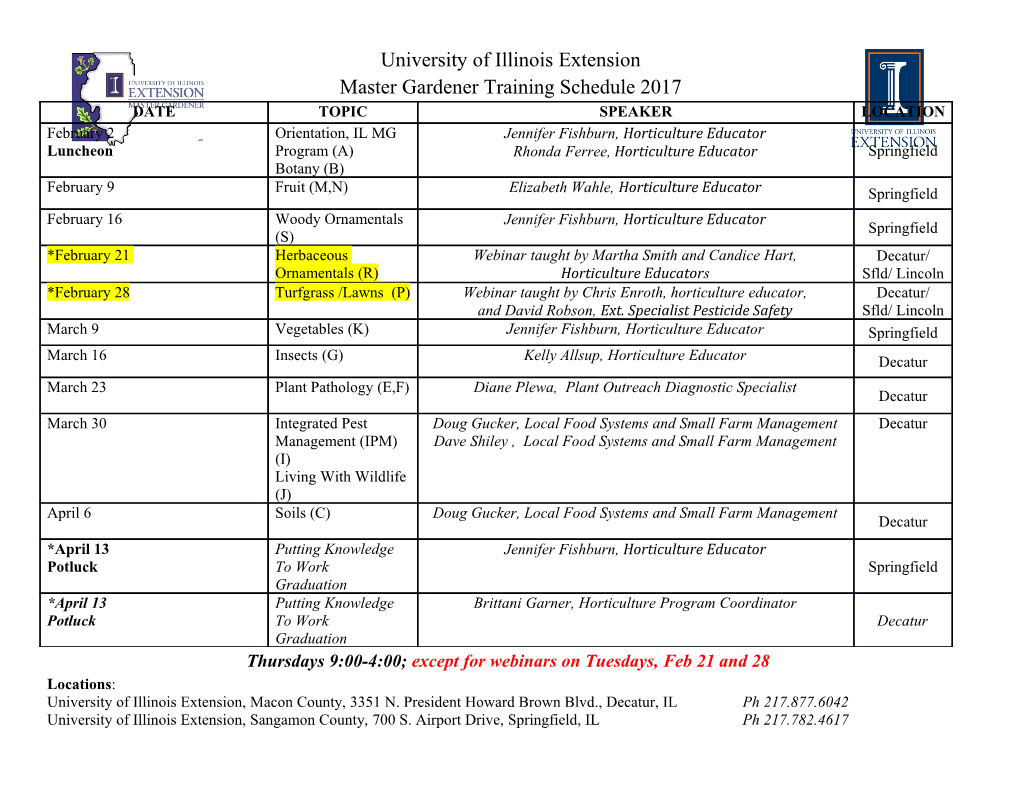
THE b a c k - e n d PROCESS Wire Bonding Considerations Design Tips for Performance and Reliability BY VIVEK DIXIT, PH.D., HEIDI DAVIS, PH.D., AND MEL CLARK, Maxtek Components Corp. ire bonding ranks among Wire-bond Connections popular and dominant Avoid chip-to-chip connec- W interconnect technolo- tions – Unless electrical per- gies due to its reputation for versatili- formance demands it, wire ty, performance, and reliability. Wire- bonding directly between bond types can be described either by ICs should be avoided. Cre- the mechanism for creating the wire ating the stitch bond trans- bond or the type of bond. Wire-bond mits mechanical energy to mechanisms offer three different the pad, which could lead to methods for imparting the requisite micro-cracking in, or under, energy to attach a wire to the bond the pad metallization. Mi- site: thermocompression, ultrasonic, cro-cracks represent a po- FIGURE 1. Top row (l-r) – Examples of typical ball, stitch, and thermosonic. Two types of bond and wedge bonds formed using 0.001-in. Au wire. tential reliability risk; there- methods exist: the ball-stitch and the Bottom row (l-r) – examples of typical failures, including fore, intermediate bond pads wedge bonds (Table 1). cratering, poor heel stick, and heel cracking. should be designed into the substrate. Ball-stitch Bonding Don’t cross wires – Bond wires should not cross over one In ball bonding, a capacitive discharge spark melts the tip another, other die, or bond pads (Figure 3). Under external of the wire and the surface tension of the molten gold forms mechanical stresses, the unsupported loop of the wire bond the ball. This is called the “flame-off” process. The ball is could droop and contact a wire directly under it, leading to then placed at the target bond site, and ultrasonic energy a short circuit. transmitted by the capillary scrubs the pad surface, creating Remember: bond pads do matter – Bond pads should be po- a metallurgical bond between the ball and pad. In this type sitioned to create the shortest bond wire possible (within pro- of bonding, the capillary does not contact the pad surface. vided design rules). The length of the wire bond determines For the second half of the bond, the capillary is moved to the the total impedance, capacitance, and inductance of the con- location for the stitch bond. Here, the capillary rests against nection. Long wire bonds can be detrimental to the overall the pad surface and ultrasonic energy forms the stitch and package performance. cuts the wire (Figure 1). The entire sequence of ball- Bond Bonding Wire Temperature Ultrasonic Pressure stitch bonding is shown in Figure 2. Type Mechanism Ball Thermosonic Au Elevated Yes Low Wedge Bonding Wedge Thermosonic Au Elevated Yes Low In wedge bonding, a stub of wire is pressed against Wedge Ultrasonic Al Ambient Yes Low the bond pad by the foot of the capillary, applying ultrasonic energy to form the bond between the Ball Thermo- Au Elevated No High compression wire and bond pad. The capillary is then moved to Comparison of wire-bonding methods by bond type. the second bond location and the process is repeat- TABLE 1. ed. Once the second bond is completed, the wire is clamped All substrate bond pads should be gold-plated to a min- and snapped above the second bond. imum thickness of 0.76 µm, otherwise the mechanical en- The following guidelines are recommended when plan- ergy of the scrubbing process can result in the wire pen- ning for the use of wire bonds in a package design. etrating the pad and damaging underlying structures. Reprinted with revisions to format, from the July 2006 edition of ADVANCED PACKAGING Copyright 2006 byPennWell Corporation THE b a c k - e n d PROCESS Stitch completed. Selecting the Wire relative to other components — a con- Clamp closes. The choice of wire diam- sideration that will increase as pack- Capillary moves up. Wire breaks. eter depends on the wire age sizes decrease and layout densities bond pitch, current car- increase. When wire bonds are to be Capillary moves to next bond. Clamp opens. rying capacity, and cost. placed in close proximity to tall com- 1-mil diameter gold wire ponents, clearance (X) required by the Wire feeds through. is a common choice, and bonding tool and tolerances for both EFO spark at wire tip. has a resistance of 1.17 die placement and bond accuracy must mΩ per mil of length, be considered. Figure 4 illustrates a sit- Ball forms at wire tip. and a burn-out current of uation when a 0.01-in. capillary tip is Capillary moves down. approximately 0.7 Å, de- used for ball-stitch bonding and a rea- Ball contacts pad. pending on wire length, sonable value of X is 0.01 in. > ¼ of the Ultrasonic energy at ball to heatsinking, etc. Typical component height (B2). form bond. inductance attributable to In a stitch bond, the actual bond area Capillary moves over and a 1-mil bond wire is 25 pH is offset from the capillary centerline. down to stitch area to form per mil length, but varies Therefore, clearance must include addi- bond. Capillary contacts pad. Ultrasonic energy to depending upon bond tional tolerance, equal to half the cap- form stitch. wire height. Aluminum illary tip diameter to ensure proper wire is almost exclusive- clearance. Thus, for a 0.01-in. tip cap- Back to Step 1. ly used in wedge-bonding illary, Y should be 0.005 in. > X. FIGURE 2. Schematic sequence of ball-stitch wire bonding. applications, because the Another solution is to use wedge 0607apbepf2 Using flash gold with Al or Au wedge bonding is an exception. However, it is D best to check the application notes for A B C the IC, since some IC manufacturers do not support wedge bonding due to A the force applied to the die during the C process. Poor bonding practice Good bonding practice A minimum of 0.005 mm is required between the edge of a bond pad and a via. A Die-to-die bonds C Extra pad to avoid die-to-die bonds Bonding too close to a discontinuity in B Crossed wire bonds D Rearrange pads to avoid crossed wire bonds the substrate can lead to material dam- FIGURE 3. General guidelines for wire bond pad locations. age from mechanical energy transmitted to the substrate while bonding. high propensity of Al to oxidize requires bonding, in which the bonding tool When wire bonding on multi-layer sub- ball bonding with Al wires to be performed has a vertical front face. Unfortunate- strates, wire-bond pads should be a mini- in an inert atmosphere. ly, as a semi-automatic process, wedge bonding is slower—and therefore more costly—than ball-stitch bonding. 0607apbepf3 Bond Placement – Lids and Glob-top Figure 4 shows the requirements for 0.025 in. 0.025 in. wire-bond placement in proximity to lid-attach locations and glob-top dam and fill. The placement requirements 0.020 in. account for the tolerances in lid dimen- B1 15° sions and placement accuracy. In the Y WB B2 X case of glob-top dam and fill, the place- 0.050 in. ment is dictated by the amount of set- FIGURE 4. Bottom left - Calculating bond / component spacing in a stitch bond situation. tling in the glob-top dam material dur- Top row / bottom right - typical location of wire bonds with respect to lid and glob-top dam ing curing. and fill placements. Pad Sizing and Spacing mum of 10 mm from the edge of adjacent Bond Placement Table 2 provides guidelines for design- conductors to allow for registration, print- In the package design process, it is im- ing pads on the substrate and specify- ing, and wire bonding tolerances. portant to consider bond placement ing pad sizes on die. The dimensions 0607apbepf4 THE b a c k - e n d PROCESS Description of Spacing Typical Values: Typical Values: identifies damaged wire bonds, misplaced or lifted bonds, 0.001-in. Wire 0.0007-in. Wire and bonds that might be shorting against other bonds or Wire length, minimum 0.040 in. 0.030 in. components. Ball-shear testing determines wire bond-to- Wire length, maximum 0.100 in. 0.075 in. pad adhesion. Loop height clearance above die 0.015 in. 0.015 in. Wire-bond reliability is usually tested by subjecting bond- ed parts to standard mechanical shock and vibration tests, Die pad: min. available circle (ball) 0.004 in. 0.003 in. temperature cycling or shock, and damp heat. Wire-bond Die pad: min. available circle (wedge) 0.0025 in. 0.002 in. stability is evaluated by comparing the destructive pull test Substrate pad: 1 bond 0.010 × 0.008 in. 0.010 × 0.008 in. of the wire bonds after reliability testing against a control Substrate pad: 2 bonds 0.010 × 0.010 in. 0.010 × 0.010 in. sample. Die 0.003 in. 0.003 in. Conclusion TABLE 2. Typical substrate and IC pad dimensions. With due care, wire bonding can be accomplished on a vari- pertain to ball and wedge bonding and to PCB and ceramic ety of substrates, ranging from PCBs to multi-layer and thick- substrates. Exceptions are noted as applicable. film ceramics to flexible circuits. While other technologies like flip chip may allow for reduction in overall package di- Failure Mechanisms & Evaluation Methods Common defects or failures that can occur in wire bonds fall 1 1 Wire break at neckdown point under three categories based on the underlying cause.
Details
-
File Typepdf
-
Upload Time-
-
Content LanguagesEnglish
-
Upload UserAnonymous/Not logged-in
-
File Pages4 Page
-
File Size-