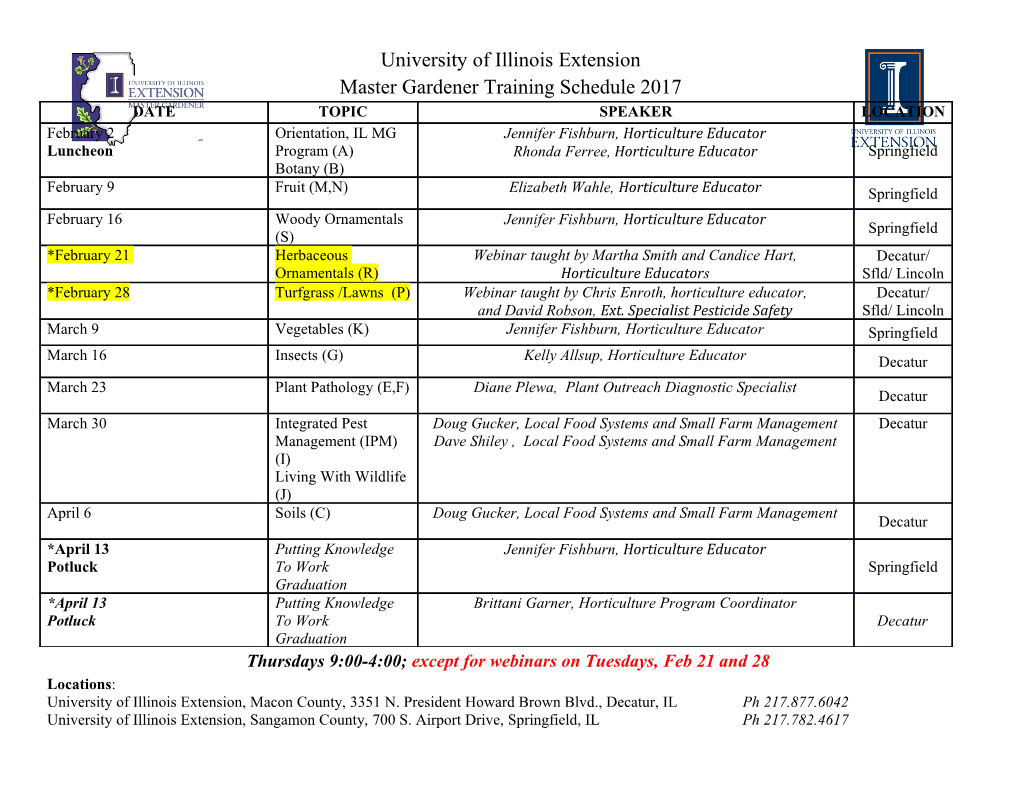
Paper Number 07ICES-295 Development of a Test Facility for Air Revitalization Technology Evaluation Sao-Dung Lu MEI Technologies, Inc. / ESCG Amy Lin Jacobs Sverdrup / ESCG Melissa Campbell Hamilton Sundstrand / ESCG Frederick Smith, Su Curley NASA Johnson Space Center Copyright © 2007 SAE International ABSTRACT surface habitat cabin. This includes the capability to remove contaminants and condition cabin atmosphere, Development of new air revitalization system (ARS) supply and store atmospheric gases, and closed loop technology can initially be performed in a subscale processes which recycle resources. Processes include laboratory environment, but in order to advance the separation by physical adsorption, absorption, and maturity level, the technology must be tested in an end- mechanical filtration. Other processes may include to-end integrated environment. The Air Revitalization chemical adsorption, reduction, and oxidation. Technology Evaluation Facility (ARTEF) at the NASA Johnson Space Center serves as a ground test bed for Lithium hydroxide and charcoal have been the dominant evaluating emerging ARS technologies in an technology used to scrub the cabin atmosphere for environment representative of spacecraft atmospheres. decades. This open loop technology is so simple and At the center of the ARTEF is a hypobaric chamber reliable that no significant changes have been which serves as a sealed atmospheric chamber for necessary. Until the International Space Station (ISS), closed loop testing. A Human Metabolic Simulator the mission durations have been short. In order to (HMS) was custom-built to simulate the consumption of develop new regenerative technology, a test facility must oxygen, and production of carbon dioxide, moisture and be able to sufficiently simulate a spacecraft atmosphere heat of up to eight persons. A multitude of gas in order to aid in the development of the technology. analyzers and dew point sensors are used to monitor the chamber atmosphere upstream and downstream of a A survey was taken of existing facilities to evaluate their test article. A robust vacuum system is needed to capabilities, strengths and weaknesses. Desired simulate the vacuum of space. A reliable data capabilities and design goals were established for an in- acquisition and control system is required to connect all house facility. This paper presents some of the issues the subsystems together. This paper presents the and lessons learned in the process. capabilities of the integrated test facility and some of the issues encountered during the integration. FACILITIES SURVEY INTRODUCTION The Johnson Space Center contains numerous environmental chambers of all sizes. During a survey of Atmospheric revitalization is a discipline within the these facilities, it was discovered that they did not meet Environmental Control and Life Support (ECLS) which our requirements. For the most part, they were either addresses the process technologies and equipment too small, too big, not sufficiently air tight, or incapable of necessary to provide, monitor, and control the being man rated. Various project managers were also atmospheric environment within a crewed spacecraft or interviewed to understand their capabilities, limitations, components and tested again on a system level. and lessons learned. Testing could occur in stages, with each stage involving a higher level of fidelity and metabolic loading. Initial The result of the survey was that all existing facilities metabolic loads would be simulated with the Human were already in full use and would not be able to support Metabolic Simulator (HMS). The last stages of testing activities conceptualized for the ARTEF. The result of could involve actual human metabolic loads. the analysis was the selection of a facility containing a hypobaric chamber that was formerly used as a plant Typical technologies include regenerable carbon dioxide growth laboratory. This space is also adjacent to the removal, carbon dioxide collection and storage, carbon water recovery lab and thus would facilitate full scale dioxide reduction to water, trace contaminant control, integration activities. and environmental monitoring systems. The hypobaric chamber was named as the Air The ARTEF would be capable of conducting multiple Revitalization Technology Integration Chamber (ARTIC). simultaneous tests. For example, smaller component This chamber contains two air tight compartments, a level testing may be performed while a long term test is main chamber and an airlock. The airlock and main under way in an integrated systems test bed. The first chamber sections can have multiple uses in technology year of development was spent in requirements evaluation testing. Initially the airlock would be used as definition and facility survey. a mixing volume for various test articles. The long term goal was for the chamber to be human rated for NASA regulations require all systems to be failsafe. extended duration testing. Critical systems are required to have redundant safety. As a future option, the ARTEF could also support A list of required functions is given below: continuous long-duration testing of bioregenerative life - facility supply of gases: air, nitrogen, oxygen, carbon support systems. The ARTEF could operate in a dioxide manner capable of sustaining continuous test operations for extended periods. The first set of tests were planned - leak-tight environmental chamber (man-rated) to consist of shorter durations in order to mature the facility and test article systems. - facility available power, 120VAC, 208VAC, 480VAC in single and three phase DESIGN GOALS - 120 VDC power for ISS applications - Chilled water cooling system The ARTEF must accommodate technology ranging from bench top breadboard type concept to a full scale - liquid nitrogen supply proven technology ready to go into a flight hardware - room temperature control packaging. Needed to accommodate level of bench level testing as well as fully integrated testing with other - deionized water and drainage related systems such as water recovery and plants. - facility vacuum Representing a fully integrated closed loop recovery system. - combustible venting to outside - data acquisition and control network We recognized that in order to adequately develop any new technology, we needed to have the capability to - gas analyzer / mass spectrometer provide a flight like atmospheric environment. This includes the capability to simulate the human metabolic - integration capability with water recovery systems plant process of consuming oxygen, and producing carbon growth systems, and thermal control systems. dioxide, heat and moisture. This would have to be capable of reproducing different number of crew members at different activity levels. Additionally, we need a sealed airtight environmental chamber, and sufficient instrumentation to monitor the environmental conditions inside the chamber. Including reduced pressure and elevated oxygen levels. Typical operation of the evaluation lab would be to bench test each component of a technology to verify proper operation and document a baseline reference. Evaluations could also include control systems and end- to-end systems. Individual and integrated components could be evaluated for short term and long term testing. Each component could be integrated with other EMS allows new technology to be tested and verified prior to human testing, including behavior under off-nominal and emergency conditions. A wide range of simulated crew Work benches Console Storage activity profiles can also be evaluated and reproduced using a HMS. The HMS has proven to be the most complex and difficult to control processes. The design concept has been previously presented at ICES (Jeng, Test Article Bench 20xx), and can be referenced for further detail. issues ARTIC that have developed during the use of the design will be presented here. Test Article Bench A HMS at a minimum is required to consume/remove oxygen, produce CO2, moisture and sensible metabolic heat for multiple people and various metabolic rates all the while maintaining a mass balance with minimal Figure 1. Layout of the ARTEF external leakage. As optional capabilities it should accommodate reduced pressure, elevated oxygen atmosphere, and trace gases. It should not remove CABIN CHAMBER anything else from the atmosphere except for oxygen (O2). A leak tight chamber is needed to simulate a spacecraft cabin. The chamber serves as a mixing volume for the Daily-average metabolic consumption and production atmospheric gases. Having the right volume provides rates can vary considerably. Of the total metabolic heat an indication of the time delay between the time the production, part is dissipated by vaporization of water atmosphere changes and when the processing occurs. (latent heat), and part is dissipated by sensible heat As such, it’s necessary to have a variable volume to transfer to the environment. In volumetric (or molar) adjust to the needs of each test. Boxes were made up terms, the ratio of CO2 production to O2 consumption is to be airtight space fillers. Mylar was the obvious choice referred to as the respiratory quotient. This ratio varies material. little with activity level except during severe exercise. A constant respiratory quotient of 0.87 was assumed in In order to maintain mass balance in the system, the Table 1. In addition to the primary effects discussed chamber must be relatively tight. The ARTIC chamber above, humans also contribute to the production (and was designed
Details
-
File Typepdf
-
Upload Time-
-
Content LanguagesEnglish
-
Upload UserAnonymous/Not logged-in
-
File Pages8 Page
-
File Size-