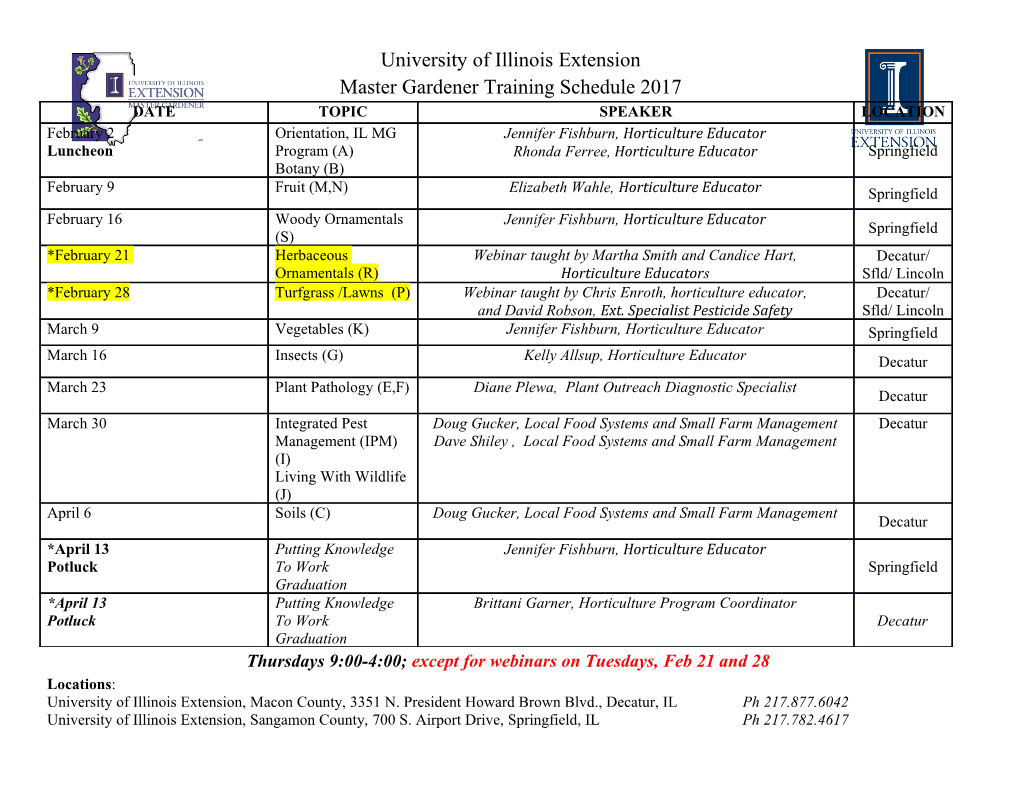
Extrusion Coating & Laminating 2008 Extrusion Coating Short Course, May 1, 2008 Beth Foederer OtOptex PSltiProcess Solutions, LLC Discuss ion T opi cs z Equipment and Purpose z Chill Water System Design and Control z Basics of Process z Calculations z TblhtiTroubleshooting Extrusion Coating & Laminating The goal in extrusion coating and/or litiitflaminating is to form a con tinuous, inclusion free polymer layer of uniform thickness, that adheres to the desired substrate(s). EtExtrus ion C oa ting Uses z Milk Cartons z Sugar Pouch z Ream Wrap z Cheese Wrap z Juice Cartons z Snacks z Sn ack F ood z Dryyes Mixes Packaging z Lidding Stock z Photo Paper z Multiwall Bags z Bakery Trays z Medical Packaging Nip Ro ll z What: Water cooled (generally double shell) roll with a rubber covering z FtiFunction: z To combine the substrate(s) and molten polymer together at the chill roll with even pressure z It removes air from the product z It facilitates cooling Nip Ro ll z Operation z Opens and closes with either pneumatic air cylinders or air bags. z Pressure is changed by adjusting air pressure to cylinders or bags. z Typical p ressure is 150 pli but can be higher. z Both rolls open for threading and safety Nip Ro ll Cover ings z Hypalon (Chlorosulfonated Polyethylene) z Shore hardness range: 40-90 z Good release, temp resistance, ozone resistance and easily reground z Neoprene (Polychloroprene) z Shore hardness range: 15-80 z Regrindable, not as durable, good release, inexpensive z Silicone ((yPolymethy lsiloxane) z Shore hardness range: 40-70 z Soft, v good release, temp resistance, good for porous substances Nip Ro ll Re lease O pti ons z Why do the edges need more release than center? z Teflon® Tape z Change for different widths z Teflon® Belts z Adjustable but difficult to use z Teflon® Sleeves z Costly Nip R o ll Defl ecti on z Bending of the roll due to gravity, tension and pressure z Backing roll helps the deflection z Function of roll diameter and construction z Can be measured by nip impression tape OR… z Corrected by crowning the roll z Caution: improper crowning will generate wrinkles in the nip BkiRllBacking Roll z What: Water Cooled z Chrome p la te ddd dou ble s he ll z Increases the life of the nip roll covering z FtiFunction: z Cools surface of nip roll to reduce sticking z Re duces bow ing /de flec tion o ffth the n ip ro ll Str ippi ng Ro ll z What: z Steel, aluminum or rubber covered idler roll z Opppyened and closed with pneumatic cylinders z Function: z Initiate even removal of product from chill roll z Location: z Metal roll is 1” or less from chill roll z Ru bber ro ll con tac ts c hill ro ll z Opens for threading and safety z Is adjustable if a wide variety of products is to be made Chill Ro ll Func tion z QhltlQuench molten polymer to strippable temperature z StSet ex trusi on line spee d– LdLead section z ItftttfilImpart surface texture to final product (extrusion coating only) Chill Roll Const ructi on z Diameter range: 18-50 inches z Mono flow z In one end, out other z Single shell desgn z Small Rolls only – not Rdd!!Recommended!! z Double shell design z Small amount of water, next to outhllter shell z Double shell spiral fluted z Most common design z Lowest delta T Chill Roll Fini sh z Surface roughness is a measure of the smoothness or texture of the roll surface z Ra – “Average Roughness” z RMS – “Root Mean Square” z 10 Ra = 11 RMS z Surface roughness determines how easily the polymer can be removed from the roll and the surface finish of an extrusion coated product. Chill Roll Fini sh es z Matte – 30-125 Ra typical z Grit blasted, plated with dull finish and good release z Gloss – 4-10 Ra typical z Precision ground and polished with good surface finish and release z Mirror – 2-4 Ra typical z BlBelt or stone po lihlish w ihhihlithhigh gloss an d poor release z Optical Mirror – 1 Ra or less MtMateri ilCalConsid erati ons z Heat Conductivity (k) – Steady state heat transfer rate within solid or liquid materials z Thermal Expansion – Fractional change in length or volume of material for unit temperature change z Durability – resistance to dents, scratches or deformation z Weight z Cost of raw materials and fabrication MtMateri ilSlalSelecti on Coefficient of Thermal Heat Conductivity** Material Expansion* Aluminum 12.8 1460 Brass 11.4 833 Chromiu m 343.4 480 Copper 9.8 2670 Gold 7.9 2090 I(Iron(pure ) 666.6 529 Nickel 7.2 421 Silver 10.5 2910 Steel(SAE 1020) 6.6 360 Steel(SAE 1095) 5.7 360 Steel 285 Grade B 6.5 - Stainless Steel(I8-8) 9.5 - *10e-6 in/in *°F **BTU-in /(°F –ft2 –hr) Chill Roll Temperat ure z Wha ttd do I need? z The ideal chill roll temperature is cool enoughht to a llow the coa ting to re lease cleanly, but warm enough so the polymer does not cool before having a chance to wet the substrate adequately. WtWater R eci rcul ltiation S yst em z Usually a closed loop system z Same water is chilled and re-circulated z CliCooling can be var idied z Based on extruder output z BhBy chang iting tempera ture o fllf rolls z Water temperature is controlled z Usually runs at 50-85oF Closed looppy chill roll system Makeup Water Temperature 50°F Controller 68°F 68°F Chiller Reservoir etc 3-Way Valve 50°F Pump T 68°F T T 65°F T 65°F Shut off Valve Pump T Thermometer Pump Chill Syst em F ouli ng z What: Any layer or deposit of extraneous material on a heat-transfer surface. This reduces thermal conductivity of surface. z Causes z Scale or mineral deposits z Algae z Rust z Prevention z Initial system treatment z Maintenance program z Removal of build-up is either chemical or mechanical Chill Roll Temperature 600°F Melt Temp. Contact time 0.24 sec Shell= 12mm (0.5”) 1.0 mil coating 120°F Substrate 70°F in Line Speed o 1000 ft/min 73 FoutF out 450°F 230°F 340°F EtExtrus ion P rocess V ar ibliables z Polymer Melt Temperature z Linespeed z Air Gap/Drawdown z Die Position Lead z Die Gap (not discussed) z Chill Roll Temperature z Nip Roll Pressure z Nip Roll Hardness OidtiOxidation ( melt ltt temperat ure) z All substances are either organic or inorganic z Organi c ma ter ia ls w ill burn z High temperatures promote faster oxida tion ra tes z At some temperature the ignition point will be reached. Bd/AdhiBond / Adhesion z All organic materials have a surface skin z This is an oxidized layer of itself (rust) z StilitidtihSome materials resist oxidation such as stainless steel z TO OBTAIN ADHESION BETWEEN TWO MATERIALS, ONE MUST BE LIQUID!!! z Too much oxidation destroys adhesion as does too little. Air Gap z The amount of time the molten polymer is in contact with air effects its adhesion to the substrate. z The longer the polymer is exposed to air, the cooler it becomes and tends to decrease adhesion z If th e me lt temperature is hig h enoug h, increase d time will increase oxidation and will improve adhesion z Therefore, an optimum air gap permitting maximum adhesion exists for each set of circumstances BdBond versus Air gap bond air gap MltCMelt Cur titain AiGAir Gap z Determined by linespeed z Raising Die z Time in air gap increases z 100ms for LDPE z TIAG=60 x ggp(ap(mm) / linespeed (m/min) z Neck-In increases z Melt temperature drops Air Gap Line Speed z 1” increase in gap = 10oF (in) (fpm) increase in melt 7.0 up to 700 8.5 700 – 1,200 temperature 10.0 1,200 – 1,800 12.0 1,800 and up NkNeck-In z Determined by: z Resin properties such as molecular weight and molecular weight distribution z Extrusion conditions such as melt temperature, line spp,peed, output rate and die pressure z Equipment geometry such as screw design, air gap and die lip gap Die Pos ition Lea d z Lead onto either substrate for improved adhesion z Issues z Substrate burn through z Web contraction on heavy coatweights z Linespeed will effect z Work needs to be done to optimize location Chill Ro ll Tempera ture Se tting z Too Cold produces rapid quench rate z Reduced adhesion z Roll mayygy sweat in high humidity z Too Warm produces slower quench rate z Polymer may stick to roll z Bond issues or tearing with substrate z Can wrap chill roll z Uneven Temperature z Poor or uneven strippability z Flow marks in product z Indication that chill roll may be fouling Chill Ro ll Str ip P ositi on If Roll to High…. …Chill Roll Surface Cannot Recover CL CL C L If Roll to Low…. Chill Roll CL ...Poor Stripability Resulting in Quality Defects A misaligned or Worn Roll Can Result in Wrinkles in the Product Chill Roll Recovery 600°F Melt Temp. 90°F 100°F 120°F B A 75°F The Chill Roll needs time and distance to recover cooling of its surface ( A to B ) Davis Standard Nip Impress ion z Amount of impression determined by: z Roll Hardness Impression z Roll Diameter Width z Nip Pressure z Wider nip z Improved adhesion z For heavier substrates z CtihlCan create pinholes z Even nip across the roll is important!!! Quick Calculation for Chill WtWater GPM mwxCpwx¨Tw = mp(Cppx¨Tp+hfp) x Eff mw = Mass Flow Water, lb/hr mp= Extruder Output, lb/hr Cpw = Specific Heat Water, BTU/lb-°F Cpp=Specific Heat Polymer, BTU/lb-°F ¨Tw= Temperature Rise Water, °F ¨Tp= Temperature Change Polymer, °F hfp = heat of Fusion Polyy,U/mer, BTU/lb Eff = Effeciency of System GPM = [(mp x 0.75 x ¨Tp)/(¨Tw x 500)] x 1.2 How much water do we need to pump through our chill roll if we have a rate or 1000 lb/hr LDPE, Melt Temperature 600°F, a Strip Temperature of 100°F, and 3°F Water Temperature Rise? lb BTU Btu BTU GPM = 1000 /hr (0.55 /lb-°F x (600-100°F)+0.48 /lb) / (1 /lb x 3°F x 480) * 0.7 = 275gpm GPM = [(1000 x 0.75 x (600-100)/(3 x 500)] x 1.3 = 325gpm *Assuming Chill roll is of adequate size **Increase GPM to allow for Nip and Backing Roll Flow Quick Calculation for Cooling Tonnage Ton = [mpx0.75x¨Tp/12,000] x 1.2 Mp = Extruder Outpp,ut, lb/hr ¨Tp = Temperature Change Polymer, °F Ton = Tonnage of Refrigeration required or available at 50°F 1.2 = Efficiency of 80% How much cooling is required if we are extruding 1000lb/hr of 600°F LDPE with a stripping Temperature of 100°F.
Details
-
File Typepdf
-
Upload Time-
-
Content LanguagesEnglish
-
Upload UserAnonymous/Not logged-in
-
File Pages26 Page
-
File Size-