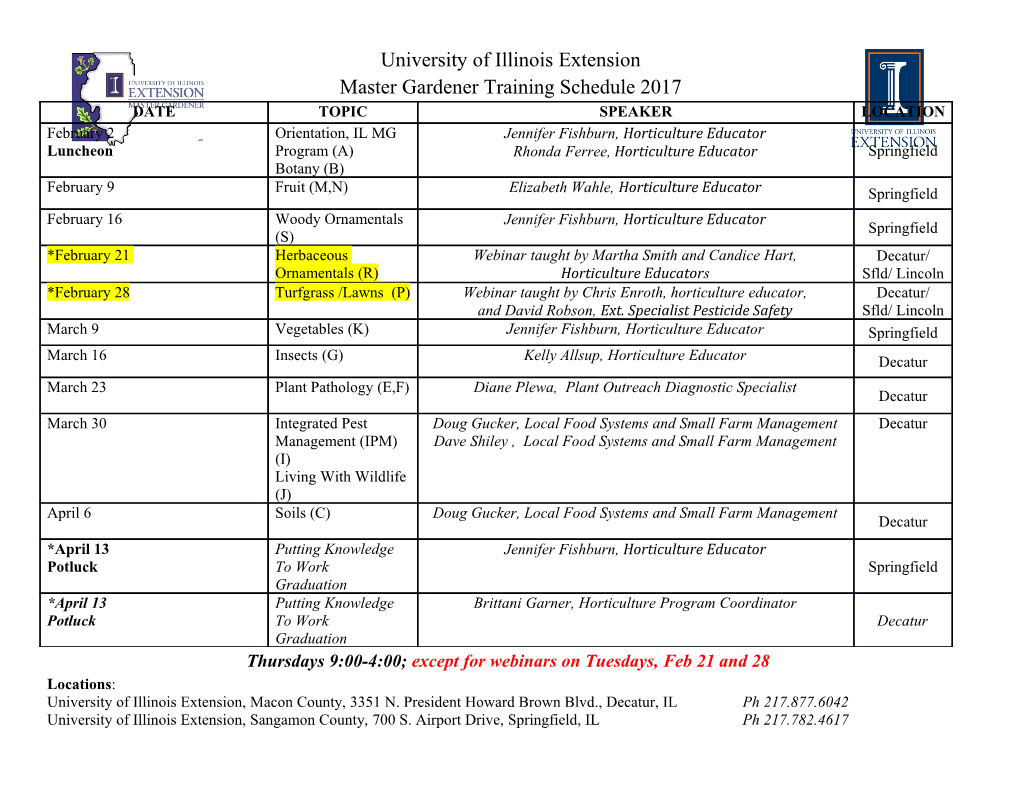
Gasworks Profile C: Water Gas Plants Gasworks Profiles Gasworks Profile A: The History and Operation of Gasworks (Manufactured Gas Plants) Contents in Britain Gasworks Profile B: Gasholders and their Tanks Gasworks Profile C: Water Gas Plants 1. Introduction................................................................................... C1 Gasworks Profile D: Producer Gas Plants 2. The Early Development of Water Gas..........................................C1 3. Different Systems Used for the Manufacture of Water Gas......... C3 ISBN 978-1-905046-26-3 © CL:AIRE 2014 4. The Development of Intermittent Water Gas Plants..................... C3 5. The ‘Run’ and ‘Blow’..................................................................... C5 Published by Contaminated Land: Applications in Real Environments (CL:AIRE), 6. Types of Intermittent Water Gas Plant......................................... C7 32 Bloomsbury Street, London WC1B 3QJ. 7. Blue-Water Gas Plants................................................................. C8 8. The Operation of an Intermittent Carburetted Water-Gas Plant... C9 All rights reserved. No part of this publication may be reproduced, stored in a retrieval 9. Types of Fuel used....................................................................... C16 system, or transmitted in any form or by any other means, electronic, mechanical, photocopying, recording or otherwise, without the written permission of the copyright 10. Oil Feedstocks used to enrich Water Gas.................................... C17 holder. All images courtesy of the National Grid Gas Archive, unless stated. 11. Oil Gas......................................................................................... C18 12. Water Gas Composition............................................................... C19 The Gasworks Profiles have been prepared by: 13. The Advantages and Disadvantages of Water Gas Systems in Dr Russell Thomas, Gas Manufacture.......................................................................... C19 Technical Director 14. Contaminants Associated with Water Gas Plants........................ C20 Parsons Brinckerhoff 15. Selected Bibliography……………………………………………….. C22 Redland, Bristol, UK Tel: 0117-933-9262 Email: [email protected] or [email protected]. The author would like to thank the National Grid Gas Archive, Warrington, UK, without whose assistance this publication would not be possible. The author would also like to thank Maria Laffey of Parsons Brinckerhoff and John Horne of IGEM Panel for the History of the Industry, for their assistance in reviewing this document. Disclaimer: The purpose of this document is to act as a pointer to the activities carried out on former water gas plants. The Author and Publisher will not be responsible for any Units loss, however arising, from the use of, or reliance on, this information. This document All units used in this profile have been converted to SI Units. Some are also shown as (‘this publication’) is provided ‘as is’, without warranty of any kind, either expressed or their former imperial units, as the data was taken from documents using this format. One implied. You should not assume that this publication is error-free or that it will be unit commonly used in the gas industry and still in partial use is the British Thermal Unit suitable for the particular purpose which you have in mind. The Author and Publisher (Btu), a common unit for the measurement of energy in the gas industry. 1 Btu is assume no responsibility or liability for errors or omissions in this publication. Readers 3 equivalent to 1.055 Kilojoules (0.001 MJ). The Btu was often expressed as Btu/ft ; this are advised to use the information contained herein purely as a guide and to take 3 has now been replaced by the Megajoule per cubic metre, expressed as MJ/m . appropriate professional advice where necessary. 1. Introduction This profile describes the manufacture of gas using the water gas process. Early water gas plants were based on retorts used for coal carbonisation; however, later water gas plants (Photograph 1) more closely resembled producer gas plants in the design of the generator and in their mode of operation. Water gas plants were popular in the UK and worldwide, particularly in the USA where they were first successfully commercialised. One of the major issues with producing gas by carbonising coal was the length of time taken to get the gas plant operational and producing gas. This led to a heavy reliance on storage in gasholders. Without sufficient gas storage, the retorts would have to be kept heated on standby to accommodate rapid increases in gas production. This was both inefficient and uneconomic for the gas manufacturer. An alternative method to meet peak demand for gas was required, leading to the development of water gas plants. Water gas plant could produce gas much more rapidly (within 1-3 hours) than traditional coal carbonisation plant, allowing gas companies to satisfy peak demand more effectively. Whilst this process was commonly employed on many larger town and city gasworks to supplement coal gas supplies, plant was also developed for smaller gasworks. In Britain, water gas was mixed with coal gas (30% water gas to 70% coal gas) prior to distribution. 2. The Early Development of Water Gas Photograph 1. The inside of the water gas plant building at the former East Greenwich Gasworks. Source: National Grid Gas Archive. The discovery of water gas was attributed to the Italian physicist Felice Fontana in 1780. He C1 discovered that when steam was passed through (oil enriched) water gas process when he The central (water gas) retort contained hot iron incandescent carbon, the oxygen of the water discharged hot coke into a water gas generator scrap (or coke) onto which a trickle of water would molecules in the steam had a greater affinity for and intermittently injected steam and air. His fall, producing water gas. The other two ‘coal’ the carbon than the hydrogen to which it was patent described that the gas produced should be retorts made rich coal gas, being operated in the bonded. This led to the formation of carbon enriched with essential oil. The process did not conventional way and receiving a supply of water monoxide and hydrogen from the water and achieve commercial success. gas by a connecting pipe from the mouthpiece of carbon in the reaction: the central retort. A Belgian scientist (M. Jobard) successfully C + H O = H + CO. 2 2 experimented with water gas production circa Ruthin in Wales, and Comrie and Dunkeld in 1833. It is reported that he sold his invention to Scotland, also adopted White’s process for gas This finding predated William Murdoch’s Alexander Selligue of Paris and Florimont Tripier manufacture. The town of Petersfield, Hampshire discovery of a commercial process to produce of Lille. Selligue was then recognised as the adopted White’s method but using coke instead of coal gas. Given its composition, water gas had inventor. Under Selligue’s name, the water gas scrap iron in the central retort. The main failure of little or no illuminating power when burnt, so little process was introduced to Dijon, Strasbourg and White’s process was the greater complexity of use was made of the discovery. Henry Antwerp, as well as parts of Paris and Lyon. The controlling this water gas process compared with Cavendish, Antoine Lavoisier, Charles Meusnier Jobard/Selligue process started by decomposing coal gas. The relative amounts of rich gas and and others also later made the same discovery as the water; the resulting hydrogen was then mixed water gas produced had to be carefully controlled Fontana. with hydrocarbon (either oil vapour or heated to ensure correct gas quality. resin) which then passed into a retort containing The first patent taken out for water gas production hot coke. The process lost popularity when The process was exported, and in 1850 it was was believed to have been by W. Vere and H.S. Selligue was unmasked as a fraud. trialled over several months at the Philadelphia Crane in 1823. The patent described the use of Gasworks (USA), but the results did not support admitting water or steam into a retort containing The next major interest in water gas occurred in full-scale adoption. coal, oil or other suitable material undergoing 1847 when Stephen White of Manchester took out decomposition, but was not developed further. a patented ‘hydrocarbon process’ which had Joseph Gillard made major advances in his works similarities to that of Jobard. White’s idea was to at Narbonne, France in 1856. Gillard managed to In 1824, John Holt Ibbetson made the first attempt produce a very rich gas, from fat, oil or tar, and light the town by burning blue-water gas with to utilise water gas on a commercial scale. He dilute it to a reasonable candle power using a argand burners over which platinum wire cage experimented by steaming the coke which cheap, low-grade carrier gas. White’s success mantles were placed. Argand burners were the remained in the horizontal retorts at the end of the was boosted by favourable reports from Samuel first scientifically designed burners, originally period of carbonisation. Ibbetson published a Clegg and Dr E. Frankland. White’s method was designed for oil lamps but later adapted for use in patent in 1826 but did not develop the technology tested on a large scale at a mill gasworks in the gas industry. They consisted of a cylindrical further. On 6 October 1830, Michael Donovan Manchester and at the gasworks of the South wick
Details
-
File Typepdf
-
Upload Time-
-
Content LanguagesEnglish
-
Upload UserAnonymous/Not logged-in
-
File Pages24 Page
-
File Size-