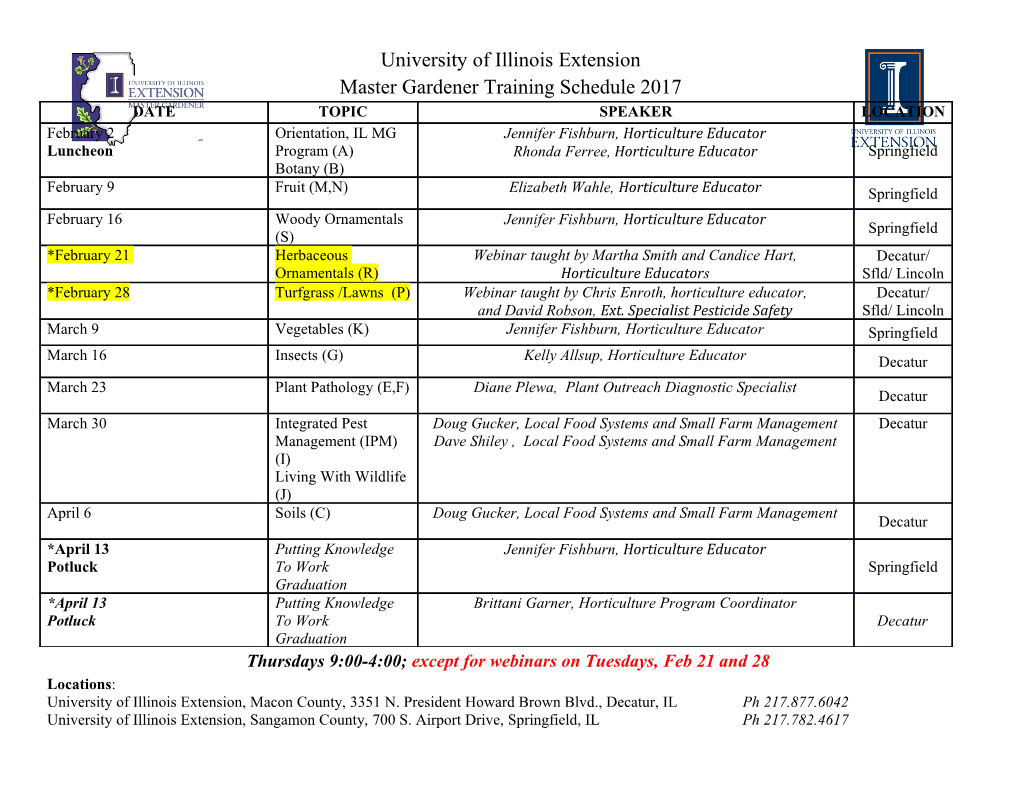
Accepted Manuscript: for final journal publication see https://doi.org/10.1016/j.tsf.2018.11.028 1 Simultaneous chemical vapor deposition and thermal strengthening 2 of glass 3 4 Peter Sundberg1, Lina Grund Bäck1, Robin Orman2, Jonathan Booth2, Stefan Karlsson1* 5 1RISE Research Institutes of Sweden, Built Environment Division, Glass Section, SE-351 96 Växjö, 6 Sweden 7 2Johnson Matthey Technology Centre, Blounts court, Sonning Common, Reading, RG4 9NH, United 8 Kingdom 9 *Corresponding author: [email protected] 10 11 Keywords: Chemical vapour deposition, thermal strengthening, crack resistance, contact angle, 12 hardness 13 14 Declaration of interest: none. 15 16 Abstract 17 In the current paper we present a concept combining metal organic chemical vapor deposition with 18 thermal strengthening process of flat glass. As the flat glass is heated to be thermally strengthened, 19 which takes a few minutes, there is an opportunity for performing a surface modification. We describe 20 the application of transparent and amorphous Al2O3 thin films during the thermal strengthening process. 21 Al2O3 was chosen due to the following desirable properties: increased surface mechanical properties 22 and increased chemical durability, the latter has not been investigated in the current paper. The residual 23 surface compressive stresses after performed strengthening of the coated glasses were quantified to 24 be in the range of 80-110 MPa. The Al2O3 content in the surface was measured using the Surface 25 Ablation Cell employed with Inductively Coupled Plasma Atomic Emission Spectroscopy and found to 26 be at least doubled at the surface and having an increased Al2O3 content at least 0.5 µm underneath 27 the glass surface. During the surface reaction, sodium is migrating to the surface giving a hazy salt layer 28 on the glass which can easily be washed off with water. The applied coatings are transparent and 29 provide increased surface hardness and crack resistance at low indentation loads. At higher indentation 30 loads the interaction volume is larger and displays the same effect on the surface mechanical properties 31 as for thermally strengthened glass. The contact angle with water compared to annealed float glass is 32 significantly increased from 5° to 45° due to the different surface chemistry and surface structure. 33 1. Introduction 34 Glass is an essentially strong material. It is evident from its strength calculated from the bonds forming 35 the vitreous network or its strength under compressive loads [1]. However, due to unavoidable surface 36 defects, glass is brittle for tensile loads. The two most common methods of strengthening glass involve 37 pre-stressing the glass surface with compressive stresses by essentially either physical or chemical 38 means. Physical strengthening is more commonly called thermal strengthening (or tempering). 39 Tempered glass is made by uniformly heating glass to a temperature of up to 700°C and immediately 40 cooling down [2]. The hot glass undergoes a rapid cooling process by a uniform and simultaneous blast 41 of air on both surfaces. This gives a solid surface that contracts lesser than the interior that still has a 42 temperature above the glass transition which upon further cooling results in a permanent parabolic 43 stress profile [3]. Chemical strengthening of glass most often means exchanging smaller ions in glass 44 surface for larger ions by a molten salt bath [4] or by a spraying process [5]. It generally gives higher 45 strength than thermally tempered glass but requires more time (hours instead of minutes), the upscaling 46 is complicated, and therefore comprise a higher cost. Thermal strengthening of glass has in general two 47 major drawbacks, the frangibility (the explosive behavior upon fracture) [1] and spontaneous fracture 48 due to NiS inclusions [6]. Thinner thermally strengthened glass is possible to be made by using 1(7) For final journal publication see https://doi.org/10.1016/j.tsf.2018.11.028 1 increased rapidity in the cooling [7]; however, at some point thermally strengthened glass also needs 2 increased surface mechanical properties. Therefore, it can be very favorable to combine thermal and 3 chemical strengthening in the same process. The traditional chemical strengthening is though not 4 possible to combine with thermal strengthening [8]. 5 There are also other methods to improve the strength of glass as well; these can also be categorized 6 as chemical methods to strengthen glass and involves gases that react with the glass surface. Some of 7 these methods are summarized in Tab. 1. To be able to thermally strengthen we require a heating cycle 8 as shown in Fig. 1. At temperatures as high as 600-700 °C there is an opportunity for enhancing the 9 surface mechanical properties. Rancoule describes benefits and problems of adding gaseous SO2 10 during the tempering process of float glass [17]. The formation of sodium sulfate is said to “benefit for 11 the contact surface longevity” i.e. being a lubricant [10] but can also lead to defects [17]. The yield of 12 the sodium sulfate depends on moisture, the temperature and the concentration of the gas during the 13 process. No details of the SO2 additions were given in the cited references. In the current paper we 14 investigated combining chemical vapor deposition for providing amorphous Al2O3 thin films during the 15 thermal strengthening process [18, 19]. Amorphous Al2O3 thin films provide various desirable properties 16 including improved chemical durability and surface mechanical properties [18-20]. 17 18 2. Experimental 19 Conventional soda-lime-silicate float glass in the size of 70×70 mm2 with thicknesses of 4 and 2 mm 20 were used with a typical composition as given in ref [21]. The general experimental procedure is given 21 in Fig. 2. The flat glass was heated in the furnace up to 640-680 °C. At higher temperatures the glasses 22 became non-flat and at lower temperatures the strengthening level became too low due to insufficient 23 difference between the temperature of the surface and the interior upon cooling. For general guidance 24 about thermal strengthening in experimental details please have a look in Barr’s Handbook [22]. The 25 Al2O3-precursor was Al-(acac)3, from Strem Chemicals, which is a commonly used precursor for 26 Metalorganic Chemical Vapor Deposition (MOCVD) [19]. The Al2O3-precursor was partly dissolved in 27 isopropyl alcohol (IPA) at elevated temperature (about 70 °C) using a magnetic stirrer with the 28 proportions of approximately 3.5:96.5 weight ratio of Al2O3-precursor and IPA respectively. The solution 29 was then sprayed manually and as homogeneous as possible on to the grating made of stainless steel 30 using a Preval sprayer at the constant spray pressure 4.4 bar and driven by the propellant gases, 31 dimethyl ether, propane and isobutane. The spray system is an aerosol-based spray system that allows 32 custom-made solutions to be turned into sprayable material. The gratings were then dried in a heating 33 cabinet at 105 °C (Thermoscientific’s Heratherm oven OMH100) making the IPA to evaporated and only 34 leaving deposited Al2O3-precursor. The gratings’ difference in weight was recorded before and after the 35 spray and drying process so that the amount of applied Al2O3-precursor on the grating could be 36 determined. The amounts of applied Al2O3-precursor on the gratings, in dried state, were in the range 37 of 100-200 mg. The size of the gratings was 10x11 cm2 for each side of the flat glass so approximately 2 38 0.5-1 mg/cm Al2O3-precursor was deposited on the grating. The grating together with an untreated float 39 glass sample were then put into a hot (640-680 °C) muffle furnace (Naber Industrieofen N2OH) with 40 normal air atmosphere as illustrated in Fig. 2A, so that the flat glass on both sides was located <1 cm 41 from the grating. In the furnace the glass and the grating heats up, the glass surface reaches the furnace 42 temperature after approximately 5 minutes, the Al2O3-precursor vaporizes creating an Al-(acac)3/air 43 atmosphere. The Al2O3-precursor starts to evaporate above its boiling temperature 189 °C [19]. As the 44 Al2O3-precursor reaches the hot glass surface it immediately decomposes and forms an Al2O3 thin film. 45 Please note that all Al2O3-precursor do not end up forming a thin film on the glass. The glass and the 46 grating were let in the furnace for 20 minutes in total as was predetermined from thermal strengthening 47 tests. The reaction was verified to be completed by weighing the grating afterwards. After 20 minutes 48 the sample and grating were removed and placed into a stream of air having an ambient temperature, 49 see Fig 2B. The air flow generators were leaf blowers from Ryobi (3 kW) providing an air flow of 16 50 m3/min. The rapidly cooled glass reach room temperature within 10-20 seconds. The weight change of 51 the samples was not recorded as the weight change of the glass could not only have been prescribed 2(7) For final journal publication see https://doi.org/10.1016/j.tsf.2018.11.028 1 to be due to the thin film deposition but also sodium migration to the surface (see results section). The 2 thermal strengthening level of the tempered samples was measured using SCALP-03, GlasStress Ltd 3 [23]. All samples were cleaned with deionized water prior to all type of characterizations and in all 4 characterizations was the air-side investigated. 5 6 The UV-Vis transmittance spectra were measured using the spectrophotometer Lambda 25 from Perkin 7 Elmer.
Details
-
File Typepdf
-
Upload Time-
-
Content LanguagesEnglish
-
Upload UserAnonymous/Not logged-in
-
File Pages17 Page
-
File Size-