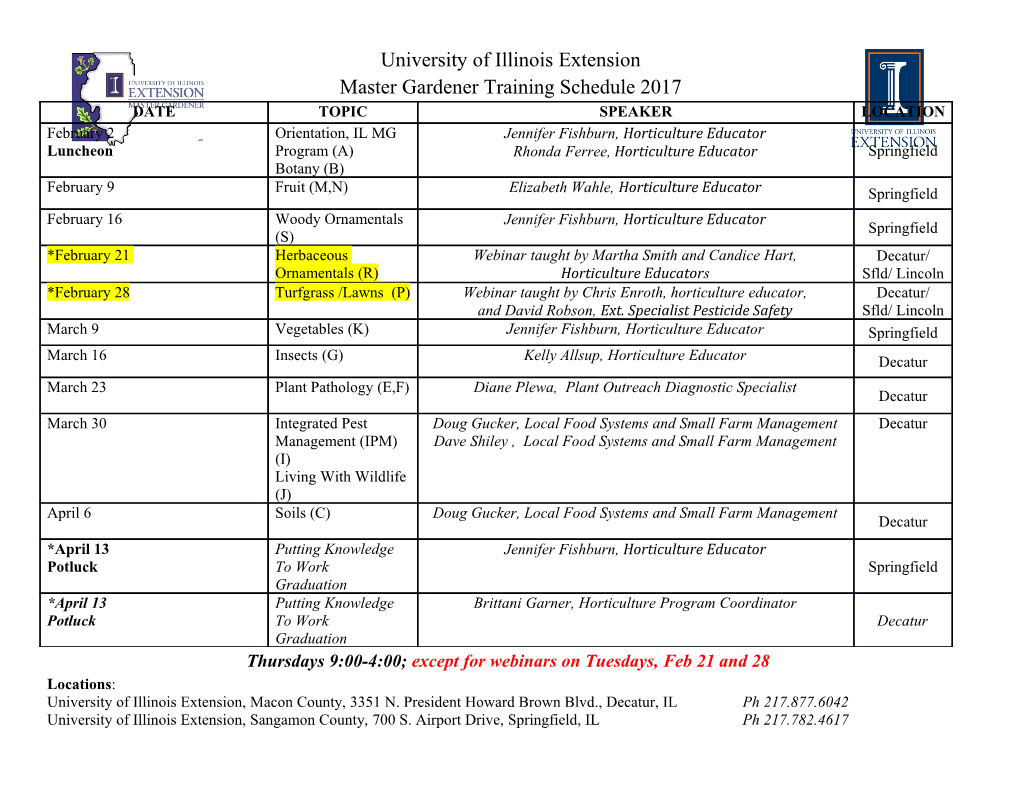
16 Nubuck Leather PRODUCT CODE : N.A. QUALITY AND STANDARDS : IS 8170 -1977 PRODUCTION CAPACITY : Quantity: 60,000 Pieces Value: Rs. 4,44,00,000 MONTH AND YEAR : January, 2003. OF PREPARATION PREPARED BY : Small Industries Service Institute 34, Industrial Estate, Nunhai, Agra-282006(U.P) Ph. No.: 381023 Fax: (0562) 3813287 E-mail: [email protected] INTRODUCTION shift of 8-hrs. a day and 25- working days in a month at 75% Nubuck leather is generally efficiency. manufactured from raw cowhide and 2. It is presumed that the capacity used for manufacturing of footwear utilisation will be 70% followed by articles, leather garments and leather 85% in the next year and 100% goods. Shoes, leather goods and leather in the subsequent year. garments are exported to different 3. The rates quoted in respect of countries to fulfil the global market. salaries and wages for skilled Nubuck leather is softer and has worker and others are on the attractive look. basis of minimum rates in the State Govts. MARKET POTENTIAL 4. Interest rate for the fixed and working capital has been taken @ There are a number of shoes, 15% on an average whether garments and goods manufacturing financed by the Bankers or units throughout the country which Financial Institutions. demand nubuck leather due to good export market for products made by 5. The margin money required is nubuck leather. minimum 30% of the total capital investment. BASIS AND PRESUMPTIONS 6. The rental value for the accommodation of office, workshop 1. The Project Profile has been and other covered area has been prepared on the basis of single taken @ Rs. 20 per sq. mtr. 96 NUBUCK LEATHER 7. The rate quoted in respect of IMPLEMENTATION SCHEDULE machineries, equipment and raw materials are those prevailing at The implementation of the project the time of preparation of the includes various jobs/exercises such as Project Profile and are likely to vary procurement of technical know how, from place to place and supplier to transfer of technology, market surveys supplier. When a tailor made project and tie-ups, preparation of project profile is prepared, necessary report, selection of site, registration, changes are to be made. financing of project, procurement of 8. The pay -back period may be 5- machinery and raw materials etc., years after the initial gestation recruitment of staff, erection/ period. commissioning of machines, trial production and commercial production 9. The gestation period in etc. In order to efficiently and implementation of the project successfully implement the project in the may be to the tune of 6 to 9 shortest period the slack period should months which includes making all be curtailed to minimum possible and arrangements, completion of all as far as possible simultaneous exercises formalities, market surveys and should be carried out. In view of above tie-ups etc. Once all the above a CPM-PERT Chart has been illustrated arrangements are made and below, according to which a minimum quality/standards achieved the period of 227 days is involved in finally 100% project capacity may be starting the project on commercial basis. achieved at the end of three years. By following this process a time period However, a detailed PERT/CPM/ of 82 days can be saved. chart with implementation period has been given in the report. 4 7 1 2 568101112 3 9 Details of Activities C.P.M. Activity Days Activity Days Particulars of Activity 1-2 15 1-2 15 Procurement of Tech. know how/ transfer of technology. 3-4 15 3-4 15 Market survey, tie up and obtaining quotations. 4-5 7 2-3 7 Selection of site. NUBUCK LEATHER 97 Activity Days Activity Days Particulars of Activity 5-6 70 4-5 7 Preparation of Project report 6-7 45 5-6 70 Registration and financing. 7-10 30 6-7 45 Placement of orders for machineries and receipt of machines. 10-11 30 6-8 30 Recruitment of staff and training 11-12 15 6-9 30 Addition/Alteration in rental premises 8-10 15 Procurement of raw material/Bought out components 7-10 30 Erection, Electrification and Commissioning 10-11 30 Trial Production 11-12 15 Commercial Production Total 227 309 TECHNICAL ASPECTS Slaked Lime 4% -6% Salt 2% Process of Manufacture The liming takes 18-20 hours, the drum is run for 2 –3 minutes every two Raw Material: Wet salted hair slip quality hours, rinsed in soft water for 10 cow hide of average weight 11-15 Kg. minutes, fleshed and scudded and limed each. weight is taken. Soaking: The hides are washed Deliming: The fleshed pelt is washed in thoroughly and soaked in a paddle running water in drum for 20 minutes containing the following chemicals : and drained out. The following chemicals Na2S 0.2% are taken on pelt weight: Water 400 –500% Water 250% (Percentage is taken on the raw weight) Ammonium Sulphate 1.2% to 1.7% The hides are kept in the paddle over Sodium bi Sulphate 0.4% to 0.6% night. Next morning the paddle is run for The drum is run for 30-40 minutes 30 minutes and checked for proper soaking and checked by phenolphthalein and and then washed in running water, test should show 20 –25 red or drained drained out and soaked weight is taken. out and washed thoroughly with 2 changes of water for 20 minutes then Liming: Liming is done in drum. The pelts are scudded. following chemicals are taken on soaked weight: Pickling: The pelts are pickled with the Water 300% following chemicals: Nitrogen LS 0.2% Water 70% Na2S5% Salt 5% 98 NUBUCK LEATHER Drum run for 10 minutes and then Sodium bicarbonate 0.7% add H2SO4 –1.5%. (dissolved The acid is diluted with water and 1:10) added in three instalments at an interval and drum run for 45 of 10 minutes and after last instalment minutes and pH should run the drum for 45 minutes. Checked be 4.5 –4.8 then add: the pH of pelt with bromophenol blue wattle extract powder 4% indicator which should be 2.8. Tanigun pR –(Buyer) 1% Chrome Tanning: Half of the pickle liquor Chestnut extract powder 1% (pelt) is drained out and the hide is run Drum run for 45 Minutes then drain for 15 minutes then add: only and rinse for 5 minutes. Basic Chrome Powder 7% Dyeing and Fat Liquoring: Sodium Acetate 0.5% Acid dye in powder 3% Soda Ash 0.3% Drum run for 25 100% Chemicals are fed in two instalments minutes and then at the interval of 15 minutes and drum add water run for further 2 ½ hours, pH 3.8 –4.0 pile up over night and next day samming Drum run for 20 6% and setting, splitting, shaving, to 1.3 – minutes and then add: 1.4 mm. These shaved leathers are Soundozal KB washed for 10 minutes in warm water Drum run for 1 hour 0.5% 30–35ºC. and then Add: Formic Acid – Retanning: Basic Chromium 3% (diluted 1:10) Sulphate (33%) Drum run for 20 1.1% Sodium formate 0.5% minutes and then add: Drum run for 10 2% Taffuilon 218 A minutes then add Drum run for 20 minutes and then Cationic fat liquor horse up. The leathers are sammed, set Drum run for 1 hour 2% out, saw dusted, staked, toggled, buffed then add sodium formate on grain with 400 grit emery paper and brushed off. Process Flow Chart 1. Soaking 2. Liming 3. Fleshing 4. Deliming 5. Bating 10. Splitting 7. Chrome 9. Piling 8. Basification 6. Pickling & Buffing Tanning 11. Retanning 12. Dyeing & Fat liquoring NUBUCK LEATHER 99 Production Capacity multiplied when CFLEBs are used Quality : 60,000 Cow hides in air conditioned areas, since the saving of energy by using CLEBs Value : Rs. 4,44,00,000 also corresponds to less heat Quality Control and Standards dissipation reducing load on air conditioners. The life of CFLEBs Indian standard specification IS is about 8000/10000 hours i.e. 8170:1977 is used in maintaining about 10 times that of ordinary bulb. standards for cow nubuck leather The typical pay-back period in Motive Power 130 HP. terms of savings of energy bills and cost of ordinary lamps is Water : Rs. 1000 about 6 months operation. Unlike ordinary bulbs, these CFLEBs Energy Conservation provide choice of three colours The following steps may be taken for designated A, B and C, to suit the conservation of energy: individual requirements. 1. Machinery and Equipment’s parts Electronic Ballast, with which are revolving and protection against high voltage reciprocating should be properly spikes, along with high quality lubricated from time-to-time with CFLs make these composite suitable lubricant oil. CFLEBs (or self ballasted CFLs) 2. Lay out of the unit should be in Slim, light weight, efficient and such a way in that no back reliable units. tracking of material is there. 6. As far as possible Solar Energy 3. All electric switches may be kept and day light will be used keeping off, when not required. all the other lights off. 4. The entire transmission belt will 7. As far as possible inductive load be tightened before starting the of motor will be reduced and high work, wherever applicable. power factor will be used with the 5. Fluorescent tube with electronic aid of capacitors of appropriate sizes. Chokes may be used for energy Pollution Control saving. Further recently developed compact fluorescent tubes The unit requires an effluent called(CFT) of 10,15, watts Treatment Plant of its own which involves Philips/Glaux made may be used the following main operation In general for energy saving and decoration.
Details
-
File Typepdf
-
Upload Time-
-
Content LanguagesEnglish
-
Upload UserAnonymous/Not logged-in
-
File Pages9 Page
-
File Size-