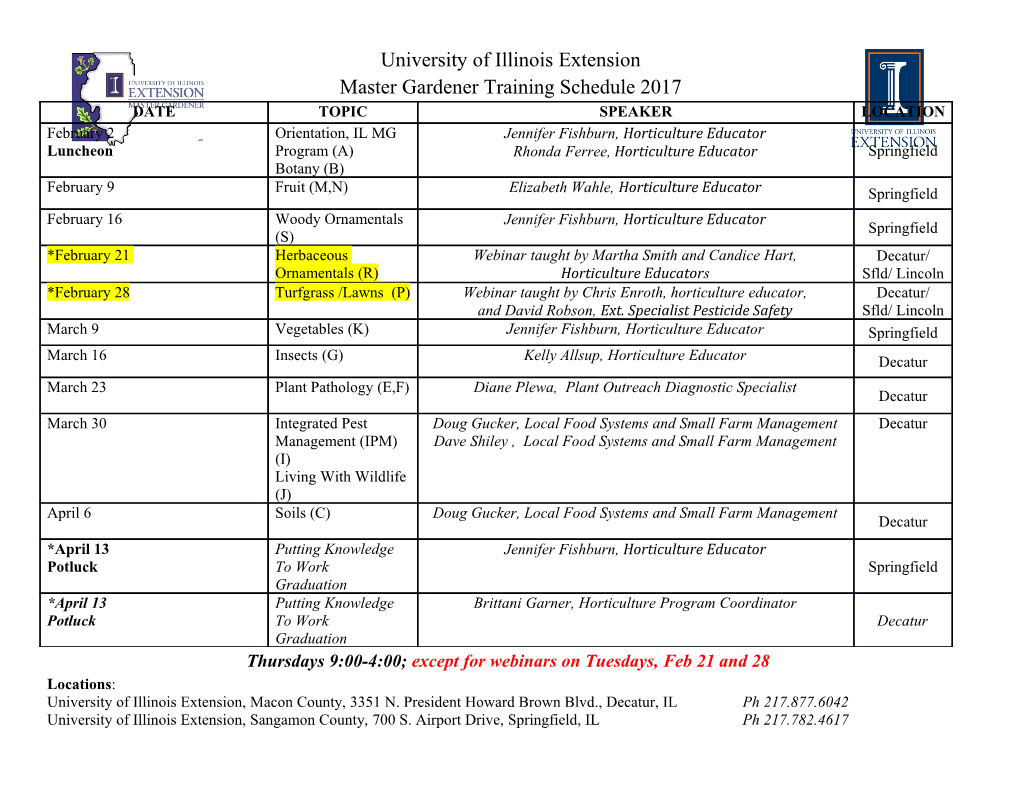
Materials Research. 2015; 18(4): 843-852 © 2015 DOI: http://dx.doi.org/10.1590/1516-1439.000314 Microstructural and Micromechanical Effects of Cold Roll-forming on High Strength Dual Phase Steels Meritxell Ruiz-Andresa, Ana Condea, Juan de Damboreneaa, Ignacio Garciaa* aCentro Nacional de Investigaciones Metalúrgicas – CENIM-CSIC, Madrid, Spain Received: June 18, 2015; Revised: June 29, 2015 In this work correlation between the 1000 MPa dual phase (DP) steel microstructure and the strain gained after roll-forming process have been studied by both microstructural and micromechanical analysis. The scanning electron microscope (SEM) inspection in the bent area reveals changes in the ferrite-martensitic microstructure. The plastic deformation of DP steels originates defects at the edges of bent sheet make them partly responsible for the damage caused. In addition, electron backscatter diffraction (EBSD) measurements have been carried out for an in-depth characterization after roll-forming. A high density of misorientation of the crystal lattice within the ferrite strained grains is observed, mainly concentrated in the ferrite/martensite grain boundaries. Furthermore, the ultramicrohardness tests exhibit little dependence between mechanical parameters and the material properties. Keywords: dual phase steel, roll-forming, EBSD, ultramicrohardness, microstructure 1. Introduction High strength low alloy (HSLA) steels, specifically dual or cup drawing. Luo & Wierzbicki15 analysed the failure phase (DP) steels, are widely used in the automotive industry behaviour of DP steels during stretch-bending operations due to the necessity of improving fuel efficiency1-3, with its and summarized the typical damage accumulation in this subsequent energy saving and environmental protection4. area. Wu-rong et al.8 found that DP steels show competitive In addition, these DP steels have been developed to increase formability after cup drawing tests, despite encountering the highly demanding collision safety standards5 in the consistent shear cracks on the damage surfaces. Wang & vehicle body frame parts like bumper beam, door beam and Wei 16 showed that in stretch-bending tests not only latitudinal panel reinforcement. but also longitudinal cracks were propagated along DP steels DP steels are characterized by a microstructure consisting in a mixed propagation mode, i.e. along ferrite-martensite of about 75-85% ferrite phase with the remainder being a interfaces and/or also across martensite grains. Subsequently, mixture of the martensite and lower amounts of other such Wang et al.4 discussed that the fracture mode experiences as bainite and retained austenite6,7. a transition from shear fracture to necking before fracture. Such a structure leads to different unique properties, as Mishra & Thuillier17 concluded that bending area of maximum high tensile strength, low yield strength ratio followed by strain is not highly localised, but more uniform. continuous yielding behavior (no-yield point elongation), high However, to the author’s best knowledge no studies work-hardening rate at early stages of plastic deformation have been reported on the DP steels evolution in cold as well as good ductility8-10. Furthermore, the absence of the roll-forming processes. yield point elongation provides DP steels with a high crash In this work, microstructural and micromechanical study resistance, good formability and excellent surface finish11. have been performed in order to go deep in the understanding of Roll-forming is a bending process in which a sheet metal the behaviour between the microstructure and the deformation is continuously and gradually formed into a profile with a during cold roll-forming processes and provides overall desired cross-section along the transverse direction by passing responses to the automobile manufacturing industry, which through a series of rolls arranged in tandem12. It can be is a subject of main concern, from both industry sector, in performed at high speeds and therefore has been considered, ever increasing new designs for car structural components, in recent years, very interesting for the manufacturing of and also in academic research. automobile components. However, during roll-forming the microstructure of the sheet metal can undergo serious 2. Experimental Procedure damage. The outer surface remains stretched consequently The chemical composition of the commercial high the inner surface is compressed. Thus, these outer surfaces, strength dual phase DP1000 used is given in Table 1. highly deformed, are preferential nucleation sites, growth The 1.5mm thick DP1000 sheet was roll-forming in hat-section and coalescence of voids and/or cracks13,14. geometry profile by Autotech Engineering (AIE, Gestamp Several studies4,7,15-19 have been conducted on the DP R&D). The roll-forming direction was parallel to the steels behaviour under formability tests, as bending, stamping rolling direction of the sheet and performed at a feed rate *e-mail: [email protected] of 50 m/min. Hat-section was formed by 6-stages, in which 844 Ruiz-Andres et al. Materials Research the arrangements of the roll bend angles were varied over Finally, for Electron Back Scatter Diffraction (EBSD) 15º → 30º → 45º→ 60º → 75º → 90º. analysis, the specimens were mounted in epoxy resin, grounded Specimens were taken from a DP1000 sheet after being in SiC and polished with diamond paste of 3 and 1 µm processed revealing the LT-ST plane (Figure 1). as it was above described. After this stage the specimens The specimens analysed are presented in Figure 2. were automatically polished with colloidal silica for 30 s. One of specimens was taken from an area free from any Then, the specimens were rinsed in distilled water, soaked strain - blank specimen-. Three specimens were taken from in ethanol and dried in direct warm air. Immediately after, the bent area characterized by three distinctive regions: the the specimens were etched with 2% Nital solution for 15 s. outer edge, the middle zone and the inner edge. SEM images and EBSD scans were carried out in a field Metallographic specimens were prepared according to emission gun scanning electron microscopy (FEG-SEM) standard procedures. They were mounted in an epoxy resin, J8M6500F JEOL equipped with energy-dispersive spectroscopy ground down through successive grades of SiC paper to (EDS) facilities. A statistically relevant area of 322 x 257 µm 2000 grade, degreased with alkaline cleaner and rinsed in was scanned using step size of 0.1 µm. The EBSD raw data were post-processed in detail by making use of the HKL tap water followed by deionized water and finally polished Analysis Software. Grain boundaries were characterized by with diamond paste of 3 and 1 µm. a misorientation larger than 5º between among neighbouring For scanning electron microscopy (SEM) inspections, measurements points. the specimens were etched with 2% Nital solution for 15 s, Several parameters on the basis of EBSD, such as the given that Nital preferentially etches ferrite and outlines their image quality (IQ), the inverse pole figure (IPF) and the kernel grain boundaries leaving martensite undissolved. average misorientation (KAM) maps are powerful tools in In order to calculate the volume fraction of ferrite and order to characterize the material. However, the similarity martensite phases, metallographic analysis were conducted between the crystalline structure of the microconstituents in by using an image software analysis. Using a commercial dual-phase steels -ferrite (bcc) and martensite (bct, with a imaging software (Analysisdocu®) the martensite and ferrite low tretagonality)- limits the software in order to distinguish phases were automatically distinguished by adjusting the between both phases, specifically when ferrite is highly contrast and colour, so martensite grains turn black, while strained20. In this work, it has been indexed ferrite as the ferrite grains turn white. main phase. Consequently, the Kikuchi diffraction patterns that differ from the ferrite crystalline structure (bcc) will be considered not indexed, given as a dark point and related to strained ferrite, martensite phase or grain boundaries. Hardness measurements were performed by a NanoTest 550 Micro Materials Ltd nanoindenter, using a Berkovich diamond tip. Tests were carried out at two indentation depths of 500 nm and 5000 nm. The local hardness and elastic modulus results were estimated from the loading and unloading curves using the standard Oliver-Pharr methodology21. Figure 1. DP1000 specimen (a) Hat-section profile; (b) Scheme 3. Results main directions. 3.1. SEM characterization Figure 3 clearly shows that the microstructure of DP1000 steel is comprised by harden island-shaped martensite inclusions randomly distributed (bright contrast) and a soft ferrite matrix (dark contrast). Figure 3a reveals the microstructure corresponding to the blank specimen. This DP1000 specimen analysed is characterized by a 26.5 vol.% of martensite phase. Ferrite grains size range from 1.2 µm to 5 µm, approximately. The SEM images gathered in Figure 3b-d correspond to the microstructure in the bent area; outer edge, middle zone and inner edge, respectively. The microstructure corresponding to the outer edge in the bent area, Figure 3b, Figure 2. Details of DP1000 specimen (a) selected areas to analysis; shows elongated ferrite grains, with the long axis parallel to (b) representative studied regions in the bent area. the bending direction. The length of these ferrite grains
Details
-
File Typepdf
-
Upload Time-
-
Content LanguagesEnglish
-
Upload UserAnonymous/Not logged-in
-
File Pages10 Page
-
File Size-