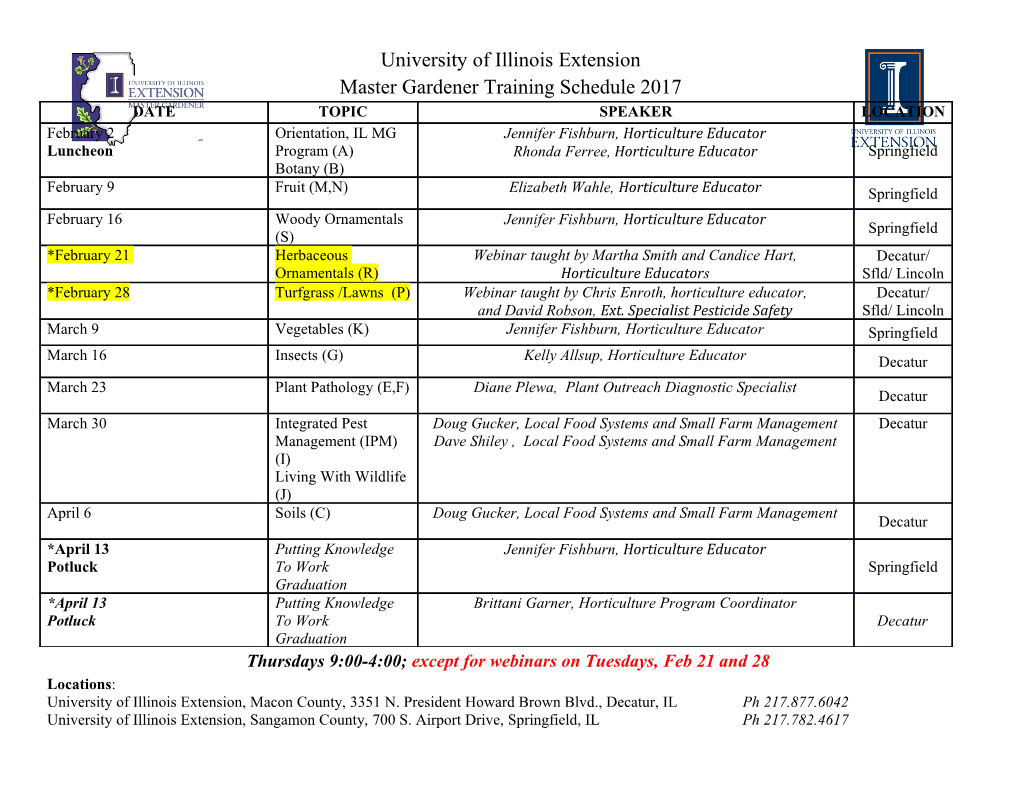
https://ntrs.nasa.gov/search.jsp?R=19970021267 2020-06-16T02:28:46+00:00Z View metadata, citation and similar papers at core.ac.uk brought to you by CORE provided by NASA Technical Reports Server NASA Technical Memorandum 112852 Research and Applications in Aeroelasticity and Structural Dynamics at the NASA Langley Research Center Irving Abel Langley Research Center, Hampton, Virginia May 1997 National Aeronautics and Space Administration Langley Research Center Hampton, Virginia 23681-0001 RESEARCH AND APPLICATIONS IN AEROELASTICITY AND STRUCTURAL DYNAMICS AT THE NASA LANGLEY RESEARCH CENTER Irving Abel Structures Division NASA Langley Research Center MS 121 Hampton, Virginia 23681 USA e-mail address: [email protected] ABSTRACT The Structures Division supports the development of more efficient structures for airplanes, An overview of recently completed programs in helicopters, spacecraft, and space transportation aeroelasticity and structural dynamics research at vehicles. Research is conducted to integrate the NASA Langley Research Center is presented. advanced structural concepts with active-control Methods used to perform flutter clearance studies concepts and smart materials to enhance structural in the wind-tunnel on a high performance fighter performance. Research in aeroelasticity ranges are discussed. Recent advances in the use of from flutter clearance studies of new vehicles smart structures and controls to solve aeroelastic using aeroelastic models tested in the wind tunnel, problems, including flutter and gust response are to the development of new concepts to control presented. An aeroelastic models program aeroelastic response, and to the acquisition of designed to support an advanced high speed civil unsteady pressures on wind-tunnel models for transport is described. An extension to transonic providing experimental data to validate unsteady small disturbance theory that better predicts flows theories. Analytical methods are developed and involving separation and reattachment is validated to solve the aeroelastic problems of presented. The results of a research study to fixed- and rotary-wing vehicles, including the determine the effects of flexibility on the taxi and control of instabilities, loads, vibration, and adverse takeoff characteristics of a high speed civil structural response. transport are presented. The use of photogrammetric methods aboard Space Shuttle This paper presents the results of some selected to measure spacecraft dynamic response is studies in aeroelasticity and structural dynamics discussed. Issues associated with the jitter that occurred during the last 2 years. This paper response of multi-payload spacecraft are begins with an overview of how flutter clearance discussed. Finally a Space Shuttle flight studies are performed in the wind tunnel. The experiment that studied the control of flexible paper then addresses research aimed at using spacecraft is described. smart materials to suppress aeroelastic response, at acquiring an experimental data base to validate computational fluid dynamics codes, at the use of a INTRODUCTION series of aeroelastic wind tunnel models to support an advanced high speed civil transport program, at The Langley Research Center (LaRC) has been advances to the state-of-the-art in small designated by the Agency as the "Center of disturbance transonic theory, at the effect of Excellence" for Structures and Materials research. vehicle flexibility on the taxi and takeoff The Structures Division at LaRC conducts characteristics of an advanced high speed civil analytical and experimental research (figure 1) in transport, at using advanced photogrammetric Aeroelasticity, Computational Structures, methods aboard Space Shuttle to measure the Structural Mechanics, Structural Dynamics, and dynamic response of spacecraft in orbit, at Thermal Structures to meet the technology reducing the jitter of spacecraft through the use of requirements for advanced aerospace vehicles. active controls, and at a Shuttle flight experiment This paper will address research being done in on the control of flexible structures. aeroelasticity and structural dynamics. Theaeroelasticity research program at LaRC Tunnel Calibration: The objectives of the TDT depends heavily on the support of the Transonic calibration are to determine the operating Dynamics Tunnel. A short description of this envelope with the new test medium and to facility and some current modifications that are in quantify test section flow uniformity and flow progress will be described. quality in air and in R-134a. As shown infigure 3, the operating boundary of the tunnel will be slightlydegraded with the new heavy gas. This is TRANSONIC DYNAMICS TUNNEL due to a reduced density and higher value of the speed of sound for R-134a as compared to R-12. The Transonic Dynamics Tunnel (TDT) is a unique Primary flow parameters will be calibrated using test "national" facility dedicated to identifying, section centerline and sidewall pressure understanding, and solving aeroelastic problems. measurements. Centerline measurements will be The TDT, shown in figure 2, is a closed-circuit, obtained with a centerline tube instrumented to continuous-flow, variable-pressure, wind tunnel measure static pressure in the settling chamber with a 16-foot square test section. The tunnel and through the test section. Sidewall pressure uses either air or a heavy gas as the test medium measurements will be obtained with and can operate at stagnation pressures from near instrumentation mounted along the test section vacuum to atmospheric, has a Mach number range walls, ceiling, and floor. Total and static pressure from near zero to 1.2, and is capable of maximum and total temperature will also be measured at Reynolds numbers of about 3 million per foot in air discrete locations in the settling chamber and test to 10 million per foot in heavy gas. The TDT is section. These latter measurements in the settling specially configured for flutter testing, with chamber and test section will be used to calculate excellent model visibility from the control room and the primary flow conditions for the facility. a rapid tunnel shutdown capability for model safety. Model mount systems include two sidewall Measurements using a flow survey rake and turntables for semispan models, a variety of stings boundary layer rakes will also be obtained during for full-span models, a cable-mount system for the TDT calibration to assess test section flow "flying" models, a rotorcraft testbed for rotor blade uniformityand quality. The flow survey rake will be loads research, and a floor turntable for launch instrumented to measure spatial variations in flow vehicle ground-wind loads studies. The TDT also angularity, Mach number, and turbulence as a offers an airstream oscillation system for gust function of tunnel speed. The boundary layer studies and supporting systems for active controls rakes will measure boundary layer variations along testing. Testing in heavy gas has important the tunnel walls, ceiling, and floor. Several advantages over testing in air including improved boundary layer rakes which can be mounted at model to full-scale similitude, higher Reynolds different streamwise locations within the test numbers, and reduced tunnel power section will be used to determine boundary layer requirements. The TDT is the only wind tunnel in characteristics as a function of test section station. the world capable of flutter testing large, full-span, aeroelastically-scaled models at transonic speeds. Data Aceuisition System: Testing of aeroelastic models in the TDT requires real-time acquisition Facility_ Modification; As stated above, the TDT and display of measured static and dynamic relies on the use of a heavy gas as the test experimental data, and complex, on-line analyses medium. Currently the TDT is undergoing a major of dynamic data. The TDT open-architecture modification to replace the previous heavy gas dynamic data acquisition system (TDT-DAS) is a (refrigerant R-12) with an environmentally friendly state-of-the-art system which meets these heavy gas (refrigerant R-134a). Facility requirements. modifications are expected to be completed in the spring of 1997, followed, first, by an extensive Figure 4 contains a schematic of the TDT-DAS system "shakedown" and, next, by a thorough which illustrates how each component of the calibration of the flow characteristics of the wind system is connected to others. The TDToDAS tunnel. It isanticipated that the TDT will become hardware is comprised of two identical fully operational with the new heavy gas in the fall subsystems, each switch-connectable to a subset of 1997. of four NEFF "front ends". Each NEFF provides 2 signal conditioning, filtering, and sample-and-hold cleared for flutter on the cable-mount system, analog-to-digital conversion for 64 channels for a numerous store configurations were flutter cleared total capability of 256 channels. Each subsystem on the cable-mount system, the stability of all- is comprised of a Motorola 88K computer which moveable stabilators with mil-spec freeplay was performs the basic data acquisition, archiving to verified, and the stability of the model with several disk, and continuous buffering of data to a fiber- failure modes was determined. Limited parametric optic data ring. Connected to the fiber-optic ring is studies were also performed to determine the an SGI Challenge L computer which provides both effect of stabilator free play, wing and fuselage on-line frequency analysis,
Details
-
File Typepdf
-
Upload Time-
-
Content LanguagesEnglish
-
Upload UserAnonymous/Not logged-in
-
File Pages22 Page
-
File Size-