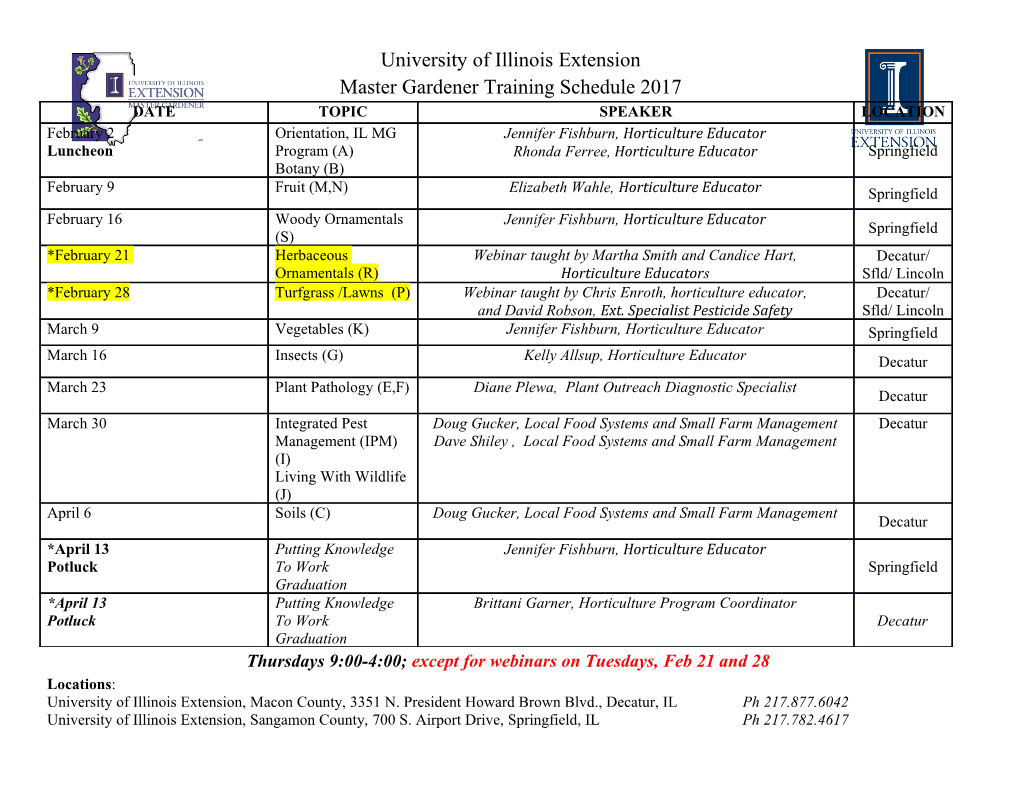
STATUS OF FAST BREEDER REACTOR DEVELOPMENT 500 °C. After several years of operation with a thermal reactor core (KNK I), IN THE FEDERAL REPUBLIC OF GERMANY, the plant has been run with fast, i.e. unmoderated, reactor cores since 1978 (KNK II). BELGIUM AND THE NETHERLANDS February 1987* While the fuel assemblies of the first fast core, KNK II/l, were identical with those of the Mk.Ia first core of the SNR 300 in their key parameters, the fuel assemblies of the second core loading, KNK 11/2 , correspond to the SNR 300 Mk.II R. HÜPER type, which is characterized by a high fuel density, 7.6 mm fuel rod diameter, Fast Breeder Project, and spark eroded spacer grids which, in the fuel assemblies of the test zone, Kernforschungszentrum Karlsruhe GmbH, are attached to the wrapper tube by means of flow aprons. Karlsruhe, Federal Republic of Germany The first fast core had been unloaded in 1982 after a peak burnup of 100.000 MWd/te. The fuel assemblies of the second core, which was commissioned iri mid-1983, have meanwhile reached an average burnup of 47.000 MWd/te. One test Abstract fuel assembly transferred from the first to the second core has reached an average burnup of 125.000 MWd/te by late 1986. In 1967 and 1968, the Federal Republic of Germany, the Kingdom of Belgium, and the Kingdom of the Netherlands ("DeBeNe") agreed in a joint program to develop In the course of the burnup of the second core so far, a change in the outlet breeder reactors. The following research organizations have taken part in this effort: temperatures of the Mk.II fuel assemblies has been observed. Probably as a result of some redistribution of the coolant flow from the test zone to the driver zone due to increased pressure loss in all fuel assemblies, the outlet Kernforschungszentrum Karlsruhe (KfK), INTERATOM, Bergisch Gladbach, temperatures of the test zone fuel assemblies rise, while those of the driver ALKEM, Hanau, assemblies drop. An extensive program of research is being conducted to eluci­ date the causes of these temperature changes. SCK/CEN, Mol, Belgonucléaire, Brussels, Four fuel assembly failures have so far occurred in operation of the KNK 11/2 core. Two test assemblies and two driver assemblies were involved. Operation of ECN, Petten, three of the assemblies was continued up to 35 days at full load and part load, TNO, Apeldoorn, respectively, after the failure had been noticed. Spotting the failed fuel NERATOOM, The Hague. assemblies in KNK II is done by a combination of load tilting operation and a dry sipping test conducted by the fueling machine. The failed fuel assemblies are subjected to extensive post-irradiation examinations at the Hot Cells of The three institutions mentioned above have been associated since 1977 in the KfK. Entwicklungsgemeinschaft Schneller Brüter. KfK, INTERATOM, and the French Commissariat à l'Energie Atomique entered into contracts in 1977 about close cooperation in the fast breeder field, to which the Belgian and Dutch partners Irradiation and post-irradiation examinations of specimens of the 1.6770 type material of the KNK II reactor vessel, which had been loaded in the first acceded. materials test assembly, have been concluded. The integrity of the vessel wall has been found to be unimpaired by irradiation effects, even in the long term. The results of activities carried out by the DeBeNe partners in 1986 have been compiled in this report. The report begins with a survey of the fast reactor plants, followed by an R&D summary. In an additional chapter, a survey is given Post-irradiation examination of a KNK 11/2 absorber assembly has also been of international cooperation in 1986. completed. The absorber rods of the first core were filled with boron carbide granulate. Only some test rods contained B.C pellets of the kind used for KNK II follow-on loadings and for the SNR 300. I. SUMMARY An investigation is being carried out of the KNK II steam generator in order to see whether the noise of the water-sodium interaction, which would arise in a steam generator failure, can be detected. For this purpose, a leak simulation 1. Operating Experience of KNK II in Karlsruhe source and ten acoustic sensors have been installed. KNK, a compact sodium-cooled reactor, is an experimental nuclear power station of 20 megawatts electric power, whose core is cooled by liquid sodium at approx. 2. Commissioning of the Kalkar Nuclear Power Station (SNR 300) In 1973, construction near Kalkar was begun of the 300 MWe SNR 300 prototype * Translated by R. Friese. breeder power plant by Internationale Natrium-Brutreaktor Bau GmbH (INB). The plant owner is Schnellbrüter-Kernkraftwerksgesellschaft mbH (SBK). Both firms 3. Planning of the SNR 2 are joint German-Belgian-Netherlands enterprises; in addition, the state-owned British CEGB holds an interest in SBK. The company awarding the contracts for planning and construction of the SNR 2 (1.500 MWe pool type facility) will be the Europaische Schnellbrüter-Kernkraft- Construction of the plant was largely completed in 1985 after lengthy delays, werksgesellschaft (ESK). Its shareholders are SBK, the Italian ENEL, and the most of them caused by political conditions. After the sodium systems had been French EdF. The project is based on the Breeder Convention agreed upon in 1973, filled, functional tests were carried out within the framework of pre-nuclear under which construction of the SPX 1 in France, now commissioned, was to come commissioning. A number of problems were overcome in this phase in 1986: first. Because of a number of leaks observed, the welds of the four dump tanks and Planning work for the SNR 2 is to provide an assured development status re­ leakage interception vessels on the secondary side were redone. As a consequence presenting an attractive basis on which to decide about the next European of similar technological, design and welding conditions as in the sodium dump breeder. Points of primary interest are engineered safeguards (passive safety and leakage interception vessels, also the partly loaded cold traps were re­ concept) and economic considerations. paired and regenerated. On the basis of the well-known inherent properties of breeder facilities, the To reject the higher-than-rated heat load, new blowers were installed in the safety potential is to be exploited further, e.g., by passive natural cir­ reactor closure head cavity. Additional tanks designed to collect leakage oil culation systems for decay heat removal. Studies of the component design va­ were installed near the primary pumps. riants of decay heat removal systems performed so far, and also the arrangements of these components, are at present being evaluated in detail by the French and Labor-intensive rerouting of cables took until mid-February 1986; it had become Italian partners. Also the British side contributes to this effort. necessary in order to meet the tighter redundancy requirements in the decay heat removal trains. Passive day heat removal is one of the key features of an accident management concept designed to minimize active measures. The studies devoted to this In January 1986, a vibration measurement lance introduced into the reactor complex of problems are intended to result in a new kind of emergency power vessel was ruptured in an attempt to dismantle it for reworking. The disrupted supply concept and a consistent control panel concept. part of the lance and several small parts which had stuck in the reactor vessel were retrieved. In March 1986, the primary system and the reactor vessel were The concept for handling core assemblies has been advanced far enough to allow again filled with sodium. consistent handling under sodium of irradiated core assemblies and, hence, solutions for passive decay heat removal to be defined. Conceptual proposals An abnormally high moisture content was measured in the cover gas of the re­ have been made for the layouts of the secondary systems and the handling de­ actor. It came from the basalt granulate used to shield the reactor closure vices. head. The basalt was dehumidified at a sodium temperature of about 240 °C. Breeder plants achieve clearly higher burnups than light water reactors. One of The tests of the emergency power supply system were completed. The systems the targets in planning for the SNR 2 ist a considerably higher burnup also designed for decay heat removal (decay heat removal specifically for each leg relative to the SNR 300. Besides this point, which is important especially with through the heat sink in the water/steam system and the emergency core cooling regard to fuel cycle costs, lower construction costs are expected to arise from system) were tested successfully. the passive safety concept. Since the end of 1986, the Kalkar facility has been ready for acceptance of the The SNR 2 allows cost reductions to be achieved especially for the following fuel assemblies. reasons : In July 1986, the North-Rhine-Westphalian State Minister of Economics, who is No safety related decay heat removal through the "balance-of-plant" sy­ responsible for issuing reactor permits, surprised everyone with the announce­ stems; consequently, conventional components and process engineering ment of reservations against further permits, because of his new assessment of simplifications are possible. facts well-known for quite a time. The German Advisory Committees on Reactor Safeguards (RSK) and Radiological Protection (SSK) as well as the Rhineland Absence of extensive emergency power supply installations because the Technical Inspectorate (TQV) had not raised any objections on grounds of tech­ sodium systems can be used for passive decay heat removal. nical safety against loading the fuel assemblies and conducting zero power tests in the SNR 300.
Details
-
File Typepdf
-
Upload Time-
-
Content LanguagesEnglish
-
Upload UserAnonymous/Not logged-in
-
File Pages19 Page
-
File Size-