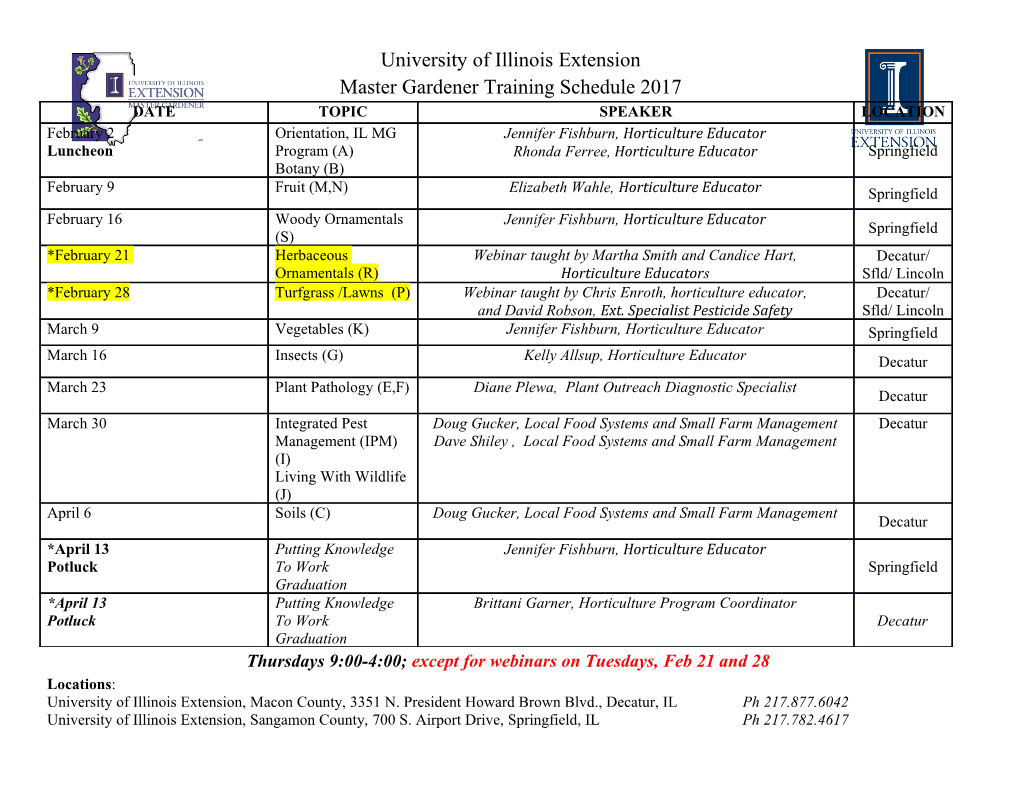
High Temperature Materials and Processes, Vol. 8, No. 1, 1988, 39-46 Ultra Fine Powder from Alloy Resources via Alkoxide. (Resources Chain and Primary Innovation) by Nobuaki Sato and Michio Nanjo Research Institute of Mineral Dressing and Metallurgy, (SENKEN) Tohoku University, Sendai 980, Japan CONTENTS Page ABSTRACT 40 1. INTRODUCTION 40 2. FERRONIOBIUM PRODUCTION 40 3. CHLORINATION OF FERRONIOBIUM AND CHLORIDE SEPARATION 41 4. Nb-Ti SUPERCONDUCTOR SCRAP AS Nb SECONDARY RESOURCES 42 5. SYNTHESIS AND SEPARATION OF ALKOXIDES 43 6. PRODUCTION OF ULTRA-FINE POWDER VIA ALKOXIDE 45 7. PROPERTIES OF UFP Nb205 45 8. CONCLUDING REMARKS 46 ISSN 0334-1704 ©1988 by Freund Publishing House Ltd. 39 Vol. 8, No. 1, 1988 Ultra Fine Powder from Alloy Resources via Alkoxide ABSTRACT The urgent problem is to develop ore processing (first grade purification) to a high level (composition An attempt has been made to combine resource control, super purification) by developing super-refin- chains and primary innovation in high technology ing processes which facilitate process expansion, from fields. Alloy materials from urban mines are discussed alloys to new material applications in high-tech fields. as a new type of rare metal resource. Recovering nio- In this paper, we try to develop a new material, i.e. bium from ferroniobium and Nb-Ti superconducting ultrafine oxide powder (function development) from alloy via chloride methods has been studied. The ferroniobium or Nb-Ti scrap via chlorine metallurgy, production process of alkoxides from alloy resources alkoxide synthesis and purification (organic), and dis- has been investigated. Ultra fine NbiOs powder was cuss the resources and metallurgy for future research. produced by hydrolysis of alkoxides and some proper- ties of the powder are evaluated. 2. FERRONIOBIUM PRODUCTION 1. INTRODUCTION In pyrometallurgy of ores, impurities are usually As rare metals such as Nb, Ta, Zr support the separated between the slag and metal phases. In iron advanced progress of high technology industries, their making, AI2O3, S1O2, MgO are present in slagoff and development for both resource and application has Cr, Co, Cu, Ni, Nb are concentrated in the metal phase become strategic in recent years /1-4/. It is now well /6/. This process corresponds exactly to solvent known that the recent trend of ore-producing coun- extraction from the iron melt to extract valuable tries such as Brazil is to export primary products metals. When applying high temperature solvent instead of raw materials /5/. For example, in Brazil, extraction to rare metal ore processing, i.e. mixing with the biggest niobium resources in the world, concentrate and Al powder, separation of metals they are exporting ferroniobium instead of pyrochlore between slag and melt iron by thermic reduction, this because of the uranium and thorium deposits con- ferroalloy shows a relatively low melting temperature tained in pyrochlore. In the chromium industry, a compared with high temperature refractory metals. similar trend is observed, i.e. ferrochromium exports Ferroniobium is produced from pyrochlore by instead of chromite. In Japan, very new types of high alumino-thermic reduction as shown in Fig. 1. This grade raw material such as ferroalloy can be stocked, ferroniobium contains 60% Nb, 40%Fe, 3% Al and a thus decreasing the need for finance and metallurgy. very small amount of impurities such as Ta, Mn, Ti, Si, Furthermore, secondary resources from production Sn. and waste are also important, and recycling of these resources is imperative. On the other hand, as compared with the supporting Igniter role in the traditional steel-making; industry, develop- ment of new materials such as the Nb-Ti superconduc- tors, Josephson elements, ceramic catalysts, in which niobium predominates, is now in fashion. In the field Al powder of new material synthesis, ultra-fine oxide powder is Fe?Oi obtained by hydrolysis of chlorides and oxidation in + Thermit Ti.Zr.U.Th^.l Slag phase reduction the vapor phase, but now the "alkoxide process" has Pyrochlore Ferroniobium Metal phase the advantages of homogeneous mixing, monodisper- concentrate (~60%Nb) sion, ultra-fine powder production, easy handling, etc. Also, raw materials for advanced ceramics production Before reaction After reaction are reverting to alkoxides, so that alkoxides have become the "key material" for ceramic production. As Japan has poor resource deposits, we have to develop Fig. 1: Production of ferroniobium from pyrochlore concentrate. higher level technology, with continuous primary innovations assisting rapid progress in underdeve- loped countries, and a new resource strategy aiming for additional values. 40 Ν. Sato and Μ. Nanjo High Temperature Materials and Processes 3. CHLORINATION OF FERRONIOBIUM AND CHLORIDE Ar gas over FNb powder, dry CI2 gas flowed at a rate SEPARATION of 500 ml/ min. When the pale yellow CI2 gas attacks the ferroniobium powder, a reaction takes place 3.1. Chlorination offerroniobium j7j rapidly as in eq. (1) and the temperature spikes due to exothermic reaction. Stability diagrams for the Fe-Ch and Nb-Ch sys- tems obtained from thermodynamical calculations are Fe-Nb(s) + 4Cl2(g) - FeCl3(g) + NbCls(g) (1) shown in Fig. 2 /8/. By controlling the partial pressure of chlorine gas, selective chlorination producing fer- The dark brown mixture of NbCls-FeCh was vapo- rous chloride and niobium pentachloride is possible. rized and condensed in the traps after producing lower chlorides. When condensing, NbCl5 tends to deposit at Temperature (°C) lower temperatures, and rough separation obtaining 80 mole % NbCls of mixed chlorides by temperature 600 300200 100 gradient is possible. dimeaimer iFeCiJ 10 3.2. Separation of NbCh-FeCl-s mixed chlorides (s) Cfl 0 ®NbCI5 rn The different methods used for mutual separation of Q. NbCI, (g) Μ NbCls-FeCh are given below. -10 ο a) Simple distillation: CL -20 The vapor-liquid equilibrium for NbCls-FeCls is shown D) in Fig. 4. Mole fraction of NbCI, in vapor phase is Ο -30 always bigger than that of liquid phase. As the mole fraction ratio between both phases becomes close to -40 unity, separation by simple distillation becomes more difficult. Pure NbCl5 of 99.9 mole % is obtained from 987 6 5 4 3 ferroniobium chlorides (63 mole % NbCls) by 15 theo- Temperature (x100K) retical plate. Fig. 2: Chemical potential diagram of Nb-Ch and Fe-Ch systems. But low pressure chlorination is not practical from the aspect of productivity. Here, separation of NbCls from FeCh was tried after the ferroniobium chlorina- tion under Pci2 = 1 atm at 300° C. Fig. 3 shows chlori- nation apparatus made of pyrex glass. After flushing Pyrex glass tube(25mm») oft gat ci. Ζ Fe-Nb alloy Condensate _ ^^ 7 II! ^ u Γ ι Ii ι 0 0.2 0.4 0.6 0.8 1.0 Mole fraction of NbCI5 in liquid,χ T.C. ΤΧ. T.C. T.C. T.C. \f7~m Trap Κ Χ— A Fig. 4: Equilibrium compositions for NbClj-FeClj system. 30 CM IOCM Reaction part Condensation part b) Selective reduction by Iron powder: Fig. 3: Chlorination apparatus. It is better for separation to reduce FeCb to non- 41 Vol. 8, No. 1,1988 Ultra Fine Powder from Alloy Resources via Alkoxide volatile FeCh by selective reduction, as shown in eq. NbCls is transferred to the "NaCl at 250° C by the (2). following reaction: 2FeCl3(g) + Fe(s) - 3FeCl2(s) (2) NbCl5-FeCl3(g) + NaCl(s) - NaNbCl6(s) + FeCl3(s) (4) When the NbCls-FeCU mixture reacts with iron powder, only FeCl3 reduces to FeCl2, producing a Separation by direct chlorination of ferroniobium in a NbCl5-FeCl2 binary system. From distillation after NaFeCU salt bath is also reported (eq. (5), (6)) /9/. selective reduction, the iron content was reduced to 0.07%. Fe-Nb(s) + NaCl(s) +7NaFeCl4(l) -NbCls(g) + c) Organic solvent method: 8NaFeCl3(l) (5) The separation methods using organic solvent are very interesting, having the advantages of low temperature, 2NaFeCl3(l) + Cl2(g) -2NaFeCl4(I) (6) homogeneity, easy handling, avoiding hydrolysis, etc. Using chlorobenzene, selective reduction of FeCl3 is The chlorination of ferroalloys is very easy and possible. The flow sheet for the organic reduction many chloride separation methods have been deve- process is shown in Fig. 5. The reaction of equation (3) loped. Impurities such as Al, Ta, Si, Ti must be inves- proceeds quantitatively at 130°C and the valuable tigated for ultra-high purities since these impurities byproduct of p-dichlorobenzene for insecticides is influence separation. obtained. 4. Nb-Ti SUPERCONDUCTING ALLOYS AS Nb SECONDARY RESOURCES ( Fe-Nb alloy) Recycle ->( HCl ) Γ Recovery of rare metals from Nb-Ti superconduc- Γ<§>— ( C.H.CI ) tor alloys as a secondary resource, and which could be -Κ C.II.CI, ) ( FeCl,-NbCI, ) an important Nb alloy, has been attempted. C404IO (447ΙΟ Solution Selective 1 st step 2nd step a) Characterization of Nb-Ti Alloy Scrap: Reduction Distillation >( NUCI, ) C403K3 ^Precipitate Nb-Ti superconductor is produced by 1) Assem- Fe,0, ) bling OFC pipe and Nb-Ti rod into a single core wire, 2) Wire drawing, 3) Assembling billet for multi-core Fig. 5: Flowsheet for recovery of NbCI5 by chlorobenzene. wire, 4) Wire drawing, 5) Heat treatment, 6) Enamel insulation, 7) Inspection and testing /10/. But almost 90% of Nb-Ti scrap becomes multi-filament wire for testing. Fig. 6 shows the cross-section of multi- 2FeCl3 + C6H5C1 - 2FeCl2 + C6H4C12 + HCl (3) filament wire of 2.6mm diameter. Ultrafine wire of Nb-Ti alloy is· observed between the internal and Another NbCls does not react with chlorobenzene. external Cu. Stripping of Cu by anodic oxidation was Furthermore, large differences of chloride solubility in first tried as for electro-refining of Cu, after which chlorobenzene enable better separation (NbCls:460, separation of Nb and Ti using chloride was attempted.
Details
-
File Typepdf
-
Upload Time-
-
Content LanguagesEnglish
-
Upload UserAnonymous/Not logged-in
-
File Pages8 Page
-
File Size-