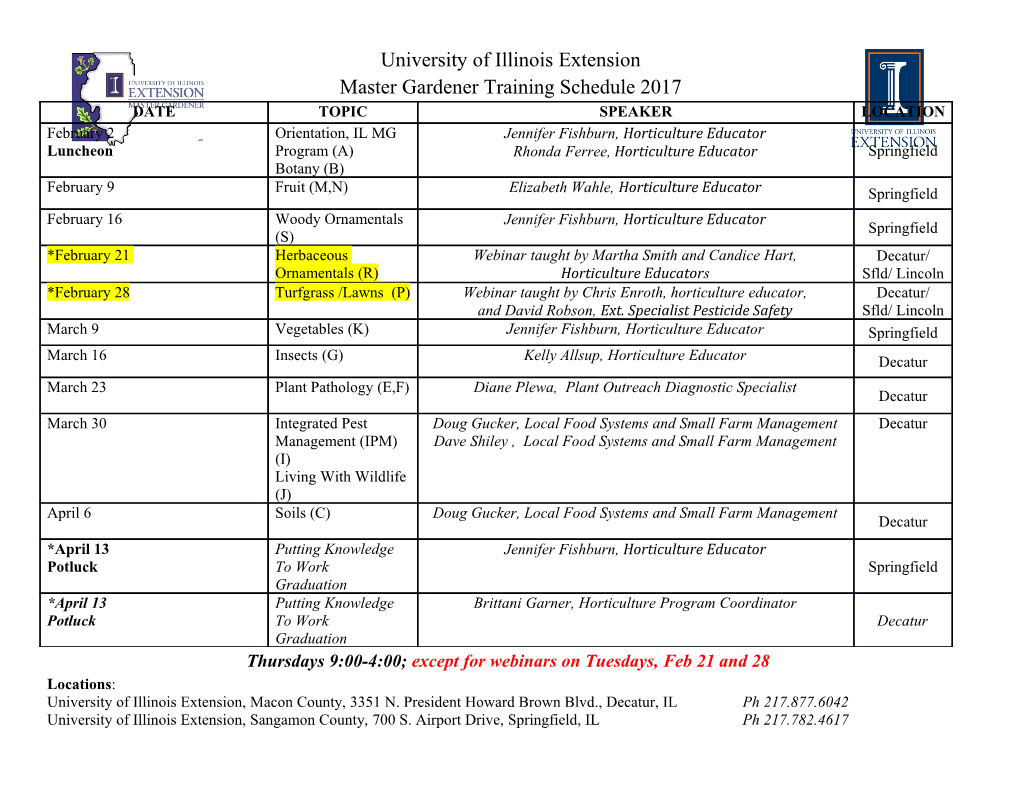
Biomed Tech 2014; 59 (s1) © 2014 by Walter de Gruyter • Berlin • Boston. DOI 10.1515/bmt-2014-4445 S1024 Development of an implantable integrated MEMS pressure sensor us- ing polyimide epoxy composite and Atomic Layer Deposition for en- capsulation P. Gembaczka1, M. Görtz1 and M. Kraft1, 1Fraunhofer Institute for Microelectronic Circuits and Systems, Duisburg, Germany, [email protected] Introduction The futher miniaturization of MEMS sensors (micro-electro-mechanical system) opens up a wide range of medical im- plants applications. Typical medically approved encapsulation materials are titanium or ceramic, which have thick layer (~100µm) and hence are relatively large. For MEMS pressure sensors the membranes must be free to move and in con- tact with tissues or body fluids. A thin and hermetically sealing encapsulation adapting to the shape of the MEMS sen- sor is needed. Flexible encapsulation based on silicone is no hermetic sealing. Here, a novel encapsulation method is demonstrated for a capacitive MEMS pressure sensor system. A high temperature resistant polyimide-epoxy composite was used as die attach material and as sealing compound for bond wires and parts of the chip surface (figure 1). This was followed by an atomic-layer-deposition (ALD) of aluminium oxide (Al2O3) and tantalum pentoxide (Ta2O5) (figure 2) providing a hermetically sealed encapsulation. The polyimide-epoxy is compatible with the ALD deposition tempera- ture of 275°C for several hours. Methods To locate even the smallest defects in the passivation a destructive amperometric measurement method in phosphate buffered saline (PBS) was chosen. To test the performance and repeatability, the pressure measurement system was op- erated and calibrated in a 0.9% saline solution (figure 3). Accelerated life testing at 60°C and 120°C in saline solution was also carried out. Results The maximal calibration error of the MEMS pressure sensor was below 2hPa in 0.9% saline solution. During continu- ous operation the sensor module survived an accelerated life testing at 60°C in saline solution for 1500 hours. During an offline accelerated life testing in saline solution at 120°C the sensor module survived for 116 hours. Conclusion With an polyimide-epoxy composite as sealing and a final ALD deposition a new encapsulation techncology for im- plantable MEMS pressure sensors was developed. Biomed Tech 2014; 59 (s1) © 2014 by Walter de Gruyter • Berlin • Boston. DOI 10.1515/bmt-2014-4445 S1025 pressure chip With sensor membranes polyimide epoxy composite wire bonds (beloW the polyimide) signal-post-processor ASIC (beloW the polyimide) silicon chip-carrier With conductor tracks 9mm Figure1. Encapsulation of the entire sensor module before the ALD passivation ALD passivation on top of the complete sur- face (50 nm Al2O3 and 50 nm Ta2O5) 750 nm silicon oxide and 500 nm silicon nitri- de passivation layer polysilicon membrane Figure 2. SEM image of the fracture edge of a pressure membrane with ALD passivation Figure 3. Pressure value of a passivated sensor module at various temperatures in saline solution [1] Betz, W.: „Flexible mikroelektromechanische Implantate für den chronischen Einsatz: Verkapselungskonzepte und Testverfahren für die Materialcharakterisierung“, Dissertation, 2011 [2] Görtz, M., Betz, W., Vogt, H., Kraft, M.: „Verkapselungstechniken für implantierbare integrierte MEMS- Drucksensoren”, MikroSystemTechnik Kongress, Aachen, 2013 Biomed Tech 2014; 59 (s1) © 2014 by Walter de Gruyter • Berlin • Boston. DOI 10.1515/bmt-2014-4446 S1026 Implantable MEMS sensors and medical MEMS packaging issues for future implants Baum, M.1; Haubold, M.1; Wiemer, M.1; Gessner, T.1,2 1Fraunhofer ENAS, Germany 2Chemnitz University of TechnoloGy [email protected] Abstract: The paper shows the potential of micro machined UsinG a special hiGh aspect ratio (HAR) Si patterninG sensors for implantation and monitoring of patients. Next to technoloGy it is possible to increase the siGnal of the sen- well known sensors it is focused on inertial sensors and a sor [3]. This could be used for a decrease of the sensor way for further miniaturization keeping the performance and size. In our case it is a capacity chanGe in relation to a accuracy of the sensor. Furthermore the ongoing investiga- base capacity that could be converted into a voltage by an tion of materials used for MEMS packaging and MEMS ASIC for example. fabrication will be described. Here, special encapsulation techniques should show a miniaturization potential realized by the substitution of thick medical packages like Titanium housings. (1) Keywords: micro sensors, MEMS, biocompatibility, As we can see in equation 1 the capacity depends on the MEMS packaginG, hermeticity, chip size packaGe CSP, area A. With hiGh aspect ratio patterninG we increase the implant depth of the sensor and herewith the area too. One could also see that the distance plays an important role. In case of decrease the distance of the electrodes the capacity would be increased. This means, the etchinG must be Motivation realized as deep and as narrow as possible. Usually the depth of functional patterninG in industry is around The need for further miniaturization especially in medical 25 µm. The HAR technique enables up to 100 µm in applications is onGoinG and micro and nano system tech- depth with an electrode distance of 3 µm to 5 µm (fiG. 1). noloGies will open new ways for product development This means factor 4 and shows the remaininG potential for and medical proGress [1]. Micro sensors based on Silicon miniaturization. (MEMS) enable the miniaturized integration of mechani- cal, electrical, optical, and other measurement principles into very small systems. For implantable devices it is necessary to ensure the compatibility of the technical system with the bioloGical host [2]. Next to that aspect it is also important to realize a communication from outside the body to the implant usinG wireless technoloGies and a power management for active implants. MEMS sensors Micro technoloGies usinG Silicon as functional material have certain advantages like lonG-time reliability and hiGh precision fabrication of micron ranGe patterns. It is known that MEMS technoloGies show hiGh correlation to medi- cal needs especially regardinG to implantable devices. FiGure 1: SEM imaGe showinG hiGh aspect ratio electrode Meanwhile some implantable devices are workinG and are structures realized by deep reactive ion etchinG of Silicon certified by authorized institutions (e.G. FDA). Examples are pressure sensors for measurinG inside bladder, cra- nium or blood vessels. Very intensive work was done Next to deep reactive ion etchinG further technoloGies for with optical sensors inside the eyes (retina implants) and high precision sensors could be applied like BDRIE electrode based implants for death people (cochlear im- (bondinG and deep reactive ion etchinG), AIM (airGap plants) [1]. But also inertial sensors are in discussion e.G. insulated microstructures, and SOI (Silicon on Insulator) for heart beat measurements and patients position. technoloGies. Biomed Tech 2014; 59 (s1) © 2014 by Walter de Gruyter • Berlin • Boston. DOI 10.1515/bmt-2014-4446 S1027 MEMS packaging for medical devices aspect ratio techniques whether the performance of the sensor could be increased or the system dimensions sig- In case of special monitoring devices for in-vivo patient nificantly decreased. In consideration of new thin film monitoring the biocompatibility of these sensor systems based encapsulation technologies the substitution of usual plays a significant role [4]. Only with strong orientation Ti housing seems to be possible and enable the further regarding to the minimum dimensions certain applications miniaturization of the implants. Further work should be were feasible. Next to the functional components of such done for defining the status of long term biocompatibility a system also packaging materials and housings were and for reliable testing concerning the single process recognized for further optimization. Actual developments steps. At least the integration of communication compo- include the use of thin film layers or multiple thin film nents and wireless strategies as well as energy or power stacks for hermetic and biocompatible sealing of medical aspects for system integration should be covered. MEMS [5]. Although first barrier properties of thin film encapsulations are presented by [6] it will be a challeng- ing topic for future packaging and encapsulation tech- nologies. With regard to standardized test procedures it is Acknowledgement focused to use biocompatible materials for the sensor This work was realized in cooperation between Fraun- system preferred. Hereunder Silicon with its native oxide hofer ENAS and Technische Universität Chemnitz, Cen- and wafer bonding materials like Gold as intermediate ter for Microtechnologies. Parts of that work were carried layer will be investigated for hermetic packaging of the out under a research project CoolPoD, supported by the sensor and the integrated electronics too. It is seen to be center of excellence Cool Silicon in Saxony, funded by distinguished between an inner level of packaging the the European Union (EFRE) and by the Free state of sensor and the electronics using joining techniques and an Saxony, Germany with its SAB - Foerderbank. outer level of encapsulation for hermetic sealing and biocompatible housing of the implant. One possible mate- rial for outside housing is Parylene, deposited
Details
-
File Typepdf
-
Upload Time-
-
Content LanguagesEnglish
-
Upload UserAnonymous/Not logged-in
-
File Pages168 Page
-
File Size-