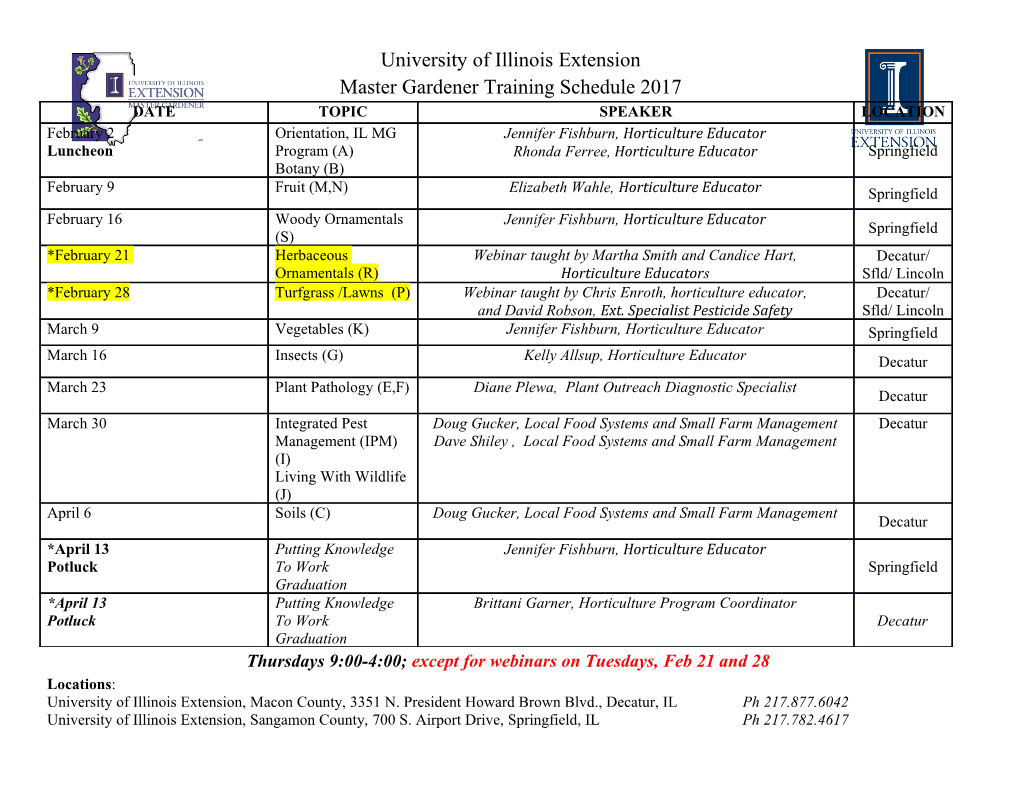
ACTA TEHNICA CORVINIENSIS – Bulletin of Engineering Tome VII [2014] Fascicule 1 [January – March] ISSN: 2067 – 3809 1. Zoran PANDILOV, 2. Vladimir DUKOVSKI COMPARISON OF THE CHARACTERISTICS BETWEEN SERIAL AND PARALLEL ROBOTS University “Sv. Kiriil I Metodij”, Faculty of Mechanical Engineering-Skopje, Karpos Ii B.B., P.O.Box 464, Mk-1000, Skopje, Republic of MACEDONIA Abstract: This paper gives survey of the position analysis, jacobian and singularity analysis, stiffness analysis, dynamics and applications of serial and parallel robots. Also a detailed comparison of the characteristics of serial and parallel robots and their advantages and disadvantages are presented. Keywords: serial robots, parallel robots, comparison INTRODUCTION - Introduction to robotics manufacturing implements through variable Robotics is a field of modern technology that programmed motions for the performance of crosses traditional engineering boundaries. specific manufacturing tasks. Understanding the complexity of robots and their The definition of a robot used by the Japanese applications requires knowledge of mechanical Industrial Robot Association widens these engineering, electrical engineering, systems and definitions in order to include arms controlled industrial engineering, computer science, directly by humans and also fixed sequence economics, and mathematics. manipulators which are not re-programmable. The term robot was first introduced into The key element in the above definitions is the re- vocabulary by the Czech playwright Karel Capek in programmability of robots. It is the computer his 1920 play Rossum’s Universal Robots, the brain that gives the robot its utility and word “robota” being the Czech word for work. adaptability. The so-called robotics revolution is, in Since then the term has been applied to a great fact, part of the larger computer revolution. Even variety of mechanical devices, such as this restricted version of a robot has several teleoperators, under-water vehicles, autonomous features that make it attractive in an industrial land rovers, etc. Virtually anything that operates environment. Among the advantages often cited in with some degree of autonomy, usually under favour of the introduction of robots are decreased computer control, has at some point been called a labour costs, increased precision and productivity, robot. increased flexibility compared with specialized There are many definitions for what a robot is and machines, and more humane working conditions as this often leads to discrepancies between statistics dull, repetitive, or hazardous jobs are performed by quoted about robots. An official definition for a robots. robot comes from the Robot Institute of America The robot, as it is defined, was born out with (RIA): A robot is a reprogrammable integration of two earlier technologies: multifunctional manipulator designed to move teleoperators and numerically controlled milling material, parts, tools, or specialized devices machines. Teleoperators, or master-slave devices, through variable programmed motions for the were developed during the Second World War to performance of a variety of tasks. handle radioactive materials. Computer numerical The commonly accepted definition in the UK is control (CNC) was developed because of the high that provided by the British Robot Association precision required in the machining of certain which is as follows: An industrial robot is a re- items, such as components of high performance programmable device designed to both manipulate aircrafts. and transport parts, tools, or specialised © copyright Faculty of Engineering - Hunedoara, University POLITEHNICA Timisoara ACTA TEHNICA CORVINIENSIS Fascicule 1 [January – March] – Bulletin of Engineering Tome VII [2014] The first robots essentially combined the we call a robot a general-purpose robot if it mechanical linkages of the teleoperator with the possesses 6 degrees of freedom, a redundant robot if autonomy and programmability of CNC machines. it possesses more than 6 degrees of freedom, and a The first successful applications of robot deficient robot if it possesses less than 6 degrees of manipulators generally involved some sort of freedom material transfer, such as injection moulding or Kinematic structure stamping, where the robot merely attends a press to Another classification of robots is according to unload and either transfer or stack the finished their structural topologies. A robot is said to be a parts. These first robots could be programmed to serial robot (fig.1.1 a) or serial (open-loop) execute a sequence of movements, such as moving manipulator if its kinematic structure takes the to a location A, closing a gripper, moving to a form of an open loop-chain, a parallel manipulator location B, etc., but had no external sensor (fig.1.1 b) if it is made of a closed-loop chain, and capability. More complex applications, such as hybrid manipulator if it is consists of both open- welding, grinding, deburring, and assembly and closed-loop chains. require not only more complex motion but also some form of external sensing such as vision, tactile, or force-sensing, due to the increased interaction of the robot with its environment. It should be pointed out that the important applications of robots are by no means limited to those industrial jobs where the robot is directly a) b) replacing a human worker. There are many other Figure 1.1 a) Serial robot (manipulator) b) parallel applications of robotics in areas where the use of manipulator humans is impractical or undesirable. Among these Drive technology are undersea and planetary exploration, satellite Typically, robots (manipulators) are electrically, retrieval and repair, the defusing of explosive hydraulically, or pneumatically driven. Most devices, and work in radioactive environments. robots use DC- or AC-servo motors or stepper Finally, prostheses, such as artificial limbs, are motors, because they are cleaner, cheaper, quieter themselves robotic devices requiring methods of and relatively easy to control. analysis and design similar to those of industrial Hydraulic drives have no rival in their speed of manipulators. response and torque producing capability. One modern robotics system usually consists of a Therefore hydraulic robots are used primarily for mechanical manipulator, an end-efector, a lifting heavy loads. The drawbacks of hydraulic microprocessor-based controller, a computer and robots are that they tend to leak hydraulic fluid, internal and external sensors/sensing devices require much more peripheral equipment (such as (contact or noncontact). pumps, which require more maintenance), and Classification of robots (robotic they are noisy. Pneumatic robots are inexpensive manipulators) and simple but cannot be controlled precisely, Robots can be classified according various criteria, because air is a compressible fluid. As a result, such as degrees of freedom, kinematic structure, pneumatic robots are limited in their range of drive technology, workspace geometry, motion applications and popularity. characteristics, control. Workspace geometry Degrees of freedom The workspace of a manipulator is defined as the One obvious classification scheme is to categorize volume of space the end effector can reach. A robots according to their degrees of freedom. In reachable workspace is the volume of space within ideal case, a manipulator should posses 6 degrees of which every point can be reached by the end freedom in order to manipulate an object freely in effector in at least one orientation. A dextrous three-dimensional space. From this point of view, workspace is the volume of space within which | 144 | ACTA TEHNICA CORVINIENSIS Fascicule 1 [January – March] – Bulletin of Engineering Tome VII [2014] every point can be reached by the end effector in all least one of the moving links in the mechanism possible orientations. Dextrous workspace is a possesses a general spatial motion (fig.1.1 b). subset of the reachable workspace. a) b) Figure 1.4 a) Planar parallel manipulator) b) spherical parallel manipulator Control Robots are classified by control method into servo and non-servo robots. The earliest robots were non-servo robots. These Figure 1.2 Five most common types robots are essentially open-loop devices whose of robots geometry [5] movement is limited to predetermined mechanical Most industrial robots (manipulators) at the present stops, and they are useful primarily for materials time have six or fewer degrees-of-freedom. These transfer. In fact, according to the definition given robots are usually classified kinematically on the previously, fixed stop robots can hardly qualify as basis of the first three joints of the arm (R-revolute robots. or P-prismatic) used for manipulating the position, Servo robots use closed-loop computer control to while the rest of joints associated with the wrist are determine their motion and are thus capable of for controlling the orientation. being truly multifunctional, reprogrammable The majority of these robots (manipulatators) fall devices. Servo controlled robots are further into one of five geometric types: Cartesian (PPP), classified according to the method that the cylindrical (RPP), spherical (RRP), SCARA controller uses to guide the end-effector. The (selective compliance assembly robot arm) (RRP), simplest type of robot in this class is the point-to- articulated (RRR) (fig.1.2). Each of these five point robot. A point-to-point robot can be taught manipulator arms are serial link robots. A sixth distinct
Details
-
File Typepdf
-
Upload Time-
-
Content LanguagesEnglish
-
Upload UserAnonymous/Not logged-in
-
File Pages18 Page
-
File Size-