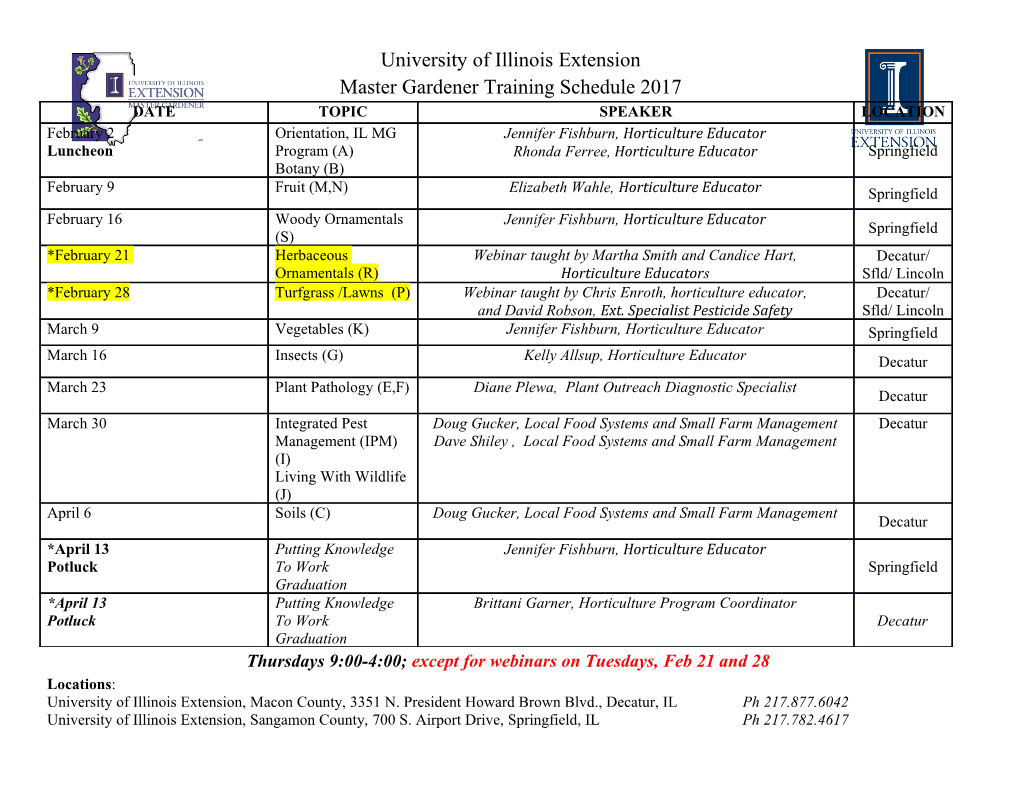
fibers Article Improvement in Carbonization Efficiency of Cellulosic Fibres Using Silylated Acetylene and Alkoxysilanes Maria Mironova *, Igor Makarov , Lyudmila Golova, Markel Vinogradov, Georgy Shandryuk and Ivan Levin A.V. Topchiev Institute of Petrochemical Synthesis, Russian Academy of Sciences, 119991 Moscow, Russia; [email protected] (I.M.); [email protected] (L.G.); [email protected] (M.V.); [email protected] (G.S.); [email protected] (I.L.) * Correspondence: [email protected]; Tel.: +7-495-647-5927 Received: 6 September 2019; Accepted: 25 September 2019; Published: 28 September 2019 Abstract: Comparative studies of the structure and thermal behavior of cellulose and composite precursors with additives of silyl-substituted acetylene and alkoxysilanes were carried out. It is shown that the introduction of silicon-containing additives into the cellulose matrix influenced the thermal behavior of the composite fibers and the carbon yield after carbonization. Comparison of the activation energies of the thermal decomposition reaction renders it possible to determine the type of additive and its concentration, which reduces the energy necessary for pyrolysis. It is shown that the C/O ratio in the additive and the presence of the Si–C bond affected the activation energy and the temperature of the beginning and the end of the pyrolysis reaction. Keywords: Cellulose fiber; Lyocell; N-methylmorpholine-N-oxide; silicon-containing additives; thermal properties 1. Introduction By means of the solid phase dissolution of cellulose in N-methylmorpholine-N-oxide (NMMO), a direct solvent for cellulose, it is possible to obtain highly concentrated solutions and to spin the Lyocell-type fibers [1]. Recently, these fibers have attracted a lot of attention, not only as an alternative to rayon textile material, but also as precursors of carbon fibers [2]. The main problems of thermal transformation of cellulose fibers into carbon fibers are the increase of the carbon yield and formation of the necessary structures that provide good mechanical properties [3]. The theoretically possible value of the carbon yield in the carbonization process of cellulose is 44.4% [4]. In order to get as close as possible to this value, it is recommended to use active substances (the catalysts) that direct the process of pyrolysis towards the formation of carbon structures and prevent the byproducts (e.g., levoglucosanes) caused by the removal of carbon in gas form [5,6]. Catalysts of pyrolysis and flame retardants can be applied by impregnation of the precursor fibers with solutions of active substances followed by their drying [7,8]. The most widely used pyrolysis catalysts for cellulose are ammonium chloride and ammonium sulfate. Recently, silicon-containing catalysts have been proposed as an alternative to these active agents. Their use allows carbon fibers with a mechanical strength of more than 1 Gpa to be obtained. In [9–14], predominant data were given on the use of silicon-containing compounds for obtaining carbon fiber, in particular, in [10], the application of Tetraethoxysilane (TEOS) makes it possible to obtain carbon fibers with a diameter of 5.5 µm, a tensile strength of 930 Mpa, and an elastic modulus of 38 GPa, with a carbon yield of ~14.5%. The introduction of the pyrolysis catalysts and flame retardants into the polymer matrix can be considered as an alternative method of their application, which achieves a better distribution Fibers 2019, 7, 84; doi:10.3390/fib7100084 www.mdpi.com/journal/fibers Fibers 2019, 7, x FOR PEER REVIEW 2 of 11 fibers with a diameter of 5.5 µm, a tensile strength of 930 Mpa, and an elastic modulus of 38 GPa, Fiberswith 2019a carbon, 7, 84 yield of ~14.5%. 2 of 12 The introduction of the pyrolysis catalysts and flame retardants into the polymer matrix can be considered as an alternative method of their application, which achieves a better distribution of the ofactive the substance active substance in the volume in the volumeof the fiber of the and fiber redu andces the reduces number the of number stages of processing stages of processing (Figure 1) (Figure[15,16].1 )[15,16]. Figure 1.1. BasicBasic stages stages of cellulose composite precursors andand carboncarbon fibersfibers production.production. TEOS, Tetraethoxysilane; VTEOS, Vinyltriethoxysilane; BTMSA, Bistrimethylsilyl acetylene; NMMO, N-methylmorpholine-N-oxide. Silicon-containing compoundscompounds as as additives additives allow allow not not only only an increase an increase in the in carbon the carbon yield during yield heatduring treatment heat treatment of fibers, of but fibers, also but to obtain also to carbon-silicon obtain carbon-silicon carbide fiberscarbide [17 fibers], and [17], it is exactlyand it is this exactly class ofthis fibers class which of fibers is thewhich most is interestingthe most interesting for obtaining for obtaining heat-resistant heat-resistant materials [materials18]. [18]. Thermogravimetry Analysis (TGA) and Differential Differential Scanning Calorimetry (DSC) methods are widely used to study the propertiesproperties of carbon fiberfiber precursors and to represent the conditions for their production [19]. [19]. However, However, the the results results of of ex experimentsperiments cannot cannot always always be be interpreted interpreted definitely. definitely. To obtainobtain moremore accurateaccurate information, information, it it is is recommended recommended to to process process the the results results mathematically. mathematically. Thus, Thus, to determineto determine the ditheff erencesdifferences in thermal in thermal behavior, behavior process, process staging, staging, thermostability thermostability of synthetic of polymers,synthetic polysaccharides,polymers, polysaccharides, cellulose fibers, cellulose and sofibers, on, it isand reasonable so on, it to is evaluate reasonable the kineticto evaluate parameters the kinetic of the decompositionparameters of the using decomposition the Broido method using the [20 Broido–23]. method [20–23]. The Broido formula allows for estimation of the activation energy of the thermal decomposition of cellulose [[24]24] ln[ln(1/y)] = A Ea/(RT), (1) ln[ln(1/y)]=A-−Ea/(RT), (1) Ì where y = (Mt Me)/M0-Me,M0 is the mass of the initial sample, t is the sample mass at temperature where y = (Mt − Me)/M0-Me, M0 is the mass of the initial sample, Мt is the sample mass at temperature T in the TG experiment, Me is the final mass of the sample, Ea is the activation energy, T is the T in the TG experiment, Me is the final mass of the sample, Ea is the activation energy, T is the temperature, and R is the universal gas constant. temperature, and R is the universal gas constant. The purpose of this study was to compare the structure and thermal behavior of cellulose and The purpose of this study was to compare the structure and thermal behavior of cellulose and composite precursors containing silyl-substituted acetylene and alkoxysilanes additives, by the TGA composite precursors containing silyl-substituted acetylene and alkoxysilanes additives, by the TGA and DSC methods. and DSC methods. In this research, we report that the addition of silyl-substituted acetylene and alkoxysilanes into In this research, we report that the addition of silyl-substituted acetylene and alkoxysilanes into the cellulose matrix led to a decrease in the activation energy. Valuable information was obtained the cellulose matrix led to a decrease in the activation energy. Valuable information was obtained from the TGA; it is shown that 5% of the additive is sufficient to significantly increase the carbon yield from the TGA; it is shown that 5% of the additive is sufficient to significantly increase the carbon compared to cellulose during heat treatment of fibers to 1000 ◦C. yield compared to cellulose during heat treatment of fibers to 1000 °C. 2. Materials and Methods 2. Materials and Methods Concentrated cellulose dopes were prepared according to the method described in [25] from Concentrated cellulose dopes were prepared according to the method described in [25] from cellulose of the Baikal Cellulose and Paper Mill (Russia) (degree of polymerization was 600, H2O contentcellulose ~8%, of the and Baikalα-cellulose Cellulose content and notPaper less Mill than (Russia) 94%). As (degree a solvent, of N-methylmorpholine-N-oxidepolymerization was 600, H2O content ~8%, and α-cellulose content not less than 94%). As a solvent, N-methylmorpholine-N-oxide with a Tm = 120–160 ◦C (H2O < 10%) (Demochem, China) was used. The silicon-containing additives arewith shown a Tm = in 120 Table–1601 (Sigma-Aldrich,°C (H2O < 10%) (Demochem, USA). China) was used. The silicon-containing additives are shownFor inhibition in Table of 1 the(Sigma-Aldrich, of thermo-oxidative USA). degradation, 0.5% of propylgallate (Sigma-Aldrich, USA) was introduced to solution. FibersFibers 20192019,, ,77,, x,x 84 FORFOR PEERPEER REVIEWREVIEW 3 of 11 3 of 12 TableTable 1. 1.TheThe main main characteristics characteristics of organosilicon of organosilicon additives. additives. Viscosity, η 3 Viscosity,3 Viscosity, , Ò Ò Density,Density, g/cm g3 /cm TheThe Compound Compound StructuralStructural Formula Тmm, °CC Тboil, °C, C η, mPa·s mPa s The Compound Structural Formula Тm,, °C°C◦ Тboilboil,, °C°C ◦ η,, mPa·smPa·s (T(T ==(T 2525 =°C)°C)25 ◦C) · (T = 25 °C) (T = 20 ◦C) (T(T == 2020 °C)°C) TetraethoxysilaneTetraethoxysilane Tetraethoxysilane −82.5 170 170 0.933 0.933 0.75 0.75 (TEOS) (ID 24848042) −82.5 170 0.933 0.75 (TEOS)(TEOS) (ID(ID 24848042)24848042) − VinyltriethoxysilaneVinyltriethoxysilane (VTEOS)(VTEOS)(VTEOS) (ID (ID(ID <<00 160 160 0.910 0.910 0.7 0.7 24850510) 24850510) Bistrimethylsilyl BistrimethylsilylBistrimethylsilyl acetyleneacetylene (BTMSA) (BTMSA) 2222 136 136 0.752 0.752 - - (ID(ID(ID 24851275) 24851275)24851275) (ID 24851275) For inhibition of the of thermo-oxidative degradation, 0.5% of propylgallate (Sigma-Aldrich, As the main objects under consideration, the fibers obtained from the filled cellulose solutions USA) was introduced to solution. in theAs NMMO the main with objects a weight under ratioconsideration, of 95/5 and the 90 fibe/10rs (cellulose obtained/ organosiliconefrom the filled cellulose additive) solutions were studied inin(Table thethe NMMONMMO2).
Details
-
File Typepdf
-
Upload Time-
-
Content LanguagesEnglish
-
Upload UserAnonymous/Not logged-in
-
File Pages12 Page
-
File Size-