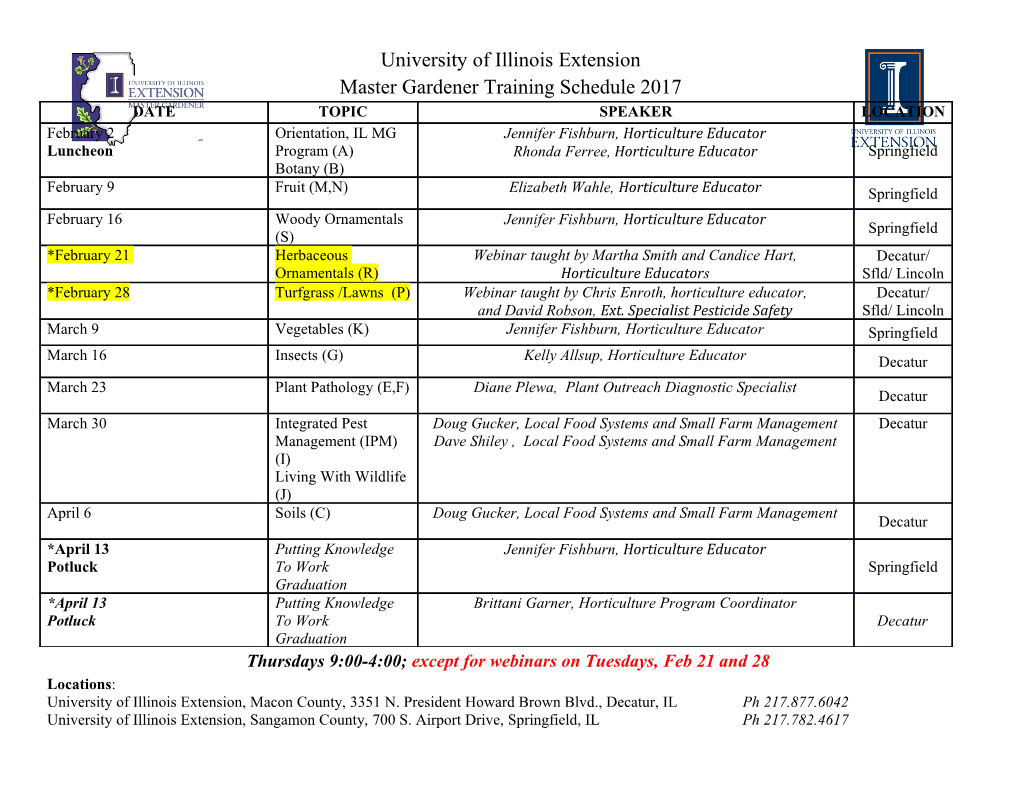
NASA/TP- 1998-206548 Recent Flight Test Results of the Joint CIAM- NASA Mach 6.5 Scramjet Flight Program Alexander S. Roudakov and Vyacheslav L. Semenov Central Institute of Aviation Motors Moscow, Russia John W. Hicks NASA Dryden Flight Research Center Edwards, California National Aeronautics and Space Administration Dryden Flight Research Center Edwards, California 93523-0273 April 1998 NOTICE Use of trade names or names of manufacturers in this document does not constitute an official endorsement of such products or manufacturers, either expressed or implied, by the National Aeronautics and Space Administration. Available from the following: NASA Center for AeroSpace Information (CASI) National Technical Information Service (NTIS) 7121 Standard Drive 5285 Port Royal Road Hanover, MD 21076-1320 Springfield, VA 22161-2171 (301) 621-0390 (703) 487-4650 RECENT FLIGHT TEST RESULTS OF THE JOINT ClAM-NASA MACH 6.5 SCRAM JET FLIGHT PROGRAM Alexander S. Roudakov* and Vyacheslav L. Semenov* Central Institute of Aviation Motors Moscow, Russia John W. Hicks + NASA Dryden Flight Research Center Edwards, California, USA Abstract space transportation. The scramjet, its performance potential, and its design methodology validation have Under a contract with NASA, a joint Central Institute been at the center of this quest. Programs, such as this of Aviation Motors (CLAM) and NASA team recently joint Russian-American project, seek to address this last conducted the fourth flight test of a dual-mode scramjet major aeronautics frontier. aboard the ClAM Hypersonic Flying Laboratory, "Kholod." With an aim test Mach 6.5 objective, the Previously, the Central Institute of Aviation Motors successful launch was conducted at the Sary Shagan test (CIAM), Moscow, Russia, conducted three rocket- range in central Kazakstan on February 12, 1998. boosted flight tests of its axisymmetric dual-mode Ground-launch, rocket boosted by a modified Russian Mach6 design scramjet (fig. I). The first was in SA5 missile, the redesigned scramjet was accelerated to November 1991, and the second involved a joint project a new maximum velocity greater than Mach 6.4. This with the French in November 1992. These flights launch allowed for the measurement of the fully achieved approximately Mach 5.5 and Mach 5.35, supersonic combustion mode under actual flight respectively (ref. 1). The third attempt was also with the conditions. The primary program objective was the French. In this March 1995 attempt, the engine failed to flight-to-ground correlation of measured data with operate because of some onboard power system preflight analysis and wind-tunnel tests in Russia and problems; however, non-fueled cold flow engine data potentially in the United States. This paper describes the were obtained to Mach 5.8. All scramjet flights were development and objectives of the program as well as the flown captive-carry atop the SA5 surface-to-air missile technical details of the scramjet and SA5 redesign to that included an experimental flight support unit known achieve the Mach 6.5 aim test condition. An overview of as the Hypersonic Flying Laboratory (HFL), "Kholod." I the launch operation is also given. Finally, preliminary flight test results are presented and discussed. In November 1994, NASA contracted with CIAM to continue exploring the scramjet operating envelope from Introduction the ram-scram, dual-mode operation below Mach 6 to the full supersonic combustion (scram) mode at Mach Internationally, several countries, such as the United 6.5. To accomplish this objective, the higher heat loads States, Japan, France, Germany, and Russia, have been required redesign of the scramjet combustor and active involved individually and jointly in the development of cooling system. Likewise, the increase to Mach 6.5 air-breathing propulsion technology solutions to required modifications to the SA5 booster to reduce drag efficient, low-cost, point-to-point rapid global access and and to improve performance. The contract specified the building of four identical engines to accomplish all required ground and flight tests. The first two engines were dedicated to wind-tunnel tests up to Mach 6.5 =Member, AIAA. simulated flight conditions. The third was designated for 'Associate Fellow, AIAA. flight test, and the fourth acted as a backup flight test Copyright © 1998 by the American Institute of Aeronautics and engine. The NASA ground testing of one of the first two Astronautics, Inc. No copyright is asserted in the United States under engines at the NASA Langley Research Center, Title 17, U.S. Code. The U.S. Government has a royalty-free license to exercise all rights under the copyright claimed herein forGovernmental Hampton, Virginia, is planned after completion of the purposes. All other rights are reserved bythe copyright owner. flight phase. The CIAM C16 V/K methane-heated 1 American Institute of AeronauticsandAstronautics 960355 Figure1.Artist's conception of scramjet external view. vitiated wind tunnel (fig. 2) was upgraded to provide conducted with a common set of instrumentation extended test time with a new facility nozzle and to test a sensors and measurement locations to facilitate data complete full-scale engine to the test conditions listed in correlation activities with predictive analysis results. table 1. Another key objective in the joint nature of the Table 1. Test conditions. program was to involve NASA engineering personnel in as much of the research, analysis, and testing as possible. Besides the comparison of results, methodologies, and Ramjet Scram jet test techniques between the two organizations, this mode mode program gave NASA a direct opportunity to learn about Hydrogen consumption, kg/sec 0.3 1.4 Russian facilities and test techniques. An additional advantage is that NASA has provided an independent Air mass flow rate, kg/sec 20 30 assessment of the engine design, instrumentation, and Air temperature, K 2000 2500 ground facility operation to CIAM. 2 Air pressure at aerodynamic 1.0-7.5 20 nozzle entrance, MPa Hypersonic Flying Laboratory, "Kholod" Air flow Mach number at 3.6 8 The HFL, "Kholod," comprises the entire experimental nozzle exit, MPa system, including the scramjet engine and propellant, Test duration, sec 30 30 engine control, engine cooling, instrumentation, and telemetry systems. This laboratory was designed to essentially replace the size and mass of the original The overall program objectives were to explore and SA5 payload. measure the full supersonic combustion mode and to correlate these flight data with ground tests and with Figure 3 shows a schematic of the complete HFL. The analysis techniques. These objectives included the HFL consists of three main support compartments: N1, opportunities to validate design and analysis methods N2, and N3A/B aft of the engine. The conical N1 and to compare NASA and CIAM ground test facility compartment comprises a transition section from the test techniques and results. This comparison was engine to the cylindrical booster and is covered by a 2 American Instituteof Aeronautics and Astronautics Exhauster 960356 Figure 2. The C-16 ClAM V/K facility for scramjet large-scale models test. 1. Experimental scramlet with compartment N1, engine _ _,_mmmwmmmm_m_ i regulation and fuel supply system - --\9 -- _a 2. Compartment N2, liquid hydrogen tank 3. Compartment N3A, nitrogen/helium pressure supply system 4. Compartment N3B, flight control system and power supply 5. Propellant tank control system 6. $A-5 rocket motor 7. Fin 8. Roll control surface 9. Solid booster rocket 960357 Figure 3. The Hypersonic Flying Laboratory. thermal protective skin to shield it from the pressures. There are 58 thermocouples; 38 of which are engine exhaust. This compartment contains the engine located along the engine duct. In addition, 46 other control, fuel regulator, and instrumentation systems. system operation sensors are included in the Compartment N2 contains the double-walled, insulated instrumentation. Figure 4 shows the main engine liquid hydrogen propellant tank, followed by the N3A flowpath instrumentation. The majority of these data are compartment containing the pressurized helium bottle telemetered at a digital 50 samples/see except for the used to pump the fuel to the engine. The N3A frequency modulation analog temperature measurements compartment also contains the high-pressure nitrogen which are transmitted at 1.5 Hz. NASA has contributed bottle used for the pneumatic actuators. The final N3B additional instrumentation to compare with or enhance compartment contains the telemetry system, system the Russian measurement system. This instrumentation batteries, and SA5 missile control system. included a body-mounted, three-axis, orthogonal Onboard HFL instrumentation includes 83 pressure accelerometer package and several flowpath pressure transducers; 43 of which measure engine duct wall transducers. 3 American Institute of Aeronautics and Astronautics Ok Pressure transducers Tw Wall temperature TB Coolant passage temperature P1, P4, P5 Static pressures Po Pitot pressure , , /.J points t 36O 33O I "n,zi#_e_ " T T_-' I -I = 300 _[ k-95 270 - [ a Dk B9 24O t93-2 r_w'4] _Dk 79 c _ Angular 210 A1, " Dk-7, ,-2 D]_- .'r2"2 _k.6_Dk"_'6"2 Dk-8__ D_8-2i_ D position, 180 l o,j.,o deg 150 -I r 120 g0 -[ _ '_ D .66-I I w-5_ D_.6: bk-6_ w-13 Dk-6e 4 Dk, r7 T ,,'.20 :, -27 Tw.40 60 Dk_4a D1-59 30 .i " Io.-L I -i !- i 0 I j I 0 100 200 300 400 500 600 700 800 900 1000 1100 1200 1300 Length, mm 980160 Figure 4. The scramjet flowpath instrumentation layout. Axisymmetric Scramjet Description low thermal conductivity as the EP666 steel. However, and Redesign its greatly increased heat capacity allows Fekral to survive longer at the elevated temperatures to complete the aim test conditions of about 5 sec at Mach 6.5. The The hydrogen-fueled axisymmetric model 58L scramjet (fig. 5) is basically a ClAM Mach 6 design with external cowl is coated with a chromium-nickel spray modifications to the combustor, inlet leading edge, and near the front to increase heat emissivity to 0.90.
Details
-
File Typepdf
-
Upload Time-
-
Content LanguagesEnglish
-
Upload UserAnonymous/Not logged-in
-
File Pages14 Page
-
File Size-