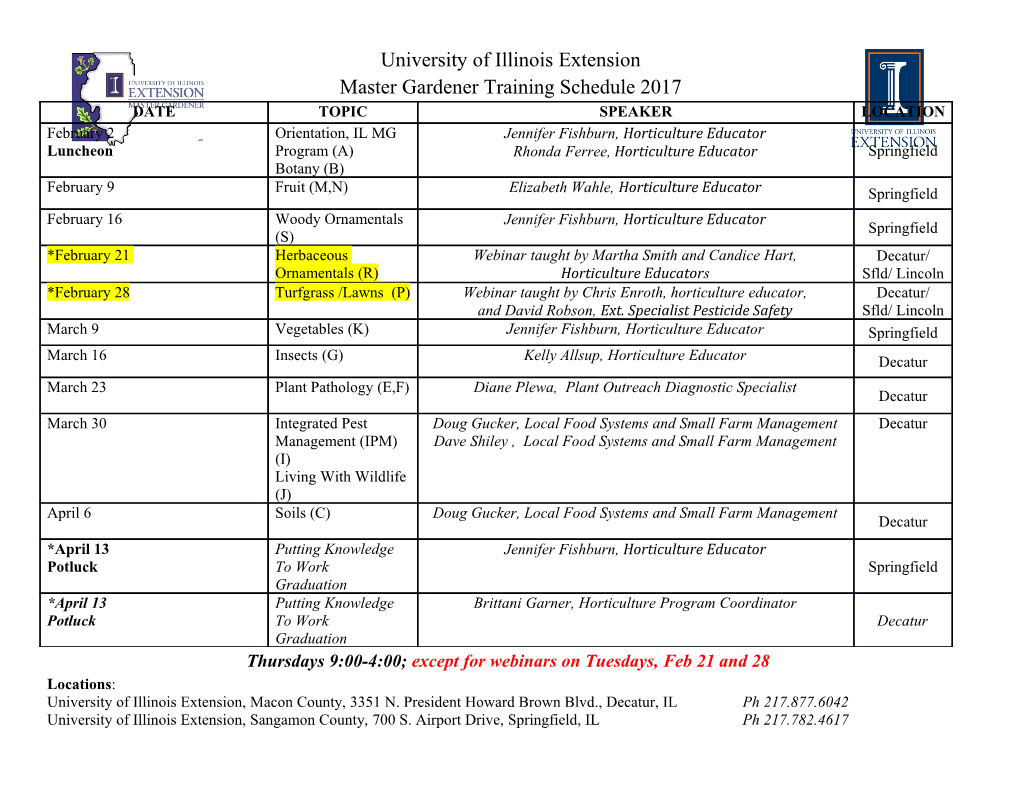
J Wood Sci (2007) 53:470–480 © The Japan Wood Research Society 2007 DOI 10.1007/s10086-007-0889-5 ORIGINAL ARTICLE Rashmi Kumari · Hirokazu Ito · Masahiro Takatani Miho Uchiyama · Tadashi Okamoto Fundamental studies on wood/cellulose–plastic composites: effects of composition and cellulose dimension on the properties of cellulose/PP composite Received: September 6, 2006 / Accepted: February 9, 2007 / Published online: May 29, 2007 Abstract Although wood/cellulose–plastic composites Introduction (WPC) of low wood/cellulose content have been more ac- cepted worldwide and are promoted as low-maintenance, high-durability building products, composites containing In recent years, interest in composites based on renewable high wood/cellulose content are not yet developed on an materials has grown tremendously because of social re- industrial scale. In this study, fl ow properties, mechanical quests for low environmental stress, low-maintenance and properties, and water absorption properties of the com- high-durability products, and ultraviolet (UV) durability.1–3 pounds of cellulose microfi ber/polypropylene (PP) and Construction, transportation, industrial, and consumer ap- maleic anhydride-grafted polypropylene (MAPP) were in- plications for wood/cellulose–plastic composites (WPC) are vestigated to understand effects of the high cellulose con- all on the rise. WPC have been primarily produced with a tent and the dimensions of the cellulose microfi ber. The low and medium percentage of wood/cellulose. Products molding processes studied included compression, injection, typically contain approximately 50% (by weight) wood/ and extrusion. It was found that fl uidity is not only depen- cellulose, although some composites contain very little dent on resin content but also on the dimension of the fi ller; wood/cellulose and others as much as 60%.1,4–7 Wood/ fl uidity of the compound declined with increased fi ber cellulose content may range from 70% to 90% and the length with the same resin content. Dispersion of the interfacial adhesion between wood/cellulose particles and composite was monitored by charge-coupled device (CCD) polymers can be improved by adding a compatibilizer. microscope. Increasing the plastic content in the cellulose– One of the major challenges for WPC is to optimize the plastic formulation improved the strength of mold in addi- content of the wood/cellulose in WPC to reduce costs and tion to the bond development between resin and fi ller, compete with solid wood and engineered wood composite and the tangle of fi bers. The processing mode affected the products. physicomechanical properties of the cellulosic plastic. Cellulose, one of the basic structural components of Compression-molded samples exhibited the lowest modu- wood fi bers, has great potential for the preparation of novel lus of rupture (MOR) and modulus of elasticity (MOE) and composite materials with thermoplastic resins. However, the highest water absorption, while samples that were injec- the highly polar nature of the cellulose surface does not tion-molded exhibited the highest MOR (70 MPa) and lend itself to strong interactions with the nonpolar polymer, MOE (7 GPa) and low water absorption (2%). such as polypropylene (PP).8,9 Various fi ber surface com- patibilizers have been reported, such as silane, alkali, com- Key words Cellulose–plastic composite · Compression · bination of alkali and silane, monomer grafting under UV Extrusion · Injection molding · High wood content radiation, maleic anhydride-grafted polypropylene, and others.8–11 Among these treatments, coupling agent maleic anhydride-grafted polypropylene (MAPP) has been found to be the most effi cient in improving the mechanical proper- ties of cellulose composite materials. R. Kumari · M. Takatani · M. Uchiyama · T. Okamoto (*) However, extruded WPC are a relatively new product Department of Applied Bioscience, Graduate School of Agriculture, for which market growth has been rapid. The engineering Kinki University, Nakamachi, Nara 631-8505, Japan design of extrusion operations requires proper knowledge Tel. +81-74-243-7383; Fax +81-74-243-8976 e-mail: [email protected] of the fl ow mechanism of these highly fi lled melts. The WPC formulations also require reliable evaluation of fl ow perfor- H. Ito Material Developing Section, Product Developing Department, mance of the composite melts. Rheological characterization Yamaha Livingtec Corporation, Hamamatsu 432-4001, Japan affords knowledge about both the fundamental fl ow behav- 471 Table 1. Basic properties of all cellulose powders Cellulose Color Structure Fiber length Fiber diameter Bulk density (mm) (mm) (g/l) BE00 White Short fi ber 120 20 150–180 BC200 White Medium fi ber 300 20 60–80 B400 White Long fi ber 900 20 20–40 ior of the highly fi lled plastics and practical methods for Table 2. Composition of cellulose powder, polypropylene (PP), and evaluating the fl ow performance for process development. maleic anhydride-grafted polypropylene (MAPP) The technical challenges are to overcome fl ow problems, No. Composition (%, w/w) the low bulk density of the wood/cellulose as well as separa- tion problems of the composite mixture. Therefore, advanc- Cellulose PP MAPP ing this area of knowledge for this new material class is BE00 BC200 B400 PM930V UMEX1010 important for further developments of the science and industry.4,12–14 1 80 18 2 2 70 28 2 In this article, a study of the properties of composites 3 80 18 2 made of cellulose microfi bers and random PP is reported. 4 90 8 2 Composites prepared with different fi ber lengths of cellu- 5 80 18 2 lose and with the different content (70%, 80% and 90%) were studied. A study on the mechanical and water absorp- tion of compression-, extrusion-, and injection-molded com- compression molding. Extruded strands were also pellet- posites is presented here. Melt fl ow characteristics such as ized and the temperatures from cylinder 1 to cylinder melt index, have been studied with special reference to the 4 were decreased from 230° to 180°C. Pellets were used effect of blend ratio, cellulose fi ber length, temperature, for extrusion-molding and injection-molding composites. and diameter of die hole. The effect of the different fi ber Crushed pellets used for injection samples were also pre- length and content of cellulose on the morphology and wa- pared with the addition of 2% (w/w) calcium stearate as a ter absorption of the composites is discussed. Finally, our lubricant. The compositions of cellulose powder, PP and ultimate aim is to make clear the possibility of the prepara- MAPP are listed in Table 2. tion of composites with very high wood/cellulose content. Molding process Experimental Three molding processes commonly used for thermoplastics Materials were used to make test specimens of cellulose/PP/MAPP for studying the effect of molding on the physicomechanical The materials used in this study were cellulose, a thermo- properties of the corresponding cellulosic plastics. plastic polymer, polypropylene (PP), and the coupling agent MAPP, which is polypropylene modifi ed with maleic acid. Compression molding The thermoplastic polymer was a random PP (PM930V, MFI 30 g/10 min, density 0.9 g/cm3) supplied by SunAllomer The specimens for mechanical tests were prepared by com- (Tokyo, Japan). Three different shapes and sizes of fi brous pression molding with an oil hydraulic press HP-1B-P cellulose (BE00, BC200, B400) were products of Retten- (method A) at 200°C. Other press conditions were set maier and Söhne (Rosenberg, Germany), produced from to provide the best opportunity to reach the theoretical softwood. The basic properties of all the cellulose powders density. The theoretical density was calculated on the basis are listed in Table 1. The coupling agent was MAPP of weight percent and the density of components. (umex1010) obtained from Sanyo Kasei (Tokyo, Japan). Specimens were cut from the sheets of the cutter mill compound molded by method A (AC) and the hammer mill Blending procedure compound molded by method A (AH). The blends were also compression-molded using a steel mold (mold dimen- The cellulose fi bers, PP, and MAPP were sequentially fed sions 1 × 8 × 10 cm) by a Shinto hot press model HCC-BSN- into a conical twin-screw extruder (Model Taitan 80, Cin- 2 (method B) at 220°C and 11 MPa for 5 min, before being cinnati). The temperature profi le of the extruder from cyl- cooled to room temperature. Tefl on fi lms were used to inder 1 through cylinder 4 was kept between 230° and 180°C avoid the adhesion of MAPP to the stainless surface of the and the extruder was operated at a screw speed of 7 rpm. mold. Twelve standard specimens (dimensions 1 × 2.5 × After compounding, the composite was then crushed into a 10 cm3) were cut from the sheets of the cutter mill sample cutter mill (wood grinder) or hammer mill and used for molded by method B (BC). 472 Table 3. Molding conditions of injection mold No.a Lubricant (%) Injection time (s) Nozzle Peak pressure temperature (°C) (MPa) 1 IX 0 0.29 210 29.6 IO 2 0.30 195 29.4 2 IX 0 0.57 185 22.7 IO 2 0.60 185 23.9 3 IX 0 0.29 210 29.5 IO 2 0.31 195 29.5 IX, injection mold without lubricant; IO, injection mold with lubricant a Same as in Table 2 Extrusion molding Water absorption test Pellets were extruded as thick long sheets in this process. The samples based on increasing fi ber length, diameter, and Pellets were fed into a conical twin-screw extruder (Titan cellulose content of compression molding were tested for 68, Taiyo Gosei, Kagawa, Japan). The molding conditions water absorption for 0 to 24 h under atmospheric pressure were as follows: temperatures on cylinder 1 to cylinder 4 at room temperature. Water absorption in weight gain (Wt), were held between 215° and 170°C and the temperature of and thickness gain (Th) were calculated by Eqs.
Details
-
File Typepdf
-
Upload Time-
-
Content LanguagesEnglish
-
Upload UserAnonymous/Not logged-in
-
File Pages11 Page
-
File Size-