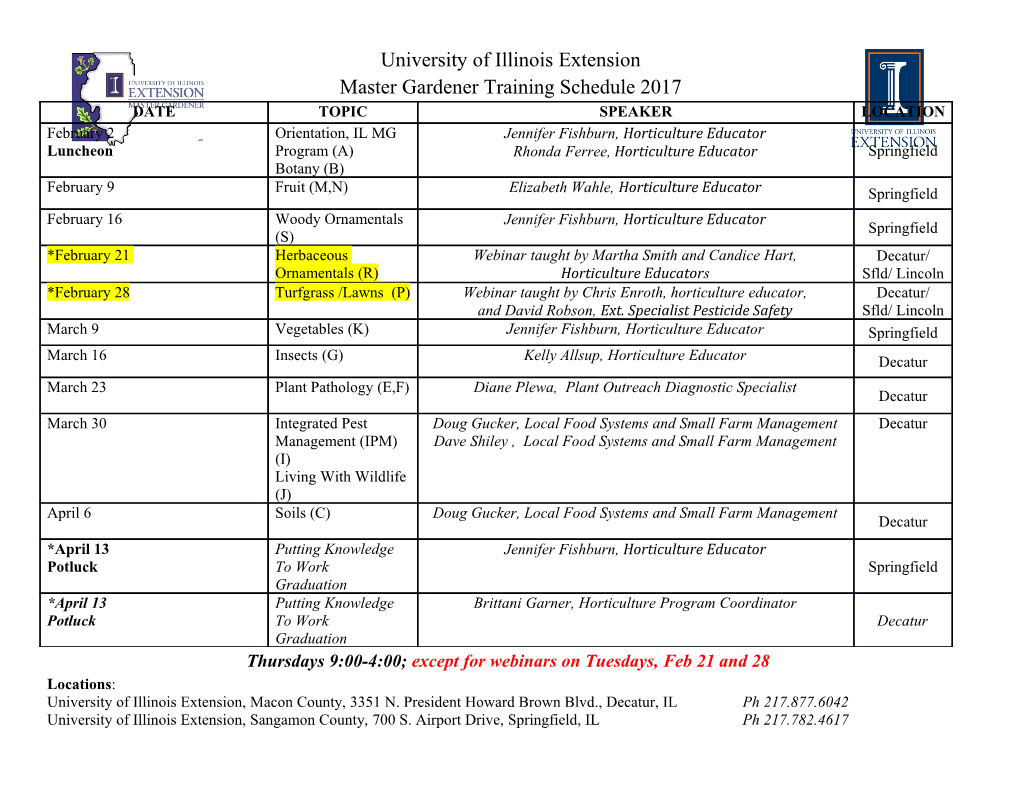
Design Verification – The Case for Verification, Not Validation Overview: The FDA requires medical device companies to verify that all the design outputs meet the design inputs. The FDA also requires that the final medical device must be validated to the user needs. When there are so many more design inputs and outputs than specific user needs, why do companies spend so little time verifying the device and so much time and money on validation? And what is the role of risk management in determining the amount of testing required? This presentation will demonstrate that if developers conduct more complete verifications of design outputs and risk mitigations, validations can be completed in a shorter time, more reliably, and more successfully. Introduction: In our experience working with medical device manufacturers to improve their Quality Management Systems and to gain regulatory clearance of new devices, we have found that Design Verification is an often underutilized tool for ensuring success during the latter stages of device development efforts. In many cases, limited verification efforts represent a lost opportunity to significantly reduce the scope of validation efforts – and thereby reduce time to market and development costs. This paper explores the use and misuse of Design Verification and how device manufactures can get the most out of their verification efforts. But first, some background . Background: Medical device manufacturers have been working to align their design and development systems with the FDA’s design control regulations (21 CFR 820.30) since their release in 1996. The regulations are structured to ensure that device manufacturers maintain control over their designs throughout the development process and that the marketed device is safe and effective for its intended use. At their most basic level, the regulations require that manufacturers: • Clearly state what they intend to produce (Planning and Design Inputs); • Develop a design that meets those needs (Design Outputs and Design Review); • Confirm that the design meets the original intent (Verification); • Confirm that manufactured product can be produced reliably and achieve the desired result (Transfer and Validation); and Page 1 of 12 MEDIcept, Inc. 200 Homer Avenue Ashland, MA 01721 May not be reprinted or copied without expressed permission from MEDIcept 11/2010 Design Verification – The Case for Verification, Not Validation • Maintain records of key development activities and decisions (Design Changes and Design History File) It would be hard to argue that any of these steps should be excluded from any development effort. Whether you are building a bridge, a cell phone, or a surgical tool, this combination of steps has a logical flow that most engineers would simply consider to be “good practice”. The challenge arises when you move from the conceptual world, where product development can be seen as single stream of water flowing down a hill: steadily moving from one point to the next without interuption; to the real world, full of rapids, eddies, branching streams, and (occasionally) deep pools of water that don’t seem to be moving at all. In this turbulent environment, it’s can be difficult to maintain a disciplined design approach – particularly when business schedules demand rapid progress and any delays in moving on to the next development phase risk affecting project milestones and development staff deployment plans. These challenges are multiplied when the device has multiple components and integration points that must be managed throughout the development process. Much has been written about the importance of early stage planning and problem solving to speed time‐to‐market and reduce development costs – and the value of clear Design and Development Plans and well‐defined Design Inputs cannot be overstated. An equal amount of attention has been focused on Design Transfer and Validation activities. At this late stage of a development effort, the project scope will have expanded to include more active involvement of Clinical, Operations and Marketing staff. In addition, the cost of validation studies and the “make or break” aspect of these studies require a great deal of attention and company resources. Problems at the validation stage will have serious implications for the success of the project and ‐ especially for small companies ‐ could determine the fate of the whole company. Compared to these early‐ and late‐stage activities, the importance of Design Verification tends to be overlooked. There are several reasons why: • Definitions: Many practitioners (and established Quality Systems) continue to have trouble defining exactly what “verification” is, and how it fits into the design control process. The term is often considered to be synonymous with “validation” ‐ and the development of combined “V&V” plans that do not establish a clear distinction between the objectives of the two efforts don’t help. [Note: when discussing verification with the FDA, it’s best not to talk about your “V&V plan” – increasingly, inspectors’ preferences are to address the two activities separately.] • Timeframe: Verification is often an ongoing effort conducted throughout the development of outputs. So, a great deal of time may pass between when the first and last output is verified. Page 2 of 12 MEDIcept, Inc. 200 Homer Avenue Ashland, MA 01721 May not be reprinted or copied without expressed permission from MEDIcept 11/2010 Design Verification – The Case for Verification, Not Validation With this extended timeframe, verification activities can get lost within all of the “churning” associated with developing final outputs. • Approaches: There are a variety of ways to complete the verification for an output, so it can be difficult to communicate that all of these activities, as a group, represent the design verification. The problem with this lack of attention is that it weakens a critical link in the design control “chain”, affecting the strength of the overall design control effort. Poor design verification can lead to problems during design transfer and validation, and can reduce your ability to track down and correct problems if (and when) they occur. Just as importantly, it may represent a lost opportunity to optimize validation activities, reduce time to market, and increase your overall confidence in the safety and efficacy of your products. Key Concepts: To make sure that we’re aligned on the proper use of the term “verification”, here are a few key points from the FDA’s Design Control Guidance For Medical Device Manufacturers: • Definition: Verification means confirmation by examination and provision of objective evidence that specified requirements have been fulfilled [§820.3(aa)]. • Types of Verification Activities: Verification activities are conducted at all stages and levels of device design. The basis of verification is a three‐pronged approach involving: tests, inspections, and analyses. Any approach which establishes conformance with a design input requirement is an acceptable means of verifying the design with respect to that requirement. In many cases, a variety of approaches are possible . the manufacturer should select and apply appropriate verification techniques based on the generally accepted practices for the technologies employed in their products. Table 1 provides some examples of the types of verification activities that device manufacturers often employ. Page 3 of 12 MEDIcept, Inc. 200 Homer Avenue Ashland, MA 01721 May not be reprinted or copied without expressed permission from MEDIcept 11/2010 Design Verification – The Case for Verification, Not Validation Table 1: Types of Verification Activities Tests Inspections Analyses o Material performance / o First article inspection o Worst case analysis of an fatigue tests o Comparison of a design to a assembly to verify that o Package integrity tests* previous product having an components are derated o Biocompatibility testing of established history of properly and not subject to materials* successful use* overstress during handling o Bioburden testing of products and use* to be sterilized* o Thermal analysis of an assembly to assure that internal or surface temperatures do not exceed specified limits* o Fault tree analysis of a process or design* o Failure modes and effects analysis* o Engineering analyses: o Finite Element Analysis (FEA) o Computational Fluid Dynamics (CFD) o Tolerance stack-up * Source: Design Control Guidance For Medical Device Manufacturers (1997) A key distinction between design verification and design validation activities is that verification only requires that a single unit be assessed. What constitutes that single unit will vary depending on the intent of the verification. It might be one batch of raw material (for material performance tests), one machined part (for first article inspection), on one package sample (for integrity tests). The intent of verification is to confirm that the design outputs (i.e., the materials or components specified in design documents) meet the design input requirements. Validations, on the other hand, require that studies be conducted to ensure that the device can be manufactured to meet design specifications on a consistent basis (i.e., process validation), and to ensure that the finished device is safe and effective for its intended purpose (i.e., design validation). For the process validation, multiple devices must be manufactured and evaluated to confirm that the production process is capable of producing devices
Details
-
File Typepdf
-
Upload Time-
-
Content LanguagesEnglish
-
Upload UserAnonymous/Not logged-in
-
File Pages12 Page
-
File Size-