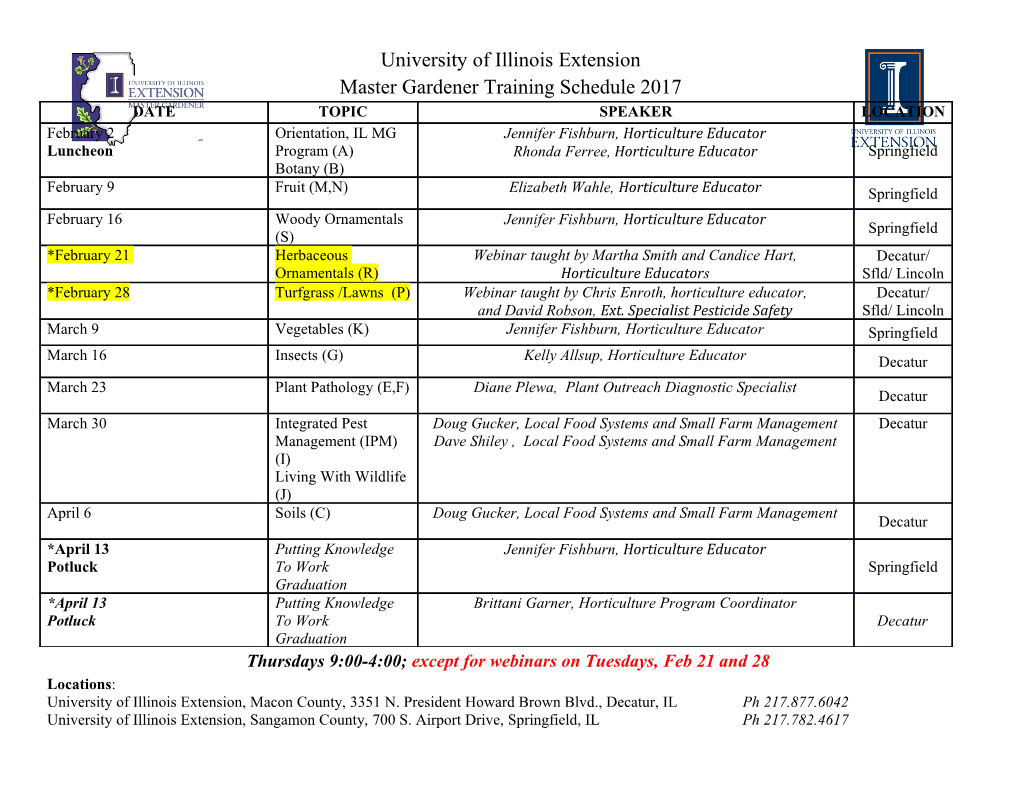
1988 Paper Paper Title Author Details Company Page No Field Experience with Flare Gas 1 Svein Louis Bersaas Statoil 3 Meters A New Gas Density Meter with J W Stansfield Schlumberger Industries 2 Reduced Velocity of Sound 15 Pieter M A van der Kam Nederlandse Gasunie Effect The EC Nozzle Transfer Pack age: Netherlands Measurement 3 A Flow Standard for High- Jos G M van der Grinten 21 Institute Pressure Gas Field Experience with Flare Gas 4 Gudmund Lindland Phillips Petroleum Co 46 Meters Compute r Concepts Data 5 Marius Wulffers HCS 56 Security and Availability The KO210 Flow Metering 6 Nils E. Standal Kongsberg Offshore A/S 60 Control System 7 Measuring the Flow of Wet Gas Greg Washington KSPEL 75 Pipeline Oil Analysis for 8 Oddfin Thowsen Phillips Petroleum Co 92 Allocation oat Ecofisk Sampling of H igh Vapour 9 Tom Welker Welker Engineering Company 106 Pressure Liquid Full Bore Continuous BS&W Jon Gjedebo Hitec AS 10 Measurement and Fiscal Bjørn G. Bjørnsen Statoil 107 Metering Scott Gaisford FMS Field -Based Water -in -Oil National Engineering 11 Nicholas W. King 124 Sampling Studies Laboratory Experience of Monitoring Oil T J Hollett & 12 Measurement System Phillips Petroleum Co Norway 150 C J Stevenson Performance 1989 Paper Paper Title Author Details Company Page No Measurement and Allocation 13 Arne S.Nielsen Phillips Petroleum Co Norway 169 for Production Through Ekofisk Auditing the Management of 14 L C Britton BP Petroleum Dev Ltd 185 Measurement NPD ’s View on Cost Effective Fiscal Metering by Means of 15 Steinar Fosse Oljedirektoratet 203 Test Separator and Well Allocation Methods Automatic Transmitte r Rolf Skatvedt & 16 Calibration – Ideas and Practical Norcontrol Training a.s 204 Rune Øverland Implementation Automatic Transmitte r 17 Calibration – Ideas and Practical Bjørn Ullebust Statoil 220 Implementation Quartz Pressure Standards for High-Performance 18 Øivind Godager PTL A/S 233 Measurement and Automation Transmitter Calibration Presentation of the Norwegian 19 Hans-Petter Klemmetsen Norwegian Calibration Service 248 Calibration Service 20 Code of Practice for ISO 5167 Philippe Grenier Gas de France 256 .: A.. FIELD EXPERIENCES WITH ULTRASONIC FLARE GAS METER AT THE STATPIPE GAS TERMINAL, KARST0 AND AT THE GULLFAKS-B PLATFORM IN THE NORTH SEA . .. ,BY SVEIN LOUIS BERSAAS TRANSPORT DIVISION STATOIL A/S KARST0. NORWAY \ 10.10. 1989 \ Why ultrasonic flare gas meter at the statpipe Gas Terminal? Problem: The existing annubar flowmeter with the calculated range of 30.000 - 640.000 Kg/h did not satisfied the necessary range of 200 to 250.000 KG/h as "normal" flaring. Solution. The ultrasonic flare gas meter FGM 100 satisfied the required low and middle range 200 - 250.000 Kg/h The annubar meter will still measure the upper part of the range. The expected low maintenance cost is also an advantage. Fluenta FGM 100 flare gas meter The Fluenta FGM 100flare gas meter measures volume flowrate and mass flowrate in flare pipes he Fluenta FG~l 100 flare gas meter has pulse travelling with the flow. This time Installation Tbeen designed to solve difficult measur- difference is used to find the gas velocity, and Fluenta A/S has transducer-mounting jigs for ing problems in flare gas pipes. with low t~ calculate the volume flow in the flare gas several pipe diameters. Transducer adaptors pressure. J wide range of velocities and large pipe. are welded to the pipe at precise angles tor pipe diameters. The signals are repeated lOa times per second. optimal pulse transmission. The FGM 100 Flare gas meter uses the transit The measurements aft' averaged every two Of time to measure the fl3re gas velocity . Two four seconds, to give a steady meter reading specially designed transducers are mounted and output. non-intrusively in the pipe wall. Each trans- For the system to be able to give readings in ducer transmits and receives ultrasonic pulses. standard cubic meters (Sm'), signals for References and the electronic svstern measures the time temperature and pressure must he given to the The FGM ICC has been developed by the Chr. the pulse needs to travel from one transducer flow computer. These signals combined with Michelsen Institute in Bergen. Norway and to the other. An unique technique is used to information about estimated sound velocitv [he project WJS sponsored bv Mobil a~d recognise the pulses and measure the transit are also used in calculation of the gr:tvity ~f Sratoil. It has been installed on platforms III r time. the gas. the North Sea .IS well 35 on J petrochemical With J gas flow in the pipe. the pulse plant. Extensive testing It the Gullfaks B has travelling Jgainst the flow will need longer FLLJENTA shown ~l much better accuracy than th ) . General Front panel Mains supply: 220 V AC/IIO V AC 50/60 Hz Mounted in 19" rack. with: 16-character alphanumeric LED display and Power SO VA max. 29~key data entrylfunction keyboard. consumption: 2-channel recorder (3-ch. optional). Pipe sizes: 8" dia. min .. 72" dia max. 8-digit electro -mechanical counter. Velocity range: 0.05 - 70 m/s for 72" dia. pipe Display functions: 0.05 - 100 mls for 36" dia, pipe Volume flowrate (5m3fhr) 0.20 - 100 m/s for 8" dla. pipe Total volume (5m3 x resolution) Mass flowrate (kg/hr) Uncertainty 5% of measured value at fully developed Total mass (kg) at 95% con- turbulent flow conditions. Temeprature (Centigrade) fidence level: Pressure (bar) Specific gravity Resolution: Velocity: 0.01 m/s for 36" dla. pipe Velocity (m/s) Repeatability: Better than I% of volume flow (with velocity from 0.3 - 100 m/s). Calibration: 0.3 - 70 mls with fully developed turbulent flow profile. Flow computer Ultrasonic transducers Flow computer and signal processor Operating temperature: -10 - + 75 deg.C mounted in 19" rack with power Pressure: 0.8 bara - 5.0 bara supplies. Weight: Each 9,6 kg excl, valve and socket. Dimensions: Lenght 0.70 m (transducer unit). Input: Veloclty: Signal from transducer Signal transmission via optical fibre cable. via optical fibre cable Electrical safety: Intrinsically safe with Temperature: 4-20mA certified power supply and cable. Pressure: 4- 20mA Safety class: EEx ia IIC T6 Specific gravlty: 4-20mA BASEEFA approval. cert. no. Ex 86B24 1I Ex 872089 Output: Recorder: 0- 10 V DC (4-20mA optional) Ch. I: Volume flowrate low Ch. 2: Volume flowrate high Ch. 3: Volume outputs optional Counter: 24 V DC pulse for electro-mechanical counter. Resolution: SO standard cubic meters for total volume. For further information, please contact: Fluenta A/S. P,O. BOl< 162, Fanaveicn U. ;-.J·5051 Ncsttun, Bergen. ","0,.,'.3\', Tel. ~ ..;- 513 75 10· Tclcial< T .. 7 513 6878 ~~ ~ "T~.~ ~- / -~:- .~~~ ... ~~: -;: .• ~~-.- ~~:'7J~ ~.~,:;.j~.-~.-',~~ ----, ::",":.,' .,~". .... ':f~ ••• "';" " v ; ....: - ~-< SYSTEM CONFIGURATION ULTRASONIC FLARE GAS METER STATPIPE GAS TERMINAL. KARST0 MAIN CONTROL CENTRE ACTUAL VALUE SAFE AREA . - MASS - VOLUME - TEMP PCDA QUANTITY VALUE OS LOKAL CONTROL ROOM ACTUAL VALUES QUANTITY VALUES 3 4-20mA CONTROL FLOW COMPUTER PCOA BUS PANEL FGM - 100 PS SAFE AREA FIBER OPTIC 4-20mA 50 M 15V PWS EX! 36n V T p 0,05 - 125 M/s -5 - 30 Cel s::: ATM 44M > 40xO L 1 HAZARDOUS AREA ~ OFFSHORE CONDITXON Experiences ~rom the installation at the Statpipe Gas Terminal. * The angle of tilt between the transducers are critical. The welding work of then the necessary pipe stubs were therefore performed with highest accuracy. Even when using a welding jig this caused some problems because of the heating up and the following drawing when cooling. * The welding was performed when the plant was shut down and inerted flare system. * The necesarry holes were drilled by using "hot tapping" technics performed by specialists. The special angles gave firstly no specially problems. By using dummy transducers the bore and the angles were tested to be in order. But later the operating showed something else. * Due to the mechanical problems a "spool piece" is recommended. * Because of the high velocities care must be taken regarding the lenght (resonance) of the necessary thermowell. For this purposes a special thermowell was made where the critical point were moved. * The termination of the fiberoptic for signal transmission need accurate work. Care must be taken to the higher minimum bending radius compared to ordinary signal cables. * The insertion of the transducers gave some problems because of the small diameter difference (2 mm) between the transducers and the bore, also that the drill have deviated from the central axis caused by the angle. The whole arrangement included the ball valve were then moved a litle bit to get "correct" position for insertion. * The other components like the flow computer etc. gave no problems including the interface to the PCDA. 1 I ...!...:.!... .eGO .' \ \ i .i\ I .~.~-\._-._-._- ._--._-. __ .---- ----- I \' , \ " j r... J/'s ',.&...... -..{.t tmH. mea-n '~'.::' c .... -;~ ..... i ''y o l 1VI" s.a.l 1111".110""lin" nUl(' M"",(.IP.lU urn l·A .. 'StUll .. ' U.I .!I&.-u.L CURRENT POSITION IDEAL POSITION PROBLEM AREA. ·. Experience from operating at the Statpipe Gas Termina1 * The flare gas meter was partly installed june -88 while an uppgraded version (interface to the PCDA etc.) was installed in january -89. * No systematically test have been performed yet, due to the fact that there was no good comperable references specially in the lower range. For the lower range referance is made to tests at Gullfaks-B plattform. For the upper range (>50.000 Kgjh) test is prepared to an annubar meter where the curve display function in the PCDA will be used for logging (30 days.) * The meter and the measurement is only "tested" by comparing to assumed values.
Details
-
File Typepdf
-
Upload Time-
-
Content LanguagesEnglish
-
Upload UserAnonymous/Not logged-in
-
File Pages266 Page
-
File Size-