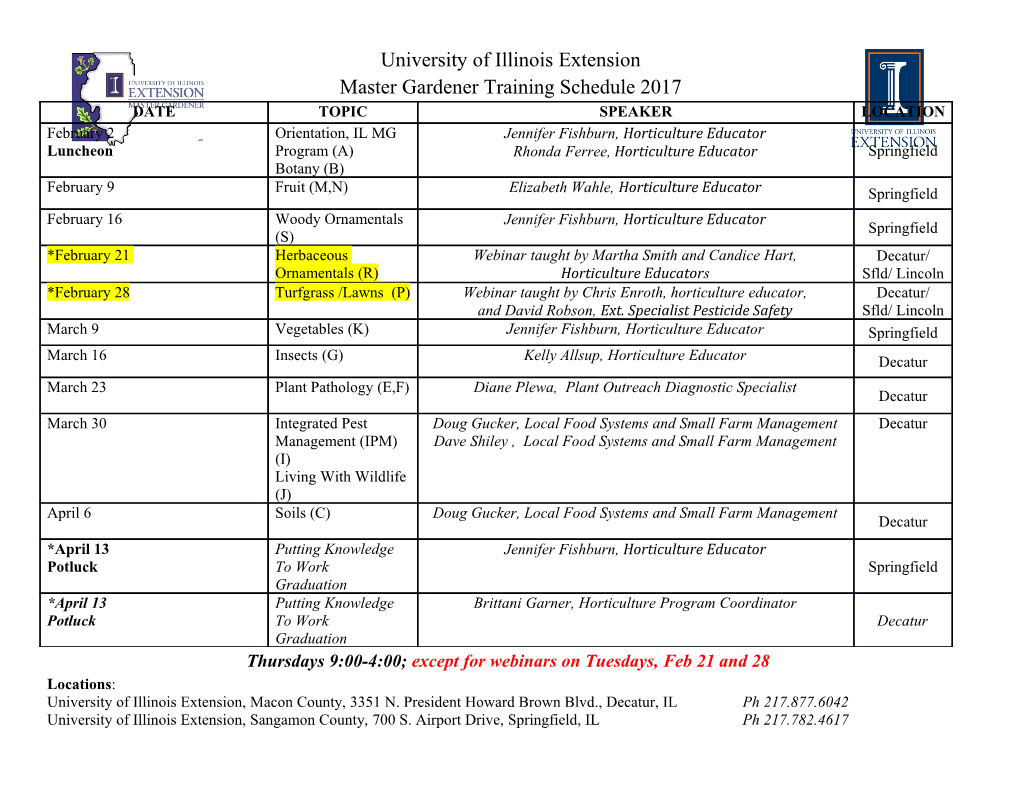
TWENTY FIFTH EUROPEAN ROTORCRAFT FORUM Paper no. C13 ACTIVE SUPPRESSION OF STALL ON HELICOPTER ROTORS BY KHANH NGUYEN ARMY/NASA ROTORCRAFT DIVISION NASA AMES RESEARCH CENTER, MOFFETT FIELD, CA SEPTEMBER 14-16, 1999 ROME ITALY ASSOCIAZIONE INDUSTRIE PER L’AEROSPAZIO, I SYSTEMI E LA DIFESA ASSOCIAZIONE ITALIANA DI AERONAUTICA ED ASTRONAUTICA Active Suppression of Stall on Helicopter Rotors Khanh Nguyen Army/NASA Rotorcraft Division NASA Ames Research Center, Moffett Field, CA to the large angle of attack requirement on the re- Abstract treating side. This paper describes the numerical analysis of Operating in an unsteady environment, the a stall suppression system for helicopter rotors. The blade encounters the most severe type of stall analysis employs a finite element method and in- known as dynamic stall. In forward flight, the blade cludes advanced dynamic stall and vortex wake experiences time-varying dynamic pressure and models. The stall suppression system is based on a angle of attack arising from blade pitch inputs, elas- transfer function matrix approach and uses blade tic responses, and non-uniform rotor inflow. If root actuation to suppress stall directly. The rotor supercritical flow develops under dynamic condi- model used in this investigation is the UH-60A tions, then dynamic stall is initiated by leading edge rotor. At a severe stalled condition, the analysis or shock-induced separation. Even with limited predicts three distinct stall events spreading over the understanding about the development of supercriti- retreating side of the rotor disk. Open loop results cal flow in the rotor environment, flow visualization show that 2P input can reduce stall only moderately, results of oscillating airfoil tests at low Mach num- while the other input harmonics are less effective. ber suggest that supercritical flow is associated with The responses of the stall index, a measure of stall, the bursting of the separation bubble as it encounters to individual input harmonics are highly nonlinear. the large adverse pressure gradient near the blade Such nonlinear stall behavior makes the closed-loop leading edge [1]. Dynamic stall is characterized by controller ineffective in suppressing stall and the the shedding of strong vortices from the leading combined effects of individual harmonics non- edge region. The leading edge vortex produces a additive. Also, stall reduction does not guarantee large pressure wave moving aft on the airfoil upper gains in rotor performance. surface and creating abrupt changes in the flow 1. Introduction field. The pressure wave also contributes to large lift and moment overshoots in excess of static values Active control has the potential to directly and prolongs flow separation, both causing signifi- suppress rotor blade stall and thus can expand the cant nonlinear hysteresis in the airfoil behavior. helicopter flight envelope. Unlike fixed-wing air- craft, stall does not limit the low speed operation of The other type of stall typically observed in helicopters. Stall on rotor blades limits the rotor two-dimensional wind tunnel tests involves trailing structural envelope, in particular, the helicopter edge separation. The phenomenon of trailing edge maximum speed and the rotor loading capabilities. separation is associated with either static or dy- At the stall boundary, the large blade pitching mo- namic conditions. Separation starts from the airfoil ment induced by stall can cause stall flutter and trailing edge, and with increasing angle of attack, excessive loading, leading to fatigue of structural the separation point progresses towards the leading components. In addition, stall increases the rotor edge region. Trailing edge separation contributes shaft torque, causes excessive vibration, and ad- to nonlinear behavior, such as hysteresis, in lift, versely affects the aircraft handling qualities. Suc- drag and pitching moment due to the loss in circu- cessful control of stall can enhance the utility of lation. In contrast to dynamic stall that is charac- rotorcraft. terized by abrupt changes in airfoil behavior, trail- ing edge stall progresses at a moderate rate. Classical treatments of rotor stall indicate that stall typically occurs near the retreating blade tip. In A recent investigation of blade pressure data forward flight, a blade encounters a time-varying from the UH-60A Airloads Program [2] has helped dynamic pressure due to the combined effects of improve understanding about rotor stall behavior. blade rotation and vehicle forward speed. Thus, the Test results reveal that stall is not confined solely to dynamic pressure is greater on the advancing side the retreating side but rather spreads to the first than the retreating side. To balance the roll moment quadrant of the rotor disk. Since stall is strongly on the rotor, the basic trim control provides low coupled with the blade dynamics, especially the angle of attack on the advancing side and high angle torsion mode, this coupling manifests in a stall cycle of attack on the retreating side. As the rotor loading that begins in the fourth quadrant of the rotor disk or the forward speed increases, stall is initiated due and continues up to the first quadrant in two cycles (three stall peaks). The stall cycle has a frequency C13-1 closely matched with the blade torsion frequency. tential of 2P blade pitch to improve rotor perform- Flight test data also indicate that rotor stall exhibits ance and cabin vibration. Test results showed no behavior similar to that observed in airfoil oscillat- reduction in the rotor shaft torque with any combi- ing tests where the shedding of the strong leading nations of amplitude and phase of the 2P input. A edge vortex dominates the flow pattern. post-test analysis revealed that the drag reduction on the retreating side due to 2P control was offset by an Passive control of blade stall typically employs increase in profile drag in the fore and aft portions the tailoring of blade twist and planform for effi- of the rotor disk. Even though stall alleviation was cient blade load distribution. Modern rotors often not attempted in the test program, such conclusions employ blade construction with multi-airfoil sec- confirmed the previous analytical predictions that tions -- thick, high-lift sections inboard and thin, 2P control could be used to redistribute the rotor transonic sections for the tip region. These designs loading. aim to provide efficient rotor disk loading and low drag and thus, are employed primarily for perform- In the early eighties, Kretz [10] wind tunnel ance benefits; however, they also provide stall alle- tested a "stall barrier feedback" system on a six-foot viation. The design of the BERP rotor [3] is one diameter two-bladed rotor for stall suppression. The notable example of passive methods. The BERP system relied on three pressure sensors mounted at blade has multiple airfoil sections and a prominent 85 percent blade radial station to monitor stall. The tip shape designed to operate efficiently in the tran- pressure sensors provided feedback signals that sonic regime (low angle of attack advancing blade activated the high frequency actuators to avoid stall. tip) and to generate high lift in subsonic flow condi- The feedback pressure signals were based on the tion (retreating blade tip). threshold values adapted from airfoil test data. Test results yielded no concrete conclusions to substanti- In an effort to expand the helicopter flight en- ate the benefits of this stall suppression system. velope, this analytical study explores the use of high frequency blade pitch actuation to alleviate blade 3. Scope of Current Investigation stall. The availability of high-frequency blade- The objective of the current study is to analyti- mounted actuators has made active stall suppression cally evaluate the effectiveness of an automatic stall realizable. Earlier investigations of active rotor suppression system for helicopters using higher control have focussed on swashplate actuation [4]. harmonic blade root input. The effects of stall sup- This scheme places a limit on the number of har- pression on rotor performance are also investigated. monics available for excitation at N-1, N, and N+1 Stall suppression is formulated as an optimization per rev, where N is the number of blades per rotor. problem in which the stall behavior of a rotor is With the blade-mounted actuators, the excitation quantified and subsequently minimized using higher frequency is not limited by the swashplate constraint harmonic control (HHC). Thus, the system sup- but by the bandwidth of the actuators. ZF Luft- presses stall directly. fahrttechnik GmbH of Germany built and flight- tested an individual-blade-control type actuator with In this paper, the term higher harmonic control excitation frequencies varying from two to twelve refers to blade pitch input with harmonic content per rev on an MBB BO-105 helicopter [5]. More greater than one per-rev. Since the focus of the recently, the same company is building larger ac- paper is on the aerodynamic performance aspects of tuators to be retrofitted into a full-scale UH-60A stall suppression, the effects of HHC on blade loads, rotor for wind tunnel testing at NASA Ames. control system loads, and vibratory hub loads, which can be significant, are not discussed. 2. Previous Stall Suppression Works The analysis used in this study will be de- In the fifties and early sixties, Stewart [6], scribed, followed by a description of the HHC sys- Payne [7], and Arcidiacono [8], conducted separate tem for stall suppression. The analysis is then used analyses to investigate the potential of using higher to model a stalled condition for the UH-60A rotor. harmonic control to delay the onset of retreating An evaluation of the open and closed-loop stall blade stall. These investigators discovered that suppression system is provided. Finally, specific higher harmonic control could be used in combina- findings from this study are presented. tion with the basic trim control to redistribute lift on the rotor.
Details
-
File Typepdf
-
Upload Time-
-
Content LanguagesEnglish
-
Upload UserAnonymous/Not logged-in
-
File Pages9 Page
-
File Size-