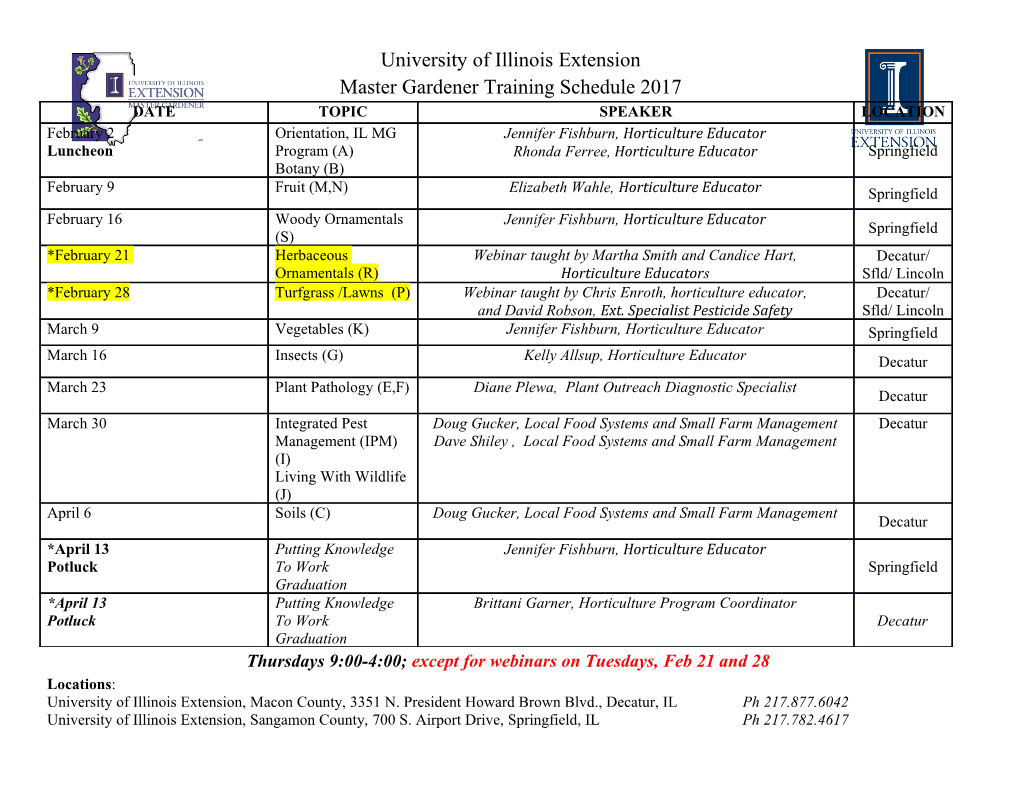
Zhang et al. Chin. J. Mech. Eng. (2021) 34:42 https://doi.org/10.1186/s10033-021-00555-6 Chinese Journal of Mechanical Engineering REVIEW Open Access Chassis Coordinated Control for Full X-by-Wire Vehicles-A Review Lei Zhang1,2 , Zhiqiang Zhang1,2, Zhenpo Wang1,2*, Junjun Deng1,2 and David G. Dorrell3 Abstract An X-by-wire chassis can improve the kinematic characteristics of human-vehicle closed-loop system and thus active safety especially under emergency scenarios via enabling chassis coordinated control. This paper aims to provide a complete and systematic survey on chassis coordinated control methods for full X-by-wire vehicles, with the primary goal of summarizing recent reserch advancements and stimulating innovative thoughts. Driving condition identifca- tion including driver’s operation intention, critical vehicle states and road adhesion condition and integrated control of X-by-wire chassis subsystems constitute the main framework of a chassis coordinated control scheme. Under steer- ing and braking maneuvers, diferent driving condition identifcation methods are described in this paper. These are the trigger conditions and the basis for the implementation of chassis coordinated control. For the vehicles equipped with steering-by-wire, braking-by-wire and/or wire-controlled-suspension systems, state-of-the-art chassis coordi- nated control methods are reviewed including the coordination of any two or three chassis subsystems. Finally, the development trends are discussed. Keywords: X-by-wire systems, Chassis coordinated control, Driving condition identifcation, Active safety 1 Introduction Several active control systems (ACSs) have been devel- Modern vehicles are being increasingly equipped with oped based on X-by-wire chassis subsystems, such as advanced sensors and electronic control systems to Active Front Steering (AFS) [6], Direct Yaw-Moment obtain full perception of the surroundings and provide Control (DYC) [7], Electronic Stability Control (ESC) efective driver assistance in complex and ever-varying [8], Electronic-Hydraulic Braking System (EHB) [9] and driving scenarios. Perception, trajectory planning and Active Suspension System (ASS) [10]. By applying an motion control constitute the three major tasks of super- additional steering angle to the front wheels, the exclu- visory control systems in connected and autonomous sive implementation of an AFS can potentially improve vehicles (CAVs) [1]. Tese have the potential of reduc- vehicle lateral stability without explicitly infuencing lon- ing driver fatigue and improving transport safety and gitudinal vehicle velocity. However, due to the limitations efciency [2–5]. Advanced X-by-wire chassis, which can of system characteristics and tire force saturation, the include drive-by-wire, steer-by-wire, brake-by-wire and AFS has a marginalized efect either when the additional active/semi-active suspension subsystems, is necessary yaw moment demand is too large or when the vehicle for autonomous driving. Efcient and coordinated con- runs at its stability boundaries. In contrast, DYC can gen- trol of X-by-wire chassis subsystems holds the key to the erate a desirable additional yaw moment by applying dif- performance and safety of CAVs. ferential driving or braking torques to both wheel sides. ESC is a kind of active safety system which expands the functions of Anti-lock Braking System (ABS) and Trac- *Correspondence: [email protected] tion Control System (TCS). EHB enables the decoupling 1 National Engineering Laboratory for Electric Vehicles, Beijing Institute of the hydraulic and the regenerative braking, and has of Technology, Beijing 100081, China Full list of author information is available at the end of the article © The Author(s) 2021. This article is licensed under a Creative Commons Attribution 4.0 International License, which permits use, sharing, adaptation, distribution and reproduction in any medium or format, as long as you give appropriate credit to the original author(s) and the source, provide a link to the Creative Commons licence, and indicate if changes were made. The images or other third party material in this article are included in the article’s Creative Commons licence, unless indicated otherwise in a credit line to the material. If material is not included in the article’s Creative Commons licence and your intended use is not permitted by statutory regulation or exceeds the permitted use, you will need to obtain permission directly from the copyright holder. To view a copy of this licence, visit http:// creat iveco mmons. org/ licen ses/ by/4. 0/. Zhang et al. Chin. J. Mech. Eng. (2021) 34:42 Page 2 of 25 the potential of enhancing both longitudinal and lat- chassis control methods ignore the infuence of suspen- eral stabilities. Recently, the burgeoning development sion. ASS can generate a vertical force at each wheel by of electric vehicles (EVs) provides great opportunities changing the corresponding spring stifness and damp- for ACSs to be increasingly adopted in production vehi- ing parameters so as to control vehicle body attitude cles [11–13]. In particular, in-wheel-motor-drive elec- and thereby enhance the handling stability and driver tric vehicles (IWMD EVs) employ four in-wheel motors comfort. installed inside each wheel hub for direct propulsion, Multiple chassis control systems may share the same and fast response and accurate control precision of actuators, so conficts and interferences can emerge these hub-motors contribute to efcient DYC implemen- because of diferent control objectives. Recent research tation [14–18]. Generally, vehicle safety can be enhanced shows that chassis coordinated control can take advan- via efcient vehicle motion control during the implemen- tage of each chassis subsystem to improve vehicle sta- tation of an ACS. But each vehicle motion is subject to bility, handling performance, and ride comfort through more than one ACS while each ACS can exert infuence the coordinated control of longitudinal, lateral, and ver- on several vehicle motions. Te relationship between tical forces, especially under critical circumstances. It is vehicle motions and conventional ACSs are succinctly widely recognized that the complex chassis coordinated illustrated in Figure 1. control task can be achieved through a three-layer hier- Suspension systems aim to transmit road excitations archical structure, which is illustrated in Figure 2, where: and damp the vibration, which is strongly related to vehi- cle roll and lateral dynamics. However, due to the com- (1) Te upper supervisor layer is responsible for iden- plexity of suspension modeling and the strong couplings tifying current driving condition based on critical of vertical dynamics and other vehicle motions, most vehicle states and driver’s inputs. Trough various Figure 1 The relationship between vehicle motions and conventional ACSs Zhang et al. Chin. J. Mech. Eng. (2021) 34:42 Page 3 of 25 Figure 2 The schematic of a chassis coordinated control scheme pattern recognition algorithms, the subject vehi- With the continuous development of advanced per- cle can clearly recognize a driving mode such as ception sensors and Vehicle-to-Everything technologies, straight running, cornering, lane change or U-turn. recent research has highlighted the intertwined relation- Tis is in addition to vehicle operating conditions, ships among chassis coordinated control, trajectory plan- i.e., rollover state, steering characteristics, and brak- ning and expanding perception of the surroundings [19, ing intensity. Te driving condition identifcation 20]. Route planning and velocity planning constitute two results can be used to trigger diferent coordinated important parts of trajectory planning [21, 22]. A safe control modes, and are employed as the precondi- and collision-free route is frst derived considering obsta- tions for selective involvements of specifc chassis cles and road boundaries, and then velocity planning subsystems. designates speeds and accelerations to each waypoint (2) Te second coordination layer utilizes driver’s considering the kinematic constraints and the route plan- inputs and real-time vehicle states to calculate ning results. Vehicle states can be formulated as the criti- the reference vehicle signals and then the desired cal inputs in the upper supervisor layer. forces/yaw moment based on a reference vehicle Te rest of the paper is organized as follows. Section 2 model. Te driving condition identifcation results describes the approaches for driving condition identif- are analyzed to determine which chassis subsys- cation and discusses their respective advantages, disad- tems are to participate in the coordinated control vantages, and application ranges. Section 3 presents an and then their respective contributions to real- extensive survey on state-of-the-art chassis coordinated ize the desired generalized forces/yaw moment. control methods reported in the literture. Tese can be (3) Te third control layer decomposes and dis- divided into two categories based on subsystem involve- patches the control tasks to individual chassis ment patterns: 1) any two of the three chassis subsystems actuators. By considering the working areas of each are involved; and 2) all the chassis subsystems participate. chassis subsystem and actuators characteristics, Te overall concluding remarks are given in Section 4. the control layer aims to control the involved sub- systems to track their target states by minizing the 2 Driving Condition Identifcation deviations of actual
Details
-
File Typepdf
-
Upload Time-
-
Content LanguagesEnglish
-
Upload UserAnonymous/Not logged-in
-
File Pages25 Page
-
File Size-