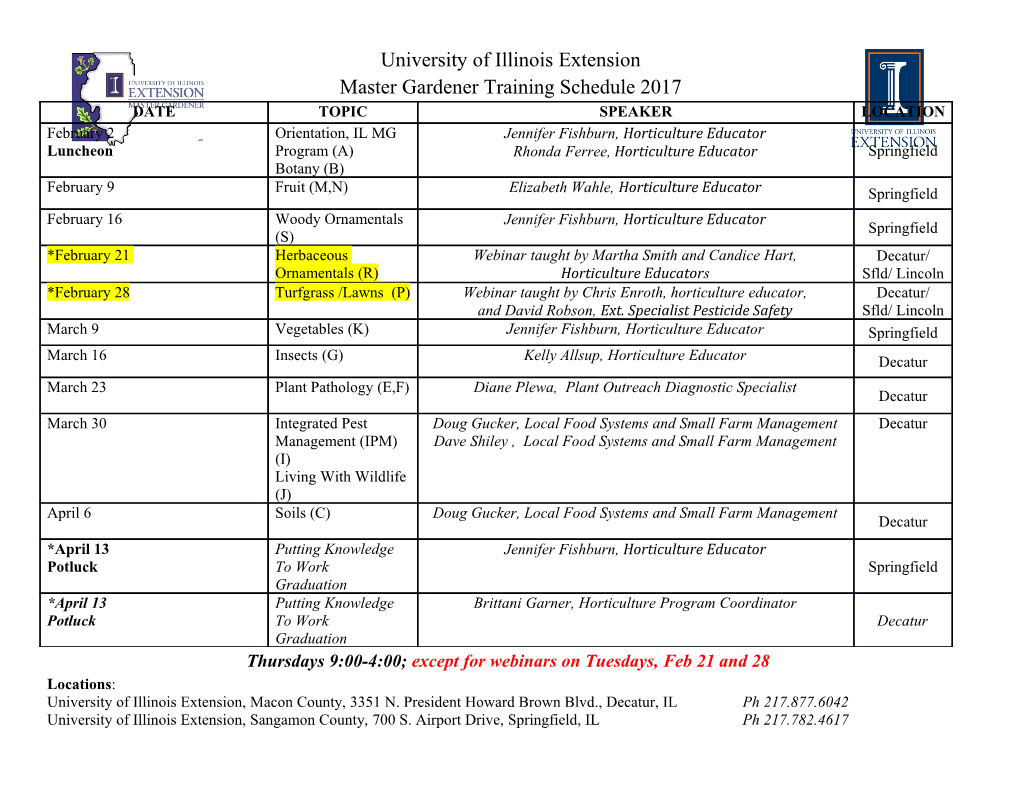
Rochester Institute of Technology RIT Scholar Works Theses 8-1-1983 A constant force bicycle transmission Thomas Chase Follow this and additional works at: https://scholarworks.rit.edu/theses Recommended Citation Chase, Thomas, "A constant force bicycle transmission" (1983). Thesis. Rochester Institute of Technology. Accessed from This Thesis is brought to you for free and open access by RIT Scholar Works. It has been accepted for inclusion in Theses by an authorized administrator of RIT Scholar Works. For more information, please contact [email protected]. A CONSTANT FORCE BICYCLE TRANSMISSION by Thomas R. Chase A Thesis Project Submitted in Partial Fulfillment of the Requirements for the Degree of MASTER OF SCIENCE in Mechanical Engineering Approved by: Prof. Richard Budynas Thesis Adviser Prof. Dr. Bhalchandra V. Karlekar Department Head Prof. '"egible Signature Prof. Ray C. Johnson DEPARTMENT OF MECHANICAL ENGINEERING ROCHESTER INSTITUTE OF TECHNOLOGY ROCHESTER, NHJ YORK August 1983 A CONSTANT FORCE BICYCLE TRANSMISSION ABSTRACT A prototype design for a human powered automatic transmission intended for use on an ordinary touring bicycle is presented. The transmission is intended to automatically adjust the gearing of the bicycle to maintain an optimum pedal force, regardless of the current riding conditions. Therefore, the transmission eliminates the need for the cyclist to manually adjust the bicycle gearing. The entire transmission is a self-contained unit designed to bolt onto the rear wheel of an otherwise unmodified 27-inch bicycle. The transmission combines a unique adaptation of a commercially popular continuously variable traction drive with a totally mechanical integral feedback controller. The features of the traction drive unique to its application to a bicycle are outlined in detail, along with an analysis of the important traction drive design parameters. The control system is also uniquely adapted to the requirements of bicycling. A detailed classical analysis of the controller is pre sented to verify its desirable performance characteristics. In addi tion, a numerical simulation of the transmission is included to accurately predict its performance under typical operating condi tions. A knowledge of typical pedal force profiles for normal touring cycling is prerequisite for the design of the constant force bi cycle transmission. This data has not been previously published. n An instrumentation package was developed especially to determine this data. A description of the system and a summary of the results are presented. These results are reduced to a set of design criteria for the constant force transmission. Table of Contents Abstract i List of Symbols 1 1. Introduction 7 1.1) Scope 7 of 1.2) History the Constant Force Bicycle Transmission . 9 1.3) History of the Pedal Data Instrumentation 12 1.4) Summary 15 2. Overview of the Constant Force Bicycle Transmission ... 16 2.1) Introduction 16 2.2) Continuously Variable Transmission Overview 16 2.3) Control System Overview 19 2.4) Additional Features 28 3. Pedal Data Instrumentation 31 3.1) Introduction 31 3.2) System Overview \ . 31 3.3) Pedal Force Sensor 35 3.4) Pedal Position Sensor 48 3.5) Frequency to Voltage Converter 53 4. Design Criteria for the Constant Force Bicycle Transmission 60 4.1) Introduction 60 4.2) Overview of the Test Data 60 i i i IV 4.3 Estimated Pedal Crank Velocity. 63 4.4 Pedal Force Profile 64 4.5 Estimated Ideal Pedal Force . 65 4.6 Design Maximum Pedal Force. 68 4.7 Estimated Loading Schedule. 71 The Continuously Variable Transmission 75 5.1 Introduction 75 5.2 Principle of Operation 76 5.3 Unique Characteristics of the Constant Force Bicycle Transmission CVT 80 5.4) CVT Analysis 91 5.4.1) Worst-Case Tractive Force Requirements . 91 5.4.2) Derivation of the Traction Ball Normal Force 93 5.4.3) Traction Fluid Performance 99 5.4.4) Maximum Stress in the CVT 102 5.4.5) Transmission Life Estimate 105 The Constant Force Controller 106 6.1 Introduction 106 6.2 Principles of Operation 107 6.3 Basic Modelling of the Constant Force Controller. 113 6.4 Shift Torque Requirements 118 6.5 Modelling the Control System Input 123 6.6 Numerically Modelling the Constant Force Controller 128 6.7 Simulation of the Control System Performance. 132 6.8 Linear Model of the Constant Force Controller . 153 -V- 6.9) Frequency Response Analysis of the Constant Force Controller 164 7. Conclusion 173 Acknowledgments 176 Bibliography 177 Appendix: Constant Force Controller Simulation Program . .180 List of Symbols c-j : Chain reduction between the output of the continuously variable transmission and the rear wheel of the bicycle c- : Total chain reduction between the pedal crank and the input of the continuously variable transmission c- : Total geardown between the integrator driven wheel, a, and the traction ball shift angle, e c. : Leverage of the floating traction ball lever f : Frequency of the sinusoidal input force from the pedal crank (hz) F : A general force (lb) f : Corner frequency of the constant force controller (hz) Fp : Force in the chain driving the input sprocket of the continuously variable transmission (lb) FCR : Normal force of a traction ball against a cradle bearing of the continuously variable transmission (lb) FD : Peak value of the ideal pedal force (lb) F. : Normal force between the integrator driving disc and the integrator driven wheel (lb) FN : Normal force of a traction ball against the input or output disc of the continuously variable transmission (lb) Fp : Pedal force (lb) -1- -2- fpp : Output frequency of the pedal position sensor instrumen tation (hz) Fg : Sum of the forces in the two springs of the chain force sensor linkage (lb) F__t : Force in the equivalent spring (with spring constant k ) of the force sensor linkage when the force sensor linkage displacement, y, is zero (lb) F-.R : Tractive (frictional) force between the traction ball and the input or output disc of the continuously variable transmission (lb) F,, : Total wedging force of a traction ball into the input and output discs of the continuously variable transmission (measured in the plane parallel to the input and output discs) (lb) G : Transfer function of the constant force controller K : Gain of the constant force controller of parallel chain k . : Actual spring constant of each the two act force sensor linkage springs (lb/in.) k : Equivalent spring constant of the two parallel chain eq force sensor linkage springs acting through the chain force sensor linkage (lb/in.) M.A. : Mechanical advantage of the chain force sensor linkage balls rb : Spherical radius of the traction (in.) -3- : Radius of the rdisc input or output disc of the continuously variable transmission at the point of contact with the traction ball (in.) ri : Radius of the integrator driven wheel (in.) r-jn : Radius from the axis of rotation of the traction ball to the point of contact with the input disc (in.) rout : Radius from the axis of rotation of the traction ball to the point of contact with the output disc (in.) rpc : Length of the pedal crank (in.) rSCVT : Pitch radius of the input sprocket of the continuously variable transmission (in.) s : A complex number t : Time (sec) T : Period of the pedal crank rotation (sec) T : Time constant of the constant force controller (sec) TDW : Torque developed by the integrator driven wheel (lb-in.) T. : Input torque to the continuously variable transmission (lb-in.) : Constant torque value for T T-_v f (lb-in.) -4- Tout : Output torque from the continuously variable transmission (lb-in.) Tref : Function describing the peak value of the sinusoidal torque required to drive the rear wheel of the bicycle (lb-in.) TRW : Torque required to drive the rear wheel of the bicycle (lb-in.) Tshl.ft : Torque required to change the shift angle of a traction ball of the continuously variable transmission (lb-in.) T"w : Input torque to a worm gear of the continuously variable transmission (lb-in.) Tw . : Output torque from a worm gear of the continuously variable transmission (lb-in.) response of model of constant force Too/ I,---- 2% time the linear the .c/d, ii near controller to a true step input (sec) x : Input function to the linear model of the constant force controller (lb) X : Magnitude of the sinusoidal input function to the linear model of the constant force controller (lb) y : Chain force sensor linkage displacement; i.e., the relative displacement between the center of the integrator driving disc and the center! ine of the integrator driven wheel (in.) ymax : The maximum allowable displacement of the chain force sensor linkage (in. ) a : Angular displacement of the integrator driven wheel (rad) y : Angular displacement of the right pedal crank from top dead center (rad) n : Efficiency of the worm gears of the continuously variable transmission e : Shift angle of the continuously variable transmission (rad, deg) : state shift angle of the variable ecc3SS Steady continuously transmission (deg) y. : Coefficient of friction between the integrator driving disc and the integrator driven wheel u : Maximum assumed value of the coefficient of friction of nriax the traction fluid of the continuously variable transmis sion traction u . : Minimum permissible coefficient of friction of the mm fluid of the continuously variable transmission a : Compressive stress (lb/in.2) function to the linear w : Frequency of the sinusoidal input model of the constant force controller (rad/sec) -6- : Corner fc>c frequency of the constant force controller (rad/sec) to . : Angular -i velocity of the integrator driving disc (rad/sec) : An9ular pedal velocity of the pedal crank (rad/sec) Chapter 1 1. Introduction 1 . 1 ) Scope The prototype design for a constant force bicycle transmission is presented here. The constant force transmission is a human powered automatic transmission intended for use on an ordinary 27 inch touring bicycle.
Details
-
File Typepdf
-
Upload Time-
-
Content LanguagesEnglish
-
Upload UserAnonymous/Not logged-in
-
File Pages216 Page
-
File Size-