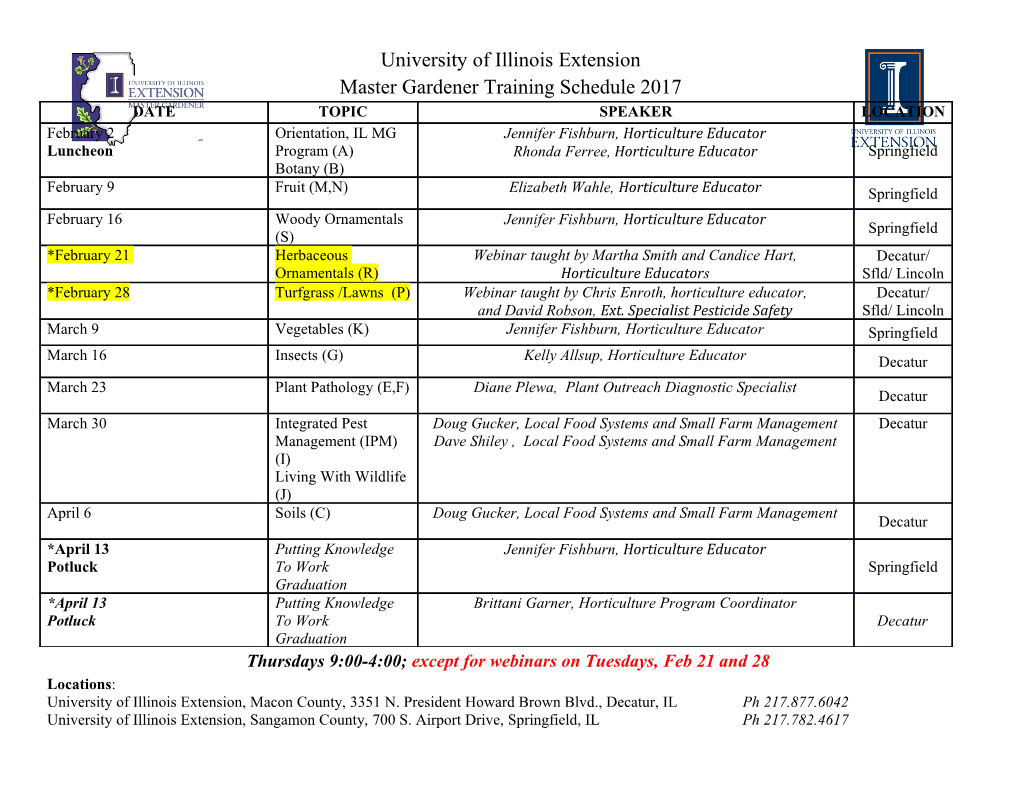
University of Nevada, Reno Computational Investigation of Cavitation Performance and Heat Transfer in Cryogenic Centrifugal Pumps with Helical Inducers A dissertation submitted in partial fulfillment of the requirements for the degree of Doctor of Philosophy in Mechanical Engineering by Enver Sinan Karakas Dr. Cahit A. Evrensel/Dissertation Advisor May, 2019 THE GRADUATE SCHOOL We recommend that the dissertation prepared under our supervision by Entitled be accepted in partial fulfillment of the requirements for the degree of , Advisor , Committee Member , Comm ittee Member , Committee Member , Graduate School Representative David W. Zeh, Ph.D., Dean, Graduate School i i. ABSTRACT In this dissertation, heat transfer and cooling mechanism of a cryogenic submerged pump motor, and cavitation behavior of a cryogenic pump are investigated. Cryogenic pumps for Liquefied Natural Gas (LNG) applications are unique in design with respect other industrial pump applications. The two distinct features of the cryogenic pumps are: (1) pump motor is submerged to process liquid for improved cooling, and (2) a helical style inducer is utilized at the suction side of the pump to enhance the cavitation performance. The first part of this dissertation investigates the cooling of the submerged induction motor considering normal operating conditions of a typical cryogenic pump to understand the effect of the motor rotor geometry. In this effort, the flow structure across the motor annulus, which is commonly known as “motor air gap”, is investigated in the presence of realistic rotor geometries commonly found in practical applications. The purpose of this study is to observe and understand the fluid dynamics of Taylor-Couette-Poiseuille (TCP) flow and its significance to the cooling performance of the submerged motor, considering various configurations of the rotor surface. Computational Fluid Dynamics (CFD) simulations are conducted to determine the flow characteristic across the “motor air gap” and temperature distribution at the stator section of the motor. CFD simulations results are compared to temperature and flow calculations according to previously published TCP flow equations and dimensionless correlations. The entrance region is explored for each rotor geometry and its impact to overall cooling performance is discussed. It is concluded that while the rotor surface has modest effect to heat transfer, TCP flow characteristics differ for each geometric configuration. In addition, TCP flow and heat transfer ii correlations can predict the temperature profile, if the similarity between dimensionless parameters are obtained. In the second part of this dissertation, the cavitation performance of the cryogenic pump in terms of Net Positive Suction Head (NPSH) is investigated considering two different style helical inducers. The inducers utilized in cryogenic industrial pumps have open shroud design with a constant tip diameter. Due to the open shroud design, inducers tip clearance has an important role in cavitation performance due to possible back leakage through the gap. The effect of the tip clearance is investigated to understand the flow structure at the inducer tip location and its impact to cavitation performance. A constant pitch inducer and a variable pitch inducer are considered in the study of the tip clearance effect. CFD simulations are performed for various tip clearances. CFD simulation results are compared to actual test data to validate the simulation predictions. The objective of this research is not only to determine the tip clearance effect to the cavitation performance, but also to understand how the tip clearance can change the cavitation performance of different style inducers. A transport-equation based cavitation model based on Rayleigh-Plesset’s bubble dynamics is implemented in the CFD code to explore the bubble dynamics and cavitation at the inducer and impeller eye sections. It is concluded that tip clearance plays an important role in cavitation performance and sensitivity to tip clearance in terms of cavitation performance is different for each style inducer. The third and last part of this dissertation is concerned with the review of four commonly used transport-equation based cavitation models. Comparison of these models and assessment of their applicability to predict cavitation performance of a cryogenic iii industrial pump with a variable pitch helical inducer are discussed in detail. To this aim, experimental results are compared to simulation findings to validate accuracy and assumptions of each model. Lastly, modifications to original empirical constants are proposed to obtain agreement with the actual cavitation and bubble dynamics observed during experimental testing. Two new sets of empirical constants are proposed to improve the prediction of cavitation in cryogenic pumps. Results show that with the new empirical constants, cavitation performance of a cryogenic pump with a helical inducer can be determined. It is shown that including the concentration of undissolved non-condensable gases and the turbulent pressure fluctuations in the models had no impact to the cavitation performance for this particular case. iv ii. ACKNOWLEDGMENTS I would like to thank my family members for their great support. I feel grateful to have such an understanding and supportive family. Especially, my wife, Beril Karakas, has been very caring and kind from the beginning to the end of this journey. My parents and my only sister have given me strength to pursue my degree. I would also like to thank my advisor and committee members. Especially, Dr. Aureli has been extraordinarily supportive, and assisted in every matter and helped me in my advancement. I would have not succeeded and finished my degree without the support and assistance of my advisor and committee members. I want to thank all of my friends and colleagues at Turbomachinery Laboratory, who have helped me during this study. I would especially like to thank Dr. Tokgoz and Burak Gulsacan for their contributions and sharing their ideas in this project. Finally, I would like to thank Elliott Group – Cryodynamics Products and Ebara Corporation, Japan for funding this research. v Table of Contents i. ABSTRACT ............................................................................................................................. i ii. ACKNOWLEDGMENTS .................................................................................................... iv List of Tables ................................................................................................................................ vii List of Figures .............................................................................................................................. viii CHAPTER 1. INTRODUCTION: ................................................................................................ 1 CHAPTER 2. FLOW AND HEAT TRANSFER THROUGH THE AIR GAP OF A SUBMERGED MOTOR PUMP: EFFECT OF GROOVES AT THE ROTOR SURFACE .. 9 Abstract ....................................................................................................................................... 9 1. Introduction ...................................................................................................................... 10 2. Problem Statement ........................................................................................................... 18 2.1 Induction Motor Configurations and Cooling Mechanism .................................. 18 2.2 Formulation of the Cooling Mechanism ................................................................ 19 2.3 Flow Structure and Convective Heat Transfer: .................................................... 22 2.4 Correlation and Formulation of Heat Transfer Coefficient: ............................... 25 3. CFD Analyses and Results .............................................................................................. 29 4. Conclusions ....................................................................................................................... 43 5. Acknowledgment .............................................................................................................. 45 References ................................................................................................................................. 45 CHAPTER 3. CAVITATION PERFORMANCE OF CONSTANT AND VARIABLE PITCH HELICAL INDUCERS FOR CENTRIFUGAL PUMPS: EFFECT OF INDUCER TIP CLEARANCE....................................................................................................................... 51 Abstract ..................................................................................................................................... 51 1. Introduction ...................................................................................................................... 52 2. Pump and Inducer Specifications ................................................................................... 58 3. Numerical Simulation ...................................................................................................... 60 3.1 Computational Fluid Dynamics (CFD) .................................................................. 61 3.2 Cavitation Parameters ............................................................................................. 62 3.3 Cavitation Model ...................................................................................................... 63 3.4 Geometric
Details
-
File Typepdf
-
Upload Time-
-
Content LanguagesEnglish
-
Upload UserAnonymous/Not logged-in
-
File Pages160 Page
-
File Size-