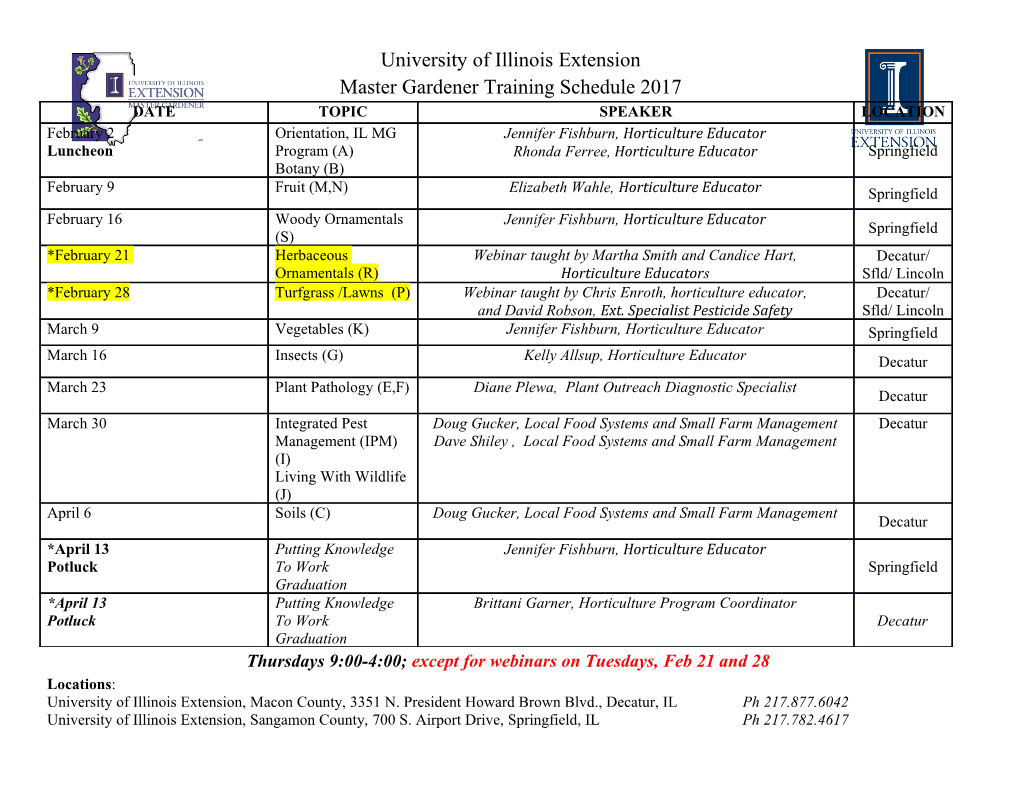
Continuous Pulping Processes Disclaimer: In some cases, the Million Book Project has been unable to trace the copyright owner. Items have been reproduced in good faith. We would be pleased to hear from the copyright owners. Queensland University of Technology. Brisbane, Australia TAPPI STAP SERIES 1 The Training of Supervisors in Corrugated Box Plants: Ten Lesson Plans; Lesson 11: Time Study 2 Petroleum Waxes: Characterization, Performance, and Addi­ tives 3 *Preparation, Circulation, and Storage of Corrugating Adhesives 4 *Operations Research and the Design of Management Informa­ tion Systems 5 Management Science in Planning and Control 6 Technical Evaluation of Petroleum Waxes * Out of print. Photocopy may be obtained from University Microfilms, Ann Arbor, Michigan 48106. Johan Richter Pioneer in Continuous Pulping Technology Born in Lier, Norway, in 1901 Continuous Pulping Processes 12 Lectures By Sven Rydholm Director of Research Billeruds AB SPECIAL TECHNICAL ASSOCIATION PUBLICATION • STAP NO. 7 Gardens Point A22810250B Continuous pulping processes : 12 lectures A22810250B ©Copyright 1970 by Technical Association of the Pulp and Paper Industry 360 Lexington Avenue, New York, N. Y. 10017 Library of Congress Catalog Card Number: 74-140131 Printed in the United States of America By Mack Printing Company, Easton, Pa. Preface This book is a compilation of lectures given at the TAPPI Pacific Section Meeting in Seattle, Wash., in September 1968. They dealt with experiences in continuous pulping obtained over more than one decade at Billeruds AB in collaboration with AB Kamyr. One reason for my choice of topic was that Kamyr digesters have dom­ inated the most vital operation in our industry for more than ten years and still do, although some signs of healthy competition have appeared. A second reason was that the Kamyr digesters are now becoming quite di­ versified, and thus the lectures would have to cover all pulping processes needing a pressure vessel. A third reason was that I have been involved in developing many of these process variants during my past sixteen years in Billerud research. A final reason was that it was then 30 years since Johan Richter started the development of a continuous digester. Someone, perhaps outside his company, should tell the story of the devoted efforts from him and his associates to realize an idea, in which he firmly believed, in spite of innumerable troubles and a general disbelief from most people in this industry for a good many years. I am not able to do that initial story justice, but shall instead cover some experiences of continuous cooking gained during the last decade. In preparing the lectures, I have endeavored to give a brief background of wood chemistry and pulping chemistry, which simplifies the understanding of what goes on in the digester and what comes out of it. The theory is treated more extensively in my book "Pulping Processes" (Wiley, New York, 1965). The treatment of the continuous cooking itself includes the results of work undertaken by my company. I think I may make clear that continuous cooking is now ready for all pulping processes and offers possibilities for carrying out process modifications which only with difficulty are feasible in batch cooking. It gives a system available for the largest mill units conceivable, lends itself well to control and automation, offers advantages in combina­ tion with other mill operations, and yields pulps which meet the highest quality standards. It is one. of the weapons needed in this industry to meet the competition from other materials in serving the markets of today and tomorrow. vii viii Continuous Pulping Processes Thanks are due to Billerud and Kamyr for allowing the comprehensive publication of all results which were previously unpublished or published only in scattered presentations at Scandinavian and American meetings and magazines. Actively involved in the administration of the Jossefors experimental pulp mill were G. Ojermark, S. Haglund, and W. Ameen of Billerud, and in the administration of the research program T. Bergek, L. JQrgensen, and myself from Billerud, K. Dahl, J. Richter, and T. Christen- son from Kamyr. Actively involved in carrying out the experimental work during different periods over the 16 years were, from Billerud, my­ self, G. Arnborger, S. Boren, T. Krantz, J. Grundstrom, U. Mohlin, E. Nilsson, G. Annergren, A. Haglund, K. Mattsson, S. Lokrantz, S. Wenneras, B. Dillner, and an experienced crew of 10-20 men. From Kamyr, particu­ larly, the following were involved in the experiments at varying periods: H. Ortqvist, L. Jansson, A. Backlund, S. Jungeblad, and L. Westerlurtd. The sparks necessary to carry the work over the critical periods and to yield the successful redesigns of the machinery were supplied by Johan Rich­ ter. With Knut Dahl, the managing director of Kamyr, and Ake Pihlgren and Gunnar Hindemark, former and present managing directors of Bil­ lerud, the financing of the program has rested. This has required from them substantial courage and belief in the soundness of research and de­ velopment efforts in machine and process design, perhaps rewarded in the continued success of digester sales of Kamyr and in the successful opera­ tion of continuous pulping processes at Billerud. Part of the work has also received substantial financial support from the Swedish development fund Malmfonden. Sven Rydholm Billeruds AB Saffie, Sweden Lectures 1 Historical Development of Continuous Kraft Cooking... 1 2 Sulfite Cooking Process Theory 11 3 Continuous Acid Sulfite Cooking 33 4 Continuous Bisulfite Cooking 51 5 Continuous Neutral Sulfite Cooking 63 6 Kraft Cooking Process Theory 75 7 Continuous Conventional Kraft Cooking 97 8 Continuous Prehydrolysis-kraft Cooking 105 9 Continuous Modified Kraft Cooking 121 10 Washing Process Theory 159 11 Continuous Digester Washing 173 12 Technical and Economic Aspects of Present and Future Developments of Continuous Pulping 179 Tndev 193 Lecture I Historical Development of Continuous Kraft Cooking The detailed story of the development of the continuous kraft digester began with a 5 ton/day pilot plant at Karlsborg in northernmost Sweden in 1938 and continued, (after an interlude during the war) in 1948 at Fengersfors, a small kraft mill in Central Sweden. During the period 1948-52, Fengersfors took the brave stride to continuous cooking from its 19th-century technique of stationary batch digesters, which opened at side lids near the bottom and were emptied manually into wheelbarrows to carry the pulp to the washing and screening departments. In this mill, the Kamyr enthusiasts introduced their first commercial unit, for 50 tons/day. The basic principle of a downflow digester with a balanced high-pressure pocket feeder (Fig. 1.1) was already established, but they had a long way to go. The high-pressure feeder is still the key feature of the Kamyr system. It solves the problem of introducing the wood chips into the high-pressure system without mechanical compression damage, without excessive wear on the feeder, and without losses of steam from the pressure room. The chips fall from the steaming vessel into the pocket of the feeder when the pocket is in vertical position, and are packed by a liquor circulation. The revolving plug of the feeder contains 2-4 such pockets at varying angles, so that always at least one pocket will receive chips. The plug, which is slightly conical, is a precision work of stainless steel in an iron housing with a monel sleeve. In turning, the plug delivers the pockets successively into a horizontal position, in contact with the high-pressure feeding line. By a circulation pump, the chips are then conveyed into the digest­ er. The pocket is thus emptied of chips but full of liquor when it arrives again at a vertical position. A liquor volume corresponding to the volume of the new chip charge must thus leave the system at an overflow in the chip chute and has to be pumped into the system again by a high-pressure pump, together with the small leakage volume from between plug and housing, and with the cooking liquor charge. The first commercial continuous kraft digester is outlined in Fig. 1.2. Its basic design is similar to that of the present digesters, but many improvements have been made. The chips are charged from a hopper 1 2 Lecture 1 Fig. 1.1. Principle of the balanced high-pressure pocket feeder. over a measuring wheel into a low-pressure feeder, which introduces the chips into the horizontal steaming vessel. After 3-5 min steaming, the chips fall into the high-pressure feeder and are pumped into the digest­ er. A top screw or separator keeps a strainer clean, through which the feeding hquor returns to the circulation pump. A torsional indicator at the end of the screw feels the chip level in the digester and gives an impulse to the discharge system for balancing the charge and discharge flows. Cooking liquor is fed into the digester top over the chip feeding circulation, and is heated in a new circulation somewhat further down the Historical Development of Continuous Kraft Cooking 3 BLOW STEAM RECOVERED FOR PRESTEAMING Fig, 1.2. First commercial Kamyr kraft cooking system. digester. The circulation strainer is kept clean by the moving chip column, but there was the problem of distributing the heated liquor over the digester cross section. The initial arrangement was improved in co­ operation with the Fengersfors mill staff, of which the contributions of Ragnar Jonsson particularly should be mentioned. He also cooperated in the improvement of the bottom scraper and discharge problems, which were connected with the pulp quality. The distribution of the cooking liquor was solved by the introduction of the central pipe, ending just above the level of the circular strainer. The final solution of the dis­ charge was yet to come.
Details
-
File Typepdf
-
Upload Time-
-
Content LanguagesEnglish
-
Upload UserAnonymous/Not logged-in
-
File Pages200 Page
-
File Size-