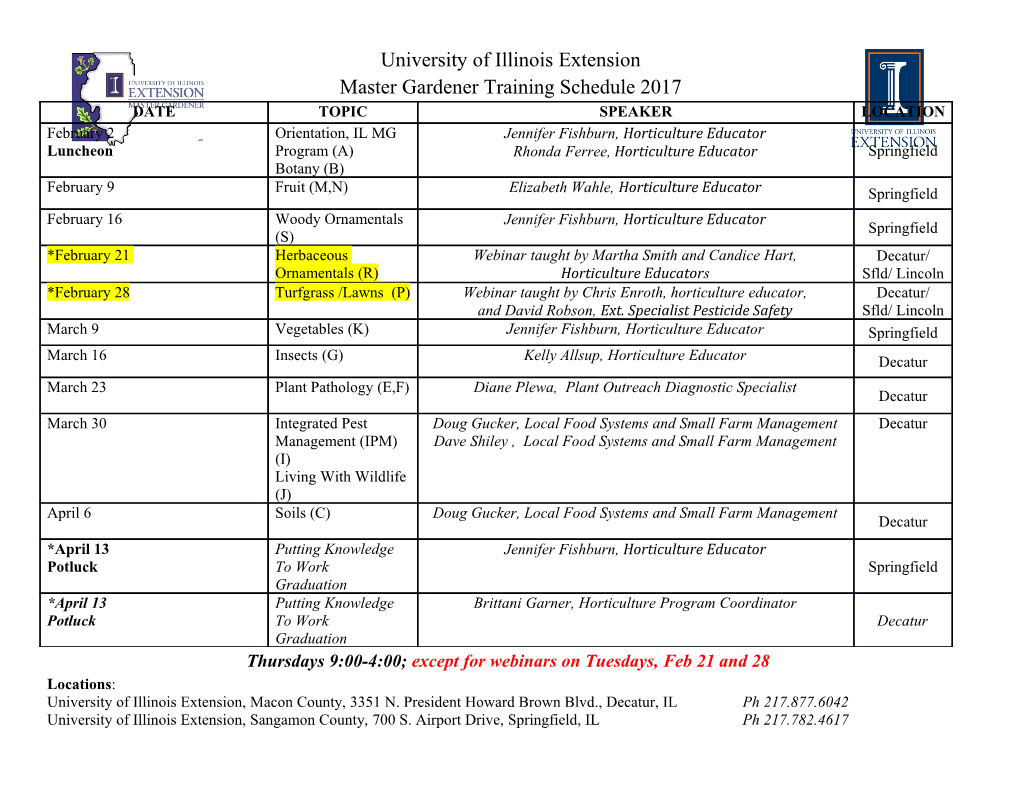
PRODUCTION PLANNING AND SCHEDULING IN MULTI-STAGE BATCH PRODUCTION ENVIRONMENT A THESIS SUBMITTED IN PARTIAL FULFILLMENT OF THE REQUIREMENTS FOR THE FELLOW PROGRAMME IN MANAGEMENT INDIAN INSTITUTE OF MANAGEMENT AHMEDABAD By PEEYUSH MEHTA Date: March 15, 2004 Thesis Advisory Committee __________________________[Chair] [PANKAJ CHANDRA] __________________________[Co-Chair] [DEVANATH TIRUPATI] __________________________[Member] [ARABINDA TRIPATHY] 1 Production Planning and Scheduling in Multi-Stage Batch Production Environment By Peeyush Mehta ABSTRACT We address the problem of jointly determining production planning and scheduling decisions in a complex multi-stage, multi-product, multi-machine, and batch-production environment. Large numbers of process and discrete parts manufacturing industries are characterized by increasing product variety, low product volumes, demand variability and reduced strategic planning cycle. Multi-stage batch-processing industries like chemicals, food, glass, pharmaceuticals, tire, etc. are some examples that face this environment. Lack of efficient production planning and scheduling decisions in this environment often results in high inventory costs and low capacity utilization. In this research, we consider the production environment that produces intermediate products, by-products and finished goods at a production stage. By-products are recycled to recover reusable raw materials. Inputs to a production stage are raw materials, intermediate products and reusable raw materials. Complexities in the production process arise due to the desired coordination of various production stages and the recycling process. We consider flexible production resources where equipments are shared amongst products. This often leads to conflict in the capacity requirements at an aggregate level and at the detailed scheduling level. The environment is characterized by dynamic and deterministic demands of finished goods over a finite planning horizon, high set-up times, transfer lot sizes and perishability of products. The decisions in the problem are to determine the production quantities and inventory levels of products, aggregate capacity of the resources required and to derive detailed schedules at minimum cost. We determine production planning and scheduling decisions through a sequence of mathematical models. First, we develop a mixed-integer programming (MIP) model to determine production quantities of products in each time period of the planning horizon. The objective of the model is to minimize inventory and set-up costs of intermediate products and finished goods, inventory costs of by-products and reusable raw materials, and cost of fresh raw materials. This model also determines the aggregate capacity of the resources required to implement the production plan. We develop a variant of the planning model for jointly planning sales and production. This model has additional market constraints of lower and upper bounds on the demand. Next, we develop an MIP scheduling model to execute the aggregate sales and productions plans obtained from the planning model. The scheduling model derives detailed equipment wise schedules of products. The objective of the scheduling model is to minimize earliness and tardiness (E/T) penalties. We use branch and bound procedure to solve the production-planning problem. Demand of finished goods for each period over the planning horizon is an input to the model. The planning model is implemented on a rolling horizon basis. 2 We consider flowshop setting for the finished goods in the production environment. The due dates of finished goods are based on the customer orders. We report some new results for scheduling decisions in a permutation flowshop with E/T penalties about a common due date. This class of problems can be sub-divided into three groups- one, where the common due date is such that all jobs are necessarily tardy; the second, where the due date is such that the problem is unrestricted; and third is a group of problems where the due date is between the above two. We develop analytical results and heuristics for flow shop E/T problems arising in each of these three classes. We also report computational performance on these heuristics. The intermediate products follow a general job shop production process with re-entrant flows. We develop heuristics to determine equipment wise schedule of intermediate products at each level of the product structure. The due date of an intermediate product is based on the schedule of its higher-level product. The models developed are tested on data for a chemical company in India. The results of cost minimization model in a particular instance indicated savings of 61.20 percent in inventory costs of intermediate products, 38.46 percent in set-up costs, 8.58 percent in inventory costs of by-products and reusable raw materials, and 20.50 percent in fresh raw material costs over the actual production plan followed by the company. The results of the contribution maximization model indicate 42.54 percent increase in contribution. We also perform sensitivity analysis on results of the production planning and scheduling problem. The contribution of this research is the new complexities addressed in the production planning and scheduling problem. Traditional models on multi-stage production planning and scheduling are primarily based on assembly and fabrication types of product structures and do not consider the issues involved in recycling process. Scheduling theory with E/T penalties is largely limited to single machine environment. We expect that models developed in this research would form basis for production planning and scheduling decisions in multi- stage, multi-machine batch processing systems. The sensitivity analysis of the models would provide an opportunity to the managers to evaluate the alternate production plans and to respond to the problem complexities in a better way. 3 Acknowledgements I wish to express my deepest gratitude to my thesis advisor Professor Pankaj Chandra. He has been a tremendous source of learning for me during my stay at IIMA. Professor Chandra has been a great motivator, and has a significant share in my academic grooming. Much of the credit for this work goes to Professor Devanath Tirupati, co-chair of my thesis committee. He has been very patient with me and has provided very useful research training. I would also like to thank Professor Arabinda Tripathy, member of my thesis committee for providing very useful feedback throughout my work. I am grateful to Professor Diptesh Ghosh, Professor P. R. Shukla, Professor Ashok Srinivasan and Professor Goutam Dutta for their useful feedback on my thesis. I am also thankful to Professor Shiv Srinivasan for giving some pointers on the drafting of this document. I wish to especially thank my wife Ritu, as this thesis would not have been possible without her support. She has a major share in raising our daughter Riti, and her break from her professional career helped me to stay focused on my work Riti always provided the much- needed break from the thesis work. I dedicate this work to my parents. They have eagerly waited to see me accomplish this work. Dhiraj, my brother, has been, as always, a source of encouragement. I would like to thank my colleagues Bharat, Rohit, Satyendra and all those with whom I have interacted at various stages of my thesis. The staff members of FPM office, computer center and library have obliged me in more ways than one. 4 Table of Contents 1 Introduction................................................................................................................. 9 1.1 Introduction................................................................................................................... 9 1.2 Production Planning and Scheduling Problem ........................................................... 12 1.2.1 Production Environment .............................................................................................13 1.2.2 Complexities in the Production Environment ................................................................16 1.2.3 Production Planning and Scheduling Decisions.............................................................18 1.3 Summary..................................................................................................................... 19 2 Literature Review..................................................................................................... 21 2.1 Integrated Production Planning and Scheduling Models ............................................ 22 2.2 Hierarchical Production Planning and Scheduling Models ........................................ 29 2.3 Earliness and Tardiness Scheduling............................................................................ 34 2.4 Research Gaps............................................................................................................. 42 3 Production Planning and Scheduling Models ........................................................ 44 3.1 Introduction................................................................................................................. 44 3.2 Production Planning Model........................................................................................ 46 3.2.1 Formulation of Production Planning Model...................................................................46 3.3 Scheduling Models.....................................................................................................
Details
-
File Typepdf
-
Upload Time-
-
Content LanguagesEnglish
-
Upload UserAnonymous/Not logged-in
-
File Pages194 Page
-
File Size-