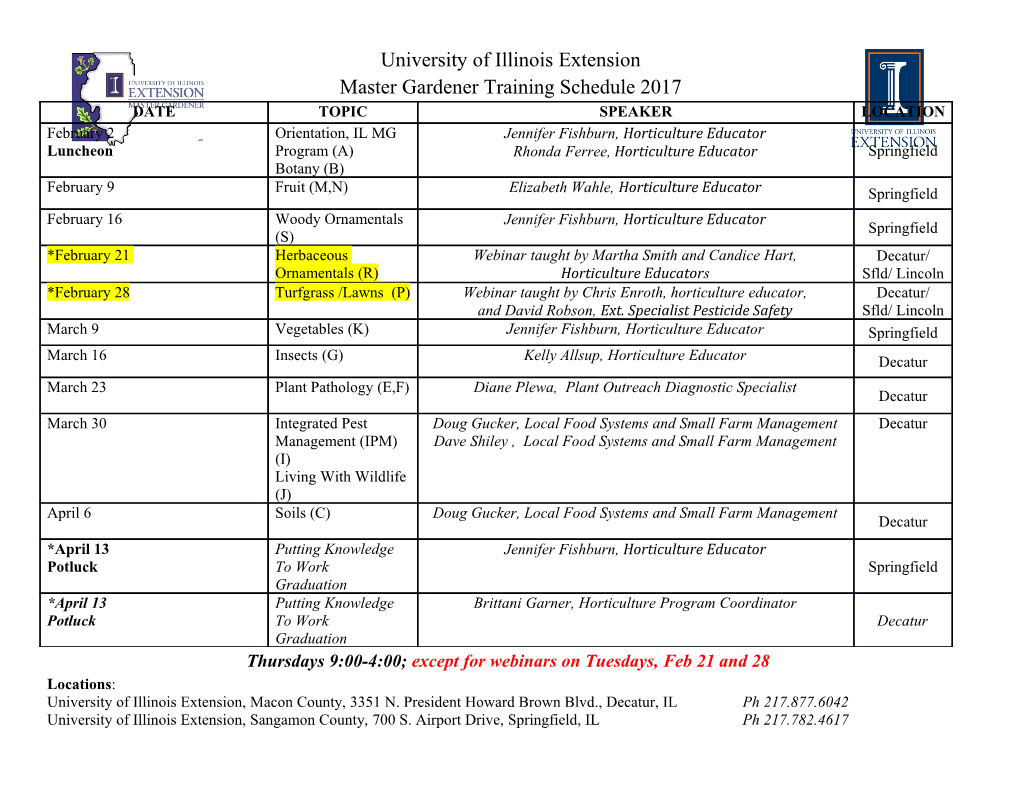
APPENDIX 387 APPENDIX A - Glossary of terminology commonly used in relation to metal matrix composites Aspect ratio: ratio of length to diameter of short fibres or whiskers. Binder: an additional phase added to the reinforcement to create a preform, with the goal of increasing the tensile and shear strength of the preform for handling prior to infiltration. Colloidal silica is the most common binder for preforms, typically applied wet prior to shaping the preform, which is subsequently dried by firing. Binders may also be used in powder metallurgy methods to increase handling strength or to lubricate flow (in injection molding for example); they are then burned off prior to consolidation. Borsic: silicon carbide coated boron monofilaments. Cellular metals (metal foams): highly porous metallic material; may be considered as MMC formed of a metal matrix "reinforced" by closed or open pores containing vacuum or gas (these are not considered composites in the present document). Centrifugal infiltration: an infiltration process in which centrifugal force is used to drive the molten matrix into the preform; typically, high angular velocities (several thousand rpm) are needed. Cermet: a metal matrix composite with a three-dimensionally continuous ceramic reinforcement, typically with more ceramic than metal (generally containing less than 20% metal by volume). A cermet is thus both a ceramic matrix composite and a metal matrix composite. Chopped fibres: short fibres produced by cutting a fibre into shorter discrete lengths. Coating processes: see Deposition processes Cold isostatic pressing (CIP): cold pressing of composites with application of hydrostatic pressure by means of a non­ compressible fluid such as oil, at temperatures too low to effect concurrent sintering of the matrix; for metal matrices this temperature is generally less than the matrix recrystallisation temperature. 388 METAL MATRIX COMPOSITES Cold pressing of composites: powder consolidation of composites with application of pressure by means of a piston, at temperatures too low to effect concurrent sintering of the matrix, which for metal matrices is generally below the matrix recrystallisation temperature. Compocasting: a primary composite manufacturing process, a variant of stir-casting in which the metal is semi-solid, i.e., a rheocasting process incorporating the reinforcing ingredient material to form the composite. This aids incorporation of the particles, in particular because the metal is more viscous. Composite consolidation: a primary composite manufacturing process in which the ingredient materials comprising matrix and reinforcement elements (generally the reinforcement coated with the matrix metal) are consolidated, with or without pressure, to eliminate porosity. Composite: a composite (or composite material) is defined as a material that consists of at least two distinct phases (or combinations of phases) that are bonded together at the atomic level in the composite, each of which originates from a separate ingredient material that pre-exists the composite. The essential elements of this definition are: (i) composite refers to a material, as opposed to a structure or a component; as such a composite material is used for the fabrication of components of various shapes or functions, which distinguishes it from a wing or other structure made of several components bonded together, or from an electronic device or packaging structure made of layered materials (although one of the materials in the packaging could be considered a composite), and (ii) the composite is produced via a physical combination of at least two pre-existing ingredient materials; this distinguishes a composite from other multiphase materials which are produced by bulk processes where one or more phases result from phase transformation: directionally solidified eutectics or molten alloys from which a ceramic phase is solidified or precipitated are thus considered to be alloys and not composites (even though their properties can be described using composite theory). Continuous fibre (cf) : a cylindrical ingredient material produced continuously to form an essentially endless reinforcement in the composite; usually delivered on bobbins of fibre tows, each tow consisting of many individual fibres of diameters typically in the APPENDIX 389 range of 5 to 20 )lm. In the production process such fibres are often coated by a polymeric size or sizing. Continuous fibre reinforced MMC (CFRM): a metal matrix composite with reinforcement of continuous fibres. Continuous MMC primary process: a primary process for the production of MMC material from its ingredients in continuous fashion (e.g., foil-fibre-foil diffusion bonding using a rolling mill, or continuous infiltration). Continuous reinforcement: a reinforcement that continues across the composite in at least one dimension (typically made of continuous fibres or an open-celled foam). Deposition processes: processes that deposit (or coat) the matrix onto individual reinforcement elements of the ingredient material. Examples include vapour deposition and electrolytic coating. Diffusion bonding: a primary process for composite fabrication in the solid state, in which stacks of reinforcement preforms (usually parallel fibre monolayers) and matrix foils are stacked, encapsulated, and bonded together after evacuation by mechanical pressure. Discontinuous reinforcement: a non-continuous reinforcement, taking the form of individual elements embedded in the metal matrix (e.g., particulates, short fibres, whiskers). Discontinuously reinforced MMC: a metal matrix composite with a discontinuous reinforcement. Dispersoid (or dispersion) reinforced MMC: a metal matrix composite with a dispersoid reinforcement occupying a volume fraction in the material greater than 5% (otherwise, the material is considered a dispersion strengthened metal; incidentally it may form the matrix of any type of MMC, i.e., a MMC with dispersion-strengthened matrix). Dispersoids (d): same as particulates except for the diameter, which is less than 1 )lm. Electrolytic co-deposition: a primary composite processing method that consists in electrolytic deposition of the matrix metal from a solution containing the reinforcement ingredient, so as to trap 390 METAL MATRIX COMPOSITES the reinforcement within the deposited metal layer. Electrolytic coating: a primary composite manufacturing process wherein the matrix is deposited from solution using electrochemical means onto individual reinforcement elements. Flake: a flat roughly equiaxed reinforcement. Graphite is, for example, often supplied in flake form (see platelet). Foil-fibre-foil method (also called foil-fibre method): process wherein layers of metal foil and ceramic monofilament fibres are alternatively stacked to produce precursor materials and subsequently hot pressed, also called diffusion bonding. Forced infiltration: an infiltration process which is not spontaneous, i.e., which requires application of mechanical force onto matrix or reinforcement. Gas pressure infiltration: a pressure infiltration process that uses pressurized gas to apply pressure on the metal surface. Hot isostatic pressing (HIP): hot pressing of composites with application of hydrostatic pressure by means of a gas, at temperatures high enough to effect concurrent sintering of the matrix, which for metal matrices is generally above the matrix recrystallisation temperature. Hot pressing: powder consolidation of composites with application of pressure by means of a piston, at temperatures high enough to effect concurrent sintering of the matrix, which for metal matrices is generally above the matrix recrystallisation tern perature. Hybrid composite: a composite consisting of at least three (as opposed to two) distinct phases (or combinations of phases) that are bonded together at the atomic level in the composite, each of which originates from a separate ingredient material that preexists the composite (there were, hence, at least three ingredient materials). Hybrid preform: a preform containing at least two types of ingredient materials that form at least two distinct reinforcements in the composite. APPENDIX 391 Infiltration: a primary process of composite production whereby the molten metal matrix is made to fill, spontaneously or under force (i.e., with supply of external mechanical work), pores within a preform of the reinforcement. Ingredient material supplier or producer: a supplier or producer of ingredient materials that are used to make a composite (includes fibre or ceramic particle producers, as well as preform producers). Ingredient materials: raw materials put together to produce the composite (e.g., the metal alloy, metal powder, ceramic particles, etc.) In-situ MMC: a MMC in which the ingredient reinforcement material changes its nature during composite processing (e.g., TiB2 reacts to form TiC in some metals by adding carbon). To obtain a MMe, the reinforcement must, however, retain its identity and in particular remain solid throughout processing of the reinforcement (otherwise, the material is a solidified alloy). Interface: the portion of the composite microstructure that lies between matrix and reinforcement. The interface may be a simple row of atomic bonds (e.g., the interface between alumina and pure aluminium), but may also include matrix/-reinforcement reaction products (e.g., aluminium carbide between aluminium and carbon fibres), or reinforcement coatings (e.g., interfacial coatings between SiC monofilaments and titanium matrices).
Details
-
File Typepdf
-
Upload Time-
-
Content LanguagesEnglish
-
Upload UserAnonymous/Not logged-in
-
File Pages36 Page
-
File Size-