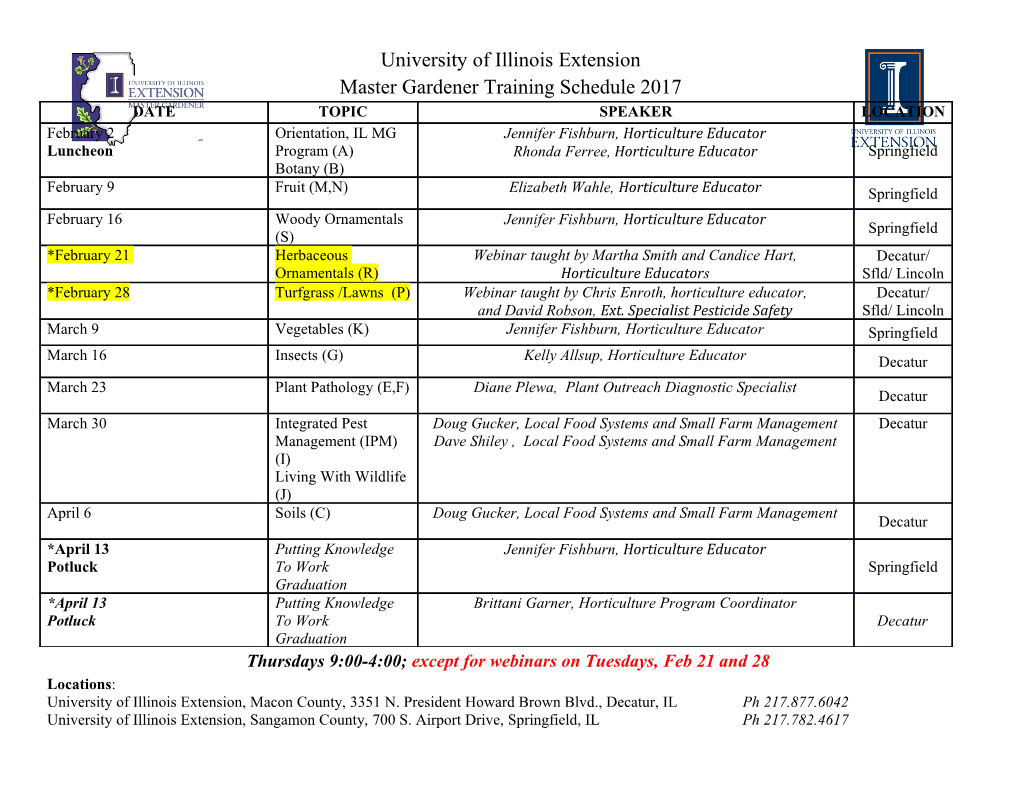
DIAMOND, PROCESSING, CUTTING AND POLISHING Websites and Resources on Gems: All About Gemstones allaboutgemstones.com ; Minerals and Gemstone Kingdom minerals.net ; International Gem Society gemsociety.org ; Wikipedia article Wikipedia ; Gemstones Guide gemstones-guide.com ; Gemological Institute of America gia.edu ; Mineralogy Database webmineral.com ; Websites and Resources Diamonds: Info-Diamond info-diamond.com ; Diamond Facts diamondfacts.org/about/index ; Diamond Mining and Geology khulsey.com/jewelry/kh_jewelry_diamond_mining ; Diamond Mine mining- technology.com/projects/de_beers ; Costellos.com costellos.com.au/diamonds ; DeeBeers debeers.com/page/home/ ; Wikipedia article Wikipedia ; American Museum of natural History amnh.org/exhibitions/diamonds ; Book: The Heartless Stone: A Journey Through the World of Diamonds, Deceit and Desire by Tom Zoellner. Diamond Processing and Sorting After diamond ore is mined it is transported to a processing plant where it is first fed into huge crushing machines. In the old days diamonds were recovered on vibrating greased tables. After the diamond ore was crushed it was mixed with water and slid down the table. Because of their surface properties, rough diamonds adhere tenaciously to the grease while other materials vibrate on through. Now the crushed rock is moved on a conveyor belt through a darkened chamber and X-rayed. Photo sensor detect the diamond's fluorescence and air jets remove it. Workers then sort the gem quality stones from the industrial diamonds by hand.<> Gem quality stones are sorted further in the large sorting room at the De Beers headquarters in London. On observing the sorting of five weeks of the world’s production of gem diamonds between two and nine carats in this sorting room, Fred Ward wrote in National Geographic, "I was dazzled with the brilliance of tens of thousands of uncut diamonds. On the counter running the length of the building, keen-eyed workers faced north windows for the indirect, even-color light needed to sort piles of roughs. Eight central tables were laden with sparkling crystals.<> A DeBeers official told Ward, “There are about 180,000 carats on those tables, worth about 70 million dollars. When we have all the stone together for next month's 'sight' or sale, including very small stones and stones over 100 carats, they will bring 250 million.”<> Diamond Cutting Diamond cutters are called lapidarists. Their goal is to get as large and as beautiful a gem as possible from a rough stone without losing too much material. To achieve this goal they essentially use the same techniques they have for the last 600 years. Lapidarist are very careful. They may study a diamond for months before working on it. Student diamond cutter who make two major mistakes fail to get certified. Diamonds can be cut several ways: 1) cleaving, in which the diamond is split with a chisel, is relatively rare these days; 2) sawing with a circular copper blade embedded with diamond dust particles; 3) grinding by pressing the diamond against a covered diamond-dust-covered steel wheel (called a skive) that spins at 3,000 rpms. Even though diamonds are quite hard they are relatively easy to cut along cleavage lines in their crystalline structure. The only thing that will cut a diamond is another diamond. The advantage of sawing over grinding is that sawing leaves behind saleable pieces of diamonds while grinding produces only dust. grounded stones never touch the wheel. They are pressed close but kept away slightly with a layer of oil. Diamond will shatter so great pains are taken to make sure this doesn't happen. They Lapidarists are especially wary of inclusions (black spots) which cause a diamond to crack. Most diamonds give a yield of 40 to 45 percent from rough to polished stone using current methods. Sometimes as much as 70 percent of a diamond is lost during the cutting and polishing process, but the price can jump six fold. The 1977 price for colorless 2½ carat rough was US$750. A flawless one carat stone can fetch as much as US$20,000.<> Types of Diamond Cuts Technology for faceting gems was not invented until the mid-17th century. The round ideal is the standard cut. Developed in 1919 by a mathematician and diamond cutter, Marcel Tokosky, as part of his doctoral dissertation at the University of London, it has 58 facets and was designed to highlight a diamond's light refraction and maximize its brilliance and fire. The Brilliant cut is similar (the same???). It is the most popular shape. Other popular cuts include the Emerald, marquise, and pear. New cuts include the Hearts of Fire, similar to the round ideal except the 58 facets are precisely aligned and polished and reveals a symmetrical heart and arrow when magnified; the Eternal, an 81-facet pedal design introduced in 1999; and the Leo, a 66-facet cut designed to bring out the brilliance. The Gemological Institute of America has devised software to enable retailers and consumers to compare diamonds of different cuts by grading the cut automatically. In most cases, large diamonds are sawed first along lines drawn on it with India ink, grounded and then polished. In 1978, a fist-size 341.9 carat diamond was cut in Belgium using such methods. It took six weeks to cut through the inch and three quarters stone.<> The largest flawless oval-cut diamond in history, a 102.23-carat stone, was cut from a 265.82- carat diamond found in Zaire along with four large diamonds by master cutter Motti Bernstein. When asked about his work, Bernstein said, "When I cut a diamond I don’t think about value; otherwise I get nervous." The value of the 102-carat stone has not been revealed. Another diamond—this one 22-carats—cut from the Congolese stone ended up a with another 22-carat diamond on a necklace for $3.5 million. Diamond Cutting and Grading Technology Some diamond cutters now use computer-driven machines with robot arms that can cut 24 diamonds at the same time. Diamond cutters use computer programs with three-dimensional images to determine the most profitable cuts. In recent years lasers have been introduced that make rough cuts and carry out “bruting” the beveling process used to give diamonds their characteristic sharp-edges shapes. Calibrated Diamonds of Johannesburg is developing an automated laser-cutting system The system can make more precise cuts and even polish diamonds. Researchers at Cambridge University’s Institute of Manufacturing claims they have devised a system that can accurately and consistently grade diamonds and other gems based on clarity. The system, called iGem, works out the value of a rough diamond and suggests ways to cut the stone to maximize value Based on the judgments of four diamond experts who classified 503 “virtual stones, computer models of stones with different kinds of flaws was devised and set of clear rules were established. Gems that are scanned using a desktop X-ray tomography machine and rated according to the system. If a stone falls somewhere in a grey area between ratings , a system kicks that suggest ways to improve the stone’s value tests by iGem show that following its rile sit could increase the value of a stone by as much as 23 percent. Diamond Cutting and Polishing Business Belgium has traditionally been the center of the diamond cutting and polishing trade. The trade for rough and polished stones revived in Belgium after World War II but the crafts of cutting and polishing moved from Belgium to India, Thailand and Israel. There are also large numbers of cutters in Vietnam and Sri Lanka. Most of the stones cut and polished in India are small. The larger stones are cut primarily in Belgium. The world’s largest diamond, the Cullinan, was cleaved by the famous diamond cutter Joseph Asscher, who studied the stone for six month before dividing it into two pieces. After he struck the famous diamond, successfully dividing it the way he wanted, he reportedly fainted and collapsed on the floor of his workshop. Antonio Blanco was one of the most famous diamond cutters in New York City’s Diamond District. His masterpiece was a 100-carat yellow diamond called the Dream that was valued at $20 million. He died in 2009. Diamond Cutting and Polishing Business in Belgium Antwerp is still regarded as world's diamond trading and cutting capital for big stones. One third of De Beers buyers are found here and they reportedly account for 60 percent of all diamond transactions. The diamond trade accounts for $4 billion a year and 6 percent of Belgium's total exports. In the 1990s about 16.8 percent of all polished diamonds imported into the United States came from Belgium by weight of carats and 27.4 percent by value in dollars Antwerp accounts for over 40 percent of the world's diamond cutting and polishing and 60 percent of the trading of large diamonds. Many of the diamonds that originate in southern Africa pass through here on their way from the mines to the jewelry stores; arriving here as raw and uncut stones and leaving as marvelous multi-faceted gems. The first documented diamond deal in Antwerp was recorded in 1447 but the industry didn't take hold into the 19th century when Ashkenazi Jews arrived from Central Europe and built up the city's diamond exchange. The Jewish population of Antwerp dropped from 50,000 to 800 during the Holocaust. The trade for rough and polished stones revived after World War II but the crafts of cutting and polishing moved from Belgium to India, Thailand and Israel. The number of diamond workers declined from 19,000 in 1968 to less than 3,500 today.
Details
-
File Typepdf
-
Upload Time-
-
Content LanguagesEnglish
-
Upload UserAnonymous/Not logged-in
-
File Pages6 Page
-
File Size-