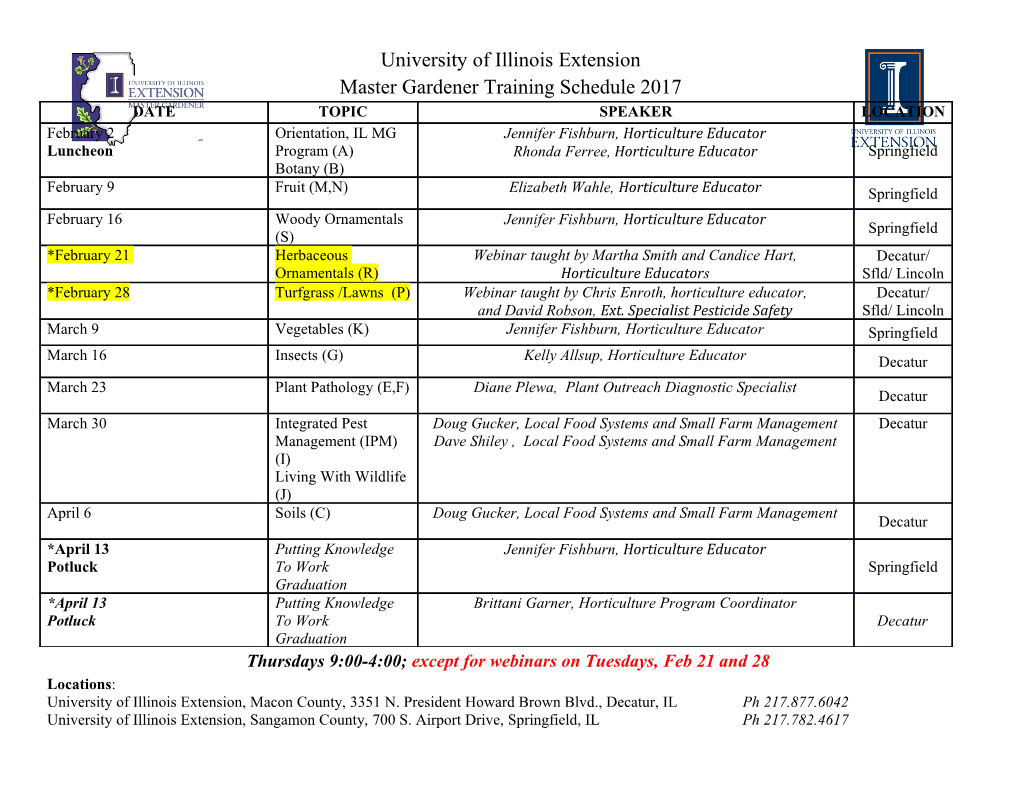
Europaisches Patentamt 0163 419 J European Patent Office Publication number: B1 Office europeen des brevets EUROPEAN PATENT SPECIFICATION C 25 D 3/58, Date of publication of patent specification: 05.10.88 © intci.4: C 25 D 7/00, A 44 C 21/00 Application number: 85302932.0 Date of filing: 25.04.85 thereof. Aureate coins, medallions and tokens and method for the production Sherritt Gordon Mines Limited Priority: 01 .05.84 CA 453305 Proprietor: 2800 Commerce Court West Toronto, Ontario (CA) Date of publication of application: 04.12.85 Bulletin 85/49 Inventor: Ruscoe, Michael J.H. 36 Gresham Boulevard Publication of the grant of the patent: St. Albert Alberta (CA) 05.10.88 Bulletin 88/40 Inventor: Seibt, Willie 10172-88th Street Edmonton Alberta (CA) Designated Contracting States: AT BE CH DE FR GB IT LI LU NL SE Representative: Lambert, Hugh Richmond et al D. YOUNG & CO. 10 Staple Inn References cited: London, WC1V7RD(GB) WO-A-84/03522 FR-A-743797 GB-A-1558 803 US-A-2886500 CO <0 Note- Within nine months from the publication of the mention of the grant of the European patent, any person may of shall qive notice to the European Patent Office of opposition to the European patent granted. Notice opposition deemed to have been filed until the opposition fee has been Q. be filed in a written reasoned statement. It shall not be 99(1 ) convention). Ul paid. (Art. European patent Courier Press, Leamington Spa, England. 0 163 419 Description vending equipment which only accepts magnetic coins. A further problem is that a coin blank must This invention relates to aureate coins, be readily mintable, i.e. it must be soft enough to medallions or tokens and blanks used for the be readily deformed by coin dies during the production of coins, medallions or tokens, that is 5 minting procedure to impart the required insignia to say metal blanks or minted coins, medallions to the coin faces. The coin blanks must not be too or tokens having a golden appearance, and a hard, otherwise the costly coin dies would wear method for the production thereof. out too quickly or an undesirable shallow impres- Many countries are replacing or planning to sion would be produced on the struck coin. This is replace bank notes by coins, mainly because bank 10 undesirable since coin dies are expensive. notes are expensive forms of currency compared It is therefore an object of the invention to to coins in view of the relatively short life of bank provide an aureate coin which overcomes the notes. Bank notes are thus not desirable as low above mentioned problems, that is to say an value currency, and inflation is of course resulting aureate coin which is relatively inexpensive to in bank notes in many countries now representing 15 produce, has a satisfactory service life with low value currency. It is bank notes of such low respect both to acceptable colour and other physi- value currency that are being replaced by coins. cal properties such as wear, is suitable for use in It has become established in many countries coin-operated vending equipment with coin that low value coins have a copper colour, and validation devices which check physical that middle and high value coins have a silver 20 properties including electrical and nagnetic colour. In the past, solid gold coins have been properties, and is not easily counterfeited. used for relatively high value currency, but today According to the invention, a coin, medallion or are struck only for the numismatic value or as a token product (i.e. a minted coin, medallion or convenient form of bullion. However, gold is now token or blanks used for the production of coins, so expensive that a present day gold coin would 25 medallions or tokens) has a coin-shaped core with necessarily comprise a base metal core with a opposed faces and a peripheral side edge of very thin gold coating, perhaps only 1-2 urn. The mintable metallic material, and an electroplated, small gold thickness would be likely to wear coating comprising copper and tin completely through to the base metal core during the normal encasing the core and providing a long lasting service life of the coin and the intrinsic value of 30 golden appearance in use. The electroplated coat- the gold would be lost. ing contains from about 8 to about 16% tin by From GB-A-1 558803 the electroplating of coin- weight, preferably from about 11 to about 14% shaped cores with Cu is known. Alloying with the balance being copper. The electroplated elements may be included in said upper coating coating has a thickness on each core face of from to increase wear of corrosion resistance, but no 35 about 10 to about 150 urn, preferably from about particular hint is disclosed to tin. The thickness of 30 to about 50 urn. The total weight of the the coating is preferably 0.05 mm or 0.14 mm. electroplated coating may be from about 2 to Various attempts have been made to produce about 26%, preferably from about 6 to about 10%, satisfactory inexpensive aureate coins for use as of the total weight of the product. relatively high value currency. Brass, typically 40 Also provided in accordance with the present 70% copper and 30% zinc, is a common yellow invention is a method of producing such blanks coinage alloy, but it tarnishes in service and is and coins, medallions or tokens. thus associated with cheapness in the public eye. Although it is known to electroplate metal An attempt has recently been made to overcome articles such a door handles with an alloy of this problem by replacing 5% of the zinc with 45 copper and tin to produce a bronze finish, bronze nickel, but the resulting colour is a pale yellow of the composition described, particularly at the rather than gold. In another attempt, an alloy high end of the tin range, is well known to be a composition of 92% copper, 6% nickel and 2% hard alloy which cannot be readily rolled or aluminium has been used, but this composition worked into strip form, i.e. which cannot normally has a pink hue and tends to turn brown in service. so be worked into a coinage product. Thus, bronzes Other attempts have also been made with other in the above composition range would not alloy compositions but none has had a long normally be considered for use as coinage lasting satisfactory golden appearance. materials. Also, considering the relatively high Another problem with common yellow coins of cost of tin, such high tin alloys would not solid low melting point brass and bronze is that 55 normally be considered for coinage. they are easy to counterfeit. Still another problem In accordance with the present invention how- is that a coin must have acceptable physical ever, it has been discovered that a coin, medallion properties, such as weight, size and electrical and or token product as described above has an magnetic properties, for use in coin-operated acceptable long-lasting aureate appearance, i.e. is vending equipment having coin testing devices 60 satisfactorily resistant to tarnishing, and with which rely on such properties to distinguish a suitable choice of core material is readily mint- required coin from other coins and fraudulent able and has suitable properties for acceptance by replicas of the required coin. For example, the conventional coin selection devices in vending nickel-modified brass coin mentioned above is machines. A coin, medallion or token product in non-magnetic and hence will not be accepted by 65 accordance with the invention is also inexpensive 0 163 419 to produce and has a satisfactory service life. an alkaline copper-tin plating bath containing Also, compared to coins with a homogeneous about 32 g/L copper and 26 g/L tin. The tempera- composition, a coin, medallion or token product ture of the bath was 75°C, and a voltage of 6.25 V in accordance with the invention is not readily was applied giving a current of 431 A. After 3.6 h, counterfeitable. 5 the barrel was removed from the plating bath and Coin, medallion or token blanks in accordance passed through a cold rinse and an anti-stain with the invention may for example be produced rinse. in barrel-plating equipment in the manner After plating, the blanks were found to have a described in Canadian patent No. 1,093,498, copper-tin electrodeposit equal to 9.1% of the issued January 13, 1981 and the corresponding io weight of the plated blank. The tin content of the United States patent No, 4,089,753 issued May 16, deposit was 13.0%, with the balance being cop- 1978, using a suitable copper-tin electroplating per. The thickness of the electrodeposit was 43 bath. um on the faces and I05 urn on the side edge. As mentioned above, the metallic core material The plated blanks were then passed to a pro- should be readily mintable, chosen for low cost, is duction annealing furnace with a temperature provide specific properties for coin selection setting of 750°C and a hot zone retention time of devices, and for optimum protection against 12 minutes to reduce their hardness from about counterfeiting. The core material may for 78 to about 32 on the Rockwell 30T hardness example comprise iron, steel or stainless steel, scale. Annealed blanks were then cleaned, nickel, nickel-plated steel, zinc, copper or various 20 polished and brightened in a two-stage process alloys of copper containing zinc and/or nickel and/ comprising acid washing followed by detergent or tin.
Details
-
File Typepdf
-
Upload Time-
-
Content LanguagesEnglish
-
Upload UserAnonymous/Not logged-in
-
File Pages5 Page
-
File Size-