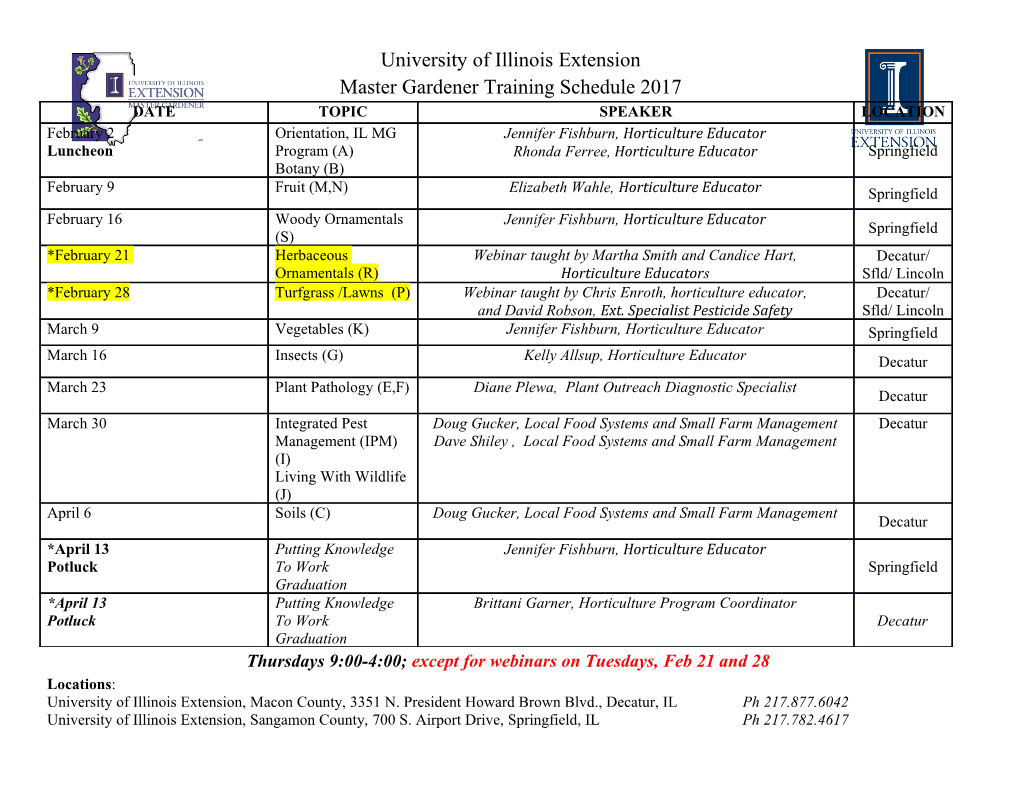
PRELIMINARY DESIGN AND ANALYSIS OF AN ENERGY STORAGE FLYWHEEL ___________________________________ A Dissertation Presented to the Faculty of the School of Engineering and Applied Science University of Virginia ___________________________________ In Partial Fulfillment of the requirements for the Degree Doctor of Philosophy by Arunvel Kailasan May 2013 APPROVAL SHEET This dissertation is submitted in partial fulfillment of the requirements for the degree of Doctor of Philosophy in Mechanical and Aerospace Engineering ___________________________________ Arunvel Kailasan This dissertation has been read and approved by the Examining Committee: __________________________________ Timothy Dimond, Advisor __________________________________ Houston Wood, Chairman __________________________________ George Gillies __________________________________ Andres Clarens __________________________________ Wei Jiang Accepted for the School of Engineering and Applied Science: _________________________________ James H. Aylor, Dean May 2013 Abstract Energy storage is becoming increasingly important with the rising need to accommodate a greater population. Flywheel energy storage systems store kinetic energy by constantly spinning a compact rotor in a low-friction environment. When short-term back-up power is required as a result of utility power loss or fluctuations, the rotor's inertia allows it to continue spinning and the resulting kinetic energy is converted to electricity. Unlike the fossil-fuel power plants and batteries, the Flywheel based energy storage systems does not emit any harmful byproducts during their operation and have gained a lot of interest recently. A typical flywheel system is comprised of an energy storage rotor, a motor-generator system, bearings, power electronics, controls and housing. Conventional flywheel designs have a large diameter energy storage rotor attached to a smaller diameter section which is used as a motor/generator. The cost to build and maintain such a system can be substantial. The goal of this thesis is to successfully design a 1KW-hr inside-out integrated ROMAC flywheel energy storage system using a single uniform composite rotor to perform the functions of energy storage, motor and generator. Active Magnetic bearings (2 radial and thrust) will be designed to support the flywheel. The weight savings from this type of design can be substantial, and additional advantages include lower component count, reduced material costs, lower mechanical complexity, and reduced manufacturing costs. The first part of the thesis deals with preliminary calculations, design and finite element analysis of the flywheel components. The subsequent parts of the thesis involve system level analyses to ensure the structural and functional integrity of the ROMAC flywheel. Acknowledgement I am sincerely and ever grateful to Prof. Paul Allaire for accepting me into the Rotating Machinery and Controls Laboratory (ROMAC). The technical and social experiences that I have gained under his guidance will last a lifetime. I am thankful to Dr. Timothy Dimond for his full- fledged support and guidance throughout my time in ROMAC. I am especially thankful for his advising and mentoring at a very difficult time. This thesis would have not been made possible without both Prof. Allaire and Dr. Dimond. I would also like to mention my thesis committee Prof. Houston Wood, Prof. George Gillies, Prof. Andre Clarens and Dr. Wei Jiang for providing me with their valuable insights to shape up this thesis. I would like to thank all my colleagues who helped me shape up this thesis. I would like to specially mention Mr. Jason Kaplan for his time in helping me with the ROMAC codes and Mr. Parinya Ananthachaisilp for his enthusiasm and patience in helping me understand the controller design. I shall always be indebted to my family for their constant support and encouragement during this time period. I would like to thank my wife, Subhashini Vel, for being there for me whenever I needed help or a shoulder. I am thankful to my parents, Muthaiyan Kailasan and Thangamani Kailasan, for showing me the right path when in doubt. I would also like to thank my sister, Dr. Kruthikaveni Kailasan, and my brother in law, Dr. Vinodh kumar, for being a pillar of strength and support. Special thanks to my nephew, Vishaal Vinodhkumar, for helping me balance work and play. I would like to end my note by mentioning that my graduate life at ROMAC and UVA has provided me with the necessary tools to succeed in my career and more importantly, to succeed as a human being. Table of Contents 1 Introduction ........................................................................................................................... 18 1.1 Problem Statement ......................................................................................................... 20 1.2 Thesis Objective ............................................................................................................. 21 1.3 Scope and novel contributions ....................................................................................... 22 1.4 Thesis Outline ................................................................................................................ 24 2 Flywheels- State of the Art and Literature Review .............................................................. 26 2.1 Introduction .................................................................................................................... 26 2.2 Components of a flywheel energy storage system ......................................................... 28 2.2.1 Rotor ....................................................................................................................... 29 2.2.2 Bearings .................................................................................................................. 29 2.2.3 Motor-Generator ..................................................................................................... 30 2.2.4 Power Electronics ................................................................................................... 30 2.2.5 Controls and Instrumentation .................................................................................. 31 2.2.6 Housing ................................................................................................................... 31 2.3 Description of commercial flywheel systems ................................................................ 32 2.3.1 Beacon Power ......................................................................................................... 33 2.3.2 Powerthru (Formerly Pentadyne) ............................................................................ 35 2.3.3 Kinetic traction........................................................................................................ 37 2.3.4 Active Power Systems ............................................................................................ 39 2.3.5 Vycon ...................................................................................................................... 40 2.3.6 Piller- Powerbridge ................................................................................................. 43 2.3.7 TSI Tribology systems ............................................................................................ 44 2.3.8 AFS Trinity Systems ............................................................................................... 46 2.3.9 Critique of commercial flywheel systems............................................................... 48 2.4 Past flywheel research .................................................................................................... 50 2.5 Current flywheel research .............................................................................................. 52 2.5.1 Non-contact bearings research ................................................................................ 54 2.5.2 Control Scheme Research ....................................................................................... 58 2.5.3 Composites Research: ............................................................................................. 59 2.5.4 Applications research .............................................................................................. 60 3 ROMAC Flywheel Design Characteristics ........................................................................... 62 3.1 Proposed Flywheel Design ............................................................................................. 63 3.1.1 Different components of ROMAC flywheel design ............................................... 64 3.1.2 Proposed Applications of ROMAC flywheel ......................................................... 69 3.2 Major limiting factors of flywheel design ...................................................................... 71 3.3 Preliminary sizing of the flywheel ................................................................................. 75 3.3.1 Energy density and specific energy ........................................................................ 75 3.4 Preliminary check ........................................................................................................... 79 4 Flywheel Mechanical System Components .......................................................................... 80 4.1 Rotor ..............................................................................................................................
Details
-
File Typepdf
-
Upload Time-
-
Content LanguagesEnglish
-
Upload UserAnonymous/Not logged-in
-
File Pages248 Page
-
File Size-