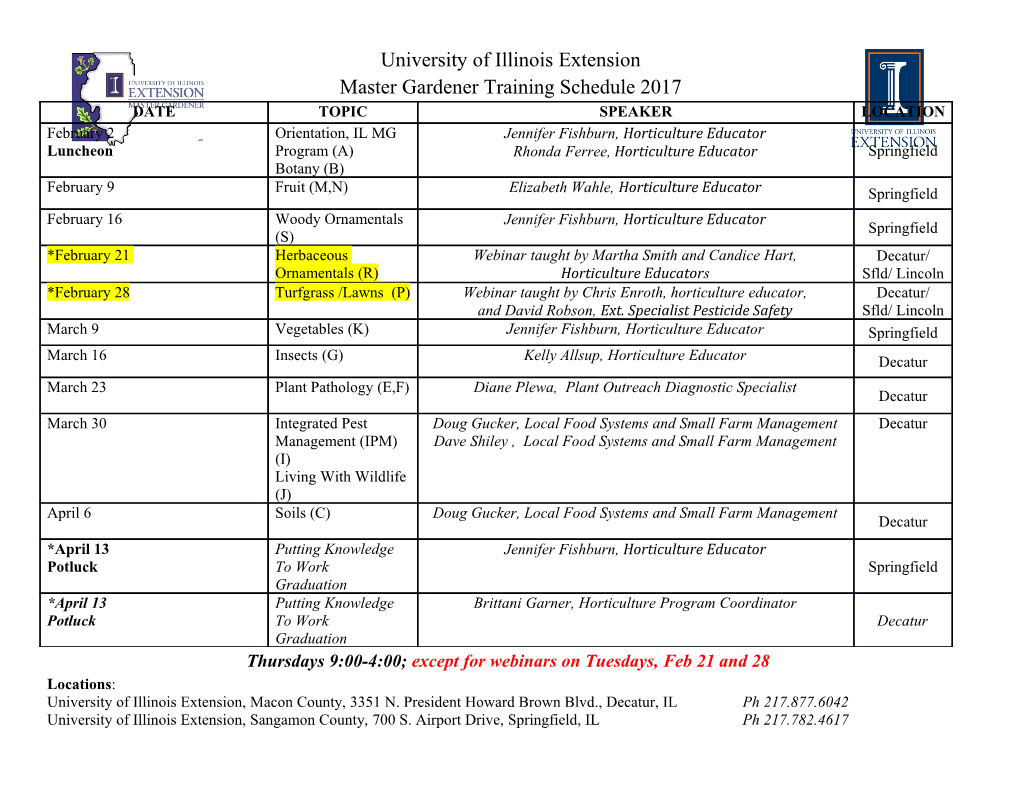
AT0100373 44 RM 9 M. Knuwer et al. 15" International Plansee Seminar, Eds. G. Kneringer, P. Rodhammer and H. Wildner, Plansee Holding AG, Reutte (2001), Vol. 1 Injection Moulded Tungsten and Molybdenum Copper Alloys for Microelectronic Housings M. Knuwer, H. Meinhardf, K.-H. Wichmanrf Fraunhofer-lnstitute for Manufacturing and Advanced Materials (IFAM), Bremen, Germany *H.C. Starck GmbH & Co. KG, Laufenburg, Germany +EADS Deutschland GmbH, Ulm, Germany Summary Molybdenum- and tungsten-copper alloys were developed as promising housing materials for high-frequency- (HF-) microelectronic packaging. Three different powder processing routes (mixing, attritor milling, compound powder), different particle sizes and copper contents were tested to achieve the best possible result in thermal and mechanical properties. Net shape processing of the parts took place via metal-injection-moulding, debindering and sintering. It could be seen that the sintering behaviour (density and shrinking rate) was strongly depending on the copper content and tungsten particle size. Lowest sinter activity was detected for a W90Cu10 powder mixture with coarse (d50=3,5um) tungsten powder, highest for the new developed Mo68Cu32 compound powder. Using compound powder leads to higher density at lower sinter temperatures compared to conventional processed WCu or MoCu powder mixtures. MoCu and WCu housing demonstrators were produced and HF-equipment was integrated. First electrical tests of the integrated demonstrator were performed successfully. Keywords tungsten, molybdenum, copper, thermal management, high frequency, thermal expansion 1 Introduction The current technical development is distinguished by an extensively growing use of mobile-communication and multi-media systems. The increasing number of these systems results in a likewise increasing demand on high 1. Kniiwer et al. RM9 45 15" International Plansee Seminar, Eds. G. Kneringer, P. Rodhammer and H. Wildner, Plansee Holding AG, Reutte (2001), Vol. 1 frequency (HF-) transmitting wave bands. Number and width of the needed wave-bands are limited, so that it will be necessary to increase the frequency limit - in future up to 300 GHz. These high frequencies require a new generation of advanced HF-circuits integrated on gallium-arsenide (GaAs) chips, a material which is much more sensitive against humidity, mechanical impact and thermal stress than silicon. Furthermore the circuits produce a high amount of heat loss which has to be dissipated by the housing material to avoid overheating and self-destruction of the module. Designated applications are automotive distance- and cruise-control systems, local communication networks or Active Phased Array Radar systems, consisting of more than 1000 of separate radar transmit/receive- (TR-) modules. So the following requirements for proper housing materials can be derived: • high denseness (protection against moisture and other environmental impacts) • high thermal conductivity (dissipation of the accrued heat loss) • coefficient of thermal expansion (a) near to GaAs: 5,8-10"6 K'1 (protection against thermal stress) • sufficient mechanical strength (protection against mechanical damages) • high shielding capability (protection against internal and external interfering signals) MMIC internal -j bond (GaAs) top cover shielding housing AI2O3- substrate adhesive I" cooling duct Fig. 1: Schematic view into a typical HF-module It is relatively easy to achieve good results in denseness and mechanical strength by using metal as housing material, but it is difficult to combine high thermal conductivity (X) and low coefficient of thermal expansion cte (a) in one material. A potential material with a low coefficient of thermal expansion 46 RM9 1. Knuwer et al. 15" International Piansee Seminar, Eds. G. Kneringer, P. Rodhammer and H. Wildner, Plansee Holding AG, Reutte (2001), Vol. 1 is Kovar®, but it also has a very low thermal conductivity which limits the performance of the HF-circuit. On the other hand, copper is a material with an excellent thermal conductivity but combined with a very high a-value. There is no single material with suitable high thermal conductivity and low cte. The combination of both is possible in an alloy system without miscibility of the two (or more) phases. In this case, the properties of the compound are determined by the properties of the single phases. Such systems are e.g. pseudoalloys of refractory metals (tungsten, molybdenum) and copper [1,2]. Tungsten and molybdenum show a moderate thermal conductivity and a very low a-value. The addition of copper increases both the thermal conductivity and the cte corresponding to the alloy composition and makes it suitable for microelectronic application. The processing of these alloys is only possible with powder metallurgy methods. A near net shape mass-production of complex shaped parts is feasible via metal-injection moulding. Other proper housing materials are SiAI-alloys with an aluminium content between 30 and 50 w.% as well as AIN. The SiAl alloys show disadvantages in the net shape processing which is only possible via machining [3]. Aluminium nitride (AIN) can be net shape produced via ceramic injection moulding but shows disadvantages both in metallisation behaviour and brittleness [4]. A comparison of some materials is shown in table 1. An impressive view into a fully integrated high-frequency demonstrator (hand made prototype with metal-injection-moulded housing) gives fig. 2. Table 1: Different potential housing materials for integrated HF circuits on GaAs chips. W/MoCu-values are theoretical values, based on the use of different mixing rules P a E 3 Material [gem ] [W m-1 K-1] [10-6K-1] [GPa] Si70AI30 2,4 130 6,8 44 Kovar(Fe54Ni31Co15) 17 4,9 138 Copper 9,0 397 17,0 128 Tungsten 19,3 174 4,5 407 Molybdenum 10,2 137 5,1 329 W80Cu20 15,66 216-252 6,1-8,8 242-309 Mo68Cu32 9,76 178-228 6,75-9,27 212-259 AIN 3,3 200 320 M. Knüwer et al. RM 9 47 15lh International Plansee Seminar, Eds. G. Kneringer, P. Ródhammer and H. Wildner, Plansee Holding AG, Reutte (2001), Vol. 1 HF-input HF-output MoCu ceramic housing, substrate metal- with injection- integrated moulded HF-circuit Fig. 2: Fully integrated HF-demonstrator with a metal-injection-moulded Mo68Cu32-housing. The housing will be closed for usage and tests by a laser welded top cover 2 Experimental details The experimental work was focused on the sintering behaviour. The influence of following parameters was investigated: • copper content • particle size • sinter temperature • sinter time • attritor milling • compound powder Copper content First important parameter is the copper content of the alloy. During sintering it determines the amount of liquid phase and therewith the sintering speed as well as the gravity induced separation of liquid and solid phase. In the sintered part it defines the cte and the thermal conductivity. In most 48 RM9 M. Kniiwer et al. 15:r International Plansee Seminar, Eds. G. Kneringer, P. Rodhammer and H. Wildner, Plansee Holding AG, Reutte (2001), Vol. 1 commercial alloys the copper content is set between 5 and 50 w.%. In this work following copper contents were investigated: • MoCu: 32 w.%, 40 w.%, 60 w.% . WCu: 10 w.%, 20 w.%, 30 w.% Particle size The particle size is the second important parameter. It was varied both for the tungsten and for the copper particles. The molybdenum particle size was constant. The particle sizes of the used powders (d50-values, laser diffraction measurement) are shown in table 2: Table 2: Particle sizes and internal code of the used metal powders powder internal code d5o [urn] Mo P89-II 6,58 Wfine P71 1,54 W coarse P72 3,55 Cu fine P73 6,04 Cu coarse P74 12,00 Sintering temperature The sintering temperature was set above the melting temperature of copper, so that liquid phase sintering occurred. On the one hand, an increasing sintering temperature decreases the viscosity of the copper melt and increases the interactivity of copper and refractory metal. On the other hand, caused by the low boiling point of copper, there is a danger of copper evaporation and contamination of the sinter furnace at higher temperatures. So the samples were sintered at temperatures between 1200°C and 1350°C [5-7]. Sintering time The densification during liquid phase sintering is mainly caused by particle rearrangement [8]. Particle rearrangement is much faster than other sintering processes, so that above the melting point of copper at first an intensive shrinkage should appear with is followed by a slight shrinkage caused by diffusion and/or solution-precipitation processes. M. Knuwer et al. RM9 49 15" International Plansee Seminar, Eds. G. Kneringer, P. Rodhammer and H. Wildner, Plansee Holding AG, Reutte (2001), Vol. 1 Attritor milling In the case of MoCu-powders the Mo60Cu40-powder was additionally 9h attritor milled after mixing. It was expected to reach a higher sinter activity with attritor milling because of the high amount of inducted mechanical energy. Furthermore it was anticipated that the cracking of agglomerates leads to a much better microstructural homogeneity of the sintered samples. Compound powder A further step in optimisation of both sinter activity and microstructural homogeneity was the development of a so called "compound powder" by H.C. Starck. It consists of a not demixable and extremely homogeneous distribution of copper and refractory metal particles. The different processed and investigated W/MoCu powders are shown in table 3. Because of the high number of investigated powders the results shown further on are a selection of the whole experimental work. Table 3: Processed and investigated W/MoCu powders powder alloy composition (w.%) powder composition P75 W90Cu10 W-P71 CU-P73 P76 W90Cu10 W-P72 Cu-P74 P125 W80Cu20 W-P71 Cu-P73 P78 W70Cu30 W-P71 CU-P74 P77 W70Cu30 W-P72 CU-P73 P84 Mo40Cu60 MO-P89-II Cu-P74 P90 Mo60Cu40 Mo-P89-ll Cu-P73 P90AT Mo60Cu40 P90 attrited P116 Mo68Cu32 compound powder P137 W80Cu20 compound powder The powders were mixed in a double sigma kneader with a polymer/wax binder system resulting in a homogeneous feedstock.
Details
-
File Typepdf
-
Upload Time-
-
Content LanguagesEnglish
-
Upload UserAnonymous/Not logged-in
-
File Pages16 Page
-
File Size-