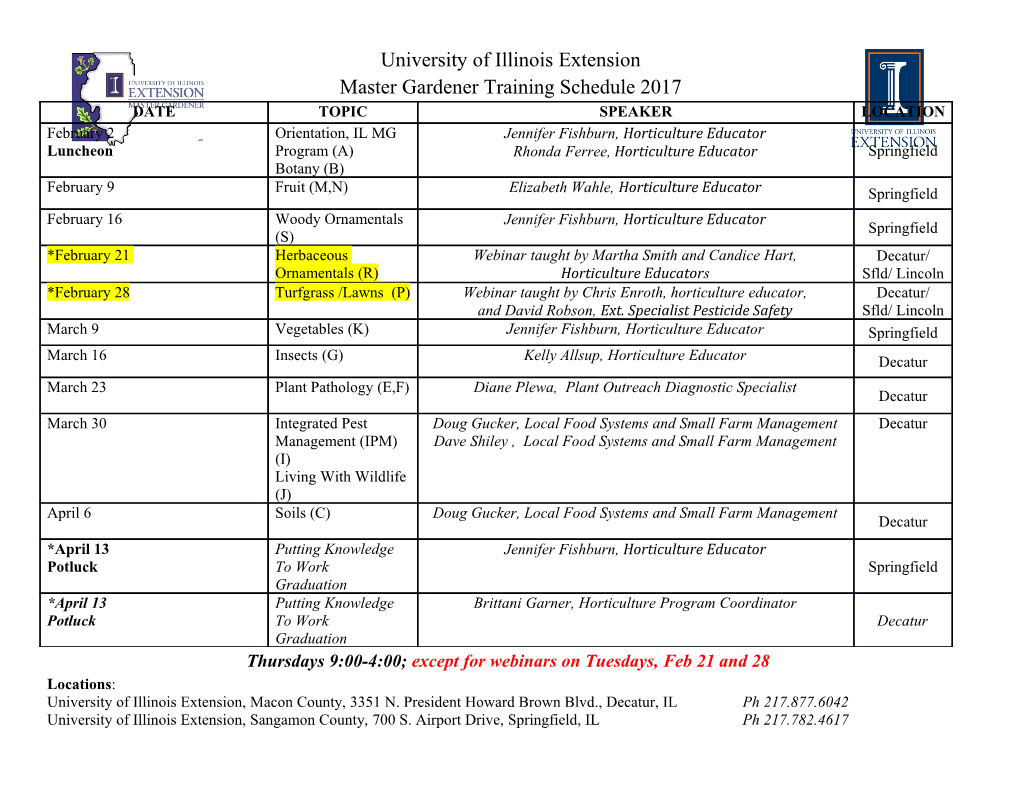
A survey of automatic control methods for liquid-propellant rocket engines Sergio Pérez-Roca, Julien Marzat, Hélène Piet-Lahanier, Nicolas Langlois, Francois Farago, Marco Galeotta, Serge Le Gonidec To cite this version: Sergio Pérez-Roca, Julien Marzat, Hélène Piet-Lahanier, Nicolas Langlois, Francois Farago, et al.. A survey of automatic control methods for liquid-propellant rocket engines. Progress in Aerospace Sciences, Elsevier, 2019, pp.1-22. 10.1016/j.paerosci.2019.03.002. hal-02097829 HAL Id: hal-02097829 https://hal.archives-ouvertes.fr/hal-02097829 Submitted on 12 Apr 2019 HAL is a multi-disciplinary open access L’archive ouverte pluridisciplinaire HAL, est archive for the deposit and dissemination of sci- destinée au dépôt et à la diffusion de documents entific research documents, whether they are pub- scientifiques de niveau recherche, publiés ou non, lished or not. The documents may come from émanant des établissements d’enseignement et de teaching and research institutions in France or recherche français ou étrangers, des laboratoires abroad, or from public or private research centers. publics ou privés. A survey of automatic control methods for liquid-propellant rocket engines Sergio Perez-Roca´ a,c,∗, Julien Marzata,Hel´ ene` Piet-Lahaniera, Nicolas Langloisb, Franc¸ois Faragoc, Marco Galeottac, Serge Le Gonidecd aDTIS, ONERA, Universit´eParis-Saclay, Chemin de la Huniere, 91123 Palaiseau, France bNormandie Universit´e,UNIROUEN, ESIGELEC, IRSEEM, Rouen, France cCNES - Direction des Lanceurs, 52 Rue Jacques Hillairet, 75612 Paris, France dArianeGroup SAS, Forˆetde Vernon, 27208 Vernon, France Abstract The main purpose of this survey paper is to review the field of convergence between the liquid-propellant rocket- propulsion and automatic-control disciplines. A comprehensive collection of academic works and some industrial developments are summarised and discussed, making the link to the current context of launcher reusability. The main control problem in liquid-propellant rocket engines (LPRE), the target of this survey, generally consists in tracking set-points in combustion-chamber pressure and mixture ratio, their main operating quantities. This goal is attained via the adjustment of flow-control valves while complying with operating constraints. Each aspect of control systems, ranging from modelling to the actual control techniques, is reviewed and subsequently related to the rest of aspects. The comparison of the different approaches points to the general use of linearised models about concrete operating points for deriving steady-state controllers, which in most cases are of PID type. Other more sophisticated approaches present in the literature, incorporating some nonlinear, hybrid or robust techniques, improve certain aspects of performance and robustness. Nevertheless, no fully nonlinear or hybrid frameworks, which may allow the control of a wider throttling domain, have been published. In addition, control during the thermally and structurally demanding transient phases is usually in open loop, and hence with low correction margins. This sort of control enhancements, probably together with more sophisticated monitoring architectures, would serve to extend the life of LPRE, a significant factor in their reusability. Therefore, this survey intends to draw a path for the future control design trends which will certainly be more suitable for reusable LPRE. Keywords: Liquid-propellant rocket engines, automatic control, thermodynamic systems, reusability, modelling, review. 1. Introduction since rocket engines are complex two-sided technologi- cal assets (with military and civil uses), generally need- The automatic control of liquid-propellant rocket ing wide technical know-how. But it could also mean propulsion systems is a specific field that presents mul- that this bi-disciplinary topic has not been extensively tiple goals and constraints and that in practical terms tackled by the research community. Hence, the ex- tends to be simplified for adapting to the restrictive real pected benefits of this article are two-fold. On the one space-engineering scenarios. hand, it is intended to provide the designers of liquid- Even if the first reference reviewed dates from the propellant rocket engines (LPRE) with possibilities to 1950s, a relatively low number of publications cover- enhance their control systems, seeing the current evolv- ing both disciplines at the same time can be found in ing context of reusable launchers. On the other hand, the literature. This fact might stem from intentional the automatic-control community may find challenging confidentiality strategies by companies and agencies, cutting-edge applications of their control techniques. Therefore, background introductions on each field are provided throughout the article. ∗Corresponding author. The automatic control of any type of system generally Phone: +33180386657 Email address: [email protected] (Sergio pursues that the system behaves as expected, according Perez-Roca)´ to some predefined references. In the case of LPRE, Postprint accepted in Progress in Aerospace Sciences April 2, 2019 Nomenclature e Subscript for nozzle exit HMS Health Monitoring System t Subscript for throat HPT High-Pressure Turbine m˙ Mass flow [kg=s] ICS Intelligent Control System γ Specific heat ratio [-] JAXA Japanese Aerospace Exploration Agency ! Rotational speed [rad=s] LCH4 Liquid Methane Φ Heat transfer [W] LEC Life-Extending Control ρ Density [kg=m3] LFT Linear Fractional Transformation c Subscript for cavity/combustion/chamber LH2 Liquid Hydrogen A Area [m2] LMI Linear Matrix Inequality A; B; C; D Standard state-space matrices LOX Liquid Oxygen C∗ Characteristic exhaust speed [m=s] LPRE Liquid-Propellant Rocket Engine F Thrust [N] LPV Linear Parameter-Varying 2 g0 Standard gravity acceleration [m=s ] LQG/LTR Linear Quadratic Gaussian/Loop Transfer- H Enthalpy [J=kg] function Recovery Isp Specific impulse [s] LQR Linear-quadratic regulator 2 ITP Shaft inertia [kg · m =s] LS Least Squares kres Component’s resistance coefficient [1=(kgm)] LVDT Linear Variable Differential Transformer L Length [m] // Liquid MBFD Model-based fault detection M Molecular weight [kg=mol] MFV Main Fuel Valve MR Mixture ratio [-] MIMO Multi-Input Multi-Output p Pressure [Pa; bar] MOV Main Oxidiser Valve R Gas constant [J=kgK] MPC Model Predictive Control s Laplace variable NASA National Aeronautics and Space Administration T Temperature [K] NLP Nonlinear Programming t Time [s] O, ox Oxidiser Tq Torque [Nm] ODE Ordinary Differential Equations u Control input [m=s] OL Open Loop V Volume [m3] OPOV Oxidiser Preburner Oxidiser Valve x State vector PI Proportional-Integrator Controller y Output vector PID Proportional-Integrator-Derivative Controller H1 H infinity norm for robust control PLC Programmable Logic Controller ACC Active Combustion Control PRBS Pseudorandom Binary Sequence CC, C Combustion chamber PWM Pulse-Width Modulation CL Closed Loop RC Reconfigurable Control CNES Centre National d’Etudes´ Spatiales RML Recursive Maximum Likelihood DF Describing functions RREC Robust Rocket Engine Concept ESA European Space Agency RTD Resistance Temperature Devices F, fu Fuel RVDT Rotary Variable Differential Transformer FDD Fault Detection and Diagnosis SISO Single-Input Single-Output FDI Fault Detection and Isolation SQP Sequential Quadratic Programming FPOV Fuel Preburner Oxidiser Valve SSME Space Shuttle Main Engine FTCS Fault-tolerant Control Systems TCV Thrust Control Valve GG, G Gas generator TP Turbopump HIL Hardware in the Loop TVC Thrust-Vector Control 2 the system studied in this paper, these references gener- constant of the mixture, g0 is the standard gravity accel- ally correspond to the two variables defining its operat- eration, pe is the exhaust pressure, CF is the thrust co- ing envelope: combustion-chamber pressure (related to efficient and Isp is the specific impulse. The latter is the thrust) and mixture ratio (oxidiser to fuel ratio), which ratio of thrust to ejected mass flow, and hence represents are usually controlled via adjustable valves. In order the efficiency of the engine. Mixture ratio (MR), defined to explain the physical meaning of these variables and as the ratio between oxidiser and fuel mass flows, has an components, an introduction to the working principles influence on the previous formulae via Tc and thermo- of rocket engines seems necessary. dynamic properties like γ and R. Several types of LPRE cycles have been conceived re- 1.1. Rocket engine generalities garding the manner in which propellants are fed to the main thrust chamber (compound of combustion cham- Chemical rocket engines, mainly used to propel ber and convergent-divergent nozzle), but the main ele- launch vehicles and spacecraft, can be classified in the ments in a LPRE cycle remain the same: first place according to the state in which the chemi- cal propellant is stored: i.e. solid-propellant, liquid- • Propellant tanks: cryogenic or not (low tempera- propellant and hybrid (mixture of both) engines. In- tures preferred for low-density propellants such as deed, propellants nature determines to a great extent the hydrogen). conception of these systems. The chemical compounds • Pipe lines: ducts joining the different elements. furnished to the rocket engine undergo several thermo- dynamic transformations throughout their flow through • Valves: control components guiding and/or regu- the engine lines and components. The main phenomena lating propellants flow through the system. They are their combustion and expansion,
Details
-
File Typepdf
-
Upload Time-
-
Content LanguagesEnglish
-
Upload UserAnonymous/Not logged-in
-
File Pages34 Page
-
File Size-