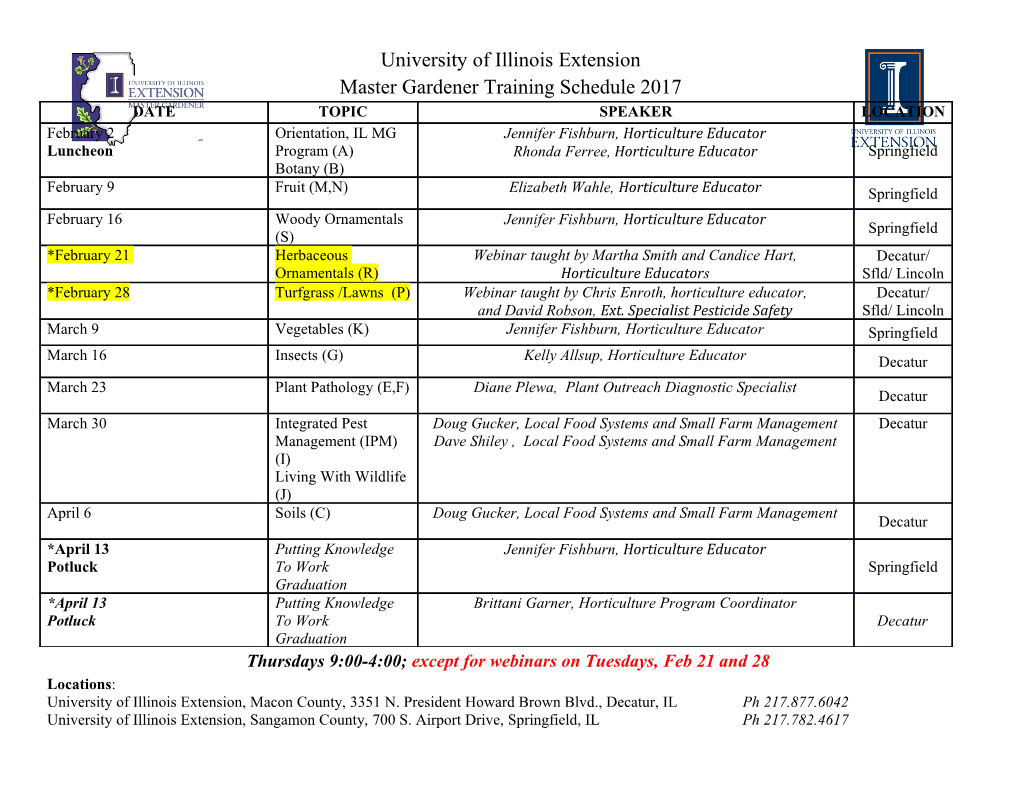
Characterization and Modeling of a High Power Thin Disk Laser by Omar R. Rodriguez B.S. University of Central Florida, 2008 A thesis submitted in partial fulfillment of the requirements for the degree of Master of Science in the School of Electrical Engineering and Computer Science in the College of Engineering and Computer Science at the University of Central Florida Orlando, Florida Summer Term 2010 Major Professor: Martin C. Richardson ABSTRACT High power lasers have been adapted to material processing, energy, military and medical applications. In the Laser Plasma Laboratory at CREOL, UCF, high power lasers are used to produce highly ionized plasmas to generate EUV emission. This thesis examines the quality of a recently acquired high power thin disk laser through thermal modeling and beam parameter measurements. High power lasers suffer from thermally induced issues which degrade their operation. Thin disk lasers use an innovative heat extraction mechanism that eliminates the transverse thermal gradient within the gain medium associated with thermal lensing. A thorough review of current thin disk laser technology is described. Several measurement techniques were performed on a high power thin disk laser. The system efficiencies, spectrum, and temporal characteristics were examined. The laser was characterized in the far-field regime to determine the beam quality and intensity of the laser. Laser cavity simulations of the thin disk laser were performed using LASCAD. The induced thermal and stress effects are demonstrated. Simulated output power and efficiency is compared to those that have been quantified experimentally. ii To my family. iii ACKNOWLEDGMENTS The culmination of this thesis represents a step in my life which I could not have ac- complished without the help of many people. I foremost thank my advisor, Dr. Martin Richardson, for all of the many opportunities he has provided and his invaluable guidance and advice. I also wish to thank my committee members Dr. Aravinda Kar and Dr. Peter Delfyett for their valuable time in reading this thesis. I thank Dr. Lawrence Shah for his advice and many intuitive and constructive conversations. I give my honest gratitude to my peers in the EUV group: Reuvani Kamtaprasad, John Szilagyi, and Nathan Bodnar for valuable ideas that helped me finish my thesis. Many thanks to Somsak (Tony) Teerawattanasook for his help on many occasions. I am also grateful to the rest of my colleagues from the Laser Plasma Laboratory at UCF for advice, equipment, and contributions to my work. I would like to express my gratitude towards several employees at TRUMPF GmbH +Co. KG, including Christian Stolzenburg, Wolfgang Schuele, and Dr. Sascha Weiller from Trumpf Laser GmbH and Thomas Osesek from Trumpf Inc. The provided training and assistance with several matters regarding the laser system was a major contribution to this work. iv I would also like to thank to Matthias Wohlmuth (University of Erlangen-Nuremberg) and Dr. Konrad Altmann (LAS-CAD GmbH) for their invaluable assistance and contributions to my work consisting LASCAD simulations. My final recognition goes to my family. Thank you for your motivation, inspiration and for believing in me. v TABLE OF CONTENTS LIST OF FIGURES :::::::::::::::::::::::::::::::::: x LIST OF TABLES ::::::::::::::::::::::::::::::::::: xii LIST OF ACRONYMS :::::::::::::::::::::::::::::::: xiii CHAPTER 1 : INTRODUCTION ::::::::::::::::::::::::: 1 CHAPTER 2 : THE THIN DISK LASER :::::::::::::::::::: 5 2.1 Solid State Lasers . .5 2.1.1 Pumping Schemes . .5 2.1.2 Laser Resonator . .7 2.1.3 Pulse Generation . .9 2.1.4 Architecture . 11 2.2 Gain Media . 15 2.2.1 Gain Requirements . 15 2.2.2 Yb:YAG . 16 vi 2.3 Technology . 24 2.3.1 Thermal Management . 24 2.3.2 Pumping . 26 2.3.3 Laser Resonator . 29 CHAPTER 3 : TRUMPF TRUMICRO 7050 SETUP ::::::::::::: 30 3.1 Cavity Design . 30 3.2 Pumping Scheme . 30 3.3 Thin Disk Design . 31 3.3.1 Disk Enclosure . 34 3.3.2 Cooling Finger . 34 3.4 Pulse Generation . 36 3.4.1 Cavity Dumping . 36 3.5 System Design . 40 3.5.1 Electrical System . 40 3.5.2 Control System . 40 3.5.3 Thermal Managment . 41 3.5.4 Humidity Control System . 41 CHAPTER 4 : LASER CHARACTERIZATION :::::::::::::::: 43 vii 4.1 Continuous Wave Operation . 43 4.1.1 Intracavity Power . 44 4.1.2 Polarizer Output Coupling . 45 4.2 Pulsed Operation . 46 4.2.1 Energy Output . 46 4.2.2 Average Power . 47 4.2.3 Pulse Duration . 48 4.2.4 Peak Power . 50 4.3 Beam Quality . 50 4.3.1 Measurement Technique . 52 4.4 Spectral Characterization . 54 4.5 Laser Intensity . 55 4.5.1 Brightness . 55 4.5.2 Intensity . 57 4.6 Improvements . 58 4.6.1 Damage Thresholds . 58 CHAPTER 5 : LASER MODELING :::::::::::::::::::::::: 59 5.1 LASCAD . 59 viii 5.1.1 Finite Element Analysis . 60 5.1.2 Laser Power CW . 61 5.1.3 Beam Propagation . 62 5.1.4 Dynamic Multimode Analysis . 63 5.2 Design . 63 5.2.1 Cavity Layout . 63 5.2.2 Pumping Technique . 64 5.3 Results . 65 5.3.1 Finite Element Analysis . 65 5.3.2 Laser Power CW . 68 CHAPTER 6 : CONCLUSION ::::::::::::::::::::::::::: 69 6.1 Future Work . 70 APPENDIX A :Copyright Permission Letter :::::::::::::::::: 71 LIST OF REFERENCES ::::::::::::::::::::::::::::::: 73 ix LIST OF FIGURES Figure 2.1 Laser Resonator Stability Criterion Plot :::::::::::::::::: 8 Figure 2.2 Energy Levels :::::::::::::::::::::::::::::::: 17 Figure 2.3 Yb:YAG Energy Levels ::::::::::::::::::::::::::: 18 Figure 2.4 Yb:YAG Cross Section Spectra ::::::::::::::::::::::: 19 Figure 2.5 Thin Disk Cooling Configuration :::::::::::::::::::::: 25 Figure 2.6 Thin Disk Multiple Pass Pumping ::::::::::::::::::::: 27 Figure 3.1 Trumpf TruMicro 7050 Cavity Layout ::::::::::::::::::: 31 Figure 3.2 Trumpf TruMicro 7050 Laser Cavity :::::::::::::::::::: 32 Figure 3.3 Trumpf TruMicro 7050 Pump Laser Diodes :::::::::::::::: 33 Figure 3.4 Trumpf TruMicro 7050 Disk Fluorescence ::::::::::::::::: 34 Figure 3.5 Trumpf TruMicro 7050 Pump Laser Diodes :::::::::::::::: 35 Figure 3.6 Trumpf TruMicro 7050 Cavity Dumping Timing Diagram :::::::: 37 Figure 3.7 Trumpf TruMicro 7050 Pockels Cell :::::::::::::::::::: 38 Figure 4.1 Trumpf TruMicro 7050 CW Efficiencies :::::::::::::::::: 44 x Figure 4.2 Trumpf TruMicro 7050 Energy Output :::::::::::::::::: 47 Figure 4.3 Trumpf TruMicro 7050 Pulsed Efficiencies ::::::::::::::::: 48 Figure 4.4 Trumpf TruMicro 7050 Pulse Duration at Various Frequencies ::::: 49 Figure 4.5 Trumpf TruMicro 7050 Pulse :::::::::::::::::::::::: 50 Figure 4.6 Trumpf TruMicro 7050 Peak Powers :::::::::::::::::::: 51 Figure 4.7 Trumpf TruMicro 7050 Beam Measurement Technique :::::::::: 53 Figure 4.8 Trumpf TruMicro 7050 Far-Field Beam Profiles at 20% Pump Power :: 55 Figure 4.9 Trumpf TruMicro 7050 Far-Field Beam Profiles at 50% Pump Power :: 56 Figure 5.1 LASCAD Cavity Configuration ::::::::::::::::::::::: 64 Figure 5.2 Thin Disk Thermal Visualizations ::::::::::::::::::::: 66 Figure 5.3 Thin Disk Structural Effects Visualizations :::::::::::::::: 67 Figure 5.4 Measured vs Simulated Efficiencies ::::::::::::::::::::: 68 xi LIST OF TABLES Table 2.1 Comparison of Different Thin Disk Laser Gain Media's Characteristics at Room Temperature :::::::::::::::::::::::::::::::::::: 23 xii LIST OF ACRONYMS AOM | Acousto-Optic Modulator AR | Anti Reflective ASE | Amplified Spontaneous Emission BBO | Beta Barium Borate CW | Continuous Wave DI | Deionized EM | Electromagnetic EOM | Electro-Optic Modulator EUV | Extreme Ultraviolet FWHM | Full Width at Half Maximum HEPA | High Efficiency Particulate Absorbing HeNe | Helium-Neon Laser HR | Highly Reflective HVM | High Volume Manufacturing LASCAD | Laser Cavity Analysis & Design LASER | Light Amplification by Stimulated Emission of Radiation MASER | Microwave Amplification by Stimulated Emission of Radiation ND | Neutral Density Nd:YAG | Neodymium Doped Yttrium Aluminum Garnet Nd:YVO4 | Neodymium Doped Yttrium Vanadate OC | Output Coupler PC | Pockel's Cell QD | Quantum Defect QE | Quantum Efficiency QWP | Quarter Wave Plate SA | Saturable Absorber TEM | Transverse Electromagnetic TFP | Thin Film Polarizer Tm:YAG | Thulium Doped Yttrium Aluminum Garnet Yb:KYW | Ytterbium Doped Potassium Yttrium Tungstate Yb:YAG | Ytterbium Doped Yttrium Aluminum Garnet xiii CHAPTER 1 INTRODUCTION In the year 1955, the first instance of stimulated emission was demonstrated by Charles H. Townes [1]. Townes effectively used ammonia (NH3) to amplify microwaves. The device was called the MASER, an acronym for microwave amplification by stimulated emission of radiation. After such demonstration, it was speculated that producing an optical maser would be possible. In 1958, Schawlow and Townes published a thorough theory behind optical masers [2]. It was not until May of 1960 that the first optical maser was demonstrated by Miaman [3]. The term LASER, an acronym for light amplification by stimulated emission of radiation, was established as the official name for such devices. At the time, there were no practical applications for this new laser technology. Afterwards, different kinds of laser technologies emerged with different wavelengths and powers. Throughout the years, scientists and engineers have adapted the use of lasers to manufacturing processes in order to increase the efficiency and performance of the end prod- ucts. The industrial laser materials processing industry, which yields over $1B of revenue every year, is one of the main consumers and contributors to laser technology [4]. For in- dustry, lasers are used for cutting, welding, and processing [5]. Lasers have also began to be used for medicinal purposes.
Details
-
File Typepdf
-
Upload Time-
-
Content LanguagesEnglish
-
Upload UserAnonymous/Not logged-in
-
File Pages90 Page
-
File Size-