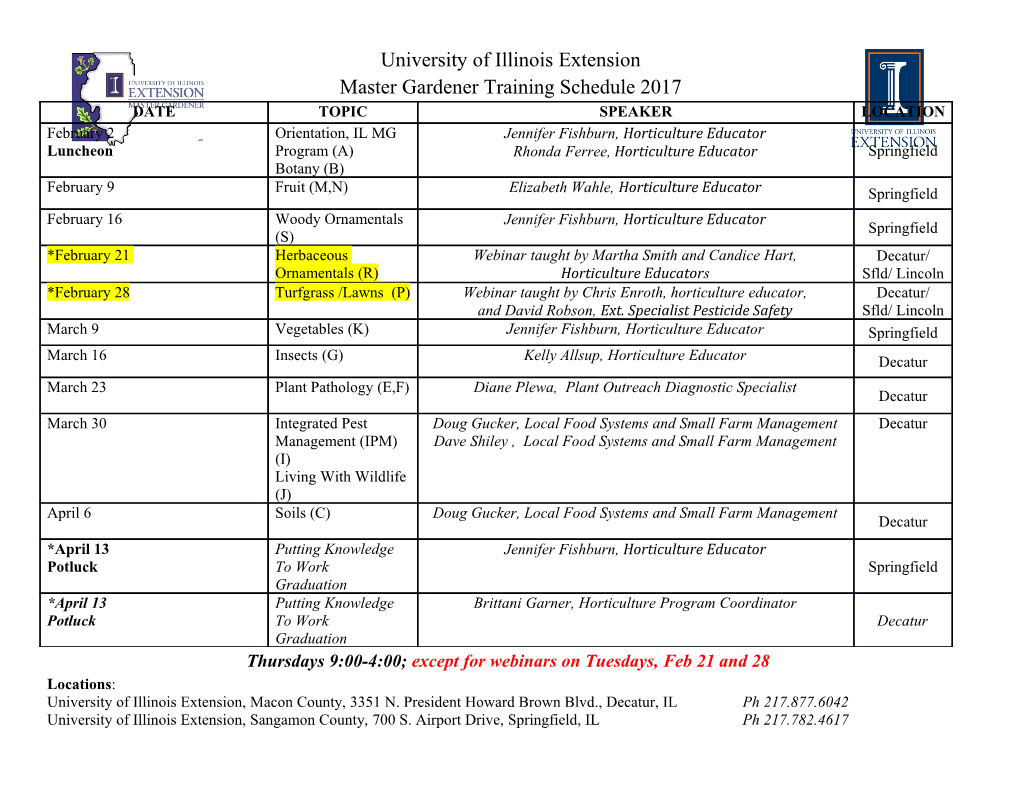
GAS TURBINE INLET AIR CHILLING FOR LNG John L. Forsyth, P.Eng. LNG Business Development Manager TAS Energy, Houston, Texas ABSTRACT It is well recognized that gas turbines used as compressor drivers in LNG liquefaction plants suffer from decreased power output as the ambient temperature increases. This fluctuation in driver output can result in reduced LNG production and process instability. An established technology in the power generation industry, gas turbine inlet air chilling (TIC) can allow the liquefaction compressor drivers to operate at near constant power output. This technology is widely accepted by gas turbine OEM's and has been proven safe and reliable in hundreds of installations worldwide. TIC can eliminate one aspect of the weather as a process variable in the liquefaction plant, and even allow a simpler approach to compressor selection. Unlike traditional evaporative cooling methods, TIC is not restricted to cooling the inlet air to the prevailing wet bulb temperature, and as such is ideal for inlet air cooling in the high humidity, coastal environments associated with LNG liquefaction plants. 1.0 INTRODUCTION Gas turbines, whether aeroderivative or heavy duty, are mass flow engines; that is, their power output is directly proportional to the mass flow of air through the turbine. For single-shaft heavy duty or frame gas turbines, the volumetric flow of air is constant making the air mass flow a function of air temperature. For multiple-shaft aeroderivative engines, the inlet air flow varies with compressor shaft speed. In both cases, the density of the air entering the compressor and therefore the air temperature plays a major role in determining the actual power produced by the engine. Since for most purposes, volumetric airflow through the gas turbine can be considered constant, increasing the density of this airflow can be used to increase the mass flow and therefore the power output. Inlet air cooling to increase and stabilize power output is a widely accepted technology in the power generation industry that has recently migrated to mechanical drive gas turbines used to drive compressors used in the LNG liquefaction process. This technology is broadly referred to as CTIAC (Combustion Turbine Inlet Air Cooling) or TIC (Turbine Inlet Chilling) specifically when the cooling is provided by a refrigeration cycle as described below. A typical chart showing shaft power for a GE LM6000 gas turbine is shown in Figure 1. As can be seen, the power vs. compressor inlet temperature curve approximates a straight line. This holds true for the vast majority of gas turbines, with the main difference being the slope of the line. For aeroderivative gas turbines the slope of the line tends to be steeper as these units exhibit a higher compression ratio. The chart also indicates gas turbine heat rate as a function of temperature. In general, operation at lower inlet air temperatures provides an improvement in heat rate, although this is generally not the primary objective in use of a CTIAC system. Depending on the system design and operating conditions, this improvement in heat rate will offset to varying extents the electrical power consumption of the CTIAC system. For heavy duty gas turbines, the slope is less steep as the compression ratio is lower – these units tend to have a higher ratio of airflow to power output. 1 Figure 1 – Performance of GE LM6000 Gas Turbine as a Function of Inlet Air Temperature CTIAC systems can be divided into two broad categories, depending on the process ultimately used to cool the air. 1) Evaporative Cooling 2) Turbine Inlet Chilling (TIC) using a refrigeration cycle 2.0 EVAPORATIVE COOLING PSYCHROMETRIC PROCESS Evaporative cooling takes advantage of the latent heat of vaporization of water which is evaporated in the airstream to be cooled. This process is often referred to as adiabatic cooling, since by definition an adiabatic process is one where heat is neither lost nor gained in the system. In this process, as water is evaporated in the airstream, the latent heat of vaporization of the water is provided by sensible heat from the air with the end result being a reduction in temperature of the air stream which is accompanied by an increase in relative humidity. These systems are typically divided into two categories, although thermodynamically they use the exact same process. Both methods attempt to maximize the air to water contact surface to maximize evaporation rates. 1) Media type evaporative coolers – These units will use a wetted media similar to cooling tower fill over which water is trickled down with the air flowing in a crossflow configuration 2) Inlet fogging systems – These systems use an array of hydraulic water atomizing nozzles mounted in the inlet airstream to produce fine droplets that are intended to evaporate quickly. 2 Figure 2 – Typical Evaporative Cooling Psychrometric Process Much has been written about the relative safety of evaporative cooling systems, in particular inlet fogging systems, which is not the intent of this paper. To concisely describe the performance of these systems, reference must be made to a psychrometric chart (Figure 2) that illustrates the adiabatic cooling process. In order to further describe the adiabatic cooling process, the concept of wet bulb temperature needs to be introduced. Wet bulb temperature of moist air is also referred to as adiabatic saturation temperature and can be most simply defined as the temperature which a quantity of air would theoretically reach if adiabatically cooled to saturation e.g. 100% relative humidity. By that very definition, the adiabatic cooling process is depicted in the psychrometric chart as moving along a line of constant wet bulb temperature towards the saturation curve. Reaching the prevailing wet bulb temperature is a theoretical low limit for evaporative cooling systems which is generally not achievable since the air/water contact surface and droplet residence times for evaporation in the case of fogging systems are insufficient to achieve this goal. Typical quoted effectiveness rates for such systems are in the range of 85%, i.e. they can achieve up to 85% of the available wet bulb depression, which is defined as the difference between prevailing dry bulb and wet bulb temperatures. Fogging system manufacturers will often quote higher effectiveness rates, although these are usually achieved through “overspray” i.e. spraying more water into the airstream than can possibly be evaporated. The reasoning behind this is that fogging nozzles do not produce droplets of uniform diameter, but rather a range of diameters. By overspraying, more of the smaller diameter droplets that evaporate quickly are introduced into the airstream, increasing system effectiveness. The excess water of course can follow one of two paths – lost to drain or ingested into the compressor where the larger droplets could cause potential erosion problems. In the example shown, air is cooled from an ambient condition of 33.3°C and 51.8 % R.H., which corresponds to 25.1°C WB, down to 26.3°C along a line that represents constant wet bulb temperature. The adiabatic cooling process from any other point on the chart would have to follow a similar process i.e. cooling along a line of constant wet bulb temperature, which will be parallel to the process line shown. 3 3.0 TIC SYSTEMS Turbine Inlet Chilling (TIC) systems can be defined as a subset of CTIAC systems in that they use a refrigeration cycle to cool the inlet air down to a desired temperature. The focus of this paper is on mechanical vapor compression refrigeration systems given their much higher popularity and reliability. Generally speaking, the refrigeration cycle is used to chill water, or an antifreeze solution such as water/propylene glycol which in turn is used to cool the air using finned tube heat exchangers (cooling coils) mounted in the air intake downstream of the filter. Although tempting and occasionally attempted, cooling the inlet air using direct expansion of refrigerant has multiple pitfalls which shouldn’t be disregarded. Two primary examples of these include: • Non-homogeneous inlet air temperature entering GT compressor – The air transit time from TIC cooling coil (heat exchanger) to compressor inlet in a gas turbine is typically less than 2 seconds. Direct expansion of refrigerant inside the cooling coil can lead to air temperature gradients across the large face area of the cooling coil. Given the limited transit time of this air, there is generally insufficient time for the air to mix and enter the GT compressor at a uniform temperature. Chilled water cooling coils tend to minimize this issue and provide a sufficiently uniform entering air temperature • Refrigerant leaks – TIC cooling coil modules inherently incorporate a system of condensate drain pans and piping to safely remove water that is condensed from the air stream. In the unlikely event of a water leak in a chilled water cooling coil, the condensate drain system would be expected to handle a reasonable amount of leakage which can be readily detected by monitoring makeup water into the chilled water closed loop. In a direct expansion type system, the gaseous refrigerant would be entrained in the airstream, ingested into the compressor and immediately thereafter into the combustor. Generally speaking, most refrigerants are not intended to be exposed to high temperatures such as those found in a GT combustor where the heat can cause them to break down and form harmful products of decomposition. One example of this is R717 (anhydrous ammonia) which decomposes into hydrogen and nitrogen gases when exposed to temperatures above 450°C. Synthetic refrigerants such as R134a or R123 may create decomposition products such as hydrochloric or hydrofluoric acid when exposed to high temperature. 3.1 Turbine Inlet Chilling Psychrometric Process As can be seen in the psychrometric chart of Figure 3, the TIC process is fundamentally different from evaporative cooling.
Details
-
File Typepdf
-
Upload Time-
-
Content LanguagesEnglish
-
Upload UserAnonymous/Not logged-in
-
File Pages16 Page
-
File Size-