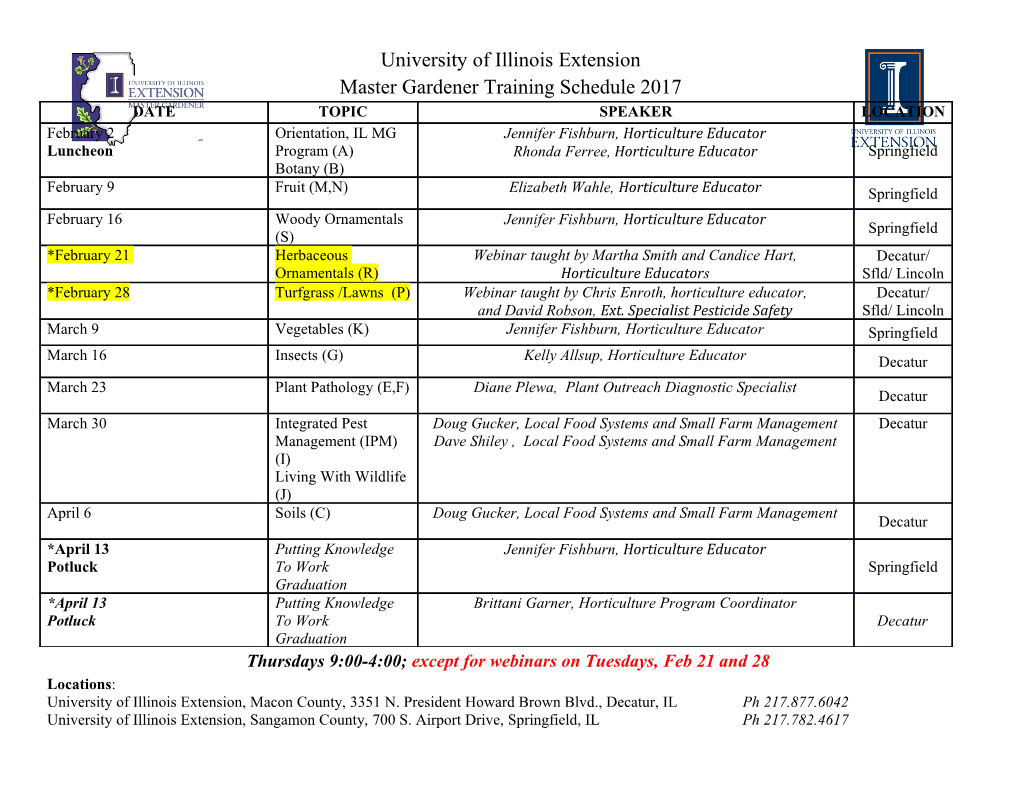
Synopsis V2.2 Single Event Effects Testing of the Intel Pentium III (P3) and AMD K7 Microprocessors Jim Howard1, Ken LaBel2, Marty Carts3, Ron Stattel3 and Charlie Rogers3 1. Jackson and Tull Chartered Engineers, Washington DC 20018 2. NASA GSFC, Greenbelt, MD 20771 3. Raytheon ITSS, Greenbelt, MD 20771 Test Dates: December 18-20, 2000. Report Date: February 16, 2001. Introduction As part of the Remote Exploration and Experimentation Project, work was funded for the “Radiation Evaluation of the INTEL Pentium III and Merced Processors and Their Associated Bridge Chips.” As a next step in the completion of this work, Intel Pentium III and AMD K7 processors were re-tested at the proton facility at the Indiana University Cyclotron Facility (IUCF). There were three main objectives for this second proton test. The first was to do a more thorough investigation of single-event-induced functional interrupts (SEFI) and the single event upsets (SEU). The initial proton test did not do a sufficient job of distinguishing between SEFIs and SEUs. The second objective was to investigate the event rate for the various components of the processors, under a variety of software and hardware configurations. Finally, the third objective was continue to look at the state-of-the-art processors (higher clock speeds of both P3 and K7) and investigate the impact on rates with Device Under Test (DUT) clock speed. The remainder of this report details the test process, methodology and results from this second proton testing. Devices Tested Pentium III devices with rated clock speeds of 750, 850 and 933 MHz were used and K7 microprocessors running at 600, 650 and 900 and 1000 MHz were tested. Pentium III devices were manufactured by Intel and the K7 devices were manufactured by Advanced Micro Devices (AMD). All devices were characterized prior to exposure. A listing of all devices used in this testing are given in Table I below. Test Facility Facility: Indiana University Cyclotron Facility Proton Energy: 189.9 MeV incident on DUT structure Flux: 2.0 x 106 to 1.5 x 108 protons/cm2/s. Test Methods Temperature: The test was conducted at room temperature. Intel P3 junction temperature was monitored using an on-die diode. Test Hardware: The system hardware consists of two subsystems, the test controller and the DUT computer, in addition to the system cabling. These subsystems are described below. Following that is a description of the DUT processors (The P3 and the K7). Figure 1 illustrates the overall test configuration. TABLE I Device Under Test (DUT) Table Device Vendor Speed DUT Number Package Markings 750/256/100/1.65V S1 Pentium III Intel 750 MHz 750_1 90260050-0092 MALAY imc '99 SL456 850/256/100/1.65V S1 Pentium III Intel 750 MHz 850_1 10280400-0071 Philippines imc '99 SL47M 850/256/100/1.65V S1 Pentium III Intel 850 MHz 850_2 10280400-0293 Philippines imc '99 SL47M 933/256/133/1.7V S1 Pentium III Intel 933 MHz 933_1 00280415-0224 COSTA RICA imc '99 SL47Q AMD-K7600MTR51B C K7 AMD 600 MHz 600_1 219949147583 AMD-K7650MTR51B A K7 AMD 650 MHz 650_1 230015009833 AMD-K7650MTR51B A K7 AMD 650 MHz 650_2 210017540094 AMD-K7900MNR53B A K7 AMD 900 MHz 900_1K 210036542751 AMD-K7100MNR53B A K7 AMD 1 GHz 1000_1 710026014044 AMD-K7100MNR53B A K7 AMD 1 GHz 1000_2 710026019051 Test Controller (PXI) Subsystem The test controller hardware is based on the PXI specification. A description of the test controller, or PXI, subsystem and the cabling between the subsystems follows. The PXI subsystem, as shown in Figure 2, consists of the components located within the PXI chassis, the intrasystem cabling and the user interface. Within the PXI chassis resides an embedded controller (running Win98, Labview (LV) environment, and a custom LV application), a signal switch matrix, and two digital multimeters (DMMs) in the voltage measurement mode. The switch matrix provides two functions: The multiplexing of analog signals to one of the DMMs, and contact closures (pulling signal levels to ground). The other DMM is dedicated to monitoring one specific analog value and measures that without regular periodic switching so that it may measure more frequently with less delay. The cabling from the PXI subsystem to the user facility includes the keyboard/monitor/mouse extension (a CAT5 cable based extender from Cybex, Inc.), a network connection for data file access, and power, in the case that the PXI system requires a hard power cycle. The keyboard/monitor/mouse is located in the user facility. The system cabling includes cabling between the PXI and the DUT subsystems, cabling between each subsystem and the user facility, and intra-subsystem cabling. The intra-PXI cabling includes only the cables from the switch matrix to the adjacent DMM modules. Protons P-III DUT Computer Card Extender Keyboard Monitor PCI Video, keyboard PS-2 port (mouse) Mouse Motherboard Memory signals Floppy Card Drive Motherboard Beam ATX Controls Control & Power Dosimetry Supply Power Supply Computer Controls Video, keyboard DUT Analog PS-2 port (mouse) Keyboard Measurements signals Monitor GPIB Mouse RS-232 DMM - 1 DMM - 2 Test Controller Switch Matrix PXI bus/chassis Test Controller User Area Irradiation Area Figure 1. Block diagram illustrating the overall test configuration. Most of the cabling between the PXI and the DUT subsystems leaves the PXI subsystem from the switch matrix (described further below). One exception is a serial (RS-232) cable bringing telemetry from the DUT computer to the PXI controller. The controller resides in the test chamber, though removed from the immediate area of the DUT computer by about 15’ and a corner of concrete in order to reduce exposure of the PXI subsystem to secondary neutrons. DUT Computer Subsystem The DUT computer subsystem consists of the components immediately connected to the motherboard without cabling, the components located nearby (e.g. disk drives), the intrasystem cabling, and the user interface. Directly attached to the commercial motherboard are the modified DUT processor (described later), a RAM module (DIMM), the video card, a DUT processor extender card and a PCI-bus memory board, added on the hypothesis that even the simple RS- 232 telemetry was subject to SEE. This board and the serial port are to store identical copies of the telemetry stream; the contents of the memory board will survive a soft reset of the DUT computer for later readout through the RS-232 port. This has proven very useful. The DUT computer motherboard resides in the test chamber, positioned directly in front of the proton beam but so that only the DUT processor is irradiated. To DUT computer Network Serial port telemetry and control Connection to Motherboard control signals User Facility Analog samples from DUT extender board To Test Controller interface in User Facility, via extender PS-2 PS-2 VGA 10b-T RS-232 Hard Test DMM DMM Disk Controller #1 #2 Drive Switch Matrix cPCI-bus interface PXI chassis/backplane Figure 2. Block diagram of the PXI subsystem. Located nearby (~6 feet) but in a hopefully greatly reduced secondary neutron environment are a standard PC ATX power supply (PS), a floppy and/or hard disk drive, and a Cybex keyboard/monitor extension. The DUT processor extender card is inserted between the DUT processor and the motherboard, extending the 242 DUT processor card contacts an additional 1.5” above the motherboard. This is done for two reasons. First, a clear line of site for the proton beam is established (connectors and the system RAM are avoided). Second, the extension provides the best opportunity for monitoring DUT currents. The extender board is modified to insert a low resistance in series with the power traces as shown in the schematic in Figure 3. The schematic of the voltage and current sampling is duplicated three times on the extender card. Also shown is the P3 temperature sensing diode schematic. Cabling is added to monitor the developed voltages. A photograph of the modified extender card can be seen in Figure 4. Intra-DUT subsystem cabling includes the disk drive cables, an extension cable for the ATX PS including a tap for test controller on/off control and the keyboard/monitor/ mouse extension (a CAT5 cable based extender from Cybex, Inc.). The motherboard is modified to allow connection to two controlling signals, both momentary contact closures. From the PXI switch matrix—motherboard power on/off + V supply - 100 uA (MotherPonoff) is intended to be controlled by a desktop computer case front panel switch, and motherboardOne of three supply soft monitors reset (MotherSR) which is sometimes implemented on Pentium III IUCF 12/00 Proton Test Extender Board Details desktop computers. P3_IU0012_Extender_Schem.ppt DUT supply On-die temperature sensing diode DUT module Isupply Extender board + To PXI Ω VD To PXI R Vcc_core: R = 1 m - Ω Vcc_L2: R = 2 m VD = ƒ(temp) Vtt: R = 10 mΩ Vsupply Motherboard V +-Supply 100 µA Figure 3. Schematic diagram for the DUT extender card. Figure 4. Photograph showing the Pentium III extender card. ATX PS on/off state is normally controlled by a constant signal from the motherboard (The ATX SP supplies a standby +5V to power such motherboard functions). This signal (PS_ON#) is, approximately, a latched toggle of the front panel signal, MotherPonoff. As modified, MotherPonoff still controls power-down functions within the motherboard, but its latch/toggled version is disconnected from the ATX power supply’s PS_ON# input so that that can be controlled directly from the PXI. The ATX PS AC power is extended back to the user facility. The DUT software periodically reports to the PXI through the motherboard’s serial port via a null modem cable.
Details
-
File Typepdf
-
Upload Time-
-
Content LanguagesEnglish
-
Upload UserAnonymous/Not logged-in
-
File Pages21 Page
-
File Size-