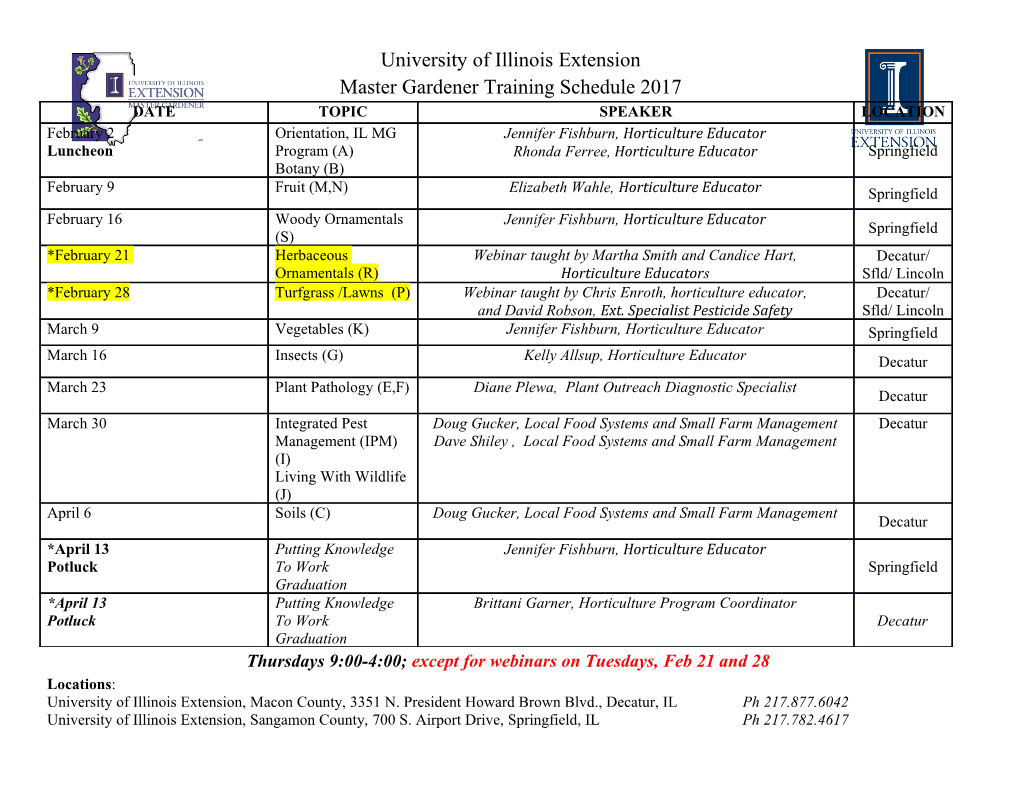
BR01B1848 ETDE-BR--0278 Hydraulic Turbines and Auxiliary Equipment Reporter: Mr. Luo Gaorong Deputy Director of International Centre of PCH of ONU in China .. Small Hydro Power in China L The Procedures of Small Hydro Power (SHP) Construction 1. The SHP Planning 1.1. The planning of middle and small rivers. Since all SHP stations are built on middle and small rivers, it is necessary to mnduct river planning before the SHP design, which shall be in accordance with multipurpose water resources utilization and cascade optimal development. To be more specific, river planning should take such purposes into account, namely, flood control, water supply, navigation, power generation, environmental protection, natural scene improvement, improvement of surviving conditions of human being, etc so as to develop water resources fully and rationally. At present, most rivers in China have been planned and the planning can be modified annually according to the social and economic development. The planning can be accomplished by water conse~ancy bureaus (departments) at the provincial, prefectural or county level as the river basin varies. 1.2. The planning of rural grid. Most SHP has been incorporated into the rural grid, so the electricity demand of the grid and load forecasting determine the SHP development. At present, most rural SHP grids face such a contradiction, i.e. abundant electricity during the flood season vs. electricity shortage during dry season, which can be relaxed a little bit by exchanging electricity with the national grid. So constructing SHP stations with yearly regulating reservoir has become a priority, 1.3. The SHP planning. If river planning and rural grid planning have been carried out, it is time to conduct SHP planning and feasibility study, which shall be accomplished by design institutions entrusted by project owners. At this stage, project size, dam type, turbine generator set should be determined, and electricity market analysis, investment estimate and economic appraisal should be conducted for the decisions-making of the project owners. After the feasibility study has been approved, preliminary design can start. 2. SHP design 2.1. SHP design can be devided into two parts, preliminary design and construction detailed drawings. During the preliminary design, the drawing of the main parts of the project and the drawing of overall set-up should be completed, major technical problems be solved, quantity of engineering work be estimated and preparation work before ordering equipments be carried out. Usually, preliminary design can be accomplished within a shoti period of time. After being further improved, the preliminary design forms the bidding design in the bidding document. 2.2. The detailed drawings should be completed by design institutions before the construction for the review of project owners and construction supervisors before they transfer them to the construction contractors to carry out construction. Or design institutions may supply the detailed drawings gradually according to the speed. The turbines with lower specific speed are used at higher heads, while turbines with higher n. are applied at low heads. Only for geometrically similar tucbines operating in kinetically similar renditions the value of the specific speed n. is the same. Peiton 12-30 TUWO 20-70 b Cross-flow 20-80 Francis 80-300 Propeller and Kaplan 300-1000 \ , The above mentioned figures of the Pelton and Turgo turbines are suitable for single jet, if Pelton turbine with two jets each having a specific speed of 15 can produce double power. This 2 jet Pelton would be equivalent to a tutiine with a specific speed of 15.2 or 21. 1. Francis turbine Francis turbine is understood as a turbine in which the water flow enters the runner inwards in radial direction, changes its direction gradually and then possesses a direction out axially. A Francis turbine may be operated over a range of discharge from approximately 40 to 105 percent of rated discharge. Below 40 percent rated discharge, there can be an area of operation where the vibration and power surge occur. The upper limit generally corresponds to the generator rating. The approximate head range for operation is from 60 to 125 percent of the design head. The maximum efficiency of a Francis turbine is established at 90 percent of the rated capacity of the turbine. This type of turbine is the most common one in use today in China. In the series design of less than 10000 kW turbines, the head range used is from 8-300 m, and the maximum discharge reaches 7.7 m3/second it also can be applicated in high heads even up to 650 m in special design. The Francis turbine may be mounted with vertical (Fig.2) or horizontal shafts (Fig.3). The vertical arrangement requires smaller area and permits a deeper setting of the turbine with respect to tailwater elevation without locating the generator below the tail-water. Generator costs for vertical units are higher than those for horizontal units because of the need for a larger thrust bearing. However, the savings on construction costs for medium and large units generally offset this equipment cost increase. 3 ~~ > 3 . The shaft arrangement is of vertical J for runner diameters above 100 cm in Chinese standard. From manufacturing considerations a horizontal one is usually economical for a relatively smaller diameter up to 84 cm. It has the advantage of providing easy access and the runner ● can be dismantled after removal of . the conical draft tube. The runner consists of a band and a -. crown joined by runner blades. Blade * profiles directly influence the energy > convert and the cavitation performance, therefore high . requirements for the accuracy of the blade shape and the smooth finish of the surface have to be met and the welding construction of the runner has i“ been widely adopted instead of the iron I I one. L The horizontal unit is mostly provided with three bearings, two of them for the generator and the other one for the turbine (see Fig.3). Nowadays a two bearing arrangement (Fig.4) as a simplification of three bearing layout is coming into vogue, especially for the unit up to 3000 kW. The flywheel is mounted on the shaft in order to stabilize the unit in operation during load rejection. The expansive joint is used to adjust the clearance of the turbine set during assembling and disassembling. The spiral casing of the turbine surrounding the guide vanes may be made of cast iron for small-sized low heads, and cast steel for high heads and sheet steel for large-sized high heads. The concrete spiral casing is suitable for large-sized one with low heads. The guide vane mechanism consists of guide vanes, level, link and regulating ring. Besides there is a breaking link or shear pin which is designed to tail on excessive load, and its adjustment is performed by means of a servomotor through action of regulating ring. The linkage-mounted control unit is used in turbine series below 500 kW. For high head varieties e.g. HL1 10-WJ the outlet diameter of the runner is small, the control parts can be moved on to the side of the draft tube for mounting and dismounting simply. I . Bearings are used to maintain alignment of the shaft and to take forces acting upon them. Rolling bearings find use only for the runner diameter less than 35 cm, but sliding ones for large units, above 42 cm in diameter. As the Francis turbine is of reaction type, the water enters the runner under pressure. This calls for a sealing arrangement to avoid the leakage inside the clearance between the rotating runner and the stationary bottom ring or the head ring which may cause an appreciable amount specially at high heads. A comb configuration is often adopted on the enter of the band and crown by shrinking. In order to reduce silt wear surfaces of the clearance between guide vanes and the bottom ring or the head cover are covered with replaceable auti-wear plates made of stainless steel. A braking device is provided for the turbine with a plain bearing, either on the side surfaces or on the outer periphery of the flywheel. As the unit begins to shut down the rotating speed of the main shaft becomes lower and lower. When its speed reduces to about 30?40of the rated value, the device will be actuated to stop the movement of the shaft immediately, othetwise the bearing may be burst out at such low speed. 2. Axial-flow turbine The future of the axial-flow turbine is that the water ,Z-e, flow passes through the runner in an axial ,. - direction with respect to the shaft. It is suitable for ~- El exploiting hydropower of low head and large ~ ‘!!/Y discharge. The changes of the discharge and the optimum !~ . - . ~ . ---00s are..- -r MI la --, . hydraulic performance may be achieved by Fie.5 ~perioon of p~vl 1,~( regulating runner blades and/or guide vanes. runner per fore:. xe Fig. 5 shows comparative efficiency curves depending on the discharge of various combination. The turbine with adjustable blades and adjustable guide vanes, so called Kaplan turbine, possesses a better efficiency curve over a wide range of operation, while the turbine with fixed blades and adjusted guide vanes (Propeller turbine) has a sharp efficiency drop at the part load range. Because of simples construction and easy manufacture, the Propeller turbine is widely adopted in small-sized units. It covers the range of the runner diameter up to 1.4 m in Chinese turbine series. In order to overcome the shortage of the efficiency drop several units are always installed at single site. The Kaplan turbine is suitable for the site with large changes in head and load.
Details
-
File Typepdf
-
Upload Time-
-
Content LanguagesEnglish
-
Upload UserAnonymous/Not logged-in
-
File Pages31 Page
-
File Size-