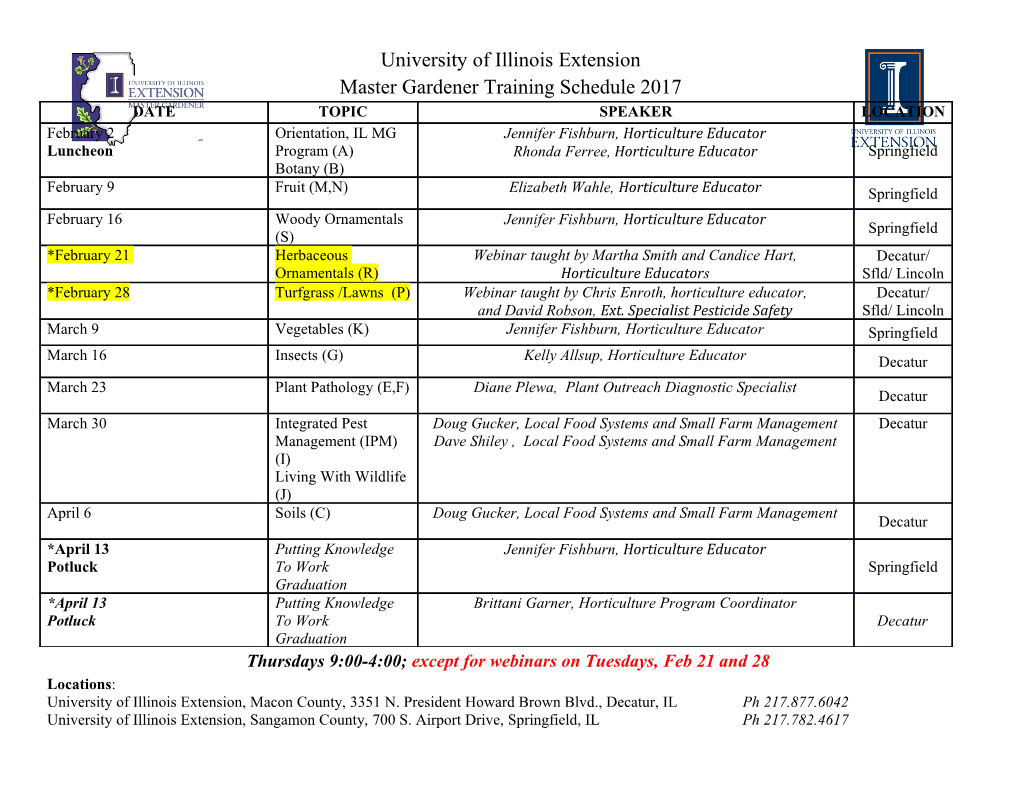
Industrial and Agricultural Published by TheEPRI Center for Materials Production Technologies and Services is tapped from the bottom theof Introduction furnace into hot-metal cars and transferred to the basic oxygen The steel industry is comprised furnace (BOF). The metallic charge of electric arc furnace (EAF) and to the BOF consists of 60 to 70% integrated steel producers. There hot metal from the blast furnace are significant differences between and 30 to 40% steel scrap. The these steelmaking processes. EAF primary functionof the BOF is to steelmakers, often referredto as refine the liquid iron tosteel by minimills, producesteel by melting reducing the carbonto a prescribed scrap, see Figure 1. The integrated level, generally less than 0.5%. as steel mills produce steel from iron well as removing impurities such Figure 2. DC Electric Arc Furnace. ore utilizingthe blast furnace and as silicon, sulfur, and phosphorus. basic oxygen furnaceprocesses. This is accomplished injecting by century. In 1996, approximately 39% In the integratedprocess, the oxygen into the bathand the of the totalof 103 million tons of blast furnace is provided with addition of fluxes. steel shipped was made in EAFs energy in the form ofcoke which is With EAF steelmaking, normally with thebalance produced by the mixed with ironore pellets/sinter 100% scrap steel is charged to the blast furnace/basic oxygen process. and limestoneto constitute afur- furnace. In the process, oxygen is The total energy required to make nace burden. Liquid iron, containing also injected and fluxesadded to one ton of liquidsteel in an EAF is approximately 4% dissolved carbon control carbon content and remove about 640 kwh or 6.4 million impurities. As Btuhon (including electricalenergy, more high quality burners, and other chemicalener- steel products are gy) which is onlya fractionof the being produced 19 million Btuhonrequired using the by EAFs, steelmak- ers are beginning blast furnacebasic oxygen furnace method. to supplement the After melting and refining, the scrap charge with liquid steel is transportedto a direct reduced iron continuous casting machine where (DRI) and iron it is cast and solidified. However, a carbide. The few ingot moldshops still exist. details ofEAF steel Continuous casting machines production are described in a produce semifinished sections, i.e., billets, blooms, and slabs. Ingots subsequent CMP require an additional rollingopera- TechCommenrary tion toproduce the semifinished titled “Under- standing Electric shapes. Final steel products, strip, Arc Furnace sheets, bars, rods, plates, tubes, etc., are manufactured from the Operations” semifinished section: ;ng avari- (TC-107714). ety ofrolling mills ar. xesses. Because -. ~. the EAF process IS more energy The Electric Arc Furnace efficient and less capital is required, The first commercial EAF in the production ofsteel United States, a 4-tOn unit, was placed in operation in 1906 by the Photo courtesy of Fuchs by EAFs has increased signifi- Holcomb Steel Co. at Syracuse, Figure 1. A 95-ton, 80-MVA dc Single ShaftArc Furnace in cantly over the New York. Production increased sig- Operation at North Star Steel, Kingman, Arizona. past quarter of a nificantly during WorldWar II, and Ore Blast Furnace BasicOxygenFurnace Ladle Refining m-1 ml Limestonea a-Coke Natural Gas Coal Electric Arc Furnace Oil Oxygen l- Scrap THE STE DRI Iron CarbideIronPig Blast Fur Electric 1 again after 1960 with theadvent of lined hearth, vertical cylindrical tapping liquidsteel into a ladle. mini steel mills. Electric furnace sidewalls, and a removable roof. Electric power is supplied from a steel production increased steadily The graphite electrodes, which pass 3-phase, multivoltage tap trans- from 8.4 million tons in1960 to 42.4 through holesin the roof, are former. The electrodes are connect- million tons in1995, or 39% of total clamped to arms which move verti- ed byheavy flexible cables to the steel production. It is expected that cally on masts mounted to the transformer which is locatedas EAF steel production will reach 50% furnace assembly. The electrodes close to the furnaceas possible to within the next 10 years. and roofcan be raised and swung avoid excessive transmission loss The rapid growth inelectric to one side to permit furnace charg- with theheavy currents employed. furnace steel is due to a number of ing. In conventional furnaces, a Most ac furnaces, see Figure 3, have factors including relatively low horizontal tapping spout isbuilt into three-electrodes, though some investment requirements, improved the hearth structure with a working newer furnaces are dc one- ortwo- technology which has reduced door located diametrically opposite electrodes, see Figure 2. Many production costs, and the generally in the sidewall. The entire furnace modern electric arc furnaces also lower price of steel scrap in com- unit can be tilted onrockers for are equipped with oxy-fuel burners parison with blast furnace hot metal. Capital investment per annual ton ofhot-rolled sheets (1996 dollars) is approximately$750 for coke oven/blast furnace, basic oxygen furnace productionvs. $213 for electric furnaces. Approximately 222 electric arc furnaces, ranging in capacity from less than 10 to 400 tons, areoperated in the UnitedStates by integrated, specialty, and minimill producers. Electric furnaces also are used in some foundry operations with their use doubling since 1957. In general, furnace capacities here are smaller (oneto 60 tons) than in basic steel operations. Steel foundries are the principalusers of electric arc furnaces. There are approximately 185 foundries with EAFs in the UnitedStates. Figure 3. An ac Electric Arc Furnacewith an Oxygen EAFs consist of a refractory- Lance and EccentricBottom Tapping. TechCommenrarv 2 ContinuousCastingRolling & Other Sheet Mill Processing Oxygen injection for cutting scrap and decarburization to reduce refining time. Lime injectionto reduce pro- Plate cessing time andheat loss. Foamy slags to shield sidewalls and rooffrom heat radiation from thearcs. This practice permits theuse of maximum Rod available secondary voltage through the use of longarcs with high powerfactors. Computer controlto optimize electric power programming and automatic tap changing Bar based on furnace condition and power demand. More complex systems provide control of metallurgical parameters (tap temperature Thls slmplifted Rowchart IS lmended to and timing of process events), provlde a brood overwew to me technology data logging, and least-cost CYCLE end roleof electncitv in me steel manufactur- mg process. Most operabons are custom charge calculations, etc. dewgned for me appllcabon ata panicular sic Oxygen Steelmaking facllny and may Include equipment or process- Arc stability is an important es not deplcted hare. For help WUI rpeclfic factor in the operation of an electric oppbca0ons. talklo your elmmc ublny marketst- ~ceSteelmaking * Ing representative or an equlpmem supplter. arc furnace. At the beginning of the melting period, power input is limited byunstable arcs which can also cause flicker in the primary voltage line. Flicker is of concern and lances for injectingoxygen, close to 1 hour. Power consumption with increasing transformer power. lime, and carbon. for an efficient operation shouldbe However, most new UHP meltshops Energy input consists of in the range of 360 to 400 kWhhon. are equipped with static VAR gener- approximately 60% electrical and Thus, for a consumption of400 ators for thisreason. Also, flicker 40% chemical which isderived kWh/ton, the monthlyelectrical is reduced significantly when a dc from oxy-fuel combustion, oxida- consumption would beapproxi- EAF is used to meltsteel. tion ofcarbon, and other chemical mately 20 million kwh. Additional state-of-the-art reactions. Approximately 53% of Total usage of electric power developments currently being the totalenergy is retained in the for the42.4 million tonsproduced introduced to improvefurnace liquid steel; heat loss in thewaste in the UnitedStates in 1995 was performance as well as steel gases is 20%, cooling losses from approximately 17 billion kwh. quality include: the walls and roof17%, with 10% The cost of producingsteel lost in theslag. in electric furnaces varies consid- Eccentric bottom tappingto reduce tap times, reduce tem- erably. The major componentis perature losses, and avoidslag raw materials 63%, followed by Operations and Costs contamination in the ladle. electric power 8%, labor 5%, Oxygen and carbon injection At the Stan aof heat cycle, with maintenance including refractories 4%, electrodes 2%, dust disposal to provide additional heat from the electrodes and roofraised and oxidation ofcarbon. swung toone side, a charge of steel 1.4%, oxygen usage I%,and the scrap is dropped into thefurnace balance fixed costs. Coated/water-cooled electrodes from a clamshell bucket. The roof to reduce electrode consumption. is replaced, electrodes lowered, Special Features Scrap preheating to recover and an arc struck. Arc length is energy from furnace waste optimized to meet the changing Modern furnaces are equipped gases. conditions during the melting with a variety of features to increase Single electrode dc furnaces to process by selecting the appropri- production rates, reduce heat times, reduce electrode consumption ate voltage tap. Two, and some- and lower operatingcosts. They and flicker. times threebuckets of scrap, are include: used in making a single heat of In summary, modern electric arc Ultra HighPower (UHP)
Details
-
File Typepdf
-
Upload Time-
-
Content LanguagesEnglish
-
Upload UserAnonymous/Not logged-in
-
File Pages4 Page
-
File Size-