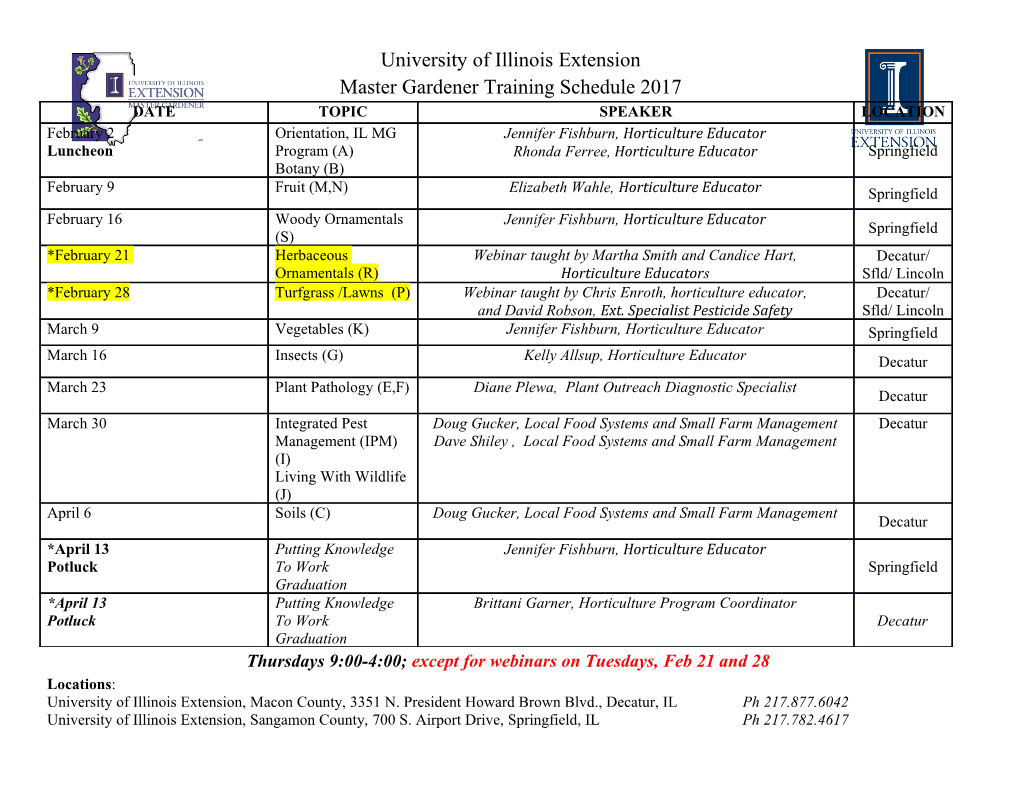
Topics in Catalysis https://doi.org/10.1007/s11244-018-1052-9 ORIGINAL PAPER Novel Catalytic Reactive Distillation Processes for a Sustainable Chemical Industry Anton A. Kiss1,2 © The Author(s) 2018 Abstract Reactive distillation (RD) is a great process intensification concept taking advantage of the synergy created when combin- ing (catalyzed) reaction and separation into a single unit, which allows the concurrent production and removal of products. This feat improves the productivity and selectivity, reduces the energy usage, eliminates the need for solvents, and leads to highly-efficient systems with improved sustainability metrics (e.g. less waste and emissions). This paper provides an over- view of the key features of RD processes, with emphasis on novel catalytic/reactive distillation processes that can make a difference at large scale and pave the way for a more sustainable chemical process industry that is more profitable, safer and less polluting. These examples include the production of: acrylic and methacrylic monomers, unsaturated polyesters resins, di-alkyl ethers, fatty esters, as well as other short alkyl esters (e.g. by enzymatic reactive distillation). The main drivers for such new RD applications are: economical (large reduction of costs and energy use), environmental (lower CO 2 emissions, no or reduced waste) and social (improved safety and health due to lower reactive content, reduced footprint and run away sensitivity). Hence RD technology strongly contributes to all three pillars of sustainability in the chemical process industry. Nonetheless, the potential of RD technology has not been fully tapped yet, and there is still undergoing research to improve it further by various means: e.g. ultrasound or microwave assisted RD, use of high-gravity fields (HiGee), internally heat integration, cyclic operation, or coupling RD with other operations such as membrane separations. Keywords Catalytic distillation · Reactive distillation · Process design · Eco-efficiency · Sustainability 1 Introduction to eco-efficient sustainable production systems. When solid catalysts are used, RD is also referred to as catalytic distil- Although distillation is the oldest and most commonly used lation. RD is considered nowadays an established industrial separation technique at industrial scale, there are still major unit operation, being the front-runner in the PI field [3, 4]. developments to improve it further [1, 2]. Among them, In general, RD is applicable to equilibrium limited reaction reactive distillation (RD) is one of the greatest process inten- systems. While the catalyst helps increasing the reaction rate sification (PI) technique profiting from the synergy gener- and shortening the time to reach the chemical equilibrium, ated when combining catalyzed reactions and separation into it does not actually change the attainable equilibrium con- a single unit. RD (also known as distillation with reaction) version. In RD, the equilibrium is shifted to full conver- greatly improves the conversion and selectivity, reduces the sion by the continuous removal of products. Thus RD can energy usage, eliminates the need for solvents, and leads use just the stoichiometric reactants ratio (neat operation) to pull the equilibrium to high conversions, in contrast to the usual practice of using an excess of reactant to push the * Anton A. Kiss equilibrium toward the desired products, with the extra cost [email protected]; [email protected] of recovery and recycle of unreacted raw materials [2]. 1 School of Chemical Engineering and Analytical Figure 1 illustrates the dependence of the equilibrium Science, The University of Manchester, Sackville Street, conversion on the equilibrium constant (Keq) and the dra- Manchester M13 9PL, UK matic positive effect of increasing the reactants ratio in case 2 Sustainable Process Technology Group, Faculty of Science of a quaternary system in which two reactants are converted and Technology, University of Twente, PO Box 217, to two products. Notably, in case of RD a similar effect 7500 AE Enschede, The Netherlands Vol.:(0123456789)1 3 Topics in Catalysis 1 is obtained by removing the products instead of using an 0.9 excess of one of the reactants. 0.8 The literature covers very well various topics related to 0.7 RD, such as: thermodynamics [5], feasibility and applica- on 0.6 bility [6, 7], conceptual design [8, 9], modeling and process si 0.5 simulations [10, 11], optimal design [12], design and con- onver 0.4 trol [13], process configurations [14], process scale-up [15], C 0.3 Reactants ratio green engineering aspects [16], industrial perspectives and 0.2 1 1.2 1.5 applications [17–19], applications in biorefineries [20], and 2 4 8 the status and future directions of RD technology [21]. RD 0.1 12 16 20 technology has been applied industrially in many processes 0 012345with production capacities of 100–3000 ktpy, e.g. produc- Keq tion of methyl acetate as well as fuel additives or oxygenates (MTBE, ETBE, TAME) [3]. However, further applications 1 remained somewhat limited. A + B ч C + D 0.9 This paper aims to provide some insights into the key 0.8 features of RD processes, along with a focused presentation 0.7 of novel catalytic/reactive distillation (industrial) processes on 0.6 reported in the past decade, such as the production of acrylic si 0.5 and methacrylic monomers, polyesters, alkyl ethers (dime- Reactants ratio onver 0.4 thyl ether, di-n-pentyl ether), fatty esters, and other short C 1 1.2 chain alkyl esters. 0.3 1.5 2 0.2 4 8 12 16 0.1 20 2 Reactive Distillation Technology 0 -8 -6 -4 -2 02468 ln Keq Along the way from taking any brilliant idea into practi- cal process implementation, there are several essential R&D steps that combine computation and process simula- Fig. 1 Equilibrium conversion vs equilibrium constant, at various reactants ratio tions with lab- and pilot-scale experimental work—as con- veniently illustrated in Fig. 2. These steps have the role to Knowledge & certainty Implementation Process comparison (economic evaluation) Process simulation (plant design, scale-up) Pilot plant validation (plant design, validate exp.) Properties (VLLE measurements, estimations) Experiments (chemistry, catalysts, kinetics, equilibrium) Conceptual design Time Idea (literature data, estimations) Fig. 2 Main research and development steps to go from an idea to process implementation 1 3 Topics in Catalysis provide (preferably in the shortest time) valuable insights equipment design. This leads usually to a very restricted area that increase the knowledge about the process and reduce in which reactive separation is feasible [4]. The combination the uncertainty to low levels that allow a confident design of R&D is not possible if there is no major overlapping of and construction of the plant. This is also the case for reac- the operating conditions of reaction and separation (e.g. a tive distillation processes, where the simulations are used to high pressure reaction can not be combined with a vacuum guide the conceptual process design and the experimental distillation). work, while the experiments decide upon the validity of the Figure 3 shows the most common RD configuration simulated model. The validated model can be used then for alternatives: conventional RD column, heterogeneous process scale-up, sensitivity analysis studies, process control azeotropic RD column, and RD column combined with and optimization. pre-reactor and/or side reactors [1]. Note that distilla- When deciding whether RD is the right choice or not, tion columns are a suitable solution only for reactions one must keep in mind both the benefits and limitations of that are sufficiently fast in order to reach high conversions reactive distillation—as summarized in Table 1 [4]. Since within the residence time range of such columns. Previous both operations take place simultaneously in the same unit, research [22] distinguished two main operating conditions: there must be a good match between the temperatures and (1) distillation controlled range (conversion is influenced pressures required for reaction and separation. The operating by the concentration of the components to be separated), window is typically limited by the thermodynamic proper- and (2) kinetics controlled range (conversion is influenced ties (e.g. boiling points) of the components involved. But mainly by the residence time and the reaction constant). also the windows in which the (catalytic) reaction deliv- The industrial design of RD should aim at operating condi- ers acceptable yields and selectivity has usually a limited tions within these two ranges, just the sufficient residence overlap with the separation window. This overlap may be time and only the necessary expenditure for the distillation. reduced further by the feasibility window concerning the Figure 4 presents the resulting principles for the choice Table 1 Advantages and drawbacks of reactive distillation technology RD advantages Process simplification: complex conventional processes can be reduced to a RD column which is typically much easier and cheaper to operate and maintain Capital savings: reducing the equipment units used leads to a considerable reduction of CapEx Increased conversion: the removal of products from the reactive liquid phase causes chemical equilibrium to be re-established at a higher conver- sion rate, and full conversion is attainable Increased selectivity: undesired side reactions can be suppressed by removing the target product from the reactive section
Details
-
File Typepdf
-
Upload Time-
-
Content LanguagesEnglish
-
Upload UserAnonymous/Not logged-in
-
File Pages17 Page
-
File Size-