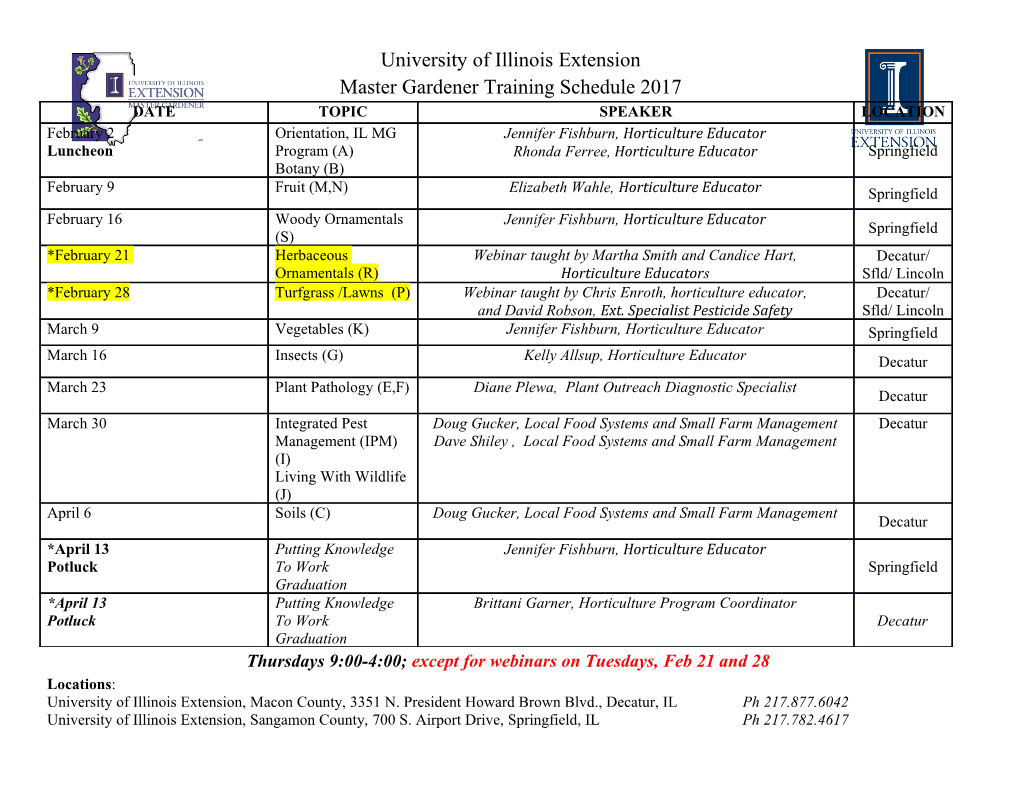
ISSN: 1402-1757 ISBN 978-91-7439-XXX-X Se i listan och fyll i siffror där kryssen är LICENTIATE T H E SI S Department of Engineering Sciences and Mathematics Division of Energy Engineering ISSN: 1402-1757 ISBN 978-91-7439-225-8 Black Liquor Gasification Luleå University of Technology 2011 Burner Characteristics and Syngas Cooling Mikael Risberg LICENTIATE THESIS Black Liquor Gasification Burner Characteristics and Syngas Cooling Mikael Risberg Division of Energy Engineering Department of Engineering Sciences and Mathematics Luleå University of Technology SE-971 87 Luleå, Sweden [email protected] March 2011 Printed by Universitetstryckeriet, Luleå 2011 ISSN: 1402-1757 ISBN 978-91-7439-225-8 Luleå 2011 www.ltu.se Abstract Black liquor gasification at high temperature is a promising alternative to the conventional recovery boiler process used in chemical pulp mills today. Compared to a conventional recovery boiler a black liquor gasifier can increase the total energy efficiency of a chemical pulp mill and produce a synthesis gas that can be used for production of motor fuel. In Piteå, a 3 MW or 20 tons per day entrained flow pressurized black liquor gasification development plant has been constructed by Chemrec at Energy Technology Center. The plant has been run more than 12 000 h since 2005. One of the key parts in the gasification process is the spray burner nozzle where the black liquor is disintegrated into the hot gasifier as a spray of fine droplets. In this thesis the spray burner nozzle was characterized with high speed photography in order to visualize the atomization process of black liquor. The results showed that black liquor forms non-spherical and stretched ligaments and droplets with the considered nozzle. Comparison of the results with atomization of a syrup/water mixture showed that the results were qualitatively very similar which means that a syrup/water mixture can be used instead of black liquor for burner optimization experiments. This is a considerable experimental simplification. Also spatially resolved measurements of the gas composition in the development plant with a water cooled quench probe have been performed. From the gas composition measurement and the spray visualization it has been showed that the preheating of black liquor has a significant influence on the gas composition. Another important part in the gasification plant is the counter-current condenser where the gas is cooled and the water content in the gas is condensed away in vertical tubes that are cooled on the outside by a counter-current flow of water or steam. In this thesis a computational fluid dynamics model of the counter-current condenser have been developed. The model consists of a two-phase fluid model on the tube-side of the condenser and a single phase model of the shell side. Predictions from the model are in excellent agreement with temperature measurements from the condenser used in the 3 MW Black Liquor Gasification development plant. However, more validation data is necessary before a definite conclusion can be drawn about the predictive capability of the code, in particular with respect to scale up with about two orders of magnitude for commercial size gas coolers. Preface The author gratefully acknowledges the Swedish Energy Agency, Mistra, Smurfit Kappa Kraftliner AB, SCA Packaging AB, Södra’s Research Foundation, Sveaskog AB, Chemrec AB and the County Administrative Board of Norrbotten for funding this work through the BLG II research program. Partial funding has also been received through the Bio4Energy program funded by the Swedish government through the Swedish Energy Agency. I would like to thank my supervisors Rikard Gebart and Lars Westerlund for their guidance and support throughout my work. Furthermore I would like to thank my colleagues at the division of Energy Engineering and Energy Technology Centre for creating a good work environment and a friendly atmosphere. A special thank to Magnus Marklund for the help with the work in paper A. Introduction ................................................................................................................................................ 1 Black liquor recovery ............................................................................................................................. 1 Black liquor gasification ....................................................................................................................... 3 Burner characterization ....................................................................................................................... 4 Connection between burner spray characteristics and syngas composition ......................................................................................................................... 6 Counter-current condensation .......................................................................................................... 7 Conclusions ................................................................................................................................................ 10 References .................................................................................................................................................. 11 APPENDED PAPERS A. Risberg, M. Marklund, M. 2009 Visualization of gas-assisted atomization of black liquor and syrup/water mixtures at elevated ambient pressures. Atomization and Sprays. 19 ,10, p.957-967 B. Gebart, R., Carlsson, P. , Grönberg, C. Marklund, M. Risberg, M., Wiinikka, H. Öhrman, O. 2009 Spatially resolved measurement of gas composition in a pressurised black liquor gasifier. Environmental Progress and Sustainable Energy. 28, 3, p.316-323. 8p. C. Risberg, M. Gebart, R. 2010 Numerical modeling of counter-current condensation in a Black Liquor Gasification plant. Manuscript Introduction Due to the increased energy demand in the world today and the alarming global warming it has become very important to expand the use of renewable and climate neutral fuel such as wood or biomass in general. From wood one can produce paper via e.g. chemical pulping and in Sweden 10.9 million tons of paper was produced in 2009 or about 2.8% of the total world paper production (Skogsindustrierna 2010). In Sweden the total energy demand from the pulp and paper industry was 72.2 TWh, which corresponds to 12.7% of the total energy used in Sweden 2008 (Energimyndigheten 2010). At the same time the pulp and paper industry produces black liquor with a total fuel value of about 40 TWh/year as a side stream from the pulping process. Because of this, the pulp and paper industry play an important role for the energy system in Sweden both as a consumer and producer of energy. By increasing the efficiency of the energy recovery systems in the pulp and paper mills more energy can be recovered from the mills and this will greatly affect the national energy balance. One technique is to replace the conventional black liquor recovery boiler used in the mills today with a black liquor gasifier. Compared to today’s recovery boiler technique, a black liquor gasifier can increase the total energy efficiency of the mill’s recovery cycle and produce a synthesis gas for production of high value end products, e.g. methanol or dimethylether (Lindblom, Landälv 2007). The potential for motor fuel production from black liquor in Sweden is to replace about 25% of the current consumption of gasoline and diesel. For this to be possible the mills need to import additional biomass. However the quality requirements on this biomass are low and estimates have shown that felling residues that are unused today could fill this need. Black liquor recovery In figure 1, the kraft pulping process is schematically described. First wood chips are fed into a digester where the cellulose fibers are separated from the wood immersion in hot white liquor. White liquor is a strong aqueous solution consisting of sodium sulfate and sodium sulfide that neutralizes the organic acid and the bounding lignin in wood and separates the fibers that later become pulp. The pulp is used to produce paper and the remaining by-products (lignin, cooking chemical, etc.) leave the digester as weak “black liquor”. The black liquor is then transformed back to white liquor via a sequence of steps. First the black liquor is sent through a series of evaporators to increase the solid content in order to make it suitable for combustion. In the evaporators the black liquor solid content is increased from about 15%wt to about 70-75%wt. The black liquor is then fired in a recovery boiler where it is thermochemically converted to an inorganic smelt and combustion products. The smelt from the recovery boiler is then dissolved into water and forms “green liquor”. The green liquor then goes through a causticising process to convert green liquor back to white liquor. Then the resulting white liquor is recycled into the digester. The concentrated black liquor that goes into the recovery boiler consists of about 30% water, 30% valuable inorganic cooking chemicals and 40% lignin and other organic matter separated from the wood. The higher heating value is about 14 MJ/kg solids. Typically, a large pulp mill will produce about 2000 ton/day of black liquor corresponding to about 300 MWth. 1 Figure 1. Schematic drawing of a recovery cycle in a conventional chemical kraft pulping process. It’s important to recover both chemicals and energy from the black liquor for economical and environmental purposes. Therefore, the recovery cycle
Details
-
File Typepdf
-
Upload Time-
-
Content LanguagesEnglish
-
Upload UserAnonymous/Not logged-in
-
File Pages70 Page
-
File Size-