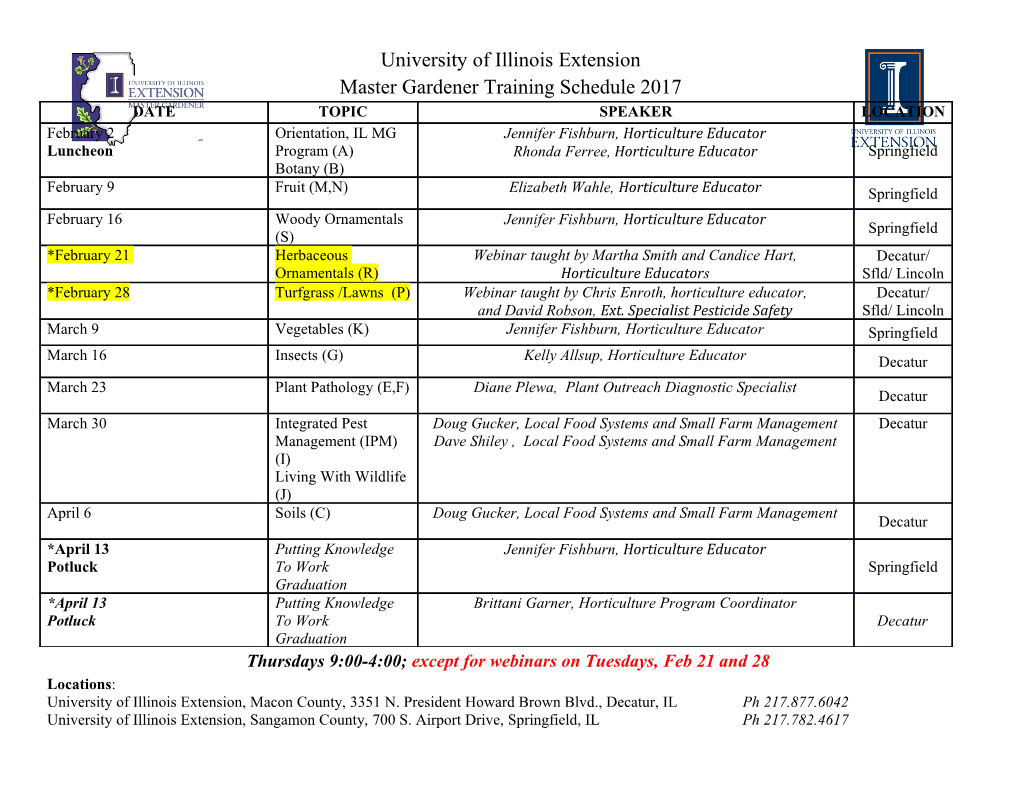
Sensors and Actuators A 318 (2021) 112434 Contents lists available at ScienceDirect Sensors and Actuators A: Physical journal homepage: www.elsevier.com/locate/sna A high-sensitivity graphene ammonia sensor via aerosol jet printing a,b a,b a,b,∗ c a,b Yuchao Zhu , Lingke Yu , Dezhi Wu , Wenlong Lv , Lingyun Wang a School of Aerospace Engineering, Xiamen University, Xiamen, 361005, China b Shenzhen Research Institute of Xiamen University, Shenzhen, 518057, China c Pen-Tung Sah Institute of Micro-Nano Science and Technology, Xiamen University, Xiamen, 361005, China a r t i c l e i n f o a b s t r a c t Article history: High-sensitivity ammonia gas sensors are paramount to many fields in our industries and lives. Due Received 2 February 2020 to its complicated fabrication processes, large size and long recovery time of most existing ammonia Received in revised form gas sensors, we present a micron-scale graphene-based ammonia gas sensor using aerosol-jet printing 19 September 2020 technology. The graphene sensor exhibited high response sensitivity (∼4.64 % for 4.35 ppm NH3 and Accepted 8 November 2020 ∼52.01 % for 97.19 ppm NH3, respectively), short adsorption / desorption time ranging from 50 s to 150 Available online 4 December 2020 s, good reversibility and repeatability. Further employment of micro-heater close to the sensing line reduced desorption time more than ∼14.3 % when 10 V being applied onto the heater. Such design of the Keywords: Graphene ammonia gas sensor by aerosol-jet printing can give an insight for graphene-based ammonia gas sensors, which may pave a way for the convenient integration with other sensors in portable instruments for coal Ammonia gas sensors Aerosol jet printing miners and pathfinders etc. © 2020 Elsevier B.V. All rights reserved. 1. Introduction hybrid composite materials (graphene/PANI, pf-MWCNT/PANI, PANI/TiO2, RGO/PANI, graphene-PEDOT/PSS, PEDOT/PSS-SWCNTs) Ammonia gas, a strong irritant, colorless and flammable gas, can [18–23], and conducting polymers (polyaniline (PANI), poly be found in various applications, including mines, caves, chemical (3,4-ethylenedioxythiophene)/ poly (styrenesulfonate) (PEDOT- manufacturing and nitrogenous fertilizers [1,2]. However, it could PSS), poly (maminoben-zene sulfonic acid) (PABS), poly(3- not only easily corrode the upper respiratory tract of human beings hexylthiophene)) [24–30] in many literatures. Among them, carbon or animals but also set off chemical reaction react with other air materials have been proved to be one of the most promising candi- pollutants (NOx or SOx) to form particulate matter less than 2.5 m dates to sense ammonia gas due to its high specific surface area and to cause severe diseases [3]. Therefore, the permitted maximum the sensitivity of electrons inside transferring inside are very sen- concentration of ammonia ca. 20 ppm in the workplace [4] and a sitive to the ammonia molecules adsorbed on the surface [31–33]. short-term (15 min) exposure limit of 35 ppm NH3 vapor in ambient Zhang et al. demonstrated a flexible wireless sensor using RGO dec- conditions has been recommended by the US Occupational Safety orated with Ag-NPs as the gas-sensitive material that can monitor and Health Administration (OSHA) [5]. So it is of great significance NH3 gas at a low concentration about 5 ppm and had a fast response to design and fabricate a high-sensitivity ammonia sensor. and recovery time (7.5 s and 20 s, respectively) [34]. Graphene- In the past few decades, electrically based ammonia sen- based device functionalized with Au-NPs could reach the maximum sor is a preferred selection in which the signal could be sensitivity (∼8 %) for 58 ppm of NH3 [35]. The reduced graphene conveniently detected with less transferring processes, com- oxide (RGO)–polyaniline (PANI) hybrids ammonia (NH3) gas sensor paring with optical and mass sensitive ammonia sensors [6,7]. presented by Huang et al. exhibited much better response (25.1 % Nowadays, numerous materials have been used in NH3 sen- and 59.2 % of resistance change with the concentration of NH3 gas sors, including carbon nanomaterials (carbon nanotubes (CNT), at 5 and 50 ppm, respectively) [36]. The prepared composite com- graphene, reduced graphene oxide (RGO)) [8–13], metal oxide bined effect of rGO/CNTs/ZnO showed good response to ammonia (In2O3, SnO2, ZnO, CuO, Fe2O3, V2O5, WO3, CeO2) [14–17], vapor at room temperature with fast response and recovery time (55 s and 116 s towards 10 ppm concentration, respectively) [37]. Graphene owns two-dimensional honeycomb structure to allow a full exposure of its atoms for the better adsorption of gas ∗ Corresponding author at: School of Aerospace Engineering, Xiamen University, molecules, thus maximizing the sensor’s surface area to volume and Xiamen, 361005, China. increasing its sensitivity to gas molecules. Moreover, it has intrinsi- E-mail address: [email protected] (D. Wu). https://doi.org/10.1016/j.sna.2020.112434 0924-4247/© 2020 Elsevier B.V. All rights reserved. Y. Zhu, L. Yu, D. Wu et al. Sensors and Actuators A 318 (2021) 112434 Fig. 1. Schematic diagram of aerosol-jet printing system. Fig. 2. Schematic illustration of the test system of ammonia gas sensor. Table 1 cally low electrical noise owing to its crystal lattice, which tends to Recommended printing parameters of the aerosol-jet system on Si/ SiO2 wafers for screen charge fluctuations more effectively than one-dimensional ammonia gas test. carbon nanomaterials such as carbon nanotubes [38,39]. Besides Material Graphene the combination of various materials, many methods including Sheath Gas Flow Rate (ccm) 65 CVD, laser direct writing, electrospinning, printing, coating etc. Atomizer Flow Rate (ccm) 11 have been proposed to fabricate sensors. In the future, laser 3D Ultrasonic Atomizer Power (V) 45 printing could be another way to fabricate the high sensitivity sen- Nozzle diameter (m) 250 sor [40]. A scaffold of porous nickel foam as a template was used to Deposition velocity (mm/s) 0.5 ◦ fabricate graphene foam network to enhance its gas detection per- Substrate temperature ( C) 80 formance (∼30 % resistance change for 1000 ppm NH3 and ∼5% for 20 ppm NH3) compared to that of CVD monolayer graphene [45]. Seekaew et al. presented a simple inkjet-printing of PEDOT:PSS 2 Y. Zhu, L. Yu, D. Wu et al. Sensors and Actuators A 318 (2021) 112434 Fig. 3. Optical microscopes of the printed graphene lines and its relationship between line width and various printing processing parameters (a)-(b) sheath gas flow, (c)-(d) stage moving speed, (e)-(f) number of the printing passes. composite film to fabricate a gas sensor with sensitivity of 0.06 performance including sensitivity, response/recovery time and −1 % ppm in a wide scope of NH3 concentrations from 5 to 1000 repeatability were evaluated with/without heating under differ- ppm [22]. Additive manufacturing technologies such as u-contact ent concentrations, and experiments results showed that high printing, electrohydrodynamic direct writing etc. are regarded as response magnitude (∼4.64 % for 4.35 ppm and ∼52.01 % for 97.19 simple and promising tools for large-scale roll-to-roll fabrication. ppm NH3 gas, respectively), fast response (response and recovery Here we introduce a rapid printing technology, aerosol-jet print- time were both 50−150 seconds), good reversibility and repeatabil- ing, to manufacture a micron-scale sized ammonia gas sensor on ity were finally obtained. Also heating process with applied voltage a silicon substrate to exhibit its superb sensing properties. Further of 10 V facilitated reduction of desorption time at least 14.3 %. employment of additional micro-heater around the periphery of the sensing unit via aerosol-jet printing gains faster and repro- 2. Experimental ducible sensing performance. In this work, the printing process parameters were dis- A commercial aerosol-jet printing system (Aerosol Jet 300, M3D, cussed firstly to fabricate uniform and stable sensors. Then their Optomec, USA) shown in Fig. 1, including three major parts such as 3 Y. Zhu, L. Yu, D. Wu et al. Sensors and Actuators A 318 (2021) 112434 an aerosol actuator, a deposition nozzle and a moving stage, was used to fabricate sensor samples, which has been also reported in details in other literatures [46–48]. Compared to the ink jet systems, aerosol jet printers have clog resistant nozzle, a contin- uous stream of high-density microdroplets, the ability to deposit a wide range of viscosity of inks (1–1000 cP for pneumatic atomizer, 1–10 cP for ultrasonic atomizer), and more tightly focused patterns. Graphene aqueous solution (conc: 1 mg/mL, MW: 12.01 g/mol, Sigma-Aldrich) in the atomizing tank was atomized to become aerosol, and then delivered to the deposition nozzle through a plas- tic tube and finally transferred onto the sensor substrates on a heating plate attached to the moving stage with the help of sheath gas. During the study of the effects of the processing parameters on width and resistance, five samples were fabricated under the same condition. The recommended printing parameters have been listed in Table 1. Fig. 2 illustrates the ammonia gas-sensing measurement setup, which includes two bottles, two injectors (one was filled with air, the other was filled with ammonia water), an air pump, a switch valve, a computer, a digital multimeter and a power source. Bottle I was used for the volatilization of ammonia and Bottle II was for gas detection. Fig. 2 also shows a sensor with micro-heater and a sensor with- out a heater for comparison was also built as illustrated in Fig. S1. They were both deposited by aerosol-jet printing system on the Si/SiO2 substrates, involving nano-silver wires. When 20 mL ammonia water was injected into the Bottle I, ammonia gas quickly evaporated to fill the bottle.
Details
-
File Typepdf
-
Upload Time-
-
Content LanguagesEnglish
-
Upload UserAnonymous/Not logged-in
-
File Pages10 Page
-
File Size-