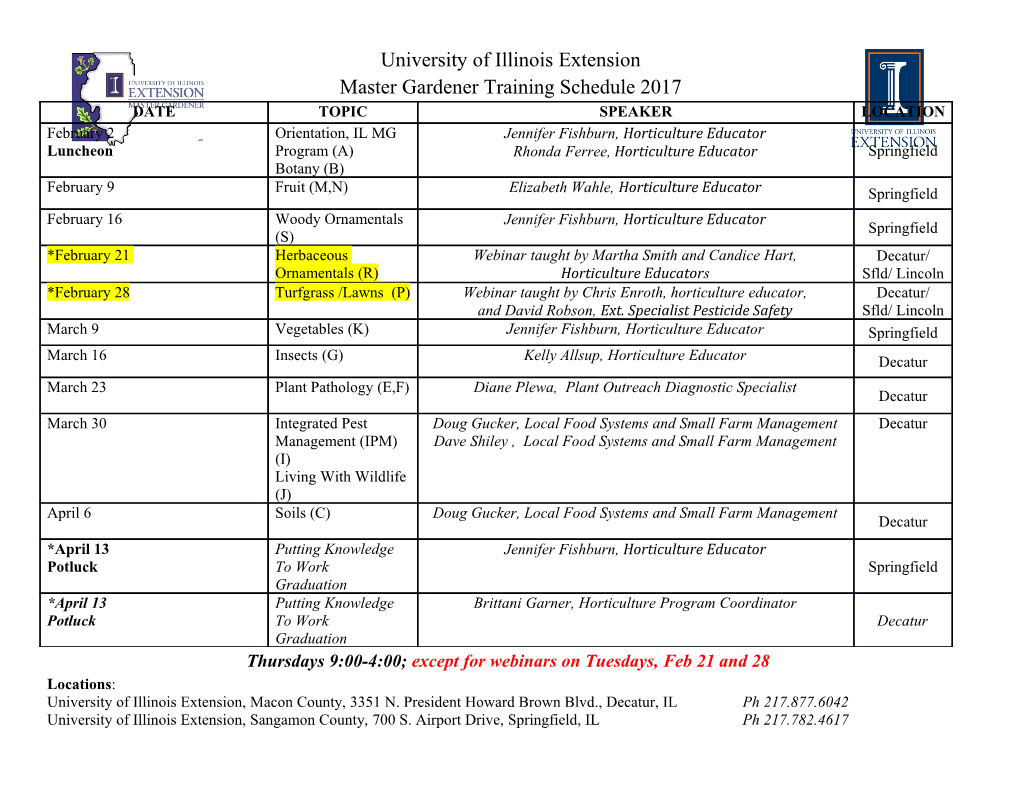
Fiber Optic Cable Splicing Two optical fiber splicing methods are available for permanent joining of two optical fibers. Both methods provide much lower insertion loss compared to fiber connectors. 1. Fiber optic cable fusion splicing – Insertion loss < 0.1dB 2. Fiber mechanical splicing – Insertion loss < 0.5dB Fiber optic cable fusion splicing Fiber optic cable fusion splicing provides the lowest-loss connection. Special equipment called fusion splicer is used to perform the fiber fusion splicing. The fusion splicer performs optical fiber fusion splicing in two steps. 1. Precisely align the two fibers 2. Generate a small electric arc to melt the fibers and weld them together High precision fusion splicers are usually bulky and expensive. With proper training, a fiber splicing technician can routinely achieve less than 0.1dB insertion loss splicing for both single mode and multimode fiber cables. Fiber optic cable splicing procedure (How to splice fiber optic cable) 1. Strip fiber cable jacket. Strip back about 3 meters of fiber cable jacket to expose the fiber loose tubes or tight buffered fibers. Use cable rip cord to cut through the fiber jacket. Then carefully peel back the jacket and expose the insides. Cut off the excess jacket. Clean off all cable gel with cable gel remover. Separate the fiber loose tubes and buffers by carefully cutting away any yarn or sheath. Leave enough of the strength member to properly secure the cable in the splice enclose. 2. Strip fiber tubes. For a loose tube fiber cable, strip away about 2 meters of fiber tube using a buffer tube stripper and expose the individual fibers. 3. Clean cable gel. Carefully clean all fibers in the loose tube of any filling gel with cable gel remover. 4. Secure cable tubes. Secure the end of the loose tube to the splice tray and lay out cleaned and separated fibers on the table. Strip and clean the other cable tube’s fiber that is to be spliced, and secure to the splice tray. 5. Strip first splicing fiber. Hold the first splicing fiber and remove the 250um fiber coating to expose 5cm of 125um bare fiber cladding with fiber coating stripper tool. For tight buffered fibers, remove 5cm of 900um tight buffer first with a buffer stripping tool, and then remove the 5cm of 250um coating. 6. Place the fusion splice protection sleeve. Put a fusion splice protection sleeve onto the fiber being spliced. 7. Clean the bare fiber. Carefully clean the stripped bare fiber with lint-free wipes soaked in isopropyl alcohol. After cleaning, prevent the fiber from touching anything. 8. Fiber cleaving. With a high precision fiber cleaver, cleave the fiber to a specified length according to your fusion splicer’s manual. 9. Prepare second fiber being spliced. Strip, clean and cleave the other fiber to be spliced. 10. Fusion splicing. Place both fibers in the fusion splicer and do the fusion splice according to its manual. 11. Heat shrink the fusion splice protection sleeve. Slide the fusion splice protection sleeve on the joint and put it into the heat shrink oven, and press the heat button. 12. Place splice into splice tray. Carefully place the finished splice into the splice tray and loop excess fiber around its guides. Ensure that the fiber’s minimum bending radius is not compromised. 13. Perform OTDR test. Perform a OTDR test of the splice and redo the splice if necessary. 14. Close the splice tray. After all fibers have been spliced, carefully close the splice tray and place it into the splice enclosure. 15. Bidirectional OTDR test (or power meter test). Test the splices with an OTDR or power meter from both directions. 16. Mount the splice enclosure. Close and mount the splice enclosure if all splices meet the specifications. Fiber optic cable mechanical splices Fiber optic cable mechanical splicing is an alternate splicing technique which does not require a fusion splicer. Mechanical splicing uses a small, mechanical splice, about 6cm long and 1cm in diameter that permanently joins the two optical fibers. A mechanical splice is a small fiber connector that precisely aligns two bare fibers and then secures them mechanically. A snap-type cover, an adhesive cover, or both, are used to permanently fasten the splice. Fiber optic cable mechanical splices are small, quite easy to use, and are very handy for either quick repairs or permanent installations. They are available in permanent and reenter able types. Fiber optic cable mechanical splices are available for single mode or multimode fibers. Their connection loss is usually less than 0.5dB which is much bigger than a 0.1dB fusion splice. Fiber Test Equipment Fiber Continuity Tester Visual Fault Locator Fiber Identifier Fiber Optic Inspection Microscope How to Splice Fiber Optic Cable The technology of fiber optics has been around for quite a few years. The technology came into full swing in the early 1970's. Since fiber optics is essential to the telecommunication industry, LAN and various networking projects, knowing how to splice these cables is mandatory. Simply put, fiber optic splicing is no more than the joining of two cables together. Any company using fiber optics will have trained technicians that are knowledgeable in how to correctly splice these intricate cables. Since this can be an expensive repair, knowledge and experience is a must. When dealing with fiber optics splicing, there are two methods of completing the work. A company needs to look at their long-term goals and finances when deciding which technique is best. Which method is chosen will basically be decided on how much money a business wants to spend. Depending on how precise the alignment needs to be, the more money will be spent on an alignment machine. The better the machine, means lower light loss and a better alignment will be achieved. Instructions Things You'll Need: • Fiber cleaver • Heat shrink wrap tubing • Silicone gel • Mechanical crimp protectors • Alignment machine • Fusion splicer • Connectors • Mechanical splice unit • Experienced technician Fusion Splicing 1. Step 1 Understand that fusion splicing is basically two or more optical fibers being permanently joined together by welding using an an electronic arc. The need for a precise cleaver is mandatory if you desire less light loss and reflection problems. Keep in mind that a quality cleaver for this precise work can run anywhere from $1000 to $4000. If a poor spice is made, the fiber ends may not melt together properly and problems can arise. 2. Step 2 Prepare the fiber by stripping the coatings, jackets and a tube, making sure that only bare fiber is left showing. You will want to clean all the fibers of any filling gel. A clean environment is imperative for a good connection. 3. Step 3 Cleave the fiber. A good cleaver is mandatory to obtain a successful splice. When fusing the fibers together, you can either align the fibers manually or automatic, depending on what type of machinery you have. Once you've obtained a proper alignment, an electrical arc is used to melt the fibers together creating a permanent weld of the two fiber ends. 4. Step 4 Protect the fiber with heat shrink tubing, silicone get. This will keep the optical fiber safe from any outside elements it may encounter or future breakage. Mechanical Splicing 5. Step 1 Understand that the basic difference between mechanical splicing and fusion splicing is you don't require a fusion splicer. It's also considered a quicker method and there is no heat involved. 6. Step 2 Prepare the fiber by stripping all the protective coatings away. You will then want to cleave the fiber as in fusion, but precision is not as critical to the splice. The ends are then mechanically joined together by positioning them inside the mechanical splice unit. In this step a connector or an adhesive cover is used to join the splice together. 7. Step 3 Protect the fiber with heat shrink tubing. As in fusion splicing, this will keep the optical fiber cable safe from the outside elements or breakage. Tips & Warnings • Depending on what type of industry you are working in, will generally decide which type of optical fiber splicing you decide to use. Though mechanical splicing costs more per splice, the initial investment will be much lower than fusion. In fusion optical splicing, the initial investment in machine costs will be much higher, but the cost per splice is much lower than mechanical. If precision alignments are mandatory, you're probably going to want to go with fusion splicing. Mechanical is quicker and easier, but the alignments of the fibers are not as accurate as fusion. Whichever method you decide to use, make sure the person doing the splicing is trained in the operation they will be performing Fiber Optic Cable Fiber optic "cable" refers to the complete assembly of fibers, strength members and jacket. Fiber optic cables come in lots of different types, depending on the number of fibers and how and where it will be installed. Choose cable carefully as the choice will affect how easy it is to install, splice or terminate and, most important, what it will cost! Choosing a cable What hazards will it face? Cable's job is to protect the fibers from the hazards encountered in an installation. Will the cables be exposed to chemicals or have to withstand a wide temperature range? What about being gnawed on by a woodchuck or prairie dog? Inside buildings, cables don't have to be so strong to protect the fibers, but they have to meet all fire code provisions. Outside the building, it depends on whether the cable is buried directly, pulled in conduit, strung aerially or whatever.
Details
-
File Typepdf
-
Upload Time-
-
Content LanguagesEnglish
-
Upload UserAnonymous/Not logged-in
-
File Pages62 Page
-
File Size-