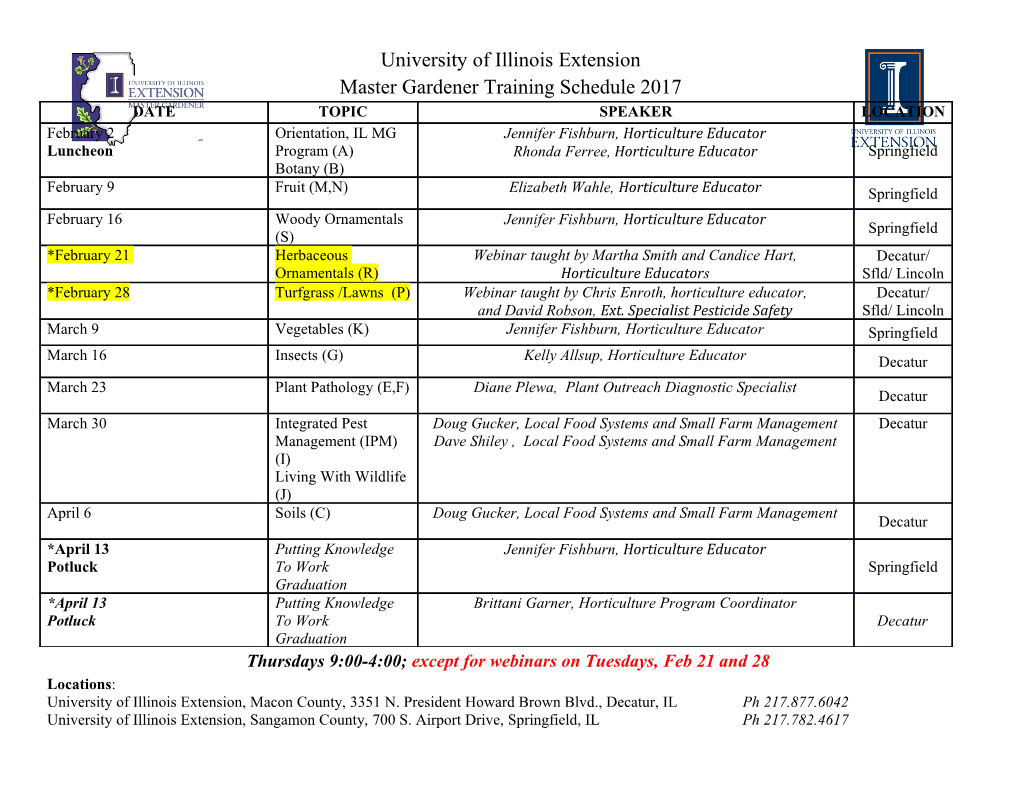
metals Article Modeling of Precipitation Hardening during Coiling of Nb–Mo Steels Jean-Yves Maetz 1, Matthias Militzer 1,*, Yu Wen Chen 2, Jer-Ren Yang 2, Nam Hoon Goo 3, Soo Jin Kim 3, Bian Jian 4 and Hardy Mohrbacher 5 1 Centre for Metallurgical Process Engineering, The University of British Columbia, Vancouver, BC V6T 1Z4, Canada; [email protected] 2 Department of Materials Science and Engineering, National Taiwan University, Taipei 10617, Taiwan; [email protected] (Y.W.C.); [email protected] (J.-R.Y.) 3 Technical Research Center, Hyundai-Steel Company, Dangjin 167-32, Korea; [email protected] (N.H.G.); [email protected] (S.J.K.) 4 Niobium Tech Asia, Singapore 068898, Singapore; [email protected] 5 NiobelCon bvba, 2970 Schilde, Belgium; [email protected] * Correspondence: [email protected]; Tel.: +1-604-822-3676 Received: 21 August 2018; Accepted: 21 September 2018; Published: 25 September 2018 Abstract: Nb–Mo low-alloyed steels are promising advanced high strength steels (AHSS) because of the highly dislocated bainitic ferrite microstructure conferring an excellent combination of strength and toughness. In this study, the potential of precipitation strengthening during coiling for hot-strip Nb–Mo-bearing low-carbon steels has been investigated using hot-torsion and aging tests to simulate the hot-rolling process including coiling. The obtained microstructures were characterized using electron backscatter diffraction (EBSD), highlighting the effects of Nb and Mo additions on formation and tempering of the bainitic ferrite microstructures. Further, the evolution of nanometer-sized precipitates was quantified with high-resolution transmission electron microscopy (HR-TEM). The resulting age hardening kinetics have been modelled by combining a phenomenological precipitation strengthening model with a tempering model. Analysis of the model suggests a narrower coiling temperature window to maximize the precipitation strengthening potential in bainite/ferrite high strength low-alloyed (HSLA) steels than that for conventional HSLA steels with polygonal ferrite/pearlite microstructures. Keywords: advanced high strength steels; HSLA steels; precipitation strengthening; tempering; bainitic ferrite; EBSD; austenite-to-ferrite transformation; hot-torsion test; coiling simulation 1. Introduction High strength low-alloyed (HSLA) and similar microalloyed low-carbon steels have been developed since the 1960s and their production continuously increases, especially for automotive and pipeline industries, because of their high strength, excellent ductility, and good weldability [1–3]. Originally the high strength of these steels was obtained by a combination of refining the ferrite-pearlite microstructure and precipitation hardening due to adding microalloying elements such as Nb, V, or Ti [1,4]. Optimizing the coil cooling process is critical to realize the precipitation strengthening potential in hot band. Models have been developed to predict the precipitation behavior for these conventional HSLA steels [4,5]. Nowadays there is a strong driving force to develop new advanced high strength steels (AHSS) to meet the future challenges in the automotive, energy and construction sectors [2,6]. In particular, Nb-Mo-bearing HSLA steels offer a tremendous opportunity to develop high-performance steels Metals 2018, 8, 758; doi:10.3390/met8100758 www.mdpi.com/journal/metals Metals 2018, 8, 758 2 of 23 with increased strength [7–10]. Nb is known to be a powerful microalloying element to accumulate strain in austenite by delaying recrystallization because of solute drag and/or strain-induced precipitation [11–13]. Mo addition affects considerably the austenite-to-ferrite transformation by delaying polygonal ferrite formation, inhibiting pearlite and promoting bainite formation [7,8,14]. The high dislocation density and the resulting fine substructure significantly increases the strength of these steels. In addition to transformation hardening, the precipitation strengthening potential of Nb–Mo HSLA steels have been observed to be substantial [8,14]. Indeed, in highly dislocated ferrite or bainite, precipitation occurs on dislocations [9,15,16]. The precipitation strengthening is thus expected to be promoted as compared to polygonal ferrite by a higher precipitate density as the dislocation density increases [8,14]. In addition, Mo has a supplementary potential for precipitation strengthening by increasing the volume fraction of precipitates as (Nbx, Mo1−x) (CN) mixed carbides or carbo-nitrides have been observed [8,9]. The goal of this study is to develop a precipitation strengthening model for hot-rolled Nb–Mo HSLA steels applicable to industrial coiling conditions. Four low-carbon steels with various levels of Nb and Mo content were investigated. Laboratory hot-torsion tests were performed to simulate the hot-rolling process. The hardening potential was assessed performing aging at typical coiling temperatures. Systematic electron backscatter diffraction (EBSD) and high-resolution transmission electron microscopy (HR-TEM) studies were conducted to capture the microstructure and precipitation changes. A first version of the precipitation strengthening model using the approach used for conventional HSLA steels [5] has been presented previously [17], in which tempering of the bainitic-ferrite microstructure during aging was not considered even though it appears to have a non-negligible effect on the resulting mechanical properties [18]. The present paper provides the detailed microstructure analyses for tempering and coiling simulations at various temperatures to assess the microstructure contribution to mechanical properties as well as a revised age hardening model that considers both precipitation and transformation hardening contributions. The proposed modeling approach is validated with laboratory coil cooling simulations of the investigated Nb–Mo HSLA steels. 2. Materials and Methods The steel compositions are similar to those of typical industrially hot-rolled HSLA steels but with systematic variations in the Nb and Mn contents, as listed in Table1. The steels are laboratory steels that were vacuum melted to produce 50 kg ingots from which torsion specimens were machined with a gage section of 12.7 mm in length and a diameter of 10.3 mm. Table 1. Chemical composition (wt.%) of the four investigated steels. Steel C Mn Si Nb Mo Nb1 0.08 1.5 0.2 0.05 0 Nb1Mo1 0.08 1.5 0.2 0.05 0.1 Nb1Mo2 0.08 1.5 0.2 0.05 0.2 Nb2Mo2 0.08 1.5 0.2 0.1 0.2 The thermo-mechanical simulations are summarized in Figure1. The as-received specimens were subjected to hot-torsion tests using a DSI HTS 100 hot torsion tester (Dynamic Systems Inc., Poestenkill, NY, USA) in order to simulate hot-rolling where the nominal deformation occurs within approximately a layer of 1 mm from the sample surface [19]. The as-received samples were soaked at 1250 ◦C for 15 min to dissolve the Nb and Mo containing precipitates, before undergoing 10 torsion passes at a strain rate of 1/s between 1100 and 900 ◦C, including three roughing passes (R1–R3) and seven finishing passes (F1–F7) for a total strain of 3.2. The details of the hot-torsion test schedule are shown in Table2. Subsequently, different cooling strategies were employed to produce (i) as-quenched (AQ), Metals 2018, 8, 758 3 of 23 i.e. under-aged, specimens and (ii) coil cooling simulated specimens. In the first test series (path 1 in Figure1), the primary goal of the hot-torsion tests had been to create as-quenched specimens without Nb and Mo containing precipitates but with a typical hot-strip rolling microstructure for subsequent age hardeningMetals 2017, 7 tests, x FOR (path PEER REVIEW 2). The specimens were quenched with pressurized He-gas from3 900 of 24◦ C to 400 ◦C at an initial cooling rate of 40 ◦C/s followed by air cooling to room temperature. In the second pressurized He-gas from 900 °C to 400 °C at an initial cooling rate of 40 °C/s followed by air cooling series of hot torsion testing (path 3 in Figure1), the specimens were cooled from 900 ◦C to a designated to room temperature. In the second series◦ of hot torsion◦ testing (path 3 in Figure◦ 1), the specimens coilingwere temperature, cooled fromT c900, in °C the to range a designated of 650 coilingC to 500 temperature,C at a cooling , in rate the ofrange 40 ofC/s 650 followed °C to 500 by °Ccooling at ◦ at 0.5coolingC/min rate for of 3 40 h °C/s to simulate followed coil by cooling cooling. at 0.5 °C/min for 3 h to simulate coil cooling. FigureFigure 1. Summary 1. Summary of of the the variousvarious thermo-mechanical thermo-mechanical trea treatmentstments employed employed in this instudy: this path study: 1 for path 1 foras-quenched as-quenched condition, condition, path path2 for 2isothermal for isothermal age hardening age hardening treatments, treatments, and path 3 and for pathcoiling 3 for coilingsimulation. simulation. Table 2. Table 2.Schedule Schedule forfor hot-torsion tests. tests. PassPass R1–R3 R1–R3 F1 F1 F2 F2 F3F3 F4 F4 F5 F5F6 F7 F6 F7 Temperature (◦TemperatureC) 1100 (°C) 10241100 1024 982 982 958958 950 950 922 922910 900 910 900 Strain (1 s−1 rate) 0.33 each 0.35 0.5 0.4 0.3 0.3 0.3 0.1 Strain (1 s−1 rate) 0.33 each 0.35 0.5 0.4 0.3 0.3 0.3 0.1 Interpass time (s) 10 4 2.4 1.6 1.2 0.8 0.6 - Interpass time (s) 10 4 2.4 1.6 1.2 0.8 0.6 - The as-quenched specimens were then subjected to isothermal aging tests (see path 2 in Figure The1) at as-quenched three temperatures, specimens i.e., were530 °C, then 580 subjected °C and 630 to isothermal °C, to cover aging the testsrange (see of typical path 2 incoiling Figure 1) at threetemperatures. temperatures, Heat i.e., treatments 530 ◦C, were 580 ◦ carriedC and 630out in◦C, a tube to cover furnace the under range argon of typical atmosphere.
Details
-
File Typepdf
-
Upload Time-
-
Content LanguagesEnglish
-
Upload UserAnonymous/Not logged-in
-
File Pages23 Page
-
File Size-