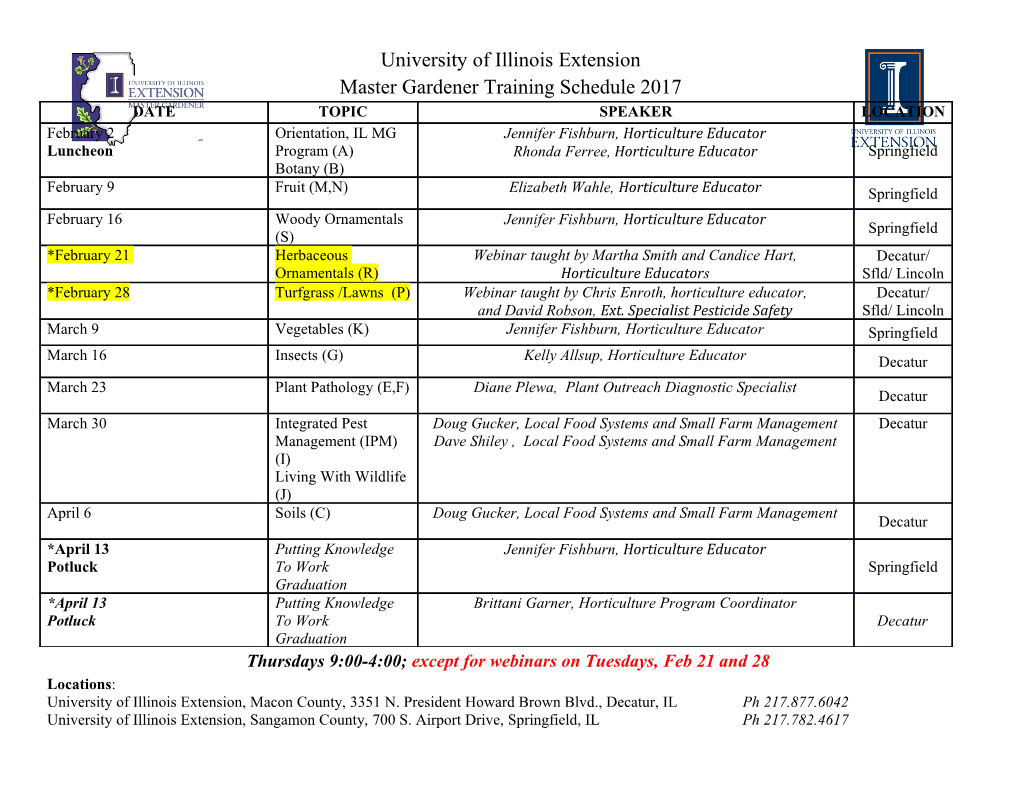
NUMERICAL AND EXPERIMENTAL STUDY ON DYNAMICS OF UNSTEADY PIPE FLOW INVOLVING BACKFLOW PREVENTION ASSEMBLIES by HYOUNG-JIN KIM A Dissertation Presented to the FACULTY OF THE USC GRADUATE SCHOOL UNIVERSITY OF SOUTHERN CALIFORNIA In Partial Fulfillment of the Requirements for the Degree DOCTOR OF PHILOSOPHY (CIVIL ENGINEERING) December 2012 Copyright 2012 HYOUNG-JIN KIM UMI Number: 3551503 All rights reserved INFORMATION TO ALL USERS The quality of this reproduction is dependent upon the quality of the copy submitted. In the unlikely event that the author did not send a complete manuscript and there are missing pages, these will be noted. Also, if material had to be removed, a note will indicate the deletion. UMI 3551503 Published by ProQuest LLC (2013). Copyright in the Dissertation held by the Author. Microform Edition © ProQuest LLC. All rights reserved. This work is protected against unauthorized copying under Title 17, United States Code ProQuest LLC. 789 East Eisenhower Parkway P.O. Box 1346 Ann Arbor, MI 48106 - 1346 Acknowledgements First, I would like to thank my advisor, Dr. Jiin-Jen Lee, for his continuous supports and efforts during my academic years at University of Southern California. Whenever I doubt myself, he was there encouraging me not to loose goals academically and personally. I have learned from him how to look a problem in a big picture, how to solve it efficiently, and how to express an idea in an effective manner. I also would like thank the staff members (at the Foundation of cross connection con- trol and hydraulic research) for giving the opportunity for testing utilities and providing the valuable information of testing equipments and experimental data. A special thank to my dad for his unconditional support and trust with his generous mind. Without him, nothing would have be possible for my life. Last, but not least, I would like to thank my beloved family, Jungwan, Noah, and Sarah who have endured suffering with patience and faith over last years of study. ii Contents Acknowledgements ii List of Tables vi List of Figures vii Abstract xi Chapter 1 Introduction 1 1.1 Background . 1 1.2 Literature Review . 5 1.2.1 Fundamental Partial Differential Equations . 6 1.2.2 Classic Water Hammer Theory . 6 1.2.3 Friction Models Used In Calculation . 11 1.2.4 Dynamics Involving Backflow Prevention Assemblies . 14 1.3 Objective and Scope of Present Study . 16 iii Chapter 2 Water Hammer Equations 17 2.1 Differential Equations For Unsteady Flow . 17 2.1.1 Continuity Equation . 17 2.1.2 Momentum Equation . 18 2.1.3 Moment-of-Momentum Equation of a Valve Disk . 18 Chapter 3 Method of Characteristics 24 3.1 Solution by Method Of Characteristics . 24 3.2 Boundary Conditions . 28 3.2.1 Constant-Level Upstream Reservoir . 28 3.2.2 Series Junction . 29 3.2.3 Valve At Downstream End . 30 3.2.4 Backflow Prevention Assembly . 30 3.3 Coupling Modeling . 32 Chapter 4 Experiments 34 4.1 Experimental Setup . 35 4.2 Case 1: Without a Backflow Prevention Assembly . 37 4.3 Case 2: With A Backflow Prevention Assembly . 43 4.4 Comparison of Measured Data Between Case 1 and Case 2 . 49 iv Chapter 5 Simulation Results and Discussion 53 5.1 Selection of FT and k2 ............................. 53 5.2 Verification of Models: Case 1 . 54 5.3 Implementation of A Coupling Model: Case 2 . 63 5.3.1 Sensitivity of k2 ............................ 64 5.3.2 Classification of Assemblies: Ideal, Undamped, And Damped . 79 Chapter 6 Conclusion And Recommendation 81 6.1 Summary and Conclusion . 81 6.2 Recommendation . 86 Bibliography 87 v List of Tables 4.1 Physical Properties Of System . 37 4.2 Summary of Flow Conditions For Cases . 44 4.3 Summary of Pressure Reduction Rates by Backflow Preventer . 52 5.1 Input Parameters Used In Simulation . 55 vi List of Figures 1.1 Dynamic Characteristics of A General Non-return Valve . 15 2.1 Schematic Of A Check Valve . 19 2.2 Inherent Characteristics Of Valves . 21 2.3 Flow Coefficient Used For Present Model . 22 2.4 Computer Algorithm For Coupling Model . 23 3.1 Characteristic Lines In x-t Plane . 26 3.2 Constant-Level Upstream Reservoir . 29 3.3 Series Junction . 30 3.4 A Schematic of Check Valve Between Two Pipes . 31 4.1 Testing Loop . 36 4.2 Sequence of Water Hammers Occurred in System . 38 4.3 Case 1 Pressure Time History At Upstream For 0 ≤ t ≤ 10 . 40 4.4 Case 1 Pressure Time History At Upstream For 0 ≤ t ≤ 4 . 40 vii 4.5 Case 1 Pressure Time History At Upstream For 4 ≤ t ≤ 8 . 41 4.6 Case 1 Pressure Time History At Downstream For 0 ≤ t ≤ 10 . 41 4.7 Case 1 Pressure Time History At Downstream For 0 ≤ t ≤ 4 . 42 4.8 Case 1 Pressure Time History At Downstream For 4 ≤ t ≤ 8 . 42 4.9 Case 2 Pressure Time History At Upstream For 0 ≤ t ≤ 8 . 45 4.10 Case 2 Pressure Time History At Upstream For 0 ≤ t ≤ 2 . 45 4.11 Case 2 Pressure Time History At Upstream For 2 ≤ t ≤ 4 . 46 4.12 Case 2 Pressure Time History At Downstream For 0 ≤ t ≤ 8 . 46 4.13 Case 2 Pressure Time History At Downstream For 0 ≤ t ≤ 2 . 47 4.14 Case 2 Pressure Time History At Downstream For 2 ≤ t ≤ 4 . 47 4.15 Case 2 Pressure At Downstream for 0:7 ≤ t ≤ 0:9 . 48 4.16 Comparison of Two Cases at Upstream for 0:6 ≤ t ≤ 4:6 . 50 4.17 Comparison of Two Cases at Upstream for 0:6 ≤ t ≤ 1:6 . 50 4.18 Comparison of Two Cases at Downstream for 0:6 ≤ t ≤ 4:6 . 51 4.19 Comparison of Two Cases at Downstream for 0:6 ≤ t ≤ 1:6 . 51 5.1 Quasi-steady Model with f = Darcy-Weisbach friction coefficient for 0 ≤ t ≤ 8....................................... 56 5.2 Quasi-steady Model with f = 0.15 for 0 ≤ t ≤ 8 . 56 5.3 Quasi-steady Model with f = 0.3 for 0 ≤ t ≤ 8 . 57 viii 5.4 Quasi-steady Model with f = Darcy-Weisbach friction coefficient for 0 ≤ t ≤ 8....................................... 57 5.5 Quasi-steady Model with f = 0.15 for 0 ≤ t ≤ 8 . 58 5.6 Quasi-steady Model with f = 0.3 for 0 ≤ t ≤ 8 . 58 5.7 Case 1 Simulated By Quasi-Steady 1D Model With FT = 0:3 . 59 5.8 Case 1 Simulated By Unsteady Friction 1D Model With FT = 0:3 and k2 = 0:045.................................... 60 5.9 Case 1 Comparison of Two Different Models At Upstream . 61 5.10 Case 1 Comparison of Two Different Models At Downstream . 62 5.11 Case 2 (Downstream) Present Model With FT = 0:3 and k2 = 0:045 . 65 5.12 Case 2 (Upstream) Present Model With FT = 0:3 and k2 = 0:045 . 66 5.13 Case 2 (Downstream) Present Model FT = 0:3 and k2 = 0:045 for 0:7 ≤ t ≤ 1:5...................................... 67 5.14 Case 2 (Upstream) Present Model FT = 0:3 and k2 = 0:045 for 0:7 ≤ t ≤ 1:5 67 5.15 Case 2 Flow Rate Changes At Assembly for 0:7 ≤ t ≤ 0:8 . 68 5.16 Case 2 Disk Angle Position . 68 5.17 Case 2 (Downstream) Present Model With FT = 0:3 and k2 = 0:08 . 69 5.18 Case 2 (Upstream) Present Model With FT = 0:3 and k2 = 0:08 . 70 5.19 Case 2 (Downstream) Present Model FT = 0:3 and k2 = 0:08 for 0:7 ≤ t ≤ 1:5...................................... 71 ix 5.20 Case 2 (Upstream) Present Model FT = 0:3 and k2 = 0:08 for 0:7 ≤ t ≤ 1:5 71 5.21 Case 2 (Downstream) Present Model With FT = 0:3 and k2 = 0:2 . 72 5.22 Case 2 (Upstream) Present Model With FT = 0:3 and k2 = 0:2 . 73 5.23 Case 2 (Downstream) Present Model FT = 0:3 and k2 = 0:2 for 0:7 ≤ t ≤ 1:5 74 5.24 Case 2 (Upstream) Present Model FT = 0:3 and k2 = 0:2 for 0:7 ≤ t ≤ 1:5 74 5.25 Case 2 (Downstream) Present Model With FT = 0:3 and k2 = 0:4 . 75 5.26 Case 2 (Upstream) Present Model With FT = 0:3 and k2 = 0:4 . 76 5.27 Case 2 (Downstream) Present Model FT = 0:3 and k2 = 0:4 for 0:7 ≤ t ≤ 1:5 77 5.28 Case 2 (Upstream) Present Model FT = 0:3 and k2 = 0:4 for 0:7 ≤ t ≤ 1:5 77 5.29 Changes on Flow Rate At Assembly . 79 5.31 (Upstream) Comparison of Responses With Different Valve Types . 80 5.30 (Downstream) Comparison of Responses With Different Valve Types . 80 x Abstract When control valves at the end of pipeline close simultaneously, two pressure waves are generated at each end and the waves propagate toward to the other end. The pressure waves continue to move back and forth along pipelines until they are damped out to next steady states. This study provides information on the experimental data and the numer- ical simulation of a rapid hydraulic transient event called water hammer. The energy loss term due to friction in the present model consists of quasi-steady contribution and unsteady contribution. For the present model, an equivalent friction coefficient is used to replace the quasi-steady friction coefficient, inclusive unsteady friction loss and minor energy loss factors. The unsteady component has been related to the combination of the instant flow acceleration and instant flow convective acceleration.
Details
-
File Typepdf
-
Upload Time-
-
Content LanguagesEnglish
-
Upload UserAnonymous/Not logged-in
-
File Pages103 Page
-
File Size-