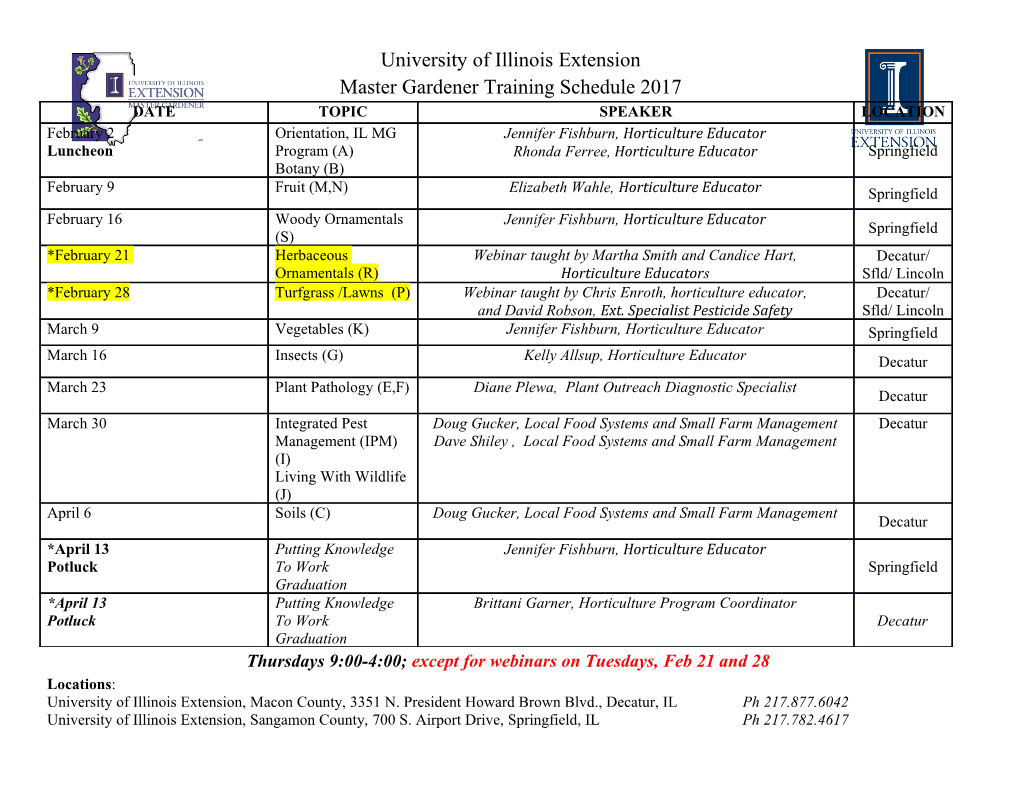
Active Heat Transfer Enhancement in Integrated Fan Heat Sinks by Wayne L. Staats, Jr. B.S., University of Wisconsin-Madison (2006) S.M., Massachusetts Institute of Technology (2008) Submitted to the Department of Mechanical Engineering in partial fulfillment of the requirements for the degree of Doctor of Philosophy in Mechanical Engineering at the MASSACHUSETTS INSTITUTE OF TECHNOLOGY September 2012 © Massachusetts Institute of Technology 2012. All rights reserved. Author.......................................................................... Department of Mechanical Engineering August 31, 2012 Certified by. J.G. Brisson Professor of Mechanical Engineering Thesis Supervisor Accepted by . David E. Hardt Chairman, Department Committee on Graduate Theses 2 Active Heat Transfer Enhancement in Integrated Fan Heat Sinks by Wayne L. Staats, Jr. Submitted to the Department of Mechanical Engineering on August 31, 2012, in partial fulfillment of the requirements for the degree of Doctor of Philosophy in Mechanical Engineering Abstract Modern computer processors require significant cooling to achieve their full performance. The “efficiency” of heat sinks is also becoming more important: cooling of electronics consumes 1% of worldwide electricity use by some estimates. Unfortunately, current cool- ing technologies often focus on improving heat transfer at the expense of efficiency. The present work focuses on a unique, compact, and efficient air cooled heat sink which ad- dresses these shortcomings. While conventional air cooled heat sinks typically use a sep- arate fan to force air flow over heated fins, the new design incorporates centrifugal fans directly into the body of a loop heat pipe with multiple planar condensers. These ”inte- grated fans” rotate between the planar condensers, in close proximity to the hot surfaces, establishing a radially outward flow of cooling air. The proximity of the rotating impellers to the condenser surfaces results in a marked enhancement in the convective heat transfer coefficient without a large increase in input power. To develop an understanding of the heat transfer in integrated fan heat sinks, a series of experiments was performed to simultaneously characterize the fan performance and average heat transfer coefficients. These characterizations were performed for 15 differ- ent impeller profiles with various impeller-to-gap thickness ratios. The local heat transfer coefficient was also measured using a new heated-thin-film infrared thermography tech- nique capable of applying various thermal boundary conditions. The heat transfer was found to be a function of the flow and rotational Reynolds num- bers, and the results suggest that turbulent flow structures introduced by the fans govern the transport of thermal energy in the air. The insensitivity of the heat transfer to the im- peller profile decouples the fan design from the convection enhancement problem, greatly simplifying the heat sink design process. Based on the experimental results, heat transfer and fan performance correlations were developed (most notably, a two-parameter corre- lation that predicts the dimensionless heat transfer coefficients across 98% of the experi- mental work to within 20% relative RMS error). Finally, models were developed to describe the scaling of the heat transfer and me- chanical power consumption in multi-fan heat sinks. These models were assessed against experimental results from two prototypes, and suggest that future integrated fan heat sink designs can achieve a 4x reduction in thermal resistance and 3x increase in coefficient of performance compared to current state-of-the-art air cooled heat sinks. Thesis Supervisor: J.G. Brisson Title: Professor of Mechanical Engineering 3 4 ACKNOWLEDGEMENTS First, I acknowledge Professor Brisson for being an inspiring mentor and advisor. He pro- vided me with a unique environment in the Cryogenic Engineering Laboratory to sharpen my research skills. I have, through innumerable discussions and arguments with Professor Brisson, learned a great deal about thermal engineering, but also about physics, engineer- ing, and teaching. I value the rapport we developed over the years and I find his candor and willingness to give honest feedback refreshing. My committee (Professor Evelyn Wang, Professor Bora Mikic,´ and Dr. Choon Tan) has been a pleasure to work with. I’m grateful that Professor Evelyn Wang gave me the chance to join the “PHUMP” project and perform this research. Evelyn’s door has always been open for discussion, and her tireless devotion to research, teaching and advising has been a source of inspiration. I consider myself fortunate to know Professor Bora Mikic´ both as a teacher and a committee member. His impressive breadth and depth of heat transfer knowledge reminds me that the learning process never stops. Finally, I appreciate the wise and thoughtful feedback of Dr. Choon Tan, whose turbomachinery and general fluid modeling expertise have led to many productive discussions. I’ve had the good fortune of working with smart, talented colleagues in this research: Professors J.G. Brisson, Evelyn Wang, and Jeffrey Lang; postdocs Teresa Peters, Martin Cleary, and Matthew McCarthy; Ph.D. candidate H. Arthur Kariya; S.M. students Jon Al- lison, Alonso Dom´ınguez, Daniel Hanks, David Jenicek, Catherine Koveal, and Nicholas Roche; and undergraduate researchers Tess Saxton-Fox, Ari Umans, Kai Cao, Jay Sircar, and Kristyn Kadala. These students exhibited a technical perseverance and general joie de vivre that made our lab an enjoyable environment. I’m thankful that the Defense Advanced Research Projects Agency (DARPA) had the foresight to address the thermal management issues that relate to this research. More generally, I’m honored by the responsibility of performing research on behalf of the U.S. taxpayers and glad that our society values science enough to devote our resources to the pursuit of additional knowledge. I’ve enjoyed being a part of the Cryogenic Engineering Laboratory at MIT. I’m fortu- nate that Professor Joseph L. Smith, Jr. was available for discussions and advice. He is a perfect example of a lifelong engineer; he’s as comfortable disassembling the helium liquefier, machining, or welding as he is discussing the subtleties of the Second Law. Pro- fessor Ernest Cravalho provided me with a teaching assistantship that I found reward- ing. I’ve known several students in the lab, as well, and have enjoyed working with them 5 or discussing interesting problems: Barbara Botros, Martin Segado, Jake Hogan, Kevin DiGenova, Alonso Dom´ınguez, Teresa Peters, Martin Cleary, Jon Allison, and Gunaranjan Chaudhry (the Grand Integrator). In particular, I enjoyed many productive and stimulat- ing discussions with Martin Segado and appreciated his thoughtful thermal-engineering perspectives. The lab would not be the same without Doris Elsemiller’s administrative acumen and colorful personality. Verily, one of the best aspects of my time at MIT has been the opportunity to befriend many unique but invariably exceptional people (too many to enumerate here). Several of these friends have directly helped in my research. I thank: Joe Petrzelka for wiring and PCB advice; Kevin Cedrone (and the Sloan Automotive Lab) for lending a thermal mass flow meter; Misha Wolfson for developing the MEX interface between MATLAB and the motor controller; Mark Belanger, expert machinist, for managing my favorite shop on the MIT campus (the Edgerton Student Shop); Matt Humbert for many discussions and for helping me cut impellers on the waterjet; Adam Wahab for his tips on soldering surface mount components; and John W. Roberts, Jr. for sharing his expertise and giving advice about tuning closed-loop control systems. I thank Mike Fischer of Engineered Metal Prod- ucts in Jackson, Wisconsin for his help over the years in laser cutting parts (notably, many of the parts in the circular stator apparatus). Finally, two parts of the Mechanical Engi- neering Department at MIT deserve a special thanks: the graduate office (Leslie Regan and Joan Kravit) for their advocacy of graduate students, and the Graduate Association of Mechanical Engineers (GAME) for providing forums for fruitful (as well as frivolous) cross-disciplinary discussion (e.g. my personal favorite, GAME coffee hour). I’m fortunate to have constant support from my family. My father (Wayne L. Staats, Sr.) and sisters (Heidi and Wendy Staats) seem to enjoy talking about my work, and are always willing to provide moral support. My mother, Judy Staats, lives on in my memory. She was a proud, loving mom who always encouraged my academic development. I admire her dedication to teaching, her profession and passion. Finally, my lovely wife Brooke and daughter Anna have been a constant source of love and support. Brooke has always encouraged me and is my steady horizon in the sometimes tumultuous seas of research. I’m incredibly lucky to have her and I can’t imagine a more fulfilling home life. 6 CONTENTS 1 Introduction 17 1.1 Motivation...................................... 18 1.2 Thermal Management of Electronics....................... 19 1.3 Air Cooled Heat Sink Design............................ 21 1.3.1 Design Compromises............................ 22 1.3.2 Performance Evaluation Criteria of Heat Sinks............. 23 1.3.3 Pipe Flow Example............................. 24 1.4 Heat Transfer Enhancement Techniques..................... 27 1.4.1 Passive Enhancement............................ 28 1.4.2 Active Enhancement............................ 28 1.5 Compact Heat Sinks:
Details
-
File Typepdf
-
Upload Time-
-
Content LanguagesEnglish
-
Upload UserAnonymous/Not logged-in
-
File Pages211 Page
-
File Size-