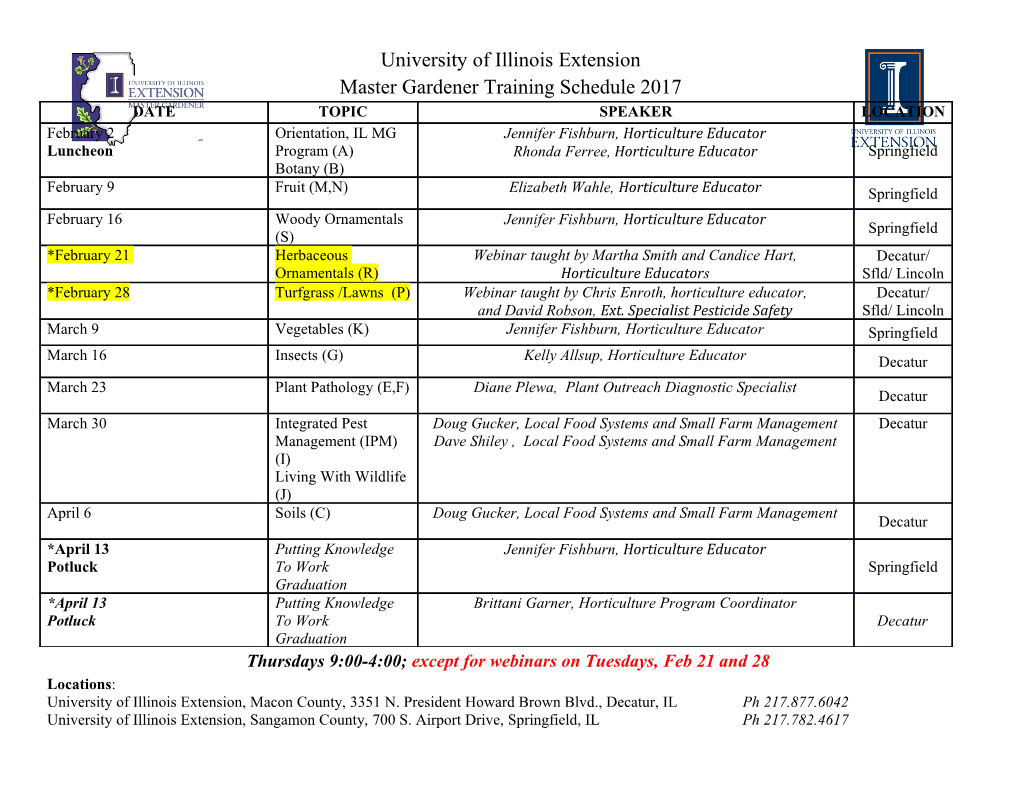
ISIJ International, Vol. 53 (2013), No. 8, pp. 1358–1364 Experimental Investigation on Direct Reduction Followed by Magnetic Separation for Nb2O5-Bearing Ore Xin JIANG,1)* Fengman SHEN,1) Ligang LIU,1) Xiaogang LI2) and Lin WANG3) 1) School of Materials and Metallurgy, Northeastern University, Shenyang, Liaoning, 110004 China. 2) Baotou Steel Group Mining Research Institute (Limited Liability Company), Baotou, Inner Mongolia, 014010 China. 3) Department of Mechanical Engineering, Shenyang Institute of Engineering, Shenyang, Liaoning, 110136 China. (Received on February 21, 2013; accepted on May 18, 2013) Recently a special attention is being paid on the ferroniobium production worldwide, especially in China. In present work, direct reduction followed by magnetic separation for Nb2O5-bearing ore is investigated. Reflected light microscope, scanning electron microscope with EDX, and high performance X-ray diffrac- tion were used for fundamental analysis. The experimental results show that, (1) the optimum reduction parameters are 0.9 of C/O, 1 200°C and 20 min. At these optimum parameters, the degree of metallization of ore-coal composite pellet is more than 90%. (2) In direct reduced pellets, metallic iron and slag have gathered respectively, and they can be magnetically separated. Nb and Ti are associated together and inserted in slag, and stay in slag phase after magnetic separation. (3) Based on the process of direct reduction followed by magnetic separation, 7.71% of Nb2O5-enriched slag is obtained, which is a good feed for producing ferroniobium or metallic niobium in electric furnace. The Nb2O5 content in Nb2O5- enriched slag is 1.8 times of the original ore, and the recovery of Nb is about 85%. These experimental results can give some theoretical references for industrial application in future. KEY WORDS: Nb2O5-bearing ore; ore-coal composite pellet; direct reduction; magnetic separation; degree of metallization. 1. Introduction 25000 Niobium is an important element for MRI (Magnetic 20000 Resonance Imaging) machines, high technology, and the steel industrial. Over three-quarters of the world’s niobium 15000 production currently comes from Brazil, with most of remainder coming from eastern Canada. Recently a special 10000 attention is being paid on the ferroniobium production 1–6) worldwide, especially in China. China has been a top Imports, Metric tons 5000 importer of ferroniobium in recent years, and its imports have increased over the last decade (Fig. 1). 0 In tradional process of ferroniobium production in China 2000 2002 2004 2006 2008 2010 2012 include, (1) the raw mineral is processed primarily by phys- Year ical processing technology to get Nb2O5-bearing concen- Fig. 1. Chinese imports for niobium. trate. (2) The Nb2O5-bearing concentrate is used to produce sinter or pellet. (3) Sinter or pellet is feed into blast furnace (BF) to produce Nb-bearing liquid iron. (4) Nb is oxidized tant factor for producing ferroniobium or metallic niobium. to niobium oxides in converting process (BOF), and Compared with Sinter-BF-BOF route, reduction followed enriched in slag. In this long Sinter-BF-BOF route, particu- by magnetic separation route has the following advantag- larly in BF, some Nb presents in liquid iron, and some Nb es.8–11) (1) At the condition of BF, the reducing potential and oxides present in slag because the selective reduction of fer- reducing temperature are uncontrollable, and they are strong rous oxides and niobium oxides can not be achieved in BF. enough to reduce both ferrous oxides and niobium oxides. So the recovery of Nb is very low (about 72%) and the ener- At direct reduction process, ferrous oxides can be reduced, gy consumption per unit Nb produced is very high.7) but niobium oxides can not be reduced by controlling reduc- As we all know, the grade of Nb2O5 content is an impor- ing potential and reducing temperature. So, direct reduction is an effective process to achieve selective reduction. (2) In * Corresponding author: E-mail: [email protected] BF and BOF, the Nb2O5-enriched slag is liquid. But in mag- DOI: http://dx.doi.org/10.2355/isijinternational.53.1358 netic separation, the Nb2O5-enriched slag is solid, so the © 2013 ISIJ 1358 ISIJ International, Vol. 53 (2013), No. 8 energy consumption is relatively lower. Therefore, aimed –74 μm is about 76%, and –99 μm is about 90%. The size for producing Nb2O5-enriched slag, direct reduction fol- distribution of this applied ore is easy for pelletization. So lowed by magnetic separation is investigated in present the ore-coal composite pellets are used as the feed material work, which can give the theoretical references for industri- for direct reduction experiments. The goal of direct reduc- al application in future. tion is that the ferrous oxides are reduced to metallic iron, but the niobium oxides are not reduced (based on the ther- modynamic analysis).14) Then metallic iron can be separated 2. Experimental Design with slag by magnetic separation. The niobium oxides pres- 2.1. Raw Materials ent in slag. This slag is named as Nb2O5-enriched slag, in Almost over 90% of Nb2O5-bearing resources in China which the Nb2O5 content is increased. This Nb2O5-enriched are found in Baiyunebo deposit in the Inner Mongolia slag is a good feed for producing ferroniobium, metallic nio- Autonomous Region. In this study, Baiyunebo ore is used as bium, and rare earth etc. The chemical compositions of coal the Nb2O5-bearing raw material. The Nb2O5 content of orig- and bentonite used in present work are listed in Table 2. inal Baiyunebo ore is very low, only 0.4–0.7%. But with the Before the pelletization, the coal and bentonite are ground development of beneficiation technology, the grade of to –74 μm. 12,13) Nb2O5 can be increased to 4.32% (Table 1). From Table 1, in addition to the ferrous oxides and niobium oxides, 2.2. Experimental Procedure there are some SiO2, TiO2, CaO, MgO and some alkalis The key for selective reduction of ferrous oxides and nio- (Na2O and K2O). bium oxides in present work is not only to reduce iron Niobium does not occur freely in nature. It primarily co- oxides and no-reduce niobium oxides, but also the reduced exists in form of pyrochlore, a niobium-rich, complex min- metallic iron particles grow to big size which is benefit for eral containing some of calcium, sodium, titanium, rare the following step --- grinding and magnetic separation. earth and other elements. Pyrochlore is the most important Another key is that the pellet can not melt during the process mineral for niobium extraction and production. Niobium can of direct reduction. If melting, the process probably is diffi- also be found in columbite, which is a niobate of iron, man- cult to be realized in industrial trial. ganese, and magnesium. X-ray diffraction of the applied ore In order to get optimum operation parameters for the is shown in Fig. 2. From the figure, one can conclude that, selective reduction of ferrous oxides and niobium oxides, (1) our applied ore is composed of hematite, magnetite, series of direct reduction experiments were conducted. In quartz, and some complex mineral including Ti, Ca, Na etc. these series of experiments, the effects of following vari- (2) Hematite is the main ferrous oxide, and there is small ables on the reduction of ore-coal composite pellets were amount of magnetite. (3) The co-exist ore containing niobi- studied: um oxides and titanium oxides is the main Nb2O5-bearing (1) The processing temperature (the temperature in the ore. The co-exist ore and the compact structure are the main Muffle furnace) for reduction. Basically, higher temperature characteristics for niobium extraction and production. (4) will result in melting of pellets, and lower temperature will The slag is mainly composed of silicate and quartz. result in low metallization degree and low rate of reduction. The size distribution of Nb2O5-bearing ore is shown in (2) The reduction time. This is related to the reduction Fig. 3. From the figure, the powder of –50 μm is about 50%, temperature, and proper time will result in high degree of metallization and big size of metallic iron, which is benefit Table 1. Chemical composition of Nb2O5-bearing concentrate ore, mass%. 100 TFe FeO Nb2O5 CaO SiO2 MgO Al2O3 MnO 8 35.52 1.6 4.32 2.42 21.87 1.05 0.26 0.31 80 Cumulative percentage, % FSPNa2OK2OTiO2 Sc2O3 TREO 6 60 0.73 0.73 0.07 2.42 0.18 6.71 0.032 2.72 4 40 ͩ Size distribution, % 2 14000 ƹ Ʒ--Fe2O3 ƹ--Ti NbO4 20 Size distribution ƾ ƾ--Fe3O4 --Ca SiO4 ƽ Cumulative percentage Ƶ--TiO2 Ƽ--NaFeO Si2O6P 12000 --SiO2 0 0 ͩ 050100150200 ƽ 1 Ʒƹ Diameter, um ƾ 10000 Ʒ Ƽ Fig. 3. Size distribution of Nb2O5-bearing concentrate ore. Ƶ Intensity Ʒ Ʒ 8000 Ƽ Ʒ ͩ Ƶ ͩ Table 2. Chemical composition of coal and bentonite, mass%. 6000 Pulverized Fixed Carbon Total Carbon Volatile Matters Ash H2O 20 40 60 80 Coal 60.49 75.4 31.23 8.28 6.68 Angle, 2θ(deg.) SiO2 Al2O3 CaO MgO Bentonite 69.74 16.60 2.41 1.14 Fig. 2. X-ray diffraction of Nb2O5-bearing concentration ore. 1359 © 2013 ISIJ ISIJ International, Vol. 53 (2013), No. 8 for the following grinding and magnetic separation. Fig. 5. From the figure, one can conclude that the pellets (3) The amount of carbon addition, in term of the gram- will seriously melt when the temperature is higher than atomic of fixed carbon in the coal added to the gram-atomic 1200°C. According to the chemical composition of ore, the of combined oxygen in iron oxides, which is denoted as C/O dominant oxides in slag should be SiO2, TiO2, and Nb2O5.
Details
-
File Typepdf
-
Upload Time-
-
Content LanguagesEnglish
-
Upload UserAnonymous/Not logged-in
-
File Pages7 Page
-
File Size-