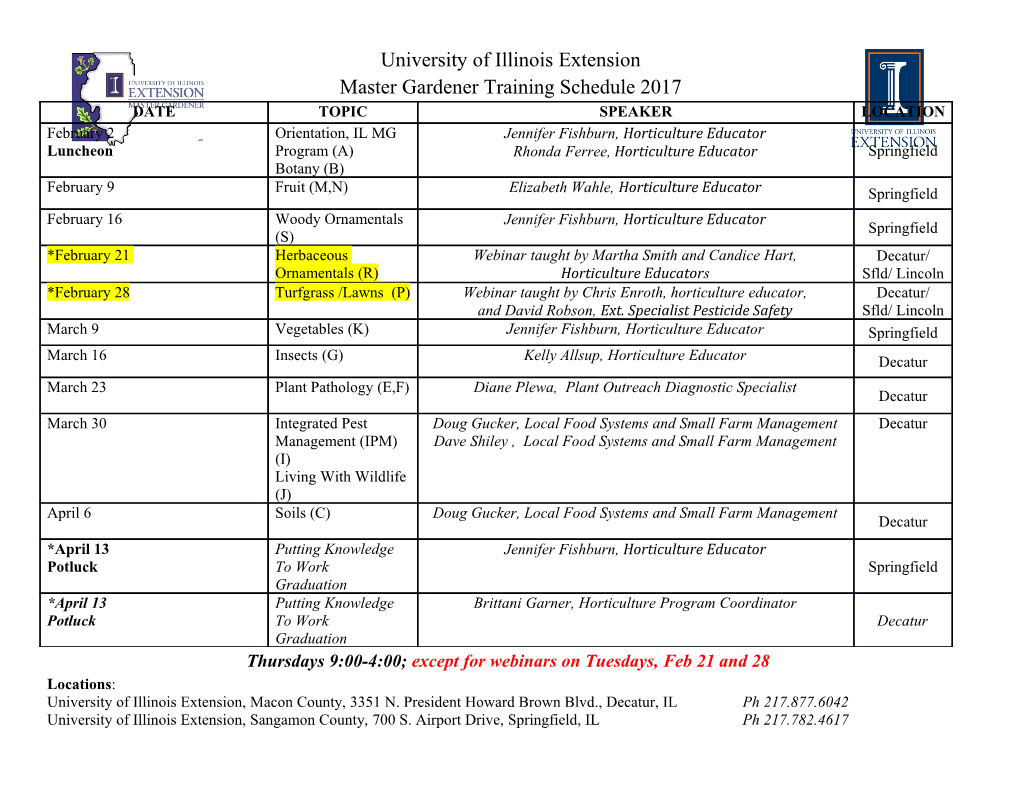
INTAKE MANIFOLD DESIGN FOR AN AIR RESTRICTED ENGINE A Thesis submitted to the Division of Research and Advanced Studies of The University of Cincinnati In Partial Fulfillment of the requirements for the degree of MASTER OF SCIENCE School of Dynamic Systems College of Engineering and Applied Science July 6, 2012 By David Anthony Moster BSME 2005 Abstract The purpose of this work is to study the effects that an air restriction has on basic intake manifold design calculations. When designing an intake manifold for a combustion engine, there are several simple methods that engineers have used historically to help determine peak volumetric efficiency per engine rpm. Methods such as Helmholtz Resonator Tuning and Pressure Wave Tuning have been used substantially to determine an engine’s operating conditions. However, these methods are flawed for the restricted engine case due to the assumption that there is an unlimited amount of air. Through experimentation of various intake manifold configurations, it is possible to determine how this false assumption affects the results of the design. Examination of each major design parameter of an intake manifold independently compared with the traditional analytical hypothesis is performed to help to determine if these methods can still be used in an air restricted environment. Based on the results from this experimentation, it appears that these calculations can still determine where peak volumetric efficiency is. However, the area around the peak volumetric efficiency is affected significantly. 1 Acknowledgments I would like to thank my advisor, Dr. Randall Allemang, for his support and guidance throughout my undergraduate and graduate studies. It is his push for educational excellence that has driven my knowledge growth. I am grateful to Dr. Kumar Vemaganti and Dr. David Thompson for taking the time to be a member of my committee. I want to thank Jeff Kenney for his work in building and testing the various intake manifold configurations as well as his support in design theory conversations. I want to express my sincere appreciation to Ryan Lake for the many hours spent discussing engine tuning theory and testing various architectures on the engine dyno that he modified; to Benjamin Stoney for his fabrication efforts that made the testing possible and his late night rants that made for laughs down the road; and to Thomas Steed for his drive and dedication which was inspirational to me as well. Special thanks to Fred Jabs, Kevin Sobkowiak, and Andrew Gorton for their help though various stages of the project. Finally, I want to thank my wife, Krystal, for her dedication and support from the very beginning. 2 Table of Contents CHAPTER 1: INTRODUCTION AND BACKGROUND ......................................................... 6 1.1 INTAKE MANIFOLD BASICS / ENGINE INDUCTION ................................................................. 9 1.2 COMPOSITION OF AN INTAKE MANIFOLD .............................................................................. 9 1.3 AIMS OF A MANIFOLD .......................................................................................................... 11 1.4 TRADITIONAL CALCULATIONS ............................................................................................ 13 1.5 SUMMARY OF THESIS ........................................................................................................... 16 CHAPTER 2: EFFECT OF RUNNER LENGTH .................................................................... 17 2.1 CALCULATIONS .................................................................................................................... 19 2.2 EXPERIMENTATION .............................................................................................................. 20 2.3 RESULTS ............................................................................................................................... 22 CHAPTER 3: EFFECT OF RUNNER DIAMETER ............................................................... 29 3.1 CALCULATIONS .................................................................................................................... 30 3.2 RESULTS ............................................................................................................................... 30 CHAPTER 4: EFFECT OF PLENUM DESIGN ...................................................................... 32 4.1 EXPERIMENTS ...................................................................................................................... 35 4.2 RESULTS ............................................................................................................................... 36 CHAPTER 5: OTHER CONSIDERATIONS ........................................................................... 38 5.1 FLOW PATH .......................................................................................................................... 39 5.2 INJECTOR PLACEMENT ......................................................................................................... 40 5.3 RESTRICTOR DESIGN............................................................................................................ 41 CHAPTER 6: CONCLUSIONS AND FUTURE RECOMMENDATIONS ........................... 43 6.1 CONCLUSIONS ...................................................................................................................... 43 6.2 FUTURE RECOMMENDATIONS .............................................................................................. 45 APPENDIX A: RAW TEST DATA .......................................................................................... 48 3 List of Figures FIGURE 1: AIR FLOW THROUGH AN ENGINE ......................................................................... 8 FIGURE 2: INTAKE MANIFOLD ............................................................................................ 10 FIGURE 3: VARIABLE INTAKE LENGTH EXAMPLE ............................................................... 11 FIGURE 4: DUAL PLENUM EXAMPLE .................................................................................. 11 FIGURE 5: DRIVING HISTOGRAM ........................................................................................ 12 FIGURE 6: PRESSURE WAVE ALONG AN INTAKE RUNNER ................................................... 15 FIGURE 7: THOMPSON’S DEMONSTRATION OF VARYING RUNNER LENGTH ......................... 18 FIGURE 8: TEST SETUP - VIEW DOWN INTAKE PORT ........................................................... 21 FIGURE 9: TEST SETUP - ADJUSTABLE LENGTH SLEEVES ................................................... 21 FIGURE 10: EXPERIMENTAL RUNNER LENGTH COMPARISON .............................................. 23 FIGURE 11: PEAK VOLUMETRIC EFFICIENCY – HELMHOLTZ VS. TEST RESULTS ................. 24 FIGURE 12: RELATIVE ERROR FOR HELMHOLTZ VS. TEST RESULTS ................................... 24 FIGURE 13: PEAK VOLUMETRIC EFFICIENCY - PRESSURE WAVE VS. TEST RESULTS ........... 25 FIGURE 14: RELATIVE ERROR FOR PRESSURE WAVE VS. TEST RESULTS ............................ 25 FIGURE 15: EFFECT OF VARYING RUNNER DIAMETER WITH A CONSTANT LENGTH ............. 31 FIGURE 16: CENTRAL LOG INTAKE MANIFOLD .................................................................. 33 FIGURE 17: SIDE LOG INTAKE MANIFOLD.......................................................................... 34 FIGURE 18: INTAKE TEMPERATURE VARIATION................................................................. 36 FIGURE 19: INTAKE VOLUMETRIC EFFICIENCY VARIATION ............................................... 37 FIGURE 20: NOZZLE FLOW CFD ........................................................................................ 42 4 List of Tables TABLE 1: HELMHOLTZ CALCULATION RESULTS; CONSTANT DIAMETER ........................... 19 TABLE 2: PRESSSURE WAVE TUNING RESULTS; CONSTANT DIAMETER............................. 20 TABLE 3: TEST RESULTS - PEAK VE SPEED AND MAGNITUDE ............................................ 22 TABLE 4: HELMHOLTZ CALCULATION RESULTS; CONSTANT LENGTH ............................... 30 5 Chapter 1: Introduction and Background In automobile racing, several rule committees overseeing the class, such as Formula SAE, develop rules to provide a safe environment, as well as a more level playing field. With Formula SAE, many of the rules are intended to challenge the designers to provide a solution, from test or analysis, to a particularly challenging issue. One rule that is often imposed is a restriction on the air intake diameter. The purpose of this is to limit the amount of power the engine can produce, to reduce the speed of the vehicle, and bring the power to more comparable levels across the class for more equal competition. With the restricted air intake rule, it becomes the design engineer’s job to maximize performance, while adhering to these rules. This is a challenging issue due to the conflicting compromises that must be made when designing a manifold and a problem that covers multiple engineering disciplines such as fluids, thermal, materials, and manufacturing. A deeper challenge comes from the very limited references available to use in the design, and the majority of what is available is either not for a restricted engine, is too application specific, or too condition specific such as Blair’s articles on a restricted engine where the engine speed is well above the typical operating range [1]. The use of traditional hand calculations becomes less insightful to
Details
-
File Typepdf
-
Upload Time-
-
Content LanguagesEnglish
-
Upload UserAnonymous/Not logged-in
-
File Pages69 Page
-
File Size-