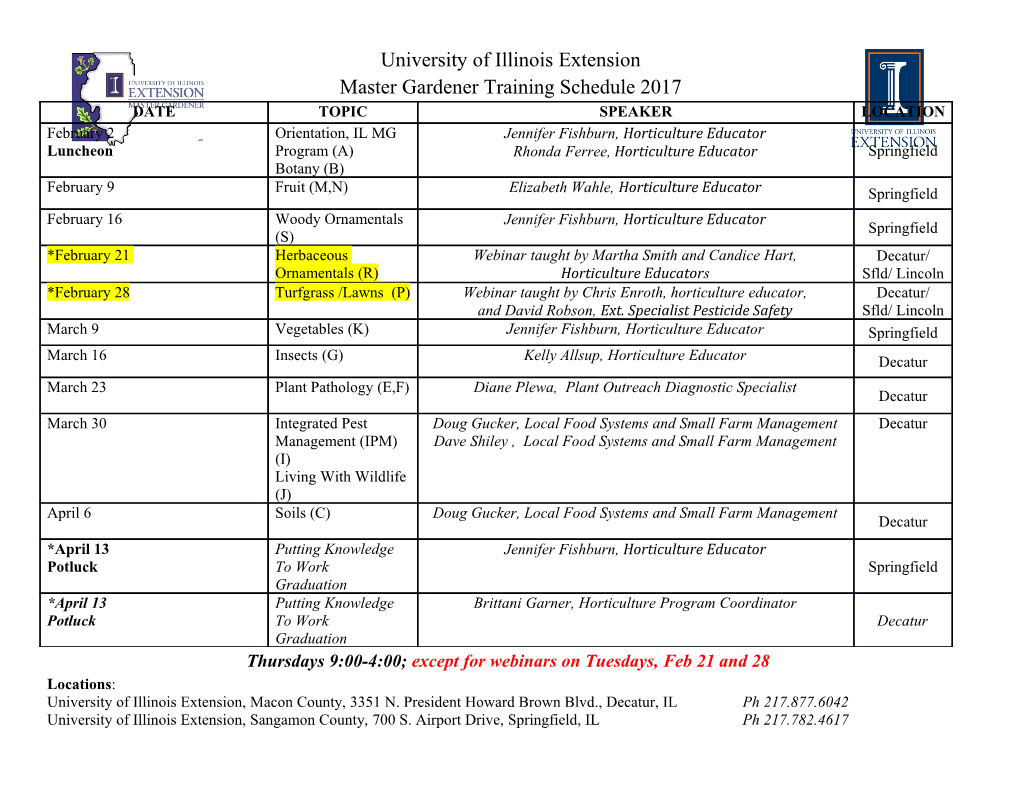
Imperial Journal of Interdisciplinary Research (IJIR) Vol-2, Issue-9, 2016 ISSN: 2454-1362, http://www.onlinejournal.in Design & Development of Special Purpose Machine for its Cycle Time Optimization A. H. Rasal1, Prof. (Dr.) V. R. Naik2 & R. A. Mane3 1M.E. (Mech) P.D.D.student, Textile and Engg. Institute, Ichalkaranji, Kolhapur. 2Head of Mechanical Department, Textile and Engg. Institute, Ichalkaranji, Kolhapur. 3Asst. manager, Paranjape Autocast Pvt, Ltd,,Satara. Abstract - The growth of Indian manufacturing the experience of the shop floor machine tool sector depends largely on its productivity & operators for optimal selection of cutting quality. Productivity depends upon many factors, conditions and tools. Considerable efforts are still one of the major factors being manufacturing in progress on the use of hand book-based efficiency with which the operation /activities are conservative cutting conditions and cutting tool carried out in the organization. Productivity can be selection at the process planning level [8]. improved by reducing the total machining time, Sawing is a metal cutting process which combining the operations etc. In case of mass makes use of cutting tools such as band saw, production where variety of jobs is less and circular saw. These tools are used on conventional quantity to be produced is huge, it is very essential sawing machines i.e. a worker holds the job on the to produce the job at a faster rate. This is not machining table and slides it further in the direction possible by using general purpose machines. The of rotating saw and the cutting process takes place. best way to improve the production rate In this paper, the component is a cylinder head (productivity) along wit quality is by use of special made of aluminium alloy (IS designation 4223). It purpose machine. The existing manually operated is cut on a band saw machine. The problems while band saw machine will be replaced with a special using this machine are discussed and solution of a purpose machine. This paper deals with such special purpose machine is presented. development undertaken for similar job under consideration. 2. Component information 1. Introduction Metallurgical specification of the In the special purpose machine, a carbide component: tipped circular saw is used which is stationary, Component under investigation and design while the table on which the component is mounted is having the following material specifications, in the fixture is given a hydraulic feed [1]. Due to the automatic feeding system the total cycle time is Name of the component : Cylinder head (Pulsar decreased. Added benefits include less chance for engine) error, less accumulated tolerance error, and Material : Aluminium alloy (IS designation 4223) eliminate changes in the saw[2]. In such a special purpose machine, the component to be machined is Hardness : 160-180 BHN hydraulically clamped in the fixture on the table. It Mass : 3.8 kg is not possible neither to clamp two or more components on the table; nor use two or more Component: tables in the same machine. Thus, in every Pulsar engine: Cylinder head. movement of the feed, only one component can be clamped in the fixture of such a machine. Next Description: component cannot be loaded before the previous The component is a Cylinder head of part is not finished. Once machining of a part is Bajaj Pulsar & its material is aluminium alloy. It is started it cannot be interrupted. manufactured through the casting process. The The customer demands the product of Cylinder head has a gate / riser, which is to be cut- right quality, right quantity, right cost, & at right off. The total thickness of the material to cut is time. Therefore it is necessary to improve about 110 mm. productivity as well as quality. One way to achieve this is by using special purpose machine [3]. The Gate thickness specification: As the Cylinder manufacturing industries depend on the skill and head is manufactured through the casting process, Imperial Journal of Interdisciplinary Research (IJIR) Page 1659 Imperial Journal of Interdisciplinary Research (IJIR) Vol-2, Issue-9, 2016 ISSN: 2454-1362, http://www.onlinejournal.in the thickness of material to cut can vary upto a few mm. Thickness of the material to cut: 110 mm. Need: A skilled labour is required for removal of gate, as it is important that, during the cutting of extra material the edge of combustion chamber is not damage. Thus, it is a very intricate and precision work[5]. During the process, the worker has to repeat several cuts of lesser dimensions. This repeatability of cuts increases the cycle time of the process, for a single engine. Also as the number of cuts goes on increasing, the material of the tool, i.e. the band saw gets worn out. This decreases the rate of productivity of band saw. This causes the frequent change of the band saw. Thus it involves additional capital investment Fig. 2: The component. in tooling [4]. 4. Compilation of data of machining When the cutting of gate is in progress, there is time of sawing a possibility of change in the angle of blade. This The data for 30 components under taken causes the bending of the blade and eventually its from machining cycle time inspection on band saw breakage & also there is a possibility of damage to machine, the data found as the engine. follows: All these problems of the process are required MACHINING CYCLE TIME to be eliminated. 1.28 3. Working process & component 1.26 1.24 images 1.22 WORKER 01 WORKER 02 1.2 WORKER 03 1.18 1.16 MACHINING TIME (MIN.) 1.14 1 2 3 4 5 6 7 8 9 10 WORKPIECE NUMBER Fig. 3: Graphical representation of machining time of the workers. 5. Problems identified by using conventional machine: The gate cutting is done by conventional band saw machines the difficulties noticed are as, Fig. 1: The manual cutting process of gate of the component. Manual handling of the component results in excess idle time: The process of gate cutting is done by the worker, on a conventional band saw machine. During the cutting process, the worker has to adjust the cut properly, in case the cut is not correctly positioned, the idle time increases. Band saw & the component requires more setting time : The conventional band saw machine consists of a vertically mounted band saw. This band saw requires accurate tensioning to avoid its Imperial Journal of Interdisciplinary Research (IJIR) Page 1660 Imperial Journal of Interdisciplinary Research (IJIR) Vol-2, Issue-9, 2016 ISSN: 2454-1362, http://www.onlinejournal.in breakage, thus it requires to be set by tightening at the end screws, at specific intervals. The component is adjusted at regular intervals so as to avoid any damage to the component. Need of skilled labour & surface finish: The process of cutting the gate on the conventional band saw machine is very intricate process. The band saw rotates at a very high speed; the worker has to be very careful while cutting the gate. Thus there is a need of skilled labour which increases the labour wages. If unskilled labour is employed, the surface finish achieved is poor, thus affecting the quality of the component. Bending of the blade and its breakage: The cutting of the gate is done using a band saw, mounted on the pulleys. Initially the Fig. 4: Conceptual model of the special purpose positioning of band saw is a time consuming machine. process. While cutting the gate, there is a The machine structure is a sheet metal possibility of change in the angle of blade. This work and has rigid supports of M.S. square bars as causes the bending of the blade and eventually its well as cross stiffening ribs to ensure adequate breakage. This involves additional capital rigidity and strength. Inside it are housed the investment in toolings & also it is hazardous to the various mechanisms as the carbide tipped circular [7] worker working on the machine. saw , workpeice carriage, speed gear box, electric motor, belt and pulley drive unit, pipes and hoses. Damage to the engine: The workpeice carriage moves to and fro on the The performance of engine depends on the guideways located at the bottom of the slide. accuracy with which it is manufactured. The Hydraulic clamping is used for clamping the bending of the blade might cause inaccuracy in the workpiece rigidly to sustain the cutting forces. part geometry of the engine, thus hampering its Proximity sensors are used to define the distance performance [6]. The surface finish achieved is of travelled by the workpeice carriage. Screw poor quality. This also leads in the increase in the conveyor is used to remove the chips developed rejection quantity of engines. through the sawing process. The hydraulic system consists of a Less productivity: hydraulic power pack which consists of a reservoir Due to the increase in the idle time the tank with fluid stored in it. A FRL unit is used rate of production is affected. Productivity also proper filtration, regulation and lubrication of the decreases, as the setting time required for the fluid throughout the system. The fluid is circulated component & saw is large. In the component, the through the system by a pump associated with the thickness of the material to cut is about 110 mm. At motor. Direction control valve is used to direct the present the cycle time required is about 1.22 min / fluid flow in appropriate direction. The flow rate component. Thus the target completion within the and pressure of fluid is controlled through the flow specified time is not achieved. and pressure control valve. Actuators are used to 6.
Details
-
File Typepdf
-
Upload Time-
-
Content LanguagesEnglish
-
Upload UserAnonymous/Not logged-in
-
File Pages5 Page
-
File Size-